Solar-thermal driven drying technologies for large-scale industrial applications: State of the art, gaps, and opportunities
Funding information: European Commission, Grant/Award Number: 731287; Orta Doğu Teknik Üniversitesi
Summary
Research and Innovation (R&I) on Large-scale Industrial Solar-thermal driven Drying technologies (LISDs) is one of the strategies required to transition to a low-carbon energy future. The objective for this work is to guide future R&I on LISDs by defining the state of the art, gaps, and opportunities. To provide a high-level perspective on the current state of solar drying research, results are presented from an analysis of the content relevant to LISDs found in 45 solar drying Review Articles published in journals over the past 25 years. A conclusion is that most of the existing solar drying research is not focused on LISDs. To build-on these existing 45 solar drying Review Articles, results are presented from an analysis of 30 Original Research Articles with significant content relevant to LISDs published over the past 5 years. A gap is identified in coupling existing or slightly modified solar thermal collectors with existing or slightly modified industrial drying technologies to create indirect LISDs. To facilitate formulating new coupling strategies, the drying characteristics most relevant to this coupling are described and four fundamental classes of industrial dryer technologies are defined based on the underlying heat transfer mechanism, which then impacts the appropriate collector choice. At their most fundamental level, many of the technologies needed to couple solar collectors and industrial dryers to create novel indirect LISDs are not unique to indirect LISDs, but rather can be generalized across a wide range of Solar Heat for Industrial Processes (SHIP) applications, and integration issues are discussed at a more fundamental SHIP level. The technical and economic characteristics of 19 existing LISDs installations throughout the world are presented, and potential and emerging areas discussed.
Abbreviations
-
- BG
-
- bulk gas
-
- CPC
-
- compound parabolic collector
-
- ETC
-
- evacuated tube collector
-
- FPC
-
- flat plate collector
-
- HB
-
- heated base
-
- HP
-
- heat pump
-
- HTF
-
- heat transfer fluid
-
- IB
-
- insulated base
-
- IC
-
- insulated cover
-
- LF
-
- linear Fresnel collector
-
- LISD
-
- large industrial solar dryer
-
- MM
-
- moist material
-
- MMBGI
-
- moist material-bulk gas interface
-
- PTC
-
- parabolic trough collector
-
- PV
-
- photovoltaic
-
- SD
-
- solar dryer (or solar-thermal driven dryer technologies)
-
- TES
-
- thermal energy storage
-
- UB
-
- uninsulated base
-
- UC
-
- uninsulated cover
1 INTRODUCTION
Solar-thermal driven drying technologies, herein referred to as Solar Dryers (SD) for brevity, includes both large-scale SDs for industry, termed Large Industrial SDs (LISDs) herein, and small-scale SDs for small-scale industrial and non-industrial applications, termed small-scale SDs herein. LISDs are a critical part of the rapidly emerging field of Solar Heat for Industrial Processes (SHIP) that encompasses a wide range of industrial processes. Currently, global SHIP markets are small but have large growth potentials. Growing these SHIP markets has several important societal benefits including (1) increasing energy security for countries with large energy imports; (2) contributing to sustainable economic growth; and (3) contributing to the transition to a low-carbon energy future. To capitalize on these potentials, 28 research institutes in 10 countries are working to develop a European Common Research and Innovation Agenda (ECRIA) on SHIP through the INSHIP project (www.inship.eu). One of the objectives for this ECRIA on SHIP is to benefit society by catalyzing and growing European and global LISDs capacities and markets. Within Europe and across other industrialized countries, a large fraction of industrial heat is used for large-scale industrial drying processes that span a wide and diverse range of sectors. Specifically, while industrial drying consumes 20%-25% of national energy consumption for Denmark and Germany, and 10%-15% of national energy consumption for France, the UK, the US, and Canada,1 the market uptake of solar thermal driven industrial dryer technologies is negligible. This article is an outcome of an exercise to assess the current state of the art for LISDs, and identify important technological gaps and opportunities that can be targeted through this ECRIA.
The remainder of this article is organized as follows. A clear distinction is made between Original Research Articles that present new knowledge, and Review Articles that compile and synthesize content from a large number of Original Research Articles. The current state of the art for LISDs is defined and associated technological gaps are identified based on a comprehensive review of 45 SD review articles published in journals over the past 25 years (Section 2) and a targeted review of 34 original solar drying research articles with content relevant to LISDs published over the past 5 years (Section 3). LISDs are just one small subset of industrial dryers, and a goal for this article is to facilitate the identification of new opportunities to drive industrial drying processes using solar thermal energy. To this end, a very brief introduction to the vast industrial dryer literature is provided in Section 4 and a very high-level synthesis of ideas found in the existing SD and Industrial Drying literature are presented in Section 5. One of the main technological barriers to market uptake of LISDs is the proper integration of solar thermal into the drying process to yield reliable and cost-effective operation, and integration issues are addressed in Section 6. In Section 7 the technical and economic characteristics for 19 existing LISDs from throughout the world are summarized, and a sample set of industrial opportunities that could potentially benefit from novel LISDs are presented. Conclusions are presented in Section 8.
2 REVIEW OF EXISTING SD REVIEW ARTICLES
- Metadata: Details such as the full title of the article, journal in which the article was published, and so on, are available in the References section of this article and are not included in Table 1 for conciseness. Within the broad area of SDs, the scope of the review articles varied significantly, and the shortened title of the review article provides important information about the scope of each article. The Year in which the article was published indicates that the rate at which SD review papers were published increased significantly starting in 2009, with 84% (38 of the 45) of the review articles being published in the last 10 years. The Authors' Country indicates that most of the review articles were written by researchers in South East Asia in general, and Malaysia and India specifically, followed by the Middle East, and Africa. In contrast, the participation of researchers from developed economies is rare, which is consistent with the general finding that most SD research focuses on at least simple and often small-scale SDs most appropriate for personal use, rural applications, and/or small-industrial applications in less-developed communities. The number of references (No. Refs.) provides information on the breadth of the literature review while the number of Citing Articles is based on Scopus and provides information on the relative impact of different articles, where of course older articles are expected to have more citations.
- Applications: Most SD research has focused on (1) agro-food, (2) marine, and (3) wastewater (WW) sludge applications, with the vast majority being specifically focused on agro-food applications. The research for agro-food and marine applications has tended to focus on small-scale SDs, while that for waste-water applications tends to be for simple but potentially larger-scale industrial SDs.
-
Technologies: Direct and Indirect SDs are the two most common classes of SDs. In Direct SDs, the product is directly exposed to solar radiation, which necessitates that the solar collector and dryer be one integral unit. In contrast, in Indirect SDs the product is not directly exposed to solar radiation but rather the collector and dryer are separate units that are thermally coupled using a Heat Transfer Fluid (HTF). Direct SDs tend to be simpler and more appropriate for lower temperature applications. One example of a direct LISD is a large greenhouse dryer. In contrast, indirect SDs tend to be more complex due to having separate collector and dryer units, but this complexity can enable several benefits important to LISDs including higher temperatures, better thermal control, higher availability, and greater design flexibility as detailed below. A high-level assessment of these articles led to the conclusion that the gaps, needs, and opportunities for Research and Development (R&D) on indirect LISDs is larger than that for direct LISDs, and therefore the content analysis presented in the Technologies columns in Table 1 is focused on facilitating R&D on indirect LISDs. These Technologies columns are roughly ordered from thermal energy source (ie, solar collector) to thermal energy end-use (ie, dryer) with supporting details as follows:
- Collectors: The collector and dryer units in an indirect SD have very different thermal objectives. The separation of these units in indirect SDs can allow each unit to be optimized independently, which can enable higher drying temperatures, better thermal control, and greater flexibility in locating each unit. A wide range of collector technologies exist ranging from simple non-tracking and non-concentrating flat plate collectors to concentrating collectors that require 2-axis tracking, and in general the complexity of the collector increasing as the desired outlet temperature increases. In Indirect SDs the collector must be thermally matched to the dryer in terms of both operating temperature and HTF, and the best type of collector for an indirect SD varies with the requirements of the drying unit. Of particular significance,44 published in 2018 contains a comprehensive review of solar collector technologies for SHIP applications while46 published in 2019 contains a comprehensive review of flat plate air collectors for SDs.
- Hybridization, Electric Heaters, and Thermal Energy Storage (TES): One barrier to the market uptake of LISDs is that the thermal output of solar collectors varies with variations in solar resources, and therefore varies hourly, daily, and seasonally. Increasing the availability of indirect LISDs through hybridization with another thermal energy source (eg, combustion), the use of electric heaters, and TES can therefore facilitate greater market uptake of LISDs.
- PV: SDs are narrowly defined herein as using solar thermal energy as the primary energy input. However, many SDs in general and indirect LISDs in particular also have parasitic electrical loads, such as for pumps and blowers. PV systems can be integrated into SDs to drive these parasitic electrical loads to support the rapidly emerging goal of 100% renewable energy industrial processes.
- Heat Pump, Dehumidification and Desiccant Technologies: R&D on SDs that use heat pump, dehumidification, and desiccant technologies to increase performance is increasing rapidly, and these trends are largely mirrored in the (non-solar) industrial drying literature.
-
Assessment: The following categories were defined to differentiate the methods used to quantify the thermal and economic performance of SDs in the different articles.
- Modeling refers to energetic, exergetic, and economic modeling based on mathematical models. Articles strong in this area may contain content on the underlying mathematical models and/or discuss the use of and associated results from packaged simulation software.
- Experiments refers to experimental work. Articles strong in this area typically have one or more of the following: (1) at least one section dedicated to summarizing experimental work; (2) experimental data presented in graphical and/or tabular form; and/or (3) content on experiments to characterize basic drying phenomena.
- Performance Evaluation and Testing (PE&T) refers to the standardization of methods and metrics to evaluate and compare the performance of SD components and systems. Articles strong in this area typically contain significant content on one or more of the following: (1) standard experimental methods to assess performance; (2) standard mathematical expressions/parameters to quantify performance; (3) table(s) comparing the performance of different SD components and/or systems.
- Economic Applications refers to assessing the economic feasibility of SDs for specific applications. Papers strong in this area typically present cost figures for SDs and/or compare different types of SDs in terms of cost.
- Recommendations: Most recommendations can broadly be classified as (1) Research recommendations corresponding to research gaps and opportunities and (2) Application recommendations corresponding to opportunities to apply existing technologies in practice, such as promising locations and/or applications.
- Type/region of applications; Collectors; and so on: The information in this column were deemed important but too diverse to concisely communicate in separate columns.
Metadata | Application | Technologies | Assessment | Recom. | Other Comments | ||||||||||||||||||||
---|---|---|---|---|---|---|---|---|---|---|---|---|---|---|---|---|---|---|---|---|---|---|---|---|---|
Shortened title of review article (SD = ~Solar Dryer or similar; TES = Thermal Energy Storage; HP = Heat Pump) | Agro-food | Marine | WW Sludge | Other | Collectors | Hybrid | Elec. heater | TES | PV | Heat pump | Dehum/desiccant | Modeling | Experiments | PE&T1 | Econ. app'l | Type/region of applications; Collectors; Etc. | |||||||||
Reference | Year | Authors' country | No. Refs | Citing articles | Energetic | Exergetic | Economic | Research | Applications | ||||||||||||||||
2 | SD systems & their testing procedures | 1994 | India | 71 | 40 | ++ | ++ | ++ | ++ | ++ | ++ | ++ | + | Flat plate collectors | |||||||||||
3 | SD systems I: Drying principles & theory | 1999 | Nigeria | 29 | 100 | ++ | ++ | ||||||||||||||||||
4 | SD systems II: Solar drying technology | 1999 | Nigeria | 136 | 224 | ++ | + | ++ | Rural farms in developing countries | ||||||||||||||||
5 | SD systems III: Low temp. Air-heating solar collectors for crop drying | 1999 | Nigeria | 15 | 69 | ++ | ++ | + | + | ++ | Flat plate collectors | ||||||||||||||
6 | R&D work on SD for grapes | 2002 | India | 21 | 114 | ++ | + | + | |||||||||||||||||
7 | Comprehen. proc. for perf. Eval. of SD for food | 2002 | Thailand | 79 | 123 | ++ | ++ | ++ | |||||||||||||||||
8 | Low-cost drying methods for devel. Countries | 2003 | Singapore | 28 | 104 | ++ | + | ++ | ++ | Rural farms & small-scale factories in developing countries | |||||||||||||||
9 | SD systems | 2009 | Taiwan | 77 | 184 | ++ | + | + | + | + | Rural farms & small-scale factories | ||||||||||||||
10 | SD technologies, models & exp. Investigations | 2009 | India | 60 | 78 | ++ | + | ++ | ++ | ++ | Small-scale drying in Asia-Pacific region | ||||||||||||||
11 | SDs developed for grape drying | 2009 | India | 42 | 52 | ++ | + | + | + | + | Grape drying on normal scale | ||||||||||||||
12 | Sol. assisted HP drying for ag. & marine prod. | 2010 | Malaysia | 137 | 55 | ++ | ++ | ++ | ++ | ++ | |||||||||||||||
13 | SD for ag. & marine products | 2010 | Malaysia | 111 | 152 | ++ | ++ | ++ | ++ | ++ | ++ | ++ | ++ | ++ | |||||||||||
14 | SD with TES for drying agro-food products | 2010 | India | 59 | 73 | ++ | ++ | ++ | Small-scale drying in developing countries & India | ||||||||||||||||
15 | Solar air collectors with TES units | 2011 | Malaysia | 122 | 91 | ++ | ++ | ++ | + | Greenhouse, Integrated collector with storage, & flat plate collectors | |||||||||||||||
16 | SD with latent heat TES for ag. products | 2011 | India & Canada | 39 | 40 | ++ | ++ | ||||||||||||||||||
17 | SD experiences in Algeria & design aspects | 2011 | Algeria | 51 | 14 | ++ | ++ | + | + | ++ | + | Algeria | |||||||||||||
18 | HP systems for drying application | 2011 | Malaysia | 106 | 45 | ++ | ++ | ++ | |||||||||||||||||
19 | Solar drying | 2011 | Greece | 137 | 106 | ++ | ++ | + | + | ++ | + | Flat plate, finned, V-corrugated, V-groove, & evac. Tube collectors | |||||||||||||
20 | Adv. in solar assisted chemical HP dryer for ag. produce | 2011 | Malaysia | 93 | 28 | ++ | ++ | ++ | ++ | ||||||||||||||||
21 | Solar drying technologies | 2012 | India & Croatia | 176 | 116 | ++ | + | + | ++ | Developing countries | |||||||||||||||
22 | Solar drying of agricultural products | 2012 | Saudi A. & Egypt | 108 | 90 | ++ | ++ | + | + | Flat plate, finned, packed bed & V-groove collectors | |||||||||||||||
23 | State of the art on solar drying technology | 2012 | India | 68 | 10 | ++ | + | + | + | ||||||||||||||||
24 | Solar drying of wastewater sludge: A review | 2012 | Algeria | 37 | 59 | ++ | + | ++ | + | ||||||||||||||||
25 | Historical review & recent trends in SD systems | 2013 | India | 93 | 67 | ++ | + | + | + | + | + | Small scale factories and rural farming | |||||||||||||
26 | Exergy anal. of drying processes & systems | 2013 | Iran | 120 | 87 | ++ | ++ | ++ | ++ | + | ++ | ++ | |||||||||||||
27 | Fund. aspects of SD of wastewater sludge | 2013 | Belgium & France | 61 | 84 | ++ | ++ | ||||||||||||||||||
28 | Solar greenhouse drying | 2014 | India | 36 | 54 | ++ | + | ++ | South-east Asia | ||||||||||||||||
29 | Development of solar drying applications | 2014 | Malaysia & UAE | 114 | 62 | ++ | ++ | ++ | ++ | + | ++ | ++ | Flat plate, evac. Tube, compound parabolic & parabolic trough coll. | ||||||||||||
30 | Global SD status | 2014 | India | 107 | 15 | ++ | + | + | + | + | + | ++ | Rural areas in developing/developed countries | ||||||||||||
31 | SD with PCM as TES medium | 2014 | Egypt | 62 | 51 | ++ | ++ | ++ | + | Solar air coll. 1) with built-in PCM & 2) connected to external PCM | |||||||||||||||
32 | Performance study of different SDs | 2014 | Malaysia | 63 | 54 | ++ | + | ++ | ++ | ++ | Tropical and sub-tropical countries | ||||||||||||||
33 | Applications of software in SD systems | 2015 | India & Thailand | 42 | 32 | ++ | ++ | + | ++ | ||||||||||||||||
34 | Techno-econ. of SD with H2O coll. in Malaysia | 2015 | Malaysia | 105 | 28 | ++ | ++ | ++ | ++ | ++ | ++ | ++ | ++ | ++ | ++ | ++ | Malaysia; air & water collectors | ||||||||
35 | SD with air collectors in Malaysia | 2015 | Malaysia | 104 | 50 | ++ | ++ | + | + | + | ++ | ++ | ++ | Malaysia | |||||||||||
36 | SD Technologies | 2015 | India | 23 | 18 | ++ | Greenhouse solar drying for low temperature drying of agro-food | ||||||||||||||||||
37 | TES-based SD systems | 2016 | India & Thailand | 75 | 33 | ++ | + | ++ | + | + | Industrial drying; Collector temps up to 250°C | ||||||||||||||
38 | Modeling techniques for the SDs | 2016 | India & Thailand | 119 | 21 | ++ | ++ | + | Rural farms & small-scale factories | ||||||||||||||||
39 | SDs for drying various commodities | 2016 | India | 136 | 71 | ++ | + | + | + | + | + | Developing countries | |||||||||||||
40 | Solar tunnel greenhouse drying system | 2016 | India | 68 | 27 | ++ | ++ | + | + | + | ++ | ++ | Small scale farmers and firms, rural areas, industry | ||||||||||||
41 | Comparative analysis on uniformity enhancement methods of SD | 2018 | Malaysia & Iraq | 85 | 0 | ++ | + | ++ | + | + | ++ | + | |||||||||||||
42 | Recent developments in greenhouse SD | 2018 | India & Thailand | 39 | 9 | ++ | + | + | + | Rural farms & small-scale factories | |||||||||||||||
43 | Review of SD with econ. & env. Assessment | 2018 | Lebanon & France | 179 | 3 | ++ | ++ | ++ | + | + | ++ | + | |||||||||||||
44 | Solar process heat in industrial systems | 2018 | Australia, Malaysia & UK | 102 | 22 | ++ | ++ | ++ | + | Extensive content on collectors | |||||||||||||||
45 | Advances in sustainable drying of ag. Produce | 2019 | UK | 166 | 3 | ++ | ++ | ++ | ++ | ++ | + | + | ++ | ++ | ++ | ++ | ++ | ++ | ++ | ||||||
46 | Flat plate air collectors for SD | 2019 | Malaysia | 144 | 0 | ++ | ++ | + | ++ | ++ | ++ | ++ | ++ | + | ++ |
- coupling commercially available or slightly modified (1) solar thermal collectors and (2) industrial dryers to create novel indirect LISDs, where the slight modifications to the solar thermal collectors and/or industrial dryer are to enable or improve the thermal coupling of the collector and the dryer.
- Using more sophisticated solar thermal collector technologies to drive higher temperature industrial drying processes.
- Increasing performance through the use of more sophisticated drying technologies such as heat pumps.
- Increasing availability through TES or by hybridization with other energy sources.
The primary exception to this gap is29 published in 2014, which addresses many of these issues. Therefore, herein29 is assumed to accurately reflect the state of the art in LISDs in 2014, and the objective of the next section is to build-on29 by reviewing advances in this area since 2014.
3 REVIEW OF RECENTLY PUBLISHED ORIGINAL SD RESEARCH PAPERS RELEVANT TO LISDS
As described above, the solar dryer review paper29 published in 2014 was identified as the best review paper relevant to LISDs. The objective of this section is to build-on29 by reviewing original SD research articles published since 2014 targeting one or more of the following gaps: (1) applications outside the agro-food sector; (2) higher temperatures; (3) large SDs; (4) more sophisticated energy supply systems such as concentrating collectors and hybridization with other thermal energy sources, PV, and TES; and/or (5) more sophisticated dryer technologies such as heat pump, fluidized bed, and infrared dryer technologies. A literature review was conducted using keywords relevant to these five objectives, which then defined the scope of this literature review; that is, original SD research papers that did not strongly address one of these five objectives were not considered. This literature review was performed in an iterative manner that spanned several months during which time the keywords used for searching were refined, and the content of the articles analyzed to identify major themes, gaps and opportunities. The distilled results from this literature review are summarized in Table 2, where the columns are defined to support the five objectives above with the following supporting information. The temperature listed is a characteristic temperature related to the collector, such as average or outlet, or a temperature inside the dryer, and allows for a course comparison of research based on temperature. The collector area is used to allow a course comparison of research based on size. The Additional Keywords column contains important words or phrases in the title, list of keywords, or similar that are not reflected in the other columns.
Metadata | Application | Technologies | Additional keywords | ||||||||||||||||
---|---|---|---|---|---|---|---|---|---|---|---|---|---|---|---|---|---|---|---|
Sector | Collector | Other | Experiments | ||||||||||||||||
Reference | Year | Authors' country | No. citations | Agro-food | Non agro-food | Dried material | T (°C) | Non-conc. | Concentrating | Air | Non-air | Area (m2) | PV | TES | HP | Fluidized bed | |||
47 | 2014 | Brazil | 5 | Y | Steel wire effluent residue | 4-41a | Y | Y | 1 | Y | Solid waste drying | ||||||||
48 | 2014 | Iran | 2 | Y | Chamomile | 40-60 | Y | Y | 0.85 | Y | Y | Y | Hybrid PV–thermal SD w/ & w/o HP | ||||||
49 | 2014 | India | 12 | Y | Copra | 43 | Y | Y | 2 | Y | Y | Solar-ambient hybrid source HP drier | |||||||
50 | 2014 | China | 14 | Y | Cut tobacco | 200 | Y | Y | 30 | Y | Parabolic trough collector | ||||||||
51 | 2014 | Turkey | 29 | Y | tomato, strawberry, mint, & parsley | 50 | Y | Y | 0.6 | Y | Y | Double-pass air collector | |||||||
52 | 2015 | China | 11 | Y | Carpet | 80 | Y | Y | 56 | Y | LISD; cabinet dryer. | ||||||||
53 | 2015 | Iran | 2 | Y | Corn | NA | Y | Y | 5.4 | Y | Y | Also spouted bed dryers | |||||||
54 | 2016 | Iran | 9 | Y | Potato | 50-70 | Y | Y | 1.1 | Y | Y | Solar-assisted intermittent infrared dryer | |||||||
55 | 2016 | Indonesia & Malaysia | 16 | Y | Cassava | 40-45 | Y | Y | 3.6 | Y | Y | SD & Solar-assisted HP dryer | |||||||
56 | 2016 | China & Egypt | 15 | Y | Radish, pepper, mushroom | 30-50 | Y | Y | 5–10 | Y | Y | Y | Heat recovery; solar-assisted | ||||||
57 | 2016 | Turkey | 12 | Y | Mint leaves | 45-50 | Y | Y | Y | Y | NA | Y | Y | Y | Y | Mixed-mode; FP & PTC. | |||
58 | 2016 | Germany & Italy | 2 | Y | Y | Cooked ham and sausages, brick | 60-220 | Y | Y | Y | 2780 | Y | Y | FP, LF, PT, Indirect steam gen. | |||||
59 | 2016 | Morocco & France | 15 | Y | Olive pomace waste | 40-80 | Y | Y | NA | Y | Indirect convective SD | ||||||||
60 | 2016 | Turkey | 12 | Y | Melon | 50-60 | Y | Y | NA | Y | Infrared; air-to-air heat recovery. | ||||||||
61 | 2016 | Thailand | 13 | Y | Rubber | 40 | Y | Y | 2 | Y | Mixed-mode & indirect SD. | ||||||||
62 | 2016 | Pakistan | 5 | Y | Guava | 65 | Y | Y | NA | Y | Dehydration rate | ||||||||
63 | 2017 | Iran | 1 | Y | Corn | 45-60 | Y | Y | NA | Y | Y | Spouted bed dryer within a draft tube | |||||||
,64 | 2017 | Argentina | 5 | Y | Various vegetables | 50-90 | Y | Y | 92 | Y | Semi-industrial; Tunnel Dryer | ||||||||
65 | 2017 | United states | 2 | Y | Prune & tomato pomaces | 90-130 | Y | Y | 98 | Y | External compound parabolic concentrator; drum dryer | ||||||||
66 | 2017 | Turkey | 3 | Y | Cranberry, medlar & cherry laurel | 40 | Y | Y | NA | Y | Y | Solar-assisted; Exergy; ANN | |||||||
67 | 2017 | Indonesia & Malaysia | 15 | Y | Paddy | 60-80 | Y | Y | 3.6 | Y | Y | Solar-assisted; biomass; exergy | |||||||
68 | 2018 | Italy | 5 | Y | Sewage sludge | 140-160 | Y | Y | 500-812 | Y | N | PT; Biogas CHP | |||||||
69 | 2018 | Indonesia & Malaysia | 1 | Y | Rice | 81 | Y | Y | 3.6 | Y | Y | Y | Solar-assisted; biomass; performance & economics | ||||||
70 | 2018 | France | 5 | 0 | Y | Wood | 50 | Y | Y | 30 | Y | Mixed-mode | |||||||
71 | 2018 | France & Canada | 1 | 0 | Y | Wood | 13-21a | Y | Y | 7.6 | Y | Applied to Central Africa | |||||||
72 | 2019 | China & Malaysia | 0 | Y | Sewage sludge | 80 | Y | Y | 0.03 | Y | Direct SD | ||||||||
73 | 2019 | Morocco | 2 | Y | Wood | 50–70 | Y | Y | 9 | Y | N | Computational drying model; Latent TES. | |||||||
74 | 2019 | Algeria | 0 | Y | Tomato pomace waste | 40–60 | Y | Y | 18 | Y | Greenhouse; drying models | ||||||||
75 | 2019 | Morocco | 0 | 0 | Y | Wood | 120 | Y | Y | 2 | Y | CPC; Hybrid; TRNSYS; Energy; Environmental | |||||||
76 | 2019 | India | 4 | Y | Fruits & vegetables | 60 | Y | Y | 1 | Y | Y | Phase Change Mat'l (PCM) capsules in collector |
- a Temperature rise through the collector.
A summary of the main findings are as follows. Consistent with Section 2, most of the SD research captured in this literature review is targeting the agro-food sector and uses non-concentrating collectors with air as the HTF for lower temperature drying applications. In contrast, SD research for industrial applications that are outside the agro-food sector, that are large in scale, or that use more sophisticated collector, integration and dryer technologies for higher value-added and more sophisticated drying processes still appears to be limited, including the use of concentrating collectors to drive higher-temperature drying processes. Furthermore, most of the SD research is still occurring in countries that are often classified as developing, emerging, or similar. Even though European countries have some of the most aggressive policies to support the development and uptake of renewable energy technologies in general and SHIP specifically as evidenced by funding the INSHIP project to create a SHIP ECRIA, the relative number of papers with authors from European countries is small. Even,71 which includes authors from France, is specifically focused on applications in Central Africa. However, it is noted that the research with the largest collector areas58, 68 did occur in Europe, and the more limited research that utilized more sophisticated technologies such as concentrating collectors was performed in more developed economies. Taken as a whole, this suggests that gaps still exist in developing LISD technologies that (1) leverage the more sophisticated technologies often found in the most developed countries and (2) can target opportunities in these most developed countries that require more sophisticated drying technologies. In theory, in locations with good solar resources any drying process that uses a thermal energy source (eg, combustion and not electricity) can be driven using solar thermal technologies if the collector and underlying drying technologies are thermally matched. The objectives for the following three sections are to more fully elaborate some of the required conditions, gaps, and opportunities to thermally match collector and dryer technologies.
4 INDUSTRIAL DRYING LITERATURE
The objective for this section is to provide a gateway to the industrial drying literature independent of SDs to frame how solar-thermal technologies may be used to drive existing industrial drying technologies. Industrial SDs are just one small area within the broader field of industrial dryers, and the industrial dryer literature is too broad for any concise summary herein to be meaningful. Rather, readers interested in entering the industrial drying literature are referred to the excellent Handbook of Industrial Drying, Fourth Edition (2014), edited by Mujumdar.77 This dense 1301 page handbook assembles65 chapters written by experts covering a wide range of industrial drying topics, including five chapters on fundamental aspects, 18 chapters describing various dryer types, 28 chapters on drying in various industrial sectors, and 14 chapters on miscellaneous topics. Each chapter contains an extensive list of references, and therefore this handbook provides an easy entry point into a vast collection of literature on industrial dryers. Two gaps were identified in this handbook relevant to LISDs. First, while this handbook does contain a dedicated chapter on SDs, and the application of SDs to different sectors is discussed in several chapters, this SD content is in general parallel to the literature reviewed in Sections 2 and 3 in that it generally focuses on small-scale SDs that use relatively simple technologies and are appropriate for less-developed communities, and not LISDs for industrialized countries. Second, as an edited book, each chapter is generally authored by different experts and written to stand independent of the other chapters. Therefore the chapters often contain overlapping content presented from different perspectives, and there is little high-level synthesis of the content from different chapters. In particular, while the handbook does contain 18 chapters on different dryer types, the method used to define each dryer type is not consistent and includes dryer types defined based on one of the following: (1) flow or handling of the product to be dried (fluidized bed, spray, spouted bed, pneumatic and flash, and conveyor); (2) dryer geometry (rotary and drum); (3) flow of the drying gas (impingement); (4) alternatives to air or combustion gases as the drying gas (superheated steam); (5) alternative to the evaporation of “liquid” water (freeze-drying); (6) alternatives to convective heating of the drying surface (indirect, infrared, and microwave and dielectric); (7) alternative energy source (solar); and (8) alternatives to steady-state operating (intermittent, and pulse combustion). Consequently, the classification system used to define each chapter is not mutually exclusive and a dryer technology defined in one chapter is often treated in a different chapter from a different perspective. This gap in dryer classification is addressed in the next section where a fundamental industrial dryer classification is presented that is specifically relevant to SDs.
5 SYNTHESIS OF EXISTING LITERATURE
This section is the result of a high-level synthesis of ideas found in the existing SD and Industrial Drying literature, and as a result much of this content builds-on rather than reflects the current literature. The objective is to provide a fundamental framework to guide and characterize R&D on indirect LISDs for readers with a background in solar thermal engineering but not drying. Specifically, the focus in this section is to define and introduce fundamental concepts for drying technologies. In contrast solar collector technologies and coupling technologies (TES, hybridization, heat exchangers, and so on) are only addressed within the context of drying technologies. Readers interested in recent reviews of solar collector technologies are referred to an excellent review paper on solar collector technologies for SHIP applications published in 201844 and a review paper on flat plate air collectors published in 2019.46
In the following subsections, drying definitions and conceptual models are introduced that are specifically focused on (1) bridging the solar thermal and industrial drying literature, and 2) developing a conceptual framework that facilitates the identification of technological gaps and opportunities, and the intuition to formulate appropriate responses. Therefore, these definitions and models are intentionally kept as simple as possible and are often not sufficiently robust for detailed drying studies, and readers are referred to the relevant literature cited above for more detailed models. In particular, the three chapters1, 78, 79in Section 1. Fundamental Aspects in the Handbook of Industrial Drying, Fourth Edition77 provide excellent content on drying fundamentals.
5.1 Drying characteristics
In this section, the physical, thermal, and material handling characteristics of dryers most relevant to SDs are introduced.
5.1.1 Physical characteristics
Drying is a thermal process that results in the removal of moisture from a moist material by vaporization to form a dry product. Drying is defined as a thermal process and is distinct from other methods to remove moisture such as mechanical extraction via centrifugation. Key terms for physically describing the drying process are graphically presented in Figure 1 and defined below. While Figure 1 is for one specific and straightforward dryer geometry, the resulting terms and definitions are easily adaptable to a wide range of dryer geometries.
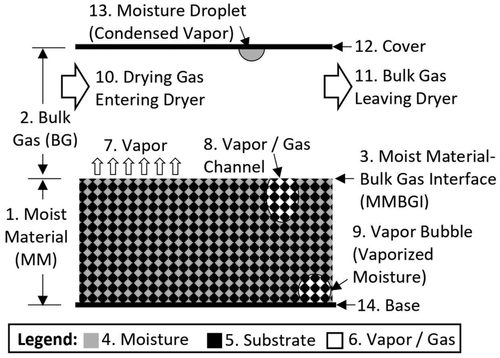
As shown on the left side of Figure 1, the inside of the drying chamber is divided into two macroscopic volumes: (a) the moist material (MM) (1) on the bottom; and b) the bulk gas (BG) (2) on the top. The moist material-bulk gas interface (MMBGI) (3) is the horizontal plane separating the moist material and the bulk gas. The moist material is the material being dried inside the dryer, and consists of two parts: (a) moisture (4), which is volatile; and (b) substrate (5), which is not volatile. The bulk gas contains at least vapor (6), which is vaporized moisture and therefore can be condensed, and often non-condensable gases. Drying processes vaporize the moisture and pass the resulting vapor (7) to the bulk gas via the MMBGI. 99% of all drying applications involve the removal of water,80 and therefore, the associated vapor is water vapor. The moist material may contain vapor/gas channels (8) that connect the interior of the moist material to the bulk gas. In addition, the moist material may contain isolated vapor bubbles (vaporized moisture) (9) that do not connect to the bulk gas. In most dryers a drying gas (10) is introduced into the dryer to at least transport the vaporized moisture away from the moist material and in some cases to also provide convective heating to the moist material. The exception are vacuum dryers, which do not have a drying gas. Almost 85% of industrial dryers use air or combustion gases as the drying gas,1 but other drying gases such as superheated steam are also used.81 The bulk gas leaving the dryer (11) always contains vaporized moisture and, except for vacuum dryers, also contains the drying gas. The cover (12) is used to contain the bulk gas. When the drying gas is cooled, such as through contact with a cold cover, it may condense to form a moisture droplet (13). The base (14) is used to support, contain, and possibly transport the moist material and is often either well-insulated or heated.
5.1.2 Thermal characteristics
Drying is inherently a thermal process as it involves a vaporization process in which heat is absorbed to transform moisture into vapor. Ignoring the particular case of freeze drying, the simplest model for the state of moisture being a liquid is assumed herein, in which case the heat of vaporization is equal to the heat of evaporation. Both surface vaporization and bulk vaporization are possible. Surface vaporization is evaporation of moisture from a free surface and occurs when the saturation pressure of the moisture is greater than the vapor pressure of the gas at the free surface. Surface vaporization can occur at the MMBGI, and at the interface between moisture and gas in the interior of the moist material, such as at a gas channel or vapor bubble. In contrast, bulk vaporization is boiling of moisture, occurs when the moisture away from a free surface is heated to the saturation temperature and results in the creation of a new vapor bubble. Note the expansion associated with the production of a vapor bubble in a closed or restricted pore of the substrate can damage the substrate's structure and reduce the quality of the dried product, and therefore bulk vaporization is often not desired for high-quality dried products. The type(s) of vaporization present in a drying process will vary with the drying technology, characteristics of the moisture, substrate, and drying gas, and will often evolve as the drying process proceeds. For example, the drying of a moist material with large pores, high initial moisture content, and with moist material temperatures uniformly below the saturation temperature may begin with surface vaporization at the MMBGI and then evolve to surface vaporization from interior channels as the moist material dries.
While the above discussion assumes that the moisture is in the liquid state, in reality, the moisture can exist over a continuum of states ranging from a tightly absorbed state on the surface of the substrate, termed bound moisture, to a liquid state, termed unbound moisture.1 The degree to which moisture is bound varies with the properties of the moisture and substrate, and decreases as the distance between a moisture molecule and the substrate increases. Bound moisture has a higher heat of vaporization and lower saturation pressure than unbound moisture. As a result, drying processes tend to vaporize unbound moisture first and strongly bound moisture last, which often results in drying rates decreasing as a drying process evolves. The complete removal of strongly bound moisture is difficult and may require high temperatures and low vapor pressures, and these conditions can be challenging to achieve and reduce the quality of the dried product.
Several key conclusions related to the thermal characteristics of dryers are as follows. Due to the onset of bulk vaporization, the temperature of the moist material will not exceed the moisture's saturation temperature at any location where moisture is present. Furthermore, the saturation temperature increases as the moisture become increasingly bound, so the temperature limits due to bulk vaporization will often increase as a drying process evolves. However, the temperature of a dry region (ie, a region that contains substrate but no moisture) is not limited by bulk vaporization, and directly heating a dry region can result in a hot spot. In parallel, due to the onset of condensation, the temperature of the bulk gas will not fall below the bulk gas's dew point temperature (the temperature at which the gas's vapor pressure equals the saturation pressure). Finally, the rate of vaporization, and therefore the rate of drying, will typically vary both spatially and temporally due to spatial and temporal variations in temperature, vapor pressure, total pressure, and the degree to which the moisture is bound.
5.1.3 Material handling characteristics
Although material handling characteristics are not as central to this presentation as physical and thermal characteristics, as elaborated in Section 4 industrial dryers are often described and differentiated based on their material handling characteristics, and therefore a short overview of key material handling terms is appropriate. Dryers are classified as batch, continuous, or semi-continuous based on material handling characteristics as follows. In all cases, the moist material enters the dryer as the moist feed and exits as the dried product. In a batch dryer, a discrete batch of moist feed enters the dryer and is heated and dried through a transient process. During this batch drying process, no moist feed enters or dried product leaves the dryer. At the end of the drying process, the resulting batch of dried product is removed. In a continuous dryer, the moist feed continuously enters the dryer, the moist material continuously moves through the dryer, dry product continuously leaves the dryer, and the drying process evolves as the moist substance moves through the dryer. Continuous dryers are often modeled as steady-state steady-flow systems. In a semi-continuous dryer, the dryer is split into several sequential zones corresponding to different stages of drying. Each zone dries a discrete batch of moist material through a transient process like a batch dryer, but the evolution of the drying process by moving moist material from one zone to another mimics a continuous dryer. To promote uniform drying, the moist material may be mixed, such as through stirring or tumbling in a rotating cylinder. Scraping is used to remove moist material and dried product from the base and may be required for effective mixing.
5.2 Four fundamental classes of dryers based on the heating mechanism
Solar thermal systems can be used to drive the drying vaporization process provided the thermal characteristics of the solar thermal system are properly matched to the drying technology. To conceptually facilitate this thermal matching, four distinct classes of dryers are defined herein based on the heating mechanism as follows: (a) convective dryers; (b) conductive dryers; (c) surface radiative dryers; and (d) bulk radiative dryers. While hybrid dryers combining two or more dryer types are possible, these cases are ignored herein for simplicity. These four classes of dryers are illustrated in Figure 2, with the left side of each of (A)-(D) illustrating the heating mechanism and location, and the right side presenting a sample temperature profile. These temperature profiles are specifically referred to as sample and not representative or typical due to their exact shape typically evolving with the drying process and varying with many factors including but not limited to (1) whether surface and/or bulk vaporization is occurring, (2) whether the moist material's temperature is increasing, constant, or decreasing with time, (3) whether the base and cover are well insulated, and (4) whether the moist material contains dry spots. These sample profiles are specifically for the case where all vaporization is occurring as surface vaporization at the MMBGI, and the moist material does not contain any dry spots. Specifically, bulk vaporization is not occurring and therefore, the temperature of the moist material must be less than the moisture's saturation temperature. Similarly, no condensation occurs from the bulk gas, and therefore the bulk gas must be at a temperature higher than the bulk gas's saturation temperature. While typically an insulated base (IB) or heated base (HB) is used, the uninsulated base (UB) case is shown in Figure 2A,C, and D to highlight where the moist material's maximum temperature typically occurs and how heat flows through the moist material. Similarly, while typically an insulated cover (IC) is used, an uninsulated cover (UC) is shown in Figure 2C to illustrate a solar dryer with a poorly insulated transparent cover used to admit solar radiation. While the details for these temperature profiles are unique to a large set of assumptions, for each dryer class the relative temperatures of the bulk gas and moist material, the location of the maximum temperature in the moist material, and the directions of the heat flows (hot to cold) within the system are representative for a large set of typical operating conditions, and therefore are conceptually significant to compare and contrast these four classes of dryers.
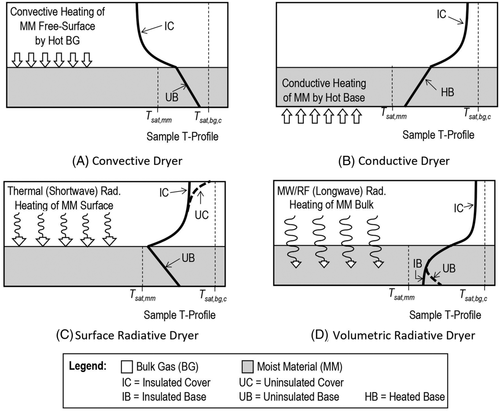
Vapor pressure and saturation pressure profiles of the bulk gas in a direction parallel to the MMBGI are also effective at comparing and contrasting these four classes of dryers. Sample profiles are presented in Figure 3 and illustrate basic trends for common operating conditions. In all cases, the vapor pressure of the bulk gas increases in the flow direction (left to right) due to the uptake of vapor from the moist material. The saturation pressure scales with the bulk gas temperature, and decreases in the flow direction if the bulk gas is being cooled (which is the case for convective dryers) and increases if the bulk gas is being heated (which is the case for conductive, surface radiative, and bulk radiative dryers). Note if the saturation and vapor pressure lines meet, the drying gas is saturated and can no longer absorb more vapor, further drying is impossible, and any cooling of the drying gas will initiate condensation.
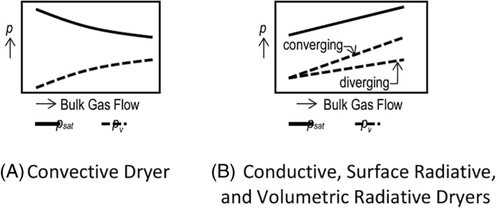
Further details for each dryer type are as follows, including options to thermally drive the dryer using different classes of solar collectors.
5.2.1 Convective dryers
In convective dryers, an externally heated, hot drying gas is continuously introduced into the dryer and heats the relatively cooler moist material via convection, as shown in Figure 2A. Among the four classes of dryers, convective dryers are unique in that under normal operating conditions (1) the maximum temperature in the dryer occurs in the bulk gas; (2) heat flows from the bulk gas to the moist material; and (3) heat transfer from the bulk gas to the moist material causes the bulk gas to cool in the flow direction, and therefore for its saturation pressure to decrease as shown in Figure 3A. As a result, the bulk gas's vapor and saturation pressures tend to converge in the bulk gas flow direction. Approximately 85% of all industrial dryers are convective.1 Solar thermal systems can be used to heat the drying gas directly by using air collectors or indirectly using a non-air collector (eg, liquid collector) coupled to a liquid-gas heat exchanger. In the industrial dryer literature convective dryers are often termed direct dryers due to the hot bulk gas directly heating the moist material, while in the SD literature convective dryers are often termed indirect dryers due to the use of a HTF to thermally couple the collector to the dryer.
5.2.2 Conductive dryers
In conductive dryers, a hot base is used to heat the moist material as shown in Figure 2B. While the name conductive dryer implies that the moist material is quiescent and therefore heat transfer occurs by conduction from the base to the moist material, convective heating from a hot base into a non-quiescent moist material such as a sludge with high moisture content is also possible. In contrast to a convective dryer, the moist material is hotter than the bulk gas and heat transfer occurs by convection from the moist material to the bulk gas. The resultant heating of the bulk gas tends to cause the bulk gas's saturation pressure to increase in the bulk gas flow direction as shown in Figure 3B. Depending on the exact conditions inside the dryer, the saturation and vapor pressures may converge or diverge. Among the four dryer types, conductive dryers are unique in that under normal operating conditions the maximum temperature in the dryer occurs at the base as shown in Figure 2B. Solar thermal systems can be used to heat the base using any solar thermal technology, including both air and liquid collectors. In the industrial dryer literature, conductive dryers are often referred to as indirect or contact dryers.
5.2.3 Surface radiative dryers
Surface radiative dryers use thermal (relatively shortwave) radiation to heat the free surface of the moist material at the MMBGI. Thermal radiation includes both the solar (visible) and infrared (IR) spectrums. Among the four drying technologies, surface radiative dryers are unique in that under normal operating conditions, the maximum temperature in the dryer occurs at the MMBGI as shown in Figure 2C. The thermal radiation can be supplied by direct exposure to solar radiation through the use of a transparent cover (termed a direct SDs in the SD literature), or by infrared (IR) heaters that use electricity or a hot heat transfer fluid. The uninsulated cover (UC) temperature profile in Figure 2C illustrates a direct SD with a poorly insulated transparent cover to admit solar radiation. The bulk gas's saturation and vapor pressure profiles are similar to conductive dryers as shown in Figure 3B. Often the cover of a direct SD is not a good insulator and may be “cold” relative to the bulk gas, and thus susceptible to condensation if the bulk gas temperature in contact with this cover reaches its saturation temperature. One important design consideration for direct SDs is that the maximum flux for unconcentrated solar radiation is approximately 1000 W m−2; that is, on a clear sunny day a surface facing the sun will receive approximately 1000 W m−2 of solar radiation. Equivalently, an IR heater behaving as a blackbody at a temperature of 90°C also emits a radiative flux of approximately 1000 W m−2. Since the emission from a blackbody scales with the temperature of the blackbody to the fourth power, IR heaters at temperatures greater than 90°C can, at least in theory, achieve much higher radiative fluxes than unconcentrated solar radiation. Typically concentrating rather than non-concentrating solar collectors are appropriate for collector temperatures >~100°C, and based on the literature review above the potential to use concentrating collector technologies to drive IR heaters has not been explored. Specifically, Direct Steam Generation (DSG) technologies may be used where steam is generated directly in the absorber and then condensed in a pipe creating an isothermal IR heater, or oil or molten salts may be used as the HTF to thermally couple the concentrating collector to a IR heater that is non-isothermal due to the HTF undergoing sensible cooling in the IR heating pipe. In the industrial dryer literature, surface radiative dryers are typically called infrared dryers.
5.2.4 Volumetric radiative dryers
Volumetric radiative dryers use relatively longwave microwave (MW) or radio frequency (RF) radiation that are absorbed volumetrically rather than at the MMBGI, resulting in volumetric heating. Among the four dryer classes, volumetric radiative dryers are unique in that the maximum temperature in the moist material does not necessarily occur at a surface, but rather can occur anywhere inside the moist material as illustrated in Figure 2D. The bulk gas's saturation and vapor pressure profiles are similar to conductive dryers, as shown in Figure 3B. In the industrial literature, volumetric radiative dryers are typically called MW dryers. MW and RF radiation are generated using electricity, and unlike the Convective, Conductive, and Surface Radiative dryer classes, there is no opportunity to directly drive volumetric radiative dryers using solar thermal technologies.
To reiterate common differences between the industrial drying and SD literature, direct dryers refers to convective dryers in the industrial dryer literature and surface radiative dryers heated directly using solar radiation in the SD literature. In contrast, indirect dryers refers to conductive dryers in the industrial dryer literature and convective dryers in the SD literature.
6 INTEGRATION
Most of the integration issues related to thermally coupling solar collectors with dryers in indirect LISDs are not unique to indirect LISDs but rather are common to a wide range of SHIP technologies and applications. Therefore, much of this section is approached at the more general SHIP level rather than the more narrow LISD level. The way solar process heat is integrated in the industrial supply system significantly influences its technical and economic feasibility. Integration issues are of central importance in SHIP as the industrial supply and distribution systems are much more complicated than most other solar thermal applications, which is due in part to both solar resources and thermal loads that may vary over multiple timescales ranging from minutes to seasons. Several research projects have addressed integration issues by developing methods to assist in the design and planning of solar process heat with an emphasis on feasibility. One of the most important projects is the International Energy Agency Solar Heating and Cooling Programme Task 49/IV (IEA SHC Task 49/IV; http://task49.iea-shc.org/) that contains three Sub-Tasks (A-C). In particular, Sub-Task B Process integration and Process Intensification combined with solar process heat has produced many resources to assist with integration issues.
6.1 Integration approaches
As illustrated in Figure 4, solar thermal is in general integrated into industrial processes at the (1) Supply Level (A) or (2) Process Level (B). Supply level integration means integrating solar thermal within the central heat distribution lines or central heat storages, while process level means integrating solar heat to one specific process step or process heat storages.
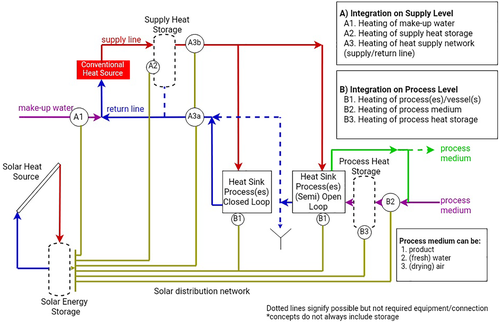
The SHIP integration guideline82 developed within IEA SHC Task 49/IV presents the overall necessary steps of an assessment methodology for solar process heat projects and leads the planner in detail through the following steps: (1) consideration of process integration for solar process heat; (2) specification of integration concepts; (3) planning of solar process heat system concepts; and (4) criteria for selecting the most promising integration points. The starting point of the methodology is always a detailed assessment of the processes (load profile, energy demand, temperature, and so on) and the energy supply system to serve as a baseline against which to evaluate the concept. This also includes possible excess heat recovery potentials (thermal energy efficiency), which is an important topic in industrial drying and depends on the drying temperature and system. Based on this assessment, the most efficient industrial process can be designed, followed by the solar thermal system. In Figure 5, an example scheme of a heat integration concept is presented based on Direct Steam Generation (DSG) using concentrating collectors. There are also several other tools available on the IEA SHC Task 49 website supporting the planner in system design (http://task49.iea-shc.org/).
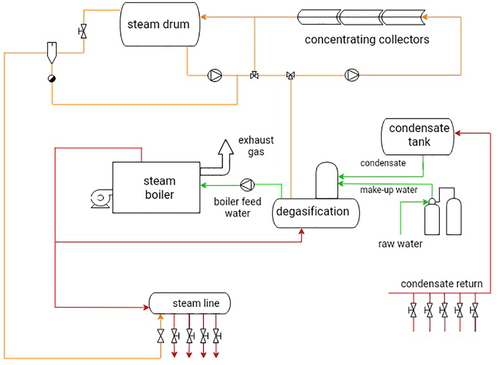
6.2 Integration concepts
Overall, a SHIP system consists of up to five subsections as shown in Figure 6: (1) collector loop; (2) charge; (3) storage; (4) discharge; and (5) integration point. Most drying processes are low-temperature systems, and in these low temperature SHIP systems that include storage, typically all five sections can be distinguished. However, depending on the envisaged system design, specific components can be dropped (eg, the storage) and/or a backup system may be included to ensure a trouble-free and continuous production irrespective of variations in solar resources.
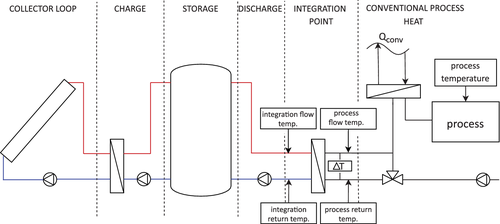
Following the methodology developed within the IEA SHC Task49/IV and consistent with standards on energy audits and energy efficiency (eg, EN 16247), the first step in the design of a SHIP system is the identification and characterization of the industrial energy demand. Based on the assessment of the existing industrial system and its energy supply, specific load profiles (energy demand, process temperature) are developed and integrated into energy efficiency measures such as excess heat recovery. Especially for drying processes, this is mandatory, as usable excess heat (air or other media) should be re-integrated into the system before investing in solar thermal systems.
Depending on the supply system of the drying process and the drying technology used (type, media, temperature, duration, and so on), a suitable integration concept for solar thermal has to be identified, which can be facilitated through a standard classification of heat consumers. This enables the choice of the most suitable integration concept among a large number of possible concepts. Details on the classes of heat consumers and respective integration concepts are documented within the Task 49 Integration Guideline.82
As for all industrial processes and their possible solar thermal supply, integration depends strongly on the process technology used with respect to the chosen/existing supply system based on the demand of the moist material.
- Convective dryers—Drying by drying gas (hot air) in the dryer (drying chamber): In case the drying is done via externally (pre)heated air (or other gas) that is introduced continuously into the dryer and regularly refreshed, either the drying gas can be (pre)heated in a collector directly or this is done via an external heat exchanger transferring the heat from a collector using a heat transfer fluid (eg, water, thermal oil) to the gas. The targeted temperature strongly depends on the moist material and the envisaged product quality.
- Conductive dryers—Drying by a hot base (contact dryer): Using this technology the base has to be heated up to a certain temperature, designated based on the requirements of the moist material (the product) and its behavior on the conductive heat and moisture transfer. The heat transfer from the supply to the base can be done using a heat transfer medium such as water or thermal oil.
- Surface radiative dryers—drying based on thermal radiation mechanism: The supply of the heat to the dryer is similar to conductive dryers and has to be based on the behavior of the moist material and its inner heat and moisture transfer respectively and the required product quality. Again, the heat transfer to the radiation area can be done using a heat transfer fluid such as water or thermal oil.
The key for reliable continuous energy supply to the dryer is the design of the overall system including the collector, the storage, the integration point, the charging and discharging strategy and if needed a backup system.
- Collector: The selection of the most efficient and appropriate collector technology and the design of the collector field strongly depend on the process requirements (temperature, load profiles, capacity, production breaks, holiday breaks, and so on). Depending on the temperature levels needed, different collector technologies can be implemented including flat plate collector, evacuated tube collector, and concentrating technologies such as parabolic trough collector. An optimized system design increases the efficiency and yield of the collector by the interaction with charging and discharging strategies and components, and the orientation and placement of the field. Finally, the collector field design has a large impact on overall costs of the system.
- Storage and back-up system: Many industrial processes require an interruption-free thermal energy supply. In cases when the heating demand and the solar availability do not match in matters of time and load profiles, thermal energy storage and/or a back-up thermal energy supply is commonly used. By the optimized integration and design of the storage (size, insulation, and so on), the economic feasibility can be significantly increased. The use of existing systems and its optimum integration in the solar system (eg, via the storage) is part of the overall design methodology.
- Integration point: As noted above, the integration point can be at the supply or the process level. Supply level integration results in the solar thermal system supplying heat to all industrial consumers, and not just the dryer(s). In contrast, process level integration results in the solar thermal system only supplying heat to the dryer(s). Process level integration in most cases requires a more complex hydraulic design than supply level integration, and as the number of processes being supplied increases, the number of heat exchangers and thermal energy storage systems required also increases. On the other hand, the required temperature to be delivered by the solar system is in most cases higher for system level integration than for process level integration, as in most cases for system level integration the solar thermal system must be designed to supply energy to the whole system and therefore its operating temperature is dictated by the thermal energy consumer with the highest temperature requirements. These higher temperatures at a minimum typically result in lower solar collector efficiencies and larger distribution losses, and may require more expensive collector technologies to be used. Due to these reasons, while more complex, process integration is often more efficient (ie, has a higher specific solar yield) than supply integration. Ultimately, the whole energy system has to be designed in the most technical and economic optimum manner, including possible excess heat recovery as well as a backup system (if necessary).
- Heat transfer enhancement;
- Conversion of batch processes to continuous processes;
- Increasing selectivity in separation processes;
- Intensification of electrohydrodynamics.
7 LISD APPLICATIONS
7.1 Existing applications
An online database of SHIP applications throughout the world was created through the International Energy Agency (IEA) Task 49/IV Solar Heating and Cooling Programme (www.ship-plants.info). As of May 1, 2020, this database contained 333 entries for a diverse set of SHIP installations. Summary information for 19 existing LISD installations were extracted from this database and are presented in Table 3 with supporting information as follows. The LISD Number (No.) is a unique identifier assigned herein, and LISD Nos. 116a and 116b are different installations at the same facility. Consistent with the definition of LISDs, all installations are large with collector areas ranging from55.6 to 1490 m2 and rated thermal power between 39 and 800 kWth. The annual heat delivered per unit area, termed the Specific Heat herein, were reported for seven installations, and although these seven installations are diverse in terms of collector type, rated thermal power, and location (and therefore solar resources), the reported specific heats are macroscopically similar and range from 0.31 to 0.81 MWh m−2 years−1. Process and/or collector temperature ranges were reported for 12 installations, and for brevity the highest reported temperature is presented as the Characteristic Temperature (Char. Temp.), which ranged from 35 to 200°C. Investment costs were reported for 10 installations and these ranged from 74 to 467 € m−2. The limited number of installations with reported investments costs and the diversity of these installations with respect to year, collector type, location, and so on, makes it difficult to draw any conclusions about trends from this investment data. In addition to the data presented in Table 3, the calculated solar thermal system lifetime was reported for four installations, with 15 years being reported for LISD No. 110, and 25 years being reported for LISD Nos. 106, 107, 116a and 116b.
LISD No. | Est. | Name | Country | Sector &/or Dried Mat'l | Collector | Investmenta | ||||||
---|---|---|---|---|---|---|---|---|---|---|---|---|
Type | Area | Power | Specific Heat | Char. Tempb | Total | Specific | ||||||
(m2) | (kWth) | (MWh m−2 years−1) | HTF | (°C) | (103 €) | (€ m−2) | ||||||
101 | 1980 | Grammer Solar Argentinia | Argentina | Tobacco | Air | 737 | 516 | — | Air | — | — | — |
102 | 1994 | Malabar Tea Drying | Indonesia | Tea leaves | Air | 600 | 420 | — | Air | 35 | — | — |
103 | 2000 | FengLi Fruit Drying | China | Fruits | Air | 55.7 | 39 | — | Air | 70 | — | — |
104 | 2004 | Duran Coffee | Panama | Coffee | Air | 900 | 630 | — | Air | 45 | — | — |
105 | 2005 | Coopeldos | Costa Rica | Coffee | Air | 860 | 602 | — | Air | 45 | — | — |
106 | 2006 | Hofigal S.A. | Romania | Medicinal plants, herbs, fruits | Air | 60 | 42 | 0.58 | Air | — | 28 | 467 |
107 | 2006 | Rockland County | USA | Wastewater waste | Air | 743 | 520 | 0.58 | Air | — | — | — |
108 | 2007 | Inter Rubber Latex Co. Ltd. | Thailand | Natural rubber | Air | 80 | 56 | 0.63 | Air | — | 36 | 450 |
109 | 2010 | LeitlBeton GmbH | Austria | Prefab. concrete components | FP | 315 | 221 | — | WG | — | 135 | 425 |
110 | 2012 | AMR Dal mill | India | Ag., forestry & fishing: Pulse | Air | 230 | 161 | — | Air | 17 | 74 | |
111 | 2012 | Acme McCary | USA | Textiles/Textile | FP | 743 | 520 | 0.81 | WG | — | — | — |
112 | 2014 | Cologne Transit Authority | Germany | Varnish/paint | ET | 237 | 166 | 0.34 | H2O | 70 | — | — |
113 | 2014 | Parc Solaire Alain Lemaire | Canada | Paper and paper products | PT | 1490 | 800 | — | Oil | 140 | 650 | 436 |
114 | 2014 | SILAMPOS S.A. | Portugal | Fabricated metal products | PT | 450 | 67 | 0.31 | Oil | 180 | ~100 | 222 |
115 | 2016 | Ultramarne Pigments | India | Pigments | PD | 570 | 399 | — | Oil | 200 | 124 | 217 |
116a | 2017 | Zacatecas Termosolar Drying | Mexico | Ag. products | Air | 120 | 84 | — | Air | 120 | 24 | 200 |
116b | " | " | " | " | FP | 125 | 87 | — | WG | 85 | 30 | 243 |
117 | 2017 | Surprise SHIP | USA | Wastewater/Sewage sludge | PT | 151 | 98 | — | WG | 100 | 59 | 388 |
118 | — | Pincasa | Spain | Fabricated metal products | EFP | 190 | 26 | 0.47 | Oil | 180 | — | — |
- Abbreviations: EFP, evacuated flat plate; ET, evacuated tube; FPC, flat plate; PD, parabolic dish; TO, thermo-oil; WG, water/glycol.
- a Excluding value added tax (VAT).
- b Maximum process or collector temperature.
7.2 Potential and emerging areas
Drying is common process with a wide range of industrial applications. For the sake of brevity, herein a representative set of industrial applications are discussed where solar drying technologies can be integrated. For each application, the typical working temperature range and appropriate types of solar collectors are discussed.
- Agro-food sector: Most of the previous SD research is focused on the agro-food sector in general and drying crops specifically. Relatively less research has focused on integrating SDs into large industrial food production processes. As a specific example, pasta is typically dried at temperatures ranging from 40°C to 100°C. Ozgener and Ozgener83, 84 studied the drying performance of solar greenhouses for pasta drying. For this temperature range, inexpensive flat plate, evacuated tube, and compound parabolic collectors can be used, with the best collector choice depending strongly on the technology of the industrial implant. Buscemi et al85studied the technical feasibility of an innovative industrial SD that integrated a system of small-size linear Fresnel collectors with concrete thermal energy storage for the production of dry pasta using a 2.4 MW capacity dryer. In this system, diathermic oil is heated from 140°C to 310°C in a linear Fresnel collector, where the amount of heating varies with the direct solar resources and ambient air temperature. This diathermic oil is then used to heat water from 120°C to 140°C, and this water then supplies the thermal loads to the pasta factory. The results of this feasibility study reveal that the solar dryer can provide 40% of annual thermal energy required by the pasta factory (11.55 GWhth), with more than 95% of this thermal load going to the dryer. As described by Buscemi et al, the solar drying should be connected at the supply level; therefore, a heat exchanger is necessary to transport the heat produced in the solar loop to the industrial drying equipment. This condition is a common situation for many actual industrial processes; therefore even if the process temperature is relatively low (<80°), the temperature of the solar loop should be higher than 100°C to obtain an adequate transfer of heat. Consequently evacuated tube, compound parabolic and parabolic trough collectors could also be appropriate for these industrial applications.
- Pharmaceuticals: A potential high-value SD application is within the pharmaceutical sector, such as for the drying of excipient, which is the powder form of the active compound. The effectiveness of these drying processes can have a significant impact on product quality and process efficiency, including subsequent tableting or encapsulation and can influence critical quality attributes of the final dosage form. The typical temperatures, for instance, for spray drying in the pharmaceutical application, are from 50°C to 160°C.86 For drying at relatively low temperatures (<100°C), flat plate and evacuated tube collectors can be used, while for the processes at temperatures higher than 120°C linear Fresnel and parabolic trough collectors can be used, with parabolic troughs being capable of supplying heat at temperatures greater than 300°C.87
- Wastewater: Evaporation is a common wastewater treatment process to separate water from solid waste materials. This process results in a sharp reduction in the mass of waste materials and in parallel a reduction in the economic and environmental costs to manage and dispose of this waste material.24 Wastewater treatment is a common process not only for treating municipal sludge, but also for treating wastewater produced across a wide range of sectors including agro-food, pharmaceutical, and mineral.24, 74, 88 The temperature required in the drying of wastewater is in the range from 30°C to 80°C, which makes greenhouse dryers, flat plate collectors, and evacuated tube collectors appropriate for this field of applications.
- Polymers: SDs can be used to dry polymers across a wide range of manufacturing industries.89 For instance, the drying of solvent-coated polymer films is an essential unit operation for the economical production of many polymeric products, including synthetic fibers and adhesive book coverings. The polymeric coatings are produced by casting a continuous single layer of polymer solution or multiple distinct solution layers onto a moving substrate and to form the final product these layers are dried in an oven with forced-air convection.90 The temperature of the dryer for polymer films is around 60°C and therefore the use of evacuated tube collectors is appropriate.
- Mining: Drying is a fundamental process in the mineral processing industry and is generally carried out for raw materials to facilitate handling or to increase the quality of the products, with one example being sand production. The drying temperature of the conventional hot air process used to dry sand is 48°C and that to dry coal is in the range of 70°C-90°C. An emerging technology in this field is the Superheated Steam Dryer technology, which uses superheated steam as the drying medium.91 The process temperature of the Superheated Steam Dryer technology is in the range of 200°C-550°C, which is significantly higher than for most conventional drying processes. In this temperature range, concentrating and tracking solar technologies such as linear Fresnel, parabolic trough, central receiver, and parabolic dish are appropriate.
Industrial drying is also required in many other sectors and processes, including those associated with textile production, microelectronics, and coating. For example, in the advanced technology field of microelectronics and nanoelectronics, drying is used in many steps of fabrication processes including the wet cleaning process after the rinsing process and in the process to dry and polymerize the polymer layers. Drying is essential in the wet cleaning process that is used for a wide variety of technologies in the semiconductor, MEMS, photonics and biotech industries.92, 93 In the convective dryer, for instance, the drying chamber is heated to evaporate the water off the product, and hot, filtered nitrogen or clean, dry air can assist the drying. The temperature of drying of the wafers ranges from 20°C to 100°C, which is particularly well-suited to SD technologies. In addition, for the present work no specific research exploring the feasibility of applying SD to advanced technological fields such as clean room facilities for micro- and nanofabrication was identified. However, the continuous upgrade of cleanroom facilities induced by the evolution of constant electronic devices and the need to transition to a low-carbon energy future could promote the study of the integration of SD into these high-tech industries.
8 CONCLUSIONS
Most of the existing SD research is focused on non-industrial or small industrial agro-food applications in less developed regions, and in many cases is focused on preserving food to alleviate poverty. In contrast, relatively little research was found that focused on SDs for (1) the large industrial drying sectors found in heavily industrialized regions; (2) the drying processes for higher-value industrial processes outside the agro-food industry; and (3) higher-temperature drying applications. In particular, a large gap was identified for indirect LISDs that use existing or slightly modified solar collector technologies to drive existing or slightly modified industrial drying technologies. This gap includes the potential to use more sophisticated concentrating solar collector technologies to drive higher temperature drying processes and more sophisticated indirect LISDs for the higher-value drying processes often found in highly industrialized regions. A specific opportunity not addressed in the reviewed literature is the potential to use concentrating collectors to generate steam either directly in the collector (Direct Steam Generation/DSG) or indirectly in a heat exchanger, and then using this steam to drive a superheated steam dryer or condensing this steam to drive a surface radiative dryer. The challenges in coupling solar collector and industrial drying technologies are in large part not unique to indirect LISDs, but rather are similar to the solar thermal integration challenges found across almost potential SHIP applications. Especially in higher value-added drying processes where high-availability and reliability of the dryer are required, further research to integrate thermal energy storage and to hybridize solar thermal with other thermal energy sources in a cost effective manner is required. Ultimately developing indirect LISDs for highly industrialized regions can play a critical role in decarbonizing these industrial sectors.
ACKNOWLEDGMENTS
This work was supported in part with funding from the European Union's Horizon 2020 research and innovation programme under grant agreement No 731287 and by in-kind contributions from Orta Doğu Teknik Üniversitesi. The authors would like to thank Ilker Tari and Dilara Cinarel for their inputs that helped frame much of this content.