Implementation of offline iterative hybrid simulation based on neural networks
Abstract
Real-time hybrid simulation (RTHS) is a testing method that combines numerical simulation and physical testing, enabling large-scale or even full-scale tests of large and complex engineering structures using the existing experimental facilities. At present, the accuracy and stability of RTHS are limited by the loading device and numerical solution efficiency. The experimental method was improved based on the neural network, and an off-line iterative hybrid simulation method based on neural networks was implemented. Taking the tuned damping structure as examples, the dynamic metamodels of the tuned mass damper and tuned liquid damper were established based on the long-short time memory (LSTM) neural network, and the model was iteratively simulated globally with the 9-story benchmark model to calculate the response of the damping structure. The error of damper reaction predicted by LSTM neural network model is within 5.16%. The global iterative method can converge after a limited number of iterations, and the peak error of the structural response is within 7.85%.
1 INTRODUCTION
LSTM can solve hard long time lag problems the real-time hybrid simulation (RTHS) technology performs physical testing on part of the test object, and numerical simulation on the rest. The physical loading part and the numerical simulation part interact online based on the boundary state, which can effectively alleviate the size effect of the test specimen caused by the size and capacity of the test device. So that the ability of the existing experimental facilities to conduct dynamic analysis of large and complex engineering structures is expanded. In 1969, Hakuno et al.1 first applied hybrid simulation technology to analyze structural dynamic response. In 1992, Nakashima et al.2 perfected the RTHS technology, whose physical loading rate is the same as the actual load, and can reflect the dynamic characteristics of the rate-dependent components.
One of the keys of RTHS is to accurately apply the interface response to the physical substructure in real time by the loading device. Commonly used loading devices include actuators and shaking tables, both of which have amplitude and phase errors in real-time loading. Horiuchi and colleagues3, 4 first regarded loading error as time delay and proposed a time delay compensation method based on polynomial interpolation. This time delay has been proved to be time-varying and related to the dynamic characteristics of the structure. Darby et al.,5 Ahmadizadeh et al.,6 and Chae et al.7 developed an adaptive delay evaluation and compensation method for the loading system. Spencer and colleagues8 and Tang et al.9 used model-based inverse dynamic compensation to improve the control accuracy of loading systems with magnitude and phase errors.
Another key aspect of RTHS is real-time numerical solution. According to whether the dynamical equation needs to be decoupled, the integral algorithm can be categorized as an explicit integral algorithm or an implicit integral algorithm. The advantage of the explicit integration algorithm is that the dynamic response of step i + 1 can be calculated from the dynamic response of the current step i and the previous step. However, its convergence condition is Δt ≤ Tn/π.10 The implicit integral algorithm is unconditionally stable, but when solving a nonlinear model, a new stiffness matrix needs to be generated and iterated at each time step, resulting in lower solution efficiency compared to the explicit algorithm. Therefore, explicit integration algorithms are typically employed in RTHS.11 To meet the requirements of convergence and solution efficiency, various numerical integration algorithms have been improved.12-14 Considering the current solving hardware conditions, the RTHS can be implemented with a numerical substructure of 27,000 degrees at intervals of 20 ms.15 For nonlinear models that require iteration solution, the application of RTHS is restricted due to the uncertain duration of iterative solution processes.
Tuning vibration reduction is one of the most commonly used vibration control methods. By adding substructures to a building, the vibration energy of the building is redistributed between the original structure and the substructure, so as to reduce structural vibration. The common tuned dampers include tuned mass damper (TMD), tuned liquid damper (TLD), and so on. When the structure vibrates under external excitation, it drives the substructure system to vibrate together, and the force produced by the relative motion of the additional substructure reacts on the structure, so as to reduce the structural vibration. The tuned damping device offers ease of installation and maintenance. This feature makes it suitable not only for new buildings but also for the renovation of existing buildings, which effectively reduces the project cost compared with aseismic structures. Dampers are commonly integrated into TMD devices to dissipate vibration energy, which exhibits nonlinear dynamic characteristics. Performing extensive scaling can result in significant size effects, which should be mitigated by conducting RTHS. For TLD systems, research indicates that conducting RTHS is advisable for large- or full-scale tests to mitigate size effects.16
With its strong nonlinear fitting ability, the artificial neural network (NN) has been widely used in the field of civil engineering in recent years, which can efficiently and accurately establish the prediction model of structural dynamic indicators. Zhang et al.17 proposed the long-short time memory (LSTM) NN based on physical information, which can establish a seismic response prediction model of damper shock-absorbing structures through dozens of seismic response records. Xu et al.18 established a nonlinear structural dynamic response prediction model suitable for earthquake excitation with arbitrary duration and sampling rate based on a recursive LSTM NN. Wang and colleagues19 established an intelligent computing framework for engineering structures based on the preattention deep & cross network based on preprocessed attention mechanism. Artificial NNs provide a way to improve RTHS methods. Bas and Moustafa20, 21 Chen et al.22 built a deep learning-based RTHS architecture, which used the LSTM network model as a numerical substructure. Tang et al.23 repeatedly loaded the physical substructure and established a constitutive agent model of its reaction based on the NARX network. The agent model was interactively simulated with the numerical substructure and realized the offline hybrid simulation of the seismic isolation structure based on the NNs.
Using NN technology to realize the hybrid simulation offline avoids the real-time interaction between the numerical solution computer and the loading equipment, thus reducing the real-time requirements, helps to apply complex numerical substructures that are difficult to calculate in real time to the hybrid simulation, and reducing the effect of loading delay. In the hybrid simulation, the numerical substructure can be solved by programming, or calculated by finite element software. In view of the fact that some commonly used finite element software such as ABAQUS and ANSYS cannot interact with the external models step by step, this study proposes an offline iterative hybrid simulation method based on NNs (OIHS-NNs), which can be applied to test objects with nondestructive physical substructure, and then verify the convergence and accuracy of the method by taking RTHS of the tuned vibration damping structure as examples.
2 THE OIHS-NN METHOD
Taking the TLD damping structure as an example, in the RTHS, the main structure is numerically modeled and solved, and the TLD with strong nonlinearity is physically loaded. The dynamic response of the structure and the reaction of the TLD interact online in real time, and the architecture of RTHS is shown in Figure 1.
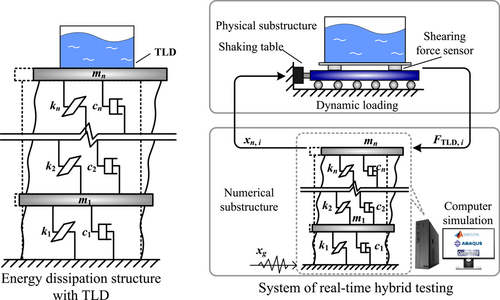
The RTHS can apply a larger TLD model to avoid overestimating the shock absorption performance of TLD due to the size effect.24
2.1 Offline global iteration strategy
Load the physical substructure in advance, then use strong nonlinear fitting techniques such as NNs to accurately model it, and finally complete the offline simulation of the numerical substructure and the physical substructure constitutive model. In the above process, the numerical solution and the loading equipment no longer interact in real time. Since there is no real-time numerical solution requirement, a larger, more refined and nonlinear numerical substructure can be further adopted. Therefore, the RTHS shown in Figure 1 can be realized through the offline hybrid simulation shown in Figure 2.
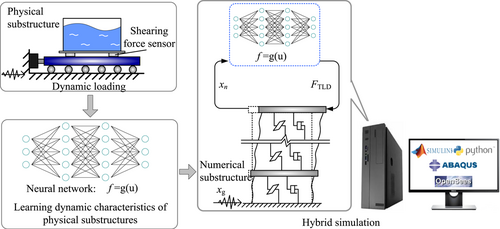
In particular, it is pointed out that the modeling of the physical substructure by NNs should be based on a large-scale data set, that is, a large number of preload tests on the physical substructure, so the offline hybrid simulation method is suitable for conditions in which the physical substructure is nondestructive. The data set is established by using the measured loading state of the loading device and the response of the physical substructure. The agent model trained is the mapping relationship between the actual load and dynamic response of the structure, which avoids the influence of the amplitude and phase errors of the loading device on RTHS.
There are general finite element software OpenSEES, ABAQUS, ANSYS, and so forth, and structural design finite element software SAP2000, ETABS, MIDAS, and so forth. Among the above six software, only OpenSEES can interact with the external models step by step, which makes it difficult to apply many large-scale, complex boundary, and nonlinear numerical models to hybrid experiments.
- 1.
Input the interface displacement time history xk−1 for the physical substructure, and calculate the interface reaction Fk, where k is the current iteration number.
- 2.
Input the external excitation time history xg and the new interface reaction time history Fk for the numerical substructure, and update the structural dynamic time history response xk.
The above iterative process can be represented by Equation (2), where k is the current iteration number.
() - 3.
If x* exists to make Equation (3) valid, then the FPI algorithm converges, and x* is the solution of the formula, otherwise the iteration divergence.
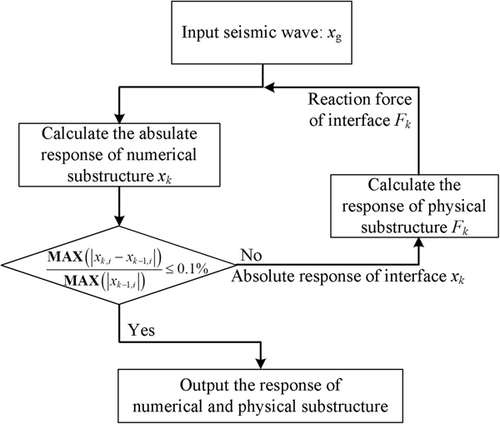
2.2 Time-series modeling method of LSTM NN
The multilayer LSTM NN is used to model and predict the nonlinear dynamic response of the physical substructure, and its topology is shown in Figure 4. LSTM NN is improved from recurrent NN (RNN). It was first proposed by Hochreiter and Schmidhuber26 in 1997 to deal with the disappearance of gradients in RNN training and to learn the long-term dependence of data.27 LSTM NN is a chain recursive structure with repetitive modules. Through the construction form of a multilayer stack, the nonlinear law representation ability of the model can be effectively improved. The model inputs the time-series data into the first LSTM layer and then takes the output of the first layer as the input of the second layer, and so on. After the last LSTM layer, the linear layer is used to integrate the high-dimensional information data output from the LSTM layer into the final prediction result of the model. LSTM neural network realizes autoregression by transmitting unit state and hidden state, and its time history prediction process is similar to the time-domain step-by-step integration method.
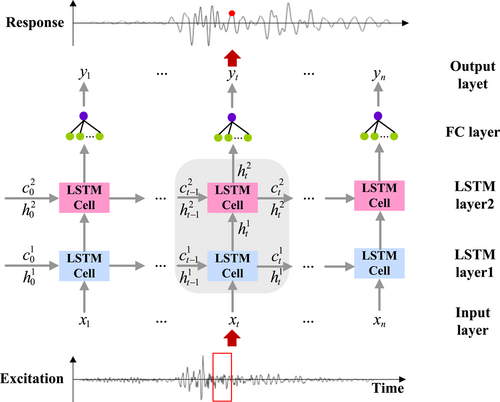
Each LSTM unit includes structures such as an input gate, a forget gate, an output gate, and a memory unit, as shown in Figure 5. Among them, the input gate controls whether the current input information is updated to the LSTM, the forget gate controls whether the memory before the current moment needs to be forgotten, and the output gate controls whether the current memory is used for output. These gating mechanisms enable LSTM to represent the timing dependence better.
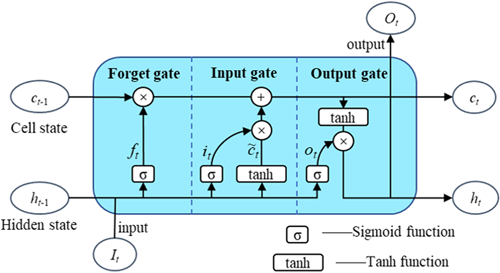
3 NUMERICAL VERIFICATION
The feasibility of the OIHS-NN method is verified by numerical simulation, taking the TMD damping structure as an example.
3.1 Numerical simulation of RTHS for TMD damping structures
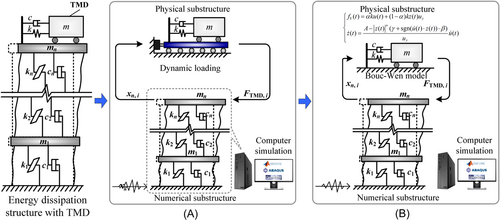
Layer | 1 | 2 | 3 | 4 | 5 | 6 | 7 | 8 | 9 |
---|---|---|---|---|---|---|---|---|---|
Mass 10⁵ (kg) | 10.1 | 9.89 | 9.89 | 9.89 | 9.89 | 9.89 | 9.89 | 9.89 | 10.7 |
Stiffness 10⁸ (N/m) | 3.1681 | 3.0604 | 2.8943 | 2.8060 | 2.7540 | 2.7008 | 2.6374 | 2.5824 | 2.5279 |
Layer | 1 | 2 | 3 | 4 | 5 | 6 | 7 | 8 | 9 |
---|---|---|---|---|---|---|---|---|---|
Yield displacement (m) | 0.035 | 0.018 | 0.019 | 0.019 | 0.020 | 0.020 | 0.021 | 0.021 | 0.022 |
mTMD (kg) | k (N/m) | ζ (%) | uy (m) | A | γ | β | j | α |
---|---|---|---|---|---|---|---|---|
1.801 × 105 | 1.255 × 106 | 10.73 | 0.1 | 1 | 0.5 | 0.5 | 1.5 | 0.2 |
- Abbreviation: TMD, tuned mass damper.
3.2 Accuracy verification of the LSTM model
To establish the neural network training data set, a total of 57 seismic waves were selected as TMD input excitations to calculate the reaction time history of TMD. The selected seismic waves and divisions of the NN train and test sets are shown in Table 4. The data in the test set did not participate in the error backpropagation process of model parameter optimization and was only used for testing the accuracy of the model.
Earthquake record | Duration (s) | Quantity | Division |
---|---|---|---|
East Japan | 300 | 26 | Train set |
Imperial Valley | 37.06–50.08 | 24 | Test set |
Coalinga | 58.16 | 2 | |
Whittier Narrows | 40.00 | 2 | |
Superstition Hills | 29.85 | 2 |
To make the amplitude generalization ability of the NN model meet the application requirements of structural seismic response prediction, the input peak ground acceleration (PGA) was selected as 1, 5, and 9 m/s2. The reaction time history under all the seismic waves was calculated, and the NN train and test sets were established.
Layer | Type | Input dimension | Output dimension |
---|---|---|---|
Input (LSTM1) | LSTM | n × (3 × 60) | n × 120 |
LSTM2 | LSTM | n × 120 | n × 60 |
Output | Linear | n × 60 | n × 1 |
- Abbreviation: LSTM, long-short time memory.
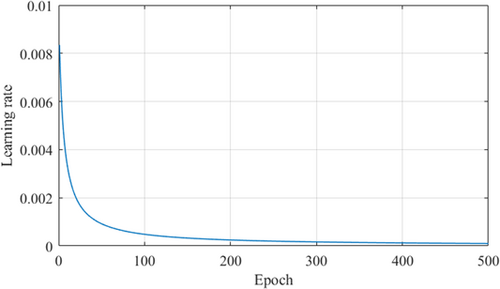
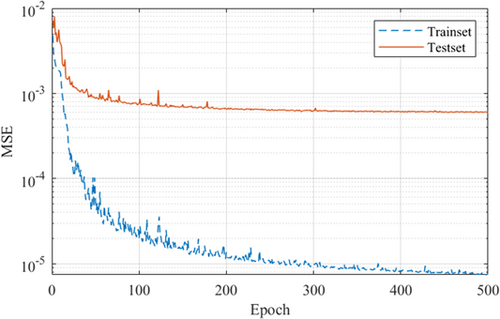
Taking the Imperial Valley earthquake input as an example, the time history prediction of TMD reaction under different amplitude excitations is shown in Figure 9.
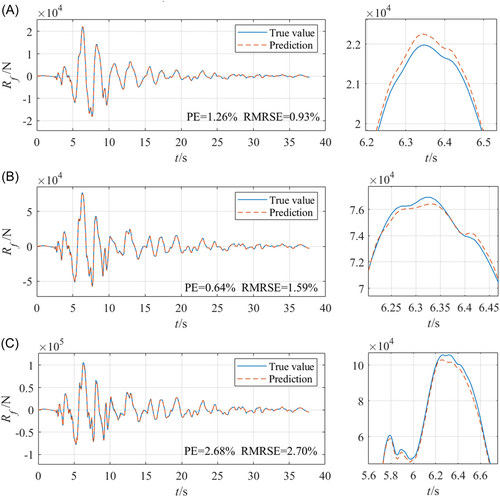
3.3 Convergence verification of OIHS-NN
The convergence of the offline iterative hybrid simulation method was verified. For this structure, the iterative process is shown in Figure 10.
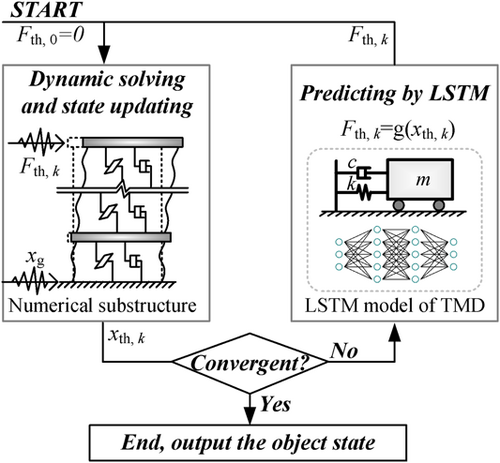
Input the Imperial Valley wave, and PGA = 4 m/s2. It has converged after 40 times of iteration, and the comparison between the iteration results and the RTHS numerical simulation results is shown in Figure 11.
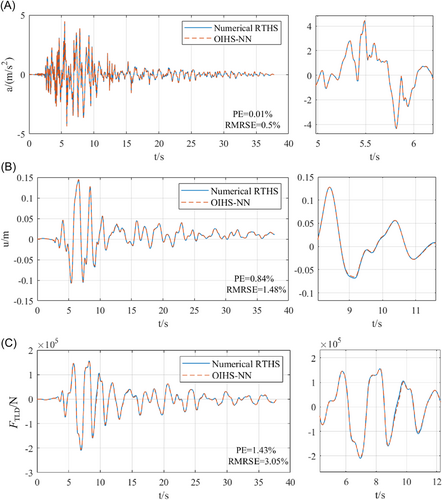
The results show that the LSTM NN has a strong fitting ability for nonlinear physical substructures, and the prediction PE and RMRSE are within 2.7%. The OIHS-NN method based on the FPI method converged after 40 iterations, and the errors of the structural response and TMD reaction time history of the overall structure is within 3.05%. The OIHS-NN can effectively converge and has high precision.
The analysis on the convergence behavior and accuracy of the OIHS-NN method with various PGAs was conducted. The 30 seismic records in the test set was employed for this purpose. The convergence condition count and the average iteration count for different PGAs are depicted in Figure 12, as well as the corresponding errors.
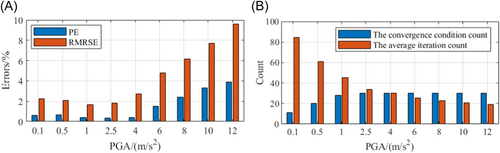
At lower PGAs, the OIHS-NN method necessitates a higher number of iterations, and in some cases may be even divergent. As the PGA gradually extends within the range of the training data set, OIHS-NN achieves stable convergence, and the iteration count diminishes with increasing PGA values. Furthermore, with the amplification of PGA, the convergence error also enlarges. Hence, to ensure the convergence and precision of OIHS-NN, it is necessary to appropriately select the PGAs of train set in accordance with the experimental objectives.
4 EXPERIMENTAL VERIFICATION
RTHS was used to verify the convergence and accuracy of the OIHS-NN method. The TLD damping structure was taken as an example, the RTHS system is shown in Figure 1. First, the RTHS of the TLD damping was carried out, and then the data set was established based on the table excitation and the TLD reaction. The LSTM model was trained and compared with the test results and the calculation results of the classical simplified model. Finally, OIHS-NN was carried out, and compared with the RTHS results and the numerical simulation results of the simplified model.
4.1 RTHS of TLD damping structures
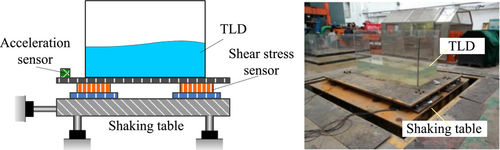
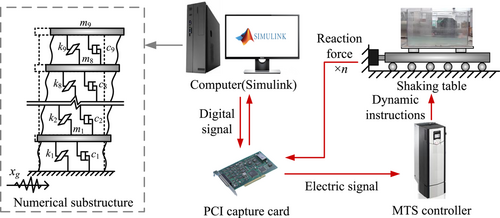
Considering the limitation of the loading displacement of the shaking table, to make the structure enter a nonlinear state, the critical yield displacement was reduced in different conditions. The variables controlled in the RTHS included seismic wave, PGA, mass ratio, and critical yield displacement reduction coefficient. The statistics of working conditions are shown in Table 6.
Seismic wave | PGA (m/s2) | Mass ratio μ (%) | Discount of yield displacement β | Quantity |
---|---|---|---|---|
El-Centro | 0.3–1.2 | 0.5–6 | 0.2–0.5/− | 20 |
Kobe | 0.3–2.5 | 0.5–6 | 0.2–0.5/− | 30 |
Northridge | 0.3–2 | 0.5–6 | 0.2–0.5/− | 18 |
Hachinohe | 0.3–0.6 | 0.5–6 | 0.2–0.5/− | 9 |
- Abbreviations: PGA, peak ground acceleration; RTHS, real-time hybrid simulation; TLD, tuned liquid damper.
4.2 Accuracy verification of the LSTM model
The input features of the LSTM model were excitation acceleration, velocity, and displacement, and the output feature was the reaction of TLD. The acceleration and displacement were measured by the sensors arranged on the connecting steel plate, and the velocity was obtained by the central difference method from displacement. The reaction was obtained by the shear force measured by the shear sensor minus the inertial force of the water tank and the connecting steel plate. The training samples of the LSTM model were divided into a train set and a test set. The six conditions in the test set were shown in Table 7, and the others were included in the train set. The data in the test set did not participate in the error backpropagation of parameter optimization, which was only used for testing LSTM model accuracy.
Condition | Seismic wave | PGA (m/s2) | Mass ratio μ (%) | Discount of yield displacement β |
---|---|---|---|---|
1 | El-Centro | 0.8 | 3.5 | 0.3 |
2 | Kobe | 0.4 | 1.5 | - |
3 | Kobe | 0.4 | 0.5 | 0.2 |
4 | Kobe | 2 | 1.5 | 0.3 |
5 | Northridge | 0.8 | 1.5 | 0.3 |
6 | Hachinohe | 0.5 | 1.5 | 0.2 |
- Abbreviation: PGA, peak ground acceleration.
To increase the amount of spatiotemporal information contained in each step in the training data, the test data with the original step length of 1 ms was downsampled to 20 ms. The dynamic response of TLD has a certain time lag, and to effectively describe this characteristic, the time window size was selected as 240, which is about twice the basic period of TLD. The structure of the LSTM model is shown in Table 8, where n represents the sequence length. In the training process, the dynamic learning rate with reciprocal decline was adopted, as shown in Figure 15. The decrease of MSE during training is shown in Figure 16. The above content was realized through the Pytorch framework in Python code.
Layer | Type | Input dimension | Output dimension |
---|---|---|---|
Input (LSTM1) | LSTM | n × (3 × 240) | n × 240 |
LSTM2 | LSTM | n × 240 | n × 120 |
Output | Linear | n × 120 | n |
- Abbreviation: LSTM, long-short time memory.

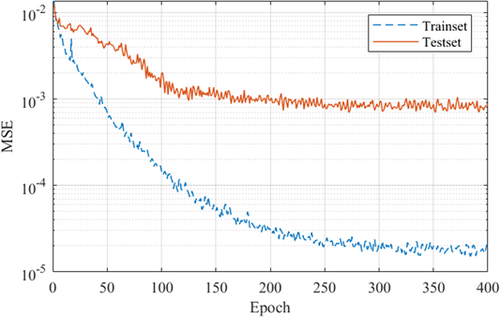
At the same time, the LSTM model was also compared with the TLD lumped mass model to verify the prediction accuracy. The TLD lumped mass model was proposed by Housner30 in 1957. It assumes that the liquid is incompressible and nonviscous, without rotation, and without wave breakage. The hydrodynamic pressure is divided into two parts, one part is the pulsating mass that generates pulsating pressure, and the other part is simplified as the oscillating mass elastically connected to the tank, which generates oscillating pressure, as shown in Figure 17.
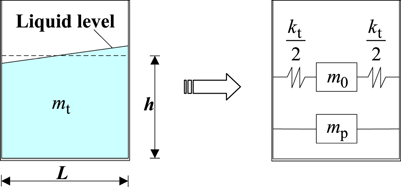
Comparing the calculation accuracy of the LSTM model and the lumped mass model, the time history of the TLD reaction is shown in Figure 18. For each working condition in the test set, the error of the LSTM model and the lumped mass model are shown in Table 9.
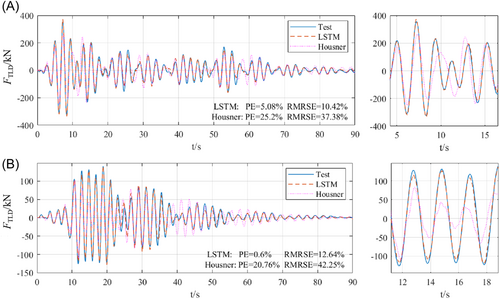
LSTM | Housner | |||
---|---|---|---|---|
Condition | PE | RMRSE | PE | RMRSE |
1 | 5.08 | 10.42 | 25.92 | 37.38 |
2 | 4.32 | 16.1 | 38.72 | 40.7 |
3 | 1.89 | 10.16 | 52 | 51.76 |
4 | 0.6 | 12.64 | 20.76 | 42.25 |
5 | 5.16 | 9.32 | 7.34 | 78.56 |
6 | 4.55 | 10.89 | 12.44 | 63.59 |
- Abbreviations: PE, peak error; RMRSE, root mean relative square error.
From Table 9, the LSTM model exhibits a stronger nonlinear representation ability for the TLD reaction. Its time history prediction PE is up to 5.16%, and RMRSE is up to 16.1%. The prediction accuracy of each working condition is significantly higher than that of the lumped mass model.
4.3 Convergence verification of OIHS-NN
The convergence and accuracy of the OIHS-NN method were verified. For the TLD damping structure, the iterative process is shown in Figure 19.
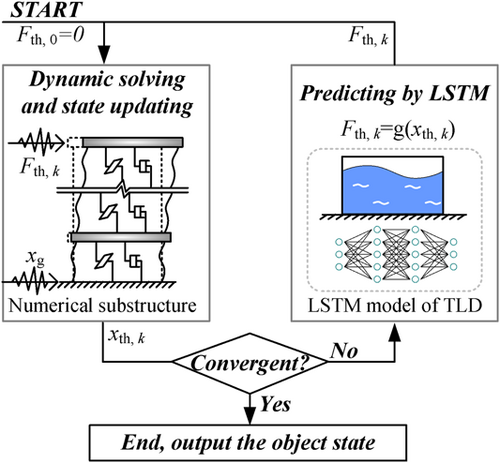
Where Fth,k is the TLD reaction time history of the kth iteration; xth,k is the absolute structural response time history of the kth iteration, xg is the earthquake time history, and the convergence criterion is shown in Equation (4). In the iterative process, the numerical substructure always satisfies Equation (16). In each iteration, the structural response time history , , , and the TLD reaction FTLD would be updated.
Taking test condition 1 as an example, the iterative process is shown in Figure 20. The test condition 1 took 24 iterations to converge. The iterative convergence results are shown in Figure 21, and are compared with the results of RTHS and the Housner model numerical simulation. The displacement and acceleration of the top layer of the structure and the reaction force of TLD all meet PE ≤ 2% and RMRSE ≤ 20%, which is significantly more accurate than the numerical simulation based on the simplified model of TLD.
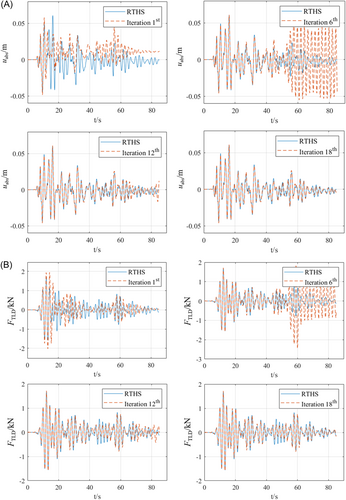
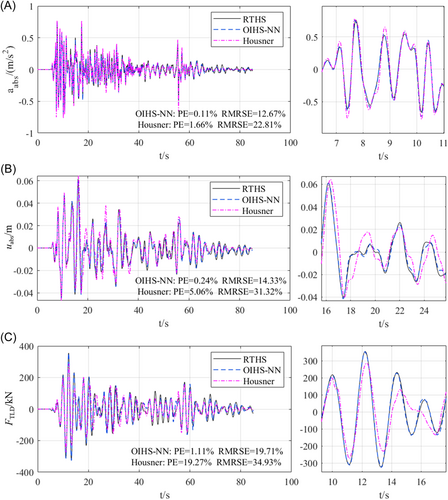
After a finite number of iterations, all the test conditions converged. The statistics of convergence speed and accuracy of each test condition are shown in Table 10.
Condition | Times of iteration | Acceleration | Displacement | FTLD | |||
---|---|---|---|---|---|---|---|
PE | RMRSE | PE | RMRSE | PE | RMRSE | ||
1 | 24 | 0.11 | 12.67 | 0.24 | 14.33 | 1.11 | 19.60 |
2 | 25 | 3.22 | 7.61 | 2.96 | 21.73 | 27.15 | 32.62 |
3 | 9 | 1.72 | 2.18 | 2.09 | 4.00 | 2.71 | 13.37 |
4 | 14 | 7.85 | 7.37 | 1.91 | 10.20 | 0.06 | 20.73 |
5 | 19 | 0.29 | 11.09 | 0.27 | 12.78 | 5.75 | 17.45 |
6 | 19 | 2.75 | 12.08 | 1.10 | 8.94 | 0.36 | 14.99 |
- Abbreviations: PE, peak error; RMRSE, root mean relative square error; TLD, tuned liquid damper.
In this chapter, the convergence and accuracy of the OIHS-NN method were verified by comparing it with the RTHS of the TLD damping structure. The test results show that the LSTM model has a strong fitting ability for the nonlinear physical substructure, and the predicted PE and RMRSE are within 2.7%, which is obviously superior to the accuracy of the simplified mechanical model. The OIHS-NN method can converge after a finite number of iterations, and has high accuracy. The PE of the structure response is within 8%, which has obvious advantages over the numerical simulation of the simplified model. However, it can also be found that some conditions had dependence on seismic waves, and the law and reason for this influence need to be further studied.
5 CONCLUSIONS
- 1.
The LSTM neural network model is used to predict the TMD reaction force with Bouc–Wen hysteresis, and its PE ≤ 2.68%. The model was also used to predict the TLD reaction with significant nonlinearity, and its PE ≤ 5.16%. The LSTM model's accuracy is significantly better than the simplified mechanical model, whose PE is 38.72%. The prediction accuracy of the neural network for the nonlinear dynamic response of the structure is high, and its nonlinear representation ability is much higher than that of the simplified mechanical model.
- 2.
It is verified by experiment that even if the physical substructure has strong nonlinearity such as the TLD, the OIHS-NN method could still converge within 25 iterations, the convergence met application requirements.
- 3.
The PE of structure response time history obtained by OIHS-NN method was less than 7.85%. Individual working conditions had dependence on the input excitation, whose error is slightly larger. Overall, OIHS-NN has much better accuracy than the numerical simulation of the simplified model. It is feasible to use this method for hybrid simulation.
In the follow-up work, the errors and convergence influencing factors of the OIHS-NN method need to be further studied, and the iterative algorithm will be improved to reduce the iteration time.
ACKNOWLEDGMENTS
The authors gratefully acknowledge the support of the National Natural Science Foundation of China (51978016) in the pursuance of this work.
CONFLICTS OF INTEREST
The authors declare no conflicts of interest.