Techno-economic assessment on the fuel flexibility of a commercial scale combined cycle gas turbine integrated with a CO2 capture plant
Summary
Post-combustion carbon capture is a valuable technology, capable of being deployed to meet global CO2 emissions targets. The technology is mature and can be retrofitted easily with existing carbon emitting energy generation sources, such as natural gas combined cycles. This study investigates the effect of operating a natural gas combined cycle plant coupled with carbon capture and storage while using varying fuel compositions, with a strong focus on the influence of the CO2 concentration in the fuel. The novelty of this study lies in exploring the technical and economic performance of the integrated system, whilst operating with different fuel compositions. The study reports the design of a natural gas combined cycle gas turbine and CO2 capture plant (with 30 wt% monoethanolamine), which were modelled using the gCCS process modelling application. The fuel compositions analysed were varied, with focus on the CO2 content increasing from 1% to 5%, 7.5% and 10%. The operation of the CO2 capture plant is also investigated with focus on the CO2 capture efficiency, specific reboiler duty and the flooding point. The economic analysis highlights the effect of the varying fuel compositions on the cost of electricity as well as the cost of CO2 avoided. The study revealed that increased CO2 concentrations in the fuel cause a decrease in the efficiency of the natural gas combined cycle gas turbine; however, rising the CO2 concentration and flowrate of the flue gas improves the operation of the capture plant at the risk of an increase in the flooding velocity in the column. The economic analysis shows a slight increase in cost of electricity for fuels with higher CO2 contents; however, the results also show a reduction in the cost of CO2 avoided by larger margins.
1 INTRODUCTION
The World Energy Council highlights in its 2019 World Energy Insights Brief that growth in electricity generation is unavoidable in the future.1 Most of the scenarios investigated in the brief suggest that the overall fossil fuel contribution in the global diverse energy mix will not get lower than 70% by 2040. Also, the brief predicts a steep growth in natural gas usage. It is projected that natural gas will contribute approximately 20% of the primary energy mix by 2040.1 The rising supply of tight gas and shale gas as well as the technology maturity of natural gas power generation units will all contribute significantly to the increase of natural gas usage.2, 3
An advantage of energy generation via natural gas combined cycle (NGCC) is the high efficiencies and reduced emissions compared to coal-fired plants.4 This also plays a role in the growing usage of natural gas in the fossil fuel energy sector as opposed to other fossil fuels. The rapidly increasing global population is going to lead to a substantial increase in energy consumption for daily use in homes and offices.5, 6 This will contribute to an increase in fossil fuel demand and subsequently to an increase in emissions from energy generation plants. Currently, 40% of the total CO2 emissions are emitted in conventional fossil fuel power units.7 Therefore, an escalation in energy demand will lead to an increase in CO2 emitted and consequently stabilizing the amount of CO2 in the atmosphere will require a variety of modifications to the power plant such as increase in plant efficiency and the development of technology to reduce the CO2 emitted into the atmosphere.8 Hence, there have been heightened interest and investments in the development of emission strategies such as the decarbonisation of electricity generation.1 One means of implementing this strategy is by the use of fossil fuels with carbon capture and storage (CCS) techniques such as post-combustion capture (PCC). CCS is debated to be a technology capable of mitigating the greenhouse gas emissions from fossil fuel power plants by 50% to 85% by 2050,9 hence bringing the 2° scenario target closer. The energy technology perspective (ETP)10 has estimated that achieving the 2° limit would require a similar amount of reductions in emissions by 2050.
The PCC is not a new technology and has been used in other industries including the iron and steel industry11 as well as the cement industry.12 The implementation of CCS into the energy sector can prove to be of high advantage once the technology has fully matured from its development stage to its fully commercial stage. Research has been carried out worldwide by universities and research groups aiming to investigate different carbon capture techniques that are able to remove CO2 from the flue gases of various power generation sources. Thus, highlighting the significance of CCS technologies in the primary energy mix of the future, with the ETP 2017 report predicting 18% of the global carbon emissions reductions by 2060 will be as a result of CCS.10 In the future, CCS is anticipated to be a key technology in mitigating the carbon emissions in an energy sector operated by fossil fuels.13 Currently, there are some CCS technologies adapted for commercially scaled fossil fuel energy generation systems, which are the SaskPower Boundary Dam in Canada,14 the Peterhead CCS project in the United Kingdom15 and the PetraNova in the United States.16 With the implementation of CCS with fossil fuels, there will be unlocking of more fossil fuel reserves, used in the energy sector. Hence, making the targeted global temperature increase of only 2°C by 2050 more realistic.17 Also, its ability to be retrofitted with existing plants makes it a promising technology for CO2 capture.8 One important concern regarding the utilisation of CCS with NGCC is its operational flexibility with different fuels of varying compositions with the aim of achieving a secure delivery of electricity.18, 19
Natural gas is a mixture of methane, ethane, propane, butane, pentane, as well as nitrogen and carbon dioxide.20 Other components include hydrogen sulphide and helium. Natural gas compositions differ in different regions due to the different processes that lead to the formation of the fossil fuel.21 Part of the components of natural gas fields that are available in large amounts is carbon dioxide.5 The carbon dioxide in many natural gas fields can vary up to 20%, with the CO2 in some other fields getting as high as 50%.21 Natural gas with very high CO2 content is usually sent for CO2 removal since high CO2 amounts will lead to a decrease in the specific lower heating value (LHV) of the fuel.5
In the literature, there are several studies that analyse the integration of an NGCC with an amine-based capture plant such as Adams and Mac Dowell,4 in which useful insights on operating both the NGCC and the amine capture plant are provided. Some researchers, such as Øi et al,22 have also investigated advanced configurations of the absorption and the desorption process in order to decrease the capital and operational cost. However, the lack of economic considerations in this study raises the issue of applicability and hence its potential to be integrated into the current energy sector.
There are several studies that look into the effect of different natural gas compositions on the operation of gas turbines and combustion performance.5, 23, 24 Also, there have been a few investigations into the techno-economic performance of amine capture plants that were coupled to NGCCs.25-28 These papers performed a comparative investigation on the effect of different NGCC configurations, including the use of systems such as EGR and S-EGR, exhaust gas recirculation and selective exhaust gas recirculation respectively, and their varying exhaust gas composition of varying capture plant specifications.
Other researchers such as Cormos et al29 investigated alternative innovative capture methods such as calcium looping to be integrated with the NGCC, and concluded that reactive gas-solid systems such as calcium looping cycles provide better techno-economic performance than other gas-liquid carbon capture options such as amine capture plants. Also, researchers such as Li et al30 and Chu et al31 focused on optimizing the operation of a pilot scale amine capture plant that uses MEA for various operating conditions and parameters. Li et al30 concluded that the optimal operating condition in a pilot plant was obtained when operating at 35 wt% MEA, 0.25 (molCO2/molMEA) lean CO2 loading, 40°C lean solvent temperature, 200 kPa stripper pressure, hence resulting in 3.6 MJ/kg CO2 as the reboiler duty. Chu et al31 suggested an increase in size of the porosity of the packing material as well as the surface area per unit volume to attain a minimum energy consumption.
Regarding various fuels being coupled with a capture plant, researchers such as Berstad et al32 performed a parametric comparative study on a MEA-based CO2 capture plant coupled with an NGCC, coal and biomass power generation units. In the study, it was concluded that the NGCC produced the lowest efficiency penalty, which is mainly due to the high efficiency in the system mentioned earlier. Also, Agbonghae et al26 performed a process modelling study in which the lean CO2 loading and solvent recirculation rate in a commercial-scale amine capture plant where optimized. Furthermore, a techno-economic assessment was conducted to obtain the optimum process design of the capture unit. The plant was simulated to service both coal-fired and offshore-based gas-fired power plants.
Overall, the utilization of varying fuel compositions with CCS is currently unclear. Thus, this study aims to deliver an in-depth understanding into the operational and economic benefits and drawbacks associated with fuel flexibility operations of an NGCC with CCS. The main novelty in this paper rests on the assessment of the effect of fuel flexibility on the performance of a commercial-scale NGCC integrated with CCS and a further analysis on its effect on the techno-economics of a commercially scaled amine capture plant. This study aims to fill the gap in knowledge pertaining to the implementation of an NGCC operating with various CO2 content fuels and the ensuing downstream effect observed when an amine capture plant is coupled. The maximum fuel CO2 concentration investigated in this study is 10 mol%, and this is to ensure the complete convergence of the combustor model in the software package used. Also, similar studies performed by Nikpey et al33 on a micro gas turbine with varying increase in CO2 content in the fuel highlight that combustor flameout occurs when operating at higher than 10 mol% CO2 in the fuel at full load operating conditions. The CCS technique investigated in this study is PCC with monoethanolamine (MEA), which serves as the base case and it is a mature technology available for CO2 capture from exhaust flue gases. From the literature, the optimal amount of solvent is 30 wt% MEA, and this value is used in this analysis.34, 35 In this context, this value is considered the benchmark for much of the research and development in CO2 capture studies.36 The developed NGCC model uses as basis a 2013 report of the United States Department of Energy37; the report provides detailed information on the parameters and performance of the plant that can foster simulations. The capture plant was modelled and modified off literature and the hydrodynamic parameters mentioned earlier.
2 PROCESS DESCRIPTION
In this paper, an NGCC plant of 650 MWe is simulated; the size is identical to that reported in the 2013 US Department of Energy (DOE)/NETL report.37 The model is based on an offsite NGCC power plant located in Greenfield, Midwestern USA. The site is located on a 300 acre of land, which is land locked, hence only access being by rail and the highway.38 Herein, we evaluate the effect of operating the NGCC with varying natural gas compositions with the focus on the CO2 content in the fuel. The downstream effect of the varying fuel composition is also investigated as the exhaust flue gas exits the heat recovery steam generators (HRSG) with different compositions and different temperatures and flowrates which affect the mechanical energy generated in the steam turbines. The fundamental flowsheet of the NGCC is depicted in Figure 1.
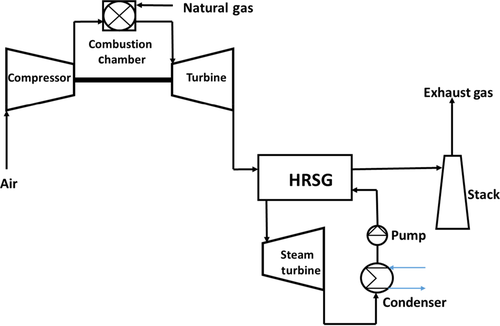
The present study extends from the baseline NGCC to investigate the incorporation of the NGCC and a CO2 capture unit when the NGCC is operating with a range of fuel compositions. When a CO2 capture unit is coupled within the cycle, the thermal energy of the heat recovery system will be affected as some steam is withdrawn from the steam cycle for the heat demand of the capture plant.39 The basic flowsheet of a CO2 capture plant using amines is shown in Figure 2. The flowsheet is comprised of two main columns, namely the absorber and the stripper columns, as well as a cross heat exchanger, coolers, pumps, reboiler and condenser. The process comprises a stream of exhaust flue gas passing through a direct contact cooler (DCC) that goes into the bottom of the packed absorber column, where it comes into contact with a counter current flow of lean amine solvent that enters the top of the absorption column. Thus, the treated gas produced, containing low amounts of CO2, leaves the absorber at the top of the column and will often pass through a water wash column (not shown in Figure 2) to get rid of any entrained amines in the treated gas. The MEA solvent flow exiting the bottom of the absorber column is pre-heated by the cross heat exchanger and, with the use of pumps, the rich solvent flows to the top of the stripper column. This helps reduce the regeneration heat demand for the solvent.38
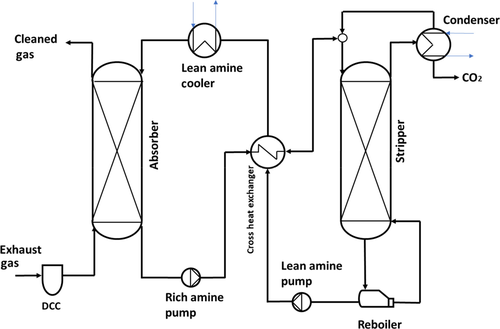
In the stripper (desorber), the solvent rich in CO2 flows downwards and is heated by the steam raised in the reboiler, thus leading to the desorption of the CO2 contained in the rich solvent. This leads to the regeneration of the lean amine solvent. The vapour stream leaving the stripper containing high amounts of CO2, steam and small entrained droplets of MEA is partially condensed in a condenser. The uncondensed CO2 is sent through the processes of drying and compression before being forwarded for CO2 storage, while the other components are condensed and refluxed to the top of the stripper.25
By increasing the CO2 content in the fuel, the LHV of the fuel and the combustion temperature in the combustion chamber will reduce. The reduction of the LHV will cause the operating point of the gas turbine to move towards its stability limit.40 To maintain the same power input in the system, the fuel flowrate increases as the CO2 concentration in the fuel also increases. The specific heat of the flue gas is also expected to increase because of the rise in the CO2 content in the flue gas, which subsequently further reduces the flue gas temperatures. Downstream, the higher flue gas flowrates impacts the CO2 capture plant, which reduces the residence time in the column and may negatively impact on the mass transfer to the solvent, however higher CO2 concentrations entering the absorber column will improve mass transfer rates and may negate this impact. The growth in CO2 concentration within the flue gas would also increase the required capture rate to match the same absolute flowrate of emissions leaving in the clean gas, which may also require the capture plant to operate beyond the 90% capture rate and this is often referred to as the optimum capture specification in the open literature.26
3 METHODOLOGY
Using process modelling, the systems and parameters in this paper were investigated. The modelling approach is analysed as well as the input parameters which need to be specified to determine the required output.
3.1 Modelling approach
The NGCC and CO2 capture plant were modelled using gCCS v1.1.0, a process modelling software package developed by PSE specifically for energy and CO2 capture systems.41 The commercial-scale NGCC power plant design comprises of two state-of-the-art commercial GE 7FA.05 gas turbines, two triple pressure level single reheat type HRSG and a condensing steam turbine with an evaporative cooling tower.37 The HRSG configuration includes high-pressure (HP), intermediate-pressure (IP) and low-pressure (LP) steam drums as well as superheaters, reheaters and economisers. In addition, the steam turbine section includes HP, IP and LP steam turbines with isentropic efficiencies of 88.3%, 92.4% and 90.7%, respectively, and the condenser operating at 5000 Pa.
The compressed air and natural gas are combined in a combustor which is manufactured to produce low NOx emissions at high temperatures. In the turbine, expansion occurs, and the flue gas produced exits the turbine at approximately 604°C (for the 2013 DOE/NETL analysis).37 There is an assumed pressure drop of 5% being simulated across the combustor.27
The gas turbine section has two main parts, namely the compressor section and the turbine section. In the compressor, the pressure ratio and the isentropic efficiencies are specified and the isentropic efficiency and the outlet pressure are the parameters specified for the gas turbine. The pressure ratio is obtained from the 2013 DOE/NETL report37 and the isentropic efficiency is calculated using the provided parameters at nominal operation. A similar procedure is used to calculate the isentropic efficiency for the turbine, while the outlet pressure is provided in the same 2013 DOE/NETL report37 used for the compressor analysis.
The HRSG is initially configured in a calibration mode at which the outlet pressures, temperatures and the heat transfer coefficients are specified in accordance to the 2013 DOE/NETL report.37 These inputs are used to estimate the heat transfer area of each component. The areas are then specified with the system which is then re-configured in an operational mode. The three steam turbines were modelled using a similar methodology as the heat transfer components in the HRSG. The turbines were configured based on the 2013 DOE/NETL report by specifying inlet and outlet states of the turbine at nominal conditions.37 These inputs are used to calculate the isentropic efficiency and stodola’s constant.
The stodola’s constant and isentropic efficiency are implemented to allow the monitoring of off-design conditions of the steam turbines.42 This is because the model has to account for different non-linear behaviours of efficiency, pressure ratios and rotational speeds between steam drums at different operating conditions of steam as mentioned by Dettori el al.43 Therefore, to estimate the steam turbines real behaviour when mass flow and pressure change, the stodola’s Ellipse equation42, 43 is applied.
The fuel and air properties as shown in Appendix A highlight the input conditions for the NGCC. These properties are similar to the NGCC conditions reported in the 2013 DOE/NETL report,37 so as to ensure an unbiased comparison in base case results for validation purposes. The combustion turbine section of the NGCC is modelled with a fixed power output of the system which was set to produce the same power output as the 2013 DOE/NETL report (420.8 MW).37 In the fuel flexibility modelling, the operating fuel is changed from a natural gas composition considered as the base case fuel, as shown in Appendix A, to other high CO2 content fuels. Other inputs such as the air composition are kept constant to examine the impact of the varying fuel compositions on the overall performance of the system.
The fuel composition is changed with the addition of CO2 to the fuel. This is employed to investigate the effect of the change in fuel composition on the operation of the NGCC system, focusing on the HRSG and steam turbine performance. With the addition of CO2 to the fuel, the LHV reduces. In order to accommodate the specified power output in the system, the combustor requires more fuel; therefore, the flowrate of the fuel into the combustor increases. Although there is no change to the air composition entering the compressor, the combustion of the fuel and air changes with increase in the CO2 content in the fuel. This changes the efficiency of the turbine and the compressor and furthermore affects the overall efficiency of the system, however, the change in combustion efficiency is not considered in this study.
3.2 Carbon dioxide capture plant
The CO2 capture plant uses the electrolyte NRTL thermodynamic property package for the liquid phase properties and gSAFT equation of state for the vapour phase properties.26, 41 The exhaust gas from the NGCC goes into a DCC/heat exchanger that reduces the temperature of the exhaust flue gas in order to improve the efficiency of the capture plant. At the entrance of the absorber, the temperature of the exhaust gas is controlled at 40°C.25, 27, 28 The pumps in the system are specified to operate at an efficiency of 75%, with the rich and lean amine pump generating a maximum pressure of 3 bar for the base case with natural gas.26, 27 The CO2 capture plant is configured to achieve a capture efficiency of 90% at its base case scenario, while utilising a solvent concentration of 30 wt% MEA and 70% water. The loading of the lean solvent was set to 0.2 mol CO2/mol MEA.44 The regeneration temperature in the reboiler is set to 120°C, at values higher solvent degradation often occurs,39 and the pressure in the reboiler is set to a value of 1.8 bara.25, 28 To supply some of the necessary hot steam to the reboiler, a fraction of the steam entering the LP turbine is extracted after leaving the IP steam turbine section. The steam is redirected to the reboiler, which is used to supplement the solvent regeneration process. The saturated steam exiting the reboiler is sent back into the steam cycle via the condenser.28 The steam draw off from the IP/LP turbine crossover was also recommended from literature.45 As a result of the reduced steam flow with the LP turbine, the power generated by the steam turbines is reduced. This in turn affects the overall steam turbine power and efficiency when CO2 capture is retrofitted into the system.
In designing the columns for the CO2 capture plant, the optimum geometry, that is, diameter and height, of the absorber and stripper columns had to be determined based on the hydrodynamic parameters, the capture rate and specific reboiler duty at a chosen packing type and solvent concentration.26 The packing type used in this process model is the structured packing Mellapak 250 Y, characterised by its specific surface area of 250 m2/m3 and a 45° angle of orientation to the vertical axis.46, 47 This packing type was chosen because of its high efficiency and low pressure drop. The mass transfer coefficients used to calculate the hydrodynamic parameters were estimated using the Billet and Schultes48 correlation.
For an optimum design of the system, we use two and one absorber and stripper columns, respectively. This design is based on the column cost and the heat requirement associated with the capture system.38 Hence, the minimum number of columns is chosen with the aim of obtaining a balance between a higher capital and operating cost and a reduced heat requirement in the system.
Using two absorber columns also provide greater operational flexibility when operating with flexible fuel scenarios.28 In addition, Lawal et al38 suggested that employing more than one absorber column could enhance the turndown ratio in processing large volumes of flue gas from the power plant.
The operating region of the packed columns is determined by its hydrodynamic parameters, the maximum pressure drop tolerated in the column and the maximum flooding velocity of the column.25, 26 At the flooding point, the pressure drop due to the gas flow increases to an extent at which the solvent cannot flow downwards in a counter-current manner against the gas flow.38 At this point, the area of the packing surfaces that are wetted is reduced and thus affecting the operation of the columns.38 At higher flue gas flowrates entering the absorber, the columns become more liable to reaching the flooding point and becoming inoperable.
The absorber column diameter is designed to operate at 80% of the flooding point for the base case scenario.25, 27, 28 The absorber height was determined by adjusting the packing height manually until 90% CO2 capture efficiency is achieved in the absorber column. With increase in packing height, there is increase in mass transfer area which improves the absorption of CO2. With columns that are higher than 18 m, the increase in efficiency of the plant is negligible and hence considered insignificant in this analysis. Also, the high cost incurred with longer absorbers was not considered feasible in this study.8 A similar criterion is employed to calculate the stripper column diameter, whilst the specific reboiler duty in the system is reduced to increase the stripper height. This was done in order to determine the extent to which there was a negligible reduction of less than 1% of the specific reboiler duty while increasing the stripper height. The packing height of the absorber column was 17.10 m and for the stripper column it was 30.27 m. While the columns diameter for the absorber column was 16.32 m and for the stripper column, it was 8.90 m.
The design of the CO2 capture system uses as basis the technical specifications presented in Appendix B. Some parameters in the system are kept constant while the changes in the rest due to the changes in fuel composition have been reported. The parameters kept constant were the solvent lean loading, the CO2 concentration of the treated gas exiting at the top of the absorber, the cross heat exchanger pressure drop and heat transfer area, the pump efficiencies and the reboiler pressure and temperature.
The mass flowrate of emitted CO2 exiting the top of the absorber is kept constant while varying CO2 concentrations in the fuel. This results in the required CO2 capture rate increasing across the cases; however, it allows for consistent analysis, whereby the plants are expected to produce a treated gas with low CO2 emissions. The constant CO2 concentration leaving the top of the absorber ensures there is no increase in emissions in the different cases, highlighting the impact of the study on the mitigation of greenhouse gas emissions.
4 RESULTS AND DISCUSSION
4.1 Base case analysis
The base case simulation results obtained for the analysis in this study are summarised in Table 1. The results are shown to be in close accordance with the published values in the 2013 DOE/NETL report.37 The auxiliary power for the pumps and other systems are determined by the gCCS software. The data shown in Table 1 highlight the comparison of the data derived from the standalone NGCC power plant and the effect of coupling the NGCC to the CO2 capture unit. The model was built in a similar way to the DOE report to ensure unbiased comparison in data. Modelling of the CO2 capture system was carried out according to the flue gas obtained from the NGCC operating with the base case fuel composition. This was to ensure the capture plant was sized to operate at optimum performance.
Standalone NGCC | 2013 DOE/NETL37 | gCCS model |
---|---|---|
Input | ||
Natural gas flowrate (kg/s) | 23.38 | 23.38 |
Gas turbine power (MWe) | 420.82 | 420.82 |
Output | ||
Air flowrate (kg/s) | 1006.34 | 1006.32 |
Steam turbine power (MWe) | 229.61 | 229.59 |
Total gross power output (MWe) | 650.42 | 650.41 |
Power plant auxiliaries (MWe) | 16.53 | 15.81 |
Total net power output (MWe) | 633.89 | 634.60 |
Net power plant efficiency (%) | 57.4 | 57.51 |
NGCC with CO2 capture plant | 2013 DOE/NETL37 | gCCS model |
---|---|---|
Steam turbine power (MWe) | 185.50 | 176.06 |
Total gross power output (MWe) | 606.32 | 596.88 |
Power plant auxiliaries (MWe) | 53.5 | 49.95 |
Total net power output (MWe) | 552.82 | 546.92 |
Net power plant efficiency (%) | 50.1 | 49.56 |
The results show that the steam turbine power reduces when the CO2 capture plant is introduced. This is due to the CO2 capture plant that extracts some steam from the IP/LP crossover from the steam turbine section, causing a decrease in the thermal energy in the steam turbine sections. As the steam turbine power reduces the total gross power output reduces. Regarding the auxiliary power in the system, there is an observed increase in this value. An integrated CO2 capture plant means there is more energy requirement in the overall system, such as the CO2 plant auxiliary pumps and the CO2 compression turbine. This increase in auxiliary power causes a reduction in the net power plant output and reduces the net power plant efficiency.
Comparing the results obtained in the model to the 2013 DOE/NETL report,37 there is strong agreement. The values reported here are all within a 5.1% of the reference report. The major deviations occurred in the NGCC coupled with CO2 capture case. This can be attributed to the fact that the dimensions for the CO2 capture plant used in this study are not similar to the 2013 DOE/NETL report and other publications using a similar NGCC process schematic, although employing similar parameters to obtain its dimensions. The sizing of the columns were higher to account for the increase in mass transfer and packing area in the columns which is necessary to operate with higher amounts of CO2 in the flue gas with an acceptable CO2 capture performance such as a low reboiler duty and capture rate of around 90%. This leads to an increase in steam drawn off from the steam turbines since higher amounts of thermal energy are required for solvent regeneration. Thus, the model having a lower steam turbine power output compared to the 2013 DOE/NETL report.37
4.2 Fuel flexibility analysis
The effect of varying the CO2 concentrations in the fuel is extensively examined with the modelling of the increased CO2 content in the fuel. The concentrations being examined are 5%, 7.5% and 10% CO2 in the fuel. The compositions of the fuels used in the analysis are shown in Table 2. The four fuel compositions are derived from the base case natural gas composition used in the 2013 DOE/NETL report.37 The compositions of the others fuels are derived from adding CO2 into the base case natural gas. This was repeated for all the examined CO2 concentrations (5%, 7.5% and 10%). Since the CO2 concentration increases, the concentrations of the hydrocarbons and the nitrogen reduce.
Natural gas | 5% CO2 | 7.5% CO2 | 10% CO2 | |
---|---|---|---|---|
Methane (mol%) | 93.1 | 89.3 | 86.9 | 84.6 |
Ethane (mol%) | 3.2 | 3.1 | 3 | 2.9 |
Propane (mol%) | 0.7 | 0.7 | 0.7 | 0.6 |
Butane (mol%) | 0.4 | 0.4 | 0.4 | 0.4 |
Nitrogen (mol%) | 1.6 | 1.5 | 1.5 | 1.5 |
Carbon dioxide (mol%) | 1 | 5 | 7.5 | 10 |
Lower heating value (MJ/kg) | 47.20 | 42.60 | 40.00 | 37.60 |
The results obtained from the modelling of the varying fuel compositions in the NGCC with CO2 capture is depicted in Table 3. The major process variables investigated are the steam turbine power output, auxiliary power, power plant output, turbine inlet temperature (TIT), CO2 capture efficiency, turbine outlet temperature (TOT), the reboiler duty and the flooding ratio in the columns.
Parameters | Natural gas | 5% CO2 | 7.5% CO2 | 10% CO2 |
---|---|---|---|---|
Fuel flowrate (kg/s) | 23.38 | 25.88 | 27.55 | 29.32 |
Gas turbine power output (MWe) | 420.82 | 420.82 | 420.82 | 420.82 |
Steam turbine power output (MWe) | 176.06 | 174.43 | 173.45 | 172.49 |
Total gross power output (MWe) | 596.88 | 595.25 | 594.27 | 593.30 |
Auxiliary power (MWe) | 49.95 | 50.45 | 50.73 | 50.99 |
Total net power plant output (MWe) | 546.92 | 544.80 | 543.54 | 542.32 |
Net power plant efficiency [LHV] (%) | 49.56 | 49.42 | 49.32 | 49.20 |
Turbine inlet temperature (°C) | 1271 | 1268 | 1267 | 1265 |
Turbine outlet temperature (°C) | 606.63 | 605.37 | 604.53 | 603.65 |
Flue gas temperature (°C) | 93.19 | 87.76 | 84.56 | 84.51 |
CO2 capture rate (%) | 90 | 90.4 | 90.6 | 90.8 |
O2 concentration in flue gas (mol%) | 12.37 | 12.36 | 12.33 | 12.3 |
CO2 concentration in flue gas (mol%) | 3.91 | 4.06 | 4.15 | 4.26 |
Flue gas flowrate (kg/s) | 1029.7 | 1032.2 | 1033.89 | 1035.66 |
Solvent rich loading (mol CO2 /mol MEA) | 0.471 | 0.472 | 0.473 | 0.474 |
As shown in Table 3, with the CO2 concentration in the fuel increasing, the LHV of the fuel decreases. This leads to an increase in the fuel flowrate entering the system. Hence, the overall combination of fuel and air into the gas turbine increases and also an increase in the flue gas flowrate exiting the system.
When operating with higher CO2 content fuels, the temperatures across the turbine are seen to reduce, specifically the TIT and the TOT. This is because the air-fuel ratio is seen to reduce as the mass flowrate of the air is constant whilst the flowrate of the fuel increases due to the reduction of the LHV. This would lead to an increase demand in excess air, however, in the model, the excess air is not observed to increase, hence causing reduction in the combustion outlet temperature which is the TIT. In addition to the TIT reducing, the TOT also reduces as a result of a lower temperature combustion gas being used for turbine expansion.
By introducing the CO2 capture unit, the power produced in the steam turbine reduces due to some energy generated being utilised to regenerate the amine solvent in the capture plant. With the introduction of CO2 in the fuel, the steam turbine power reduces even further. As shown in Table 3, the flue gas temperature exiting the HRSG reduces with increase in CO2 content in the fuel. This is because the introduction of CO2 reduces the LHV of the fuel and with its increase in concentration, the combustion temperature reduces, and hence reduces both TIT, TOT and steam turbine power output.
The three pressure sections in the steam turbine area are the HP, IP and LP sections. As explained earlier in the modelling methodology, the parameters used to configure the steam turbine sections are the isentropic efficiency and the stodola’s constant. These parameters access the operational flexibility of each section of the steam turbine as the outlet temperatures, mass flow and pressures vary according to the input of the system.
The results in Table 3 show that the increase of the CO2 content in the fuel cause a reduction in the power generated in the steam turbine. Increasing the CO2 concentration and flowrate of the flue gas entering the HRSG, there is an observed increase in thermal input into the steam turbines. With increase in CO2 concentration at absorber inlet, more steam is extracted from the IP/LP crossover to the reboiler for desorption. This is due to the higher solvent flowrate and the increase in required CO2 capture rate despite the increase in CO2 partial pressures. Thus, the thermal duty required by the capture plant increases which increases the thermal consumption from the steam turbines. This causes the LP section of the steam turbine section to have less steam energy being sent to the generators, hence reducing the steam turbine power output.
4.3 CO2 capture plant analysis
The liquid/gas (L/G) ratio also has an important effect on the performance of the CO2 capture unit. As exposed in Figure 3, the L/G ratio increases with the increase in the fuel CO2 concentration. The L/G ratio increases due to increase in the flowrate of the flue gas into the absorber, hence leading to a proportionally higher solvent flowrate being required for absorption. At higher flue gas flowrates and higher CO2 concentrations in the flue gas, with a constant lean loading, the CO2 capture rate increases in the column which implies that the CO2 concentration in the rich loading leaving the absorber will also increase.
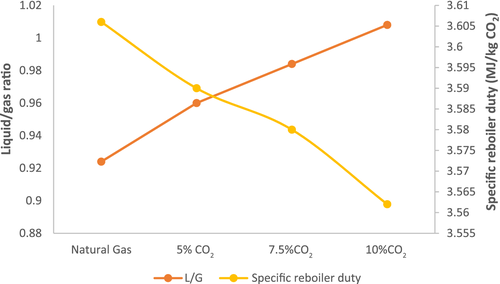
The reboiler duty also plays an important role in the techno-economic performance of NGCC power plants with CO2 capture.49 The relationship between the L/G ratio and the specific reboiler duty in the CO2 capture system is depicted in Figure 3. At a low L/G ratio, the specific reboiler duty is high. This observation is validated by models developed by Cifre et al8 and experiments performed by Akram et al.50 At a higher L/G ratio, the solvent flowrate is increased to capture the required CO2 from the flue gas. However, the energy required for regeneration per kg of CO2 decreases because there is more CO2 in the rich solvent and the CO2 is being stripped more efficiently. The increase in the L/G ratio leads to an increase in the flooding velocity in the column. Although it is desirable and practical to operate the columns as close to flooding as possible so as to enhance the interfacial mass transfer characteristics in the column,51 however, increasing the L/G ratio in the system also relates to the column approaching the flooding point. This causes the operation of the CO2 capture plant to go beyond the optimal operation for CO2 absorption. Beyond this point, there is an observed rapid increase in pressure drop in the column, liquid carryover from the top of the column and instability in the column.46
4.4 Techno-economic assessment

Parameter | Value | Unit |
---|---|---|
Capacity factor | 85 | % |
Capital charge factor with CCS | 11.1 | % |
Total as spent cost factor | 107.8 | % |
CO2 transport and storage cost over 100 km | 10 | $/tonne CO2 |
Plant operational period | 30 | Years |
Cost year | 2018 | - |

4.4.1 Capital cost
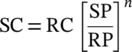
Plant component | Scaling parameter | Reference cost ($1000) | Scaling exponent |
---|---|---|---|
Feed water system and miscellaneous | Feed water flowrate (HP only) | 55 815 | 0.72 |
CO2 removal | CO2 flowrate at absorber inlet | 276 219 | 0.61 |
CO2 compression | CO2 flowrate | 36 887 | 0.77 |
HRSG, ducting and stack | HRSG duty | 55 503 | 0.7 |
Steam turbine system | Steam turbine power | 66 914 | 0.8 |
Cooling water system | Cooling tower duty | 26 192 | 0.71 |
Instrumentation and control | Net auxiliary power | 19 460 | 0.6 |
Improvements to site | Gross total | 12 025 | 0.47 |
Accessory electric plant | Net auxiliary power | 62 528 | 0.6 |
Buildings and structures | Gross total | 13 117 | 0.34 |
The scaling cost of the different plant components are based on the operational data obtained in the plant modelled in gCCS and compared to the reference case in the 2013 DOE report.37 The scaled costs are then added up to obtain the TPC, which is the overall cost of the plant. The TOC of the plant is the calculated from the TPC and other costs which are considered in the construction of the plant. The other costs and their basis of estimation are tabulated in the Appendix C. The operating expenditures of the plant are discussed in Section 4.3.2, where the basis used to estimate the fixed and variable operating costs is highlighted.
4.4.2 Operating cost
As shown in Equations (1) and (2), the COE is calculated from the TOC, OCFIX and OCVAR, and the COA is calculated from the COE. In calculating the OCFIX and OCVAR, there are other costs to be considered which are tabulated in Table 6. The estimation method is further explained elsewhere.53 Using the estimation method highlighted in Table 6, the O and M cost were calculated for the varying CO2 concentrations in the fuel.
Operating and maintenance cost (O & M) | |
---|---|
Cost | Estimate basis |
Variable operating cost (OCVAR) | Maintenance material cost (1.3% TPC CF) |
Non-fuel consumables (1.5 maintenance material cost – 1.3% TPC CF) | |
Fixed operating cost (OCFIX) | Property taxes and Insurance (0.02 TPC) Operating labour rate ($347 772/y) Operating labour burden (0.3 operating labour rate) Operators per shift (6.3) Number of shifts (4) |
Annual operating labour cost (operating labour rate x operating labour burden x operators per shift x number of shifts) | |
Maintenance labour cost (2/3 maintenance labour cost) | |
Admin and support labour (0.25 sum of other labour cost) | |
Fuel cost (FC) | 5.81 $/GJ HHV |
4.4.3 Costing results
The TPC was assumed to be constant for all scenarios with increasing the CO2 fuel content. This is because the changes in fuel compositions are expected to have a negligible effect on the cost of construction of the plant (both the NGCC and the capture plant). The results shown in Table 7 highlight the TPC difference between the model developed in gCCS and the reference case in the 2013 DOE/NETL report. The primary difference in the TPC is mainly due the use of a different CO2 capture plant in the gCCS model,28 compared to the 2013 DOE/NETL report. It is observed that the main variations that occur are in the cooling systems connecting the steam turbine to the capture plant. As previously stated, the key assumption in this work is the constant plant size used in this analysis and thereby the TPC is kept constant for all varying CO2 concentrations in the fuel. The total overnight cost is also seen to be constant for increasing CO2 concentration in the fuel. This is mainly due to constant TPC which is used as an estimate basis for majority of the cost components considered in the total preproduction cost, working and inventory capital, land, as well as initial cost for catalysts and financing costs as shown in the Appendix C.
Ref case (no CO2)37 | Natural gas (no CO2) | 5% CO2 | 7.5% CO2 | 10% CO2 | |
---|---|---|---|---|---|
Total plant cost ($) | 758 709 | 751 765 | 751 765 | 751 765 | 751 765 |
Other costs ($) | 166 763 | 165 274 | 165 274 | 165 274 | 165 274 |
Total overnight cost ($) | 925 472 | 917 039 | 917 039 | 917 039 | 917 039 |
Operation and maintenance cost ($/y) | 229 115 | 228 846 | 228 846 | 228 846 | 228 846 |
CO2 transport and storage ($/MWh) | 3.65 | 3.65 | 3.82 | 3.93 | 4.05 |
COE ($/MWh) [with CO2 T&S] | 84.27 | 83.98 | 84.15 | 84.26 | 84.37 |
COA ($/tonne CO2) | 86.59 | 85.85 | 82.63 | 80.62 | 78.60 |
As depicted in Table 7, higher CO2 concentrations fuel increases the COE and reduces the COA. The COE increases mostly due to the increase in the CO2 transport and storage cost due to the higher CO2 flowrate being sent for compression and storage. While the COA, which is costed per unit of CO2 captured, as the partial pressures of CO2 within the flue gas increases, the capture plant’s efficiency per unit of CO2 increases and it becomes cheaper to avoid the emissions.
The use of fuels with high CO2 content will incur higher COE prices; however, this is marginally offset by the increase in the capture efficiency of the CO2 capture plant, which makes CCS more applicable when fuel flexibility is desirable. However, due to the observed approach of the amine solvent to flooding point in the columns, CO2 concentrations in the fuel higher than 10% will result in the capture plant failing. To counter this, when operating with CO2 content fuels higher than 10 mol%, a taller absorber and stripper column will be necessary to increase the residence time in the columns and also ensure that the appropriate capture efficiency is achieved.
5 CONCLUSIONS
The present study has performed a fuel flexibility analysis on a NGCC integrated with CCS. The fuel compositions investigated involved the use of natural gas with increasing CO2 concentrations. The results from this study highlight the impact of operating natural gas as a fuel with increasing CO2 content in a NGCC with CCS on the associated capital and operating costs with such an operational flexibility. The NGCC without the capture plant produced a gross power output of 650 MW and with the capture plant this reduced by 8.3% to 597 MW. When operating with higher CO2 content fuels, the power output reduces because of the increase in steam extraction form the IP/LP crossover to the reboiler for amine regeneration. Other parameters affected are the temperatures across the system (TIT and TOT) which are seen to reduce. This is due to the air-fuel ratio reducing, causing the combustion temperature to decrease.
The model calculates that the COE with T&S for the natural gas scenario is 83.98 $/MWh, which increases up to 84.37 $/MWh for the 10% CO2 concentration in the fuel. While the COA reduces from 85.85 $/tonne CO2 in the natural gas scenario to 78.6 $/tonne CO2 for the 10% CO2 concentration in the fuel, it was also revealed that operating with higher CO2 content fuels the velocities in the absorber and the stripper increase towards the flooding point, at which point the plant will be inoperable. To avoid this, a taller absorber and stripper column will be necessary.
The results from this study show that a NGCC power plant with CCS can be easily operated with fuels with lower LHV in scenarios where cheaper fuels are needed for combustion. This will have no effect on the TPC and the operation and maintenance cost, but will increase the T&S for the CO2 by 4.7%, 7.7% and 10.8% for the 5%, 7.5% and 10% CO2 concentrations in the fuel, respectively. Also, the cost of the CO2 avoided will decrease by 3.7%, 6.1% and 8.4% for the 5%, 7.5% and 10% CO2 concentrations in the fuel, respectively. The reduction in COA indicates the lower efficiency losses in the CO2 capture system, because of the rise in the CO2 concentration in the flue gas, outweighing the negative effect of the cost increase in the transport and storage of the CO2. This highlights an important trade-off in operating the NGCC with different fuel compositions. Furthermore, whilst some mild variations in the CO2 content in the fuel can be easily tolerated, and are somewhat beneficial in the operation of the capture plant, it should be noted that above a limit of 10 mol% of CO2 in the fuel, design modifications will have to be implemented to the capture plant. This is to ensure an efficient operation of the system.
ACKNOWLEDGEMENT
The authors would like to acknowledge the Energy 2050 group at the University of Sheffield and the UKCCSRC (UK Carbon Capture and Storage Research Centre).