Exploring Resource Recovery Technologies for Medicinal Cannabis Waste
Abstract
With the increased acceptance, research, and production in the medicinal Cannabis sativa industry, the natural follow-on effect has amplified the amount of cannabis waste generated. This magnification of biomass weight leads to an opportunity coupled with the legislative challenges regarding Δ9-tetrahydrocannabinol (THC) content present in the waste that must be destroyed or rendered unusable. It is necessary to find appropriate waste valorization methods to prevent this waste from inhabiting landfills. This study analyzes the waste generated through the production of medicinal cannabis and compares it with the current and potential waste management institutions that are appropriate to handle said waste. Valorization opportunities are discussed for each waste processing method. It has been determined that landfilling is the most unsustainable of cannabis waste management and is limited in generating resource recovery. Current waste management systems can be sustainable for biomass waste but must be embraced by cultivators and industry alike. Novel management methods allow for promising results of waste valorization, but more research is required to determine cannabis suitability.
1 Introduction
In recent decades, the societal opinion on cannabinoids from cannabis has altered into more of a favorable outlook in both the recreational and medicinal industries. The main cannabinoids found in Cannabis sativa, Δ9-tetrahydrocannabinol (THC) and cannabidiol (CBD), the active versions of Δ9-tetrahydrocannabinolic acid (THCA) and cannabidiolic acid (CBDA) [1, 2], have unique medicinal properties that have heightened interest into the research of cannabis [3]. Due to the widespread decriminalization of cannabis worldwide and the more straightforward manufacture of medicinal products, a soar in cultivation and production will naturally occur.
For example, sales of cannabis products, including medicinal and adult use, are predicted to soar from US$37 billion in 2021 to US$102 billion by the year 2026 [4].
This intensification of cannabis cultivation and the manufacture of cannabis products raises a concern about the disposal and removal of the cannabis waste generated. An issue with the cultivation of cannabis is that the plant generates great amounts of waste biomass that are not used for products but still contain psychoactive cannabinoids. This exacerbates the difficulty of disposing of its waste due to issues around legality and legal requirements. Cannabis waste must be rendered impossible or improbable for consumption, preventing persons from ingesting cannabinoids or propagating the plant [5]. Degrading the cannabinoid content to an ineffective level can become problematic depending on the available resources for cultivators and manufacturers. Fig. 1 highlights the issues and problems faced with waste generated from the medicinal cannabis industry. From this problem comes a natural opportunity to convert the waste into value-added products, such as fertilizers or biofuels, improving yield and profit from cultivation. Converting cannabis waste is essential if the industry contributes to a circular economy and follows the waste hierarchy's recommendations. Fig. 2 displays current legal methods of cannabis waste management that are available in industry and the outputs relating to each method.
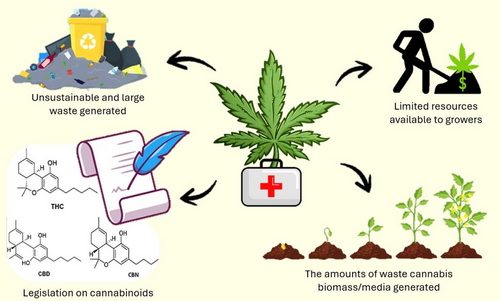
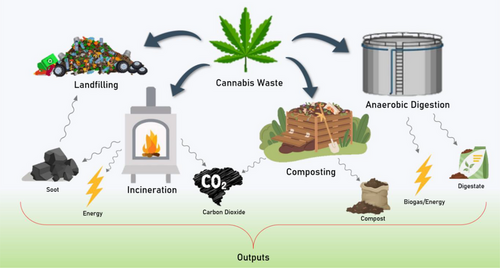
Robertson, Brar [6] call attention to the properties and amounts of waste generated by the medicinal cannabis industry from producing medicinal products. This article highlights that the main waste through cultivation is biomass, which is also the medium used. Packaging of products should also be included in the conversation of waste recovery and valorization.
With these increases in waste generation come new challenges involved with waste treatment, from which more advanced and novel treatment methods will be required to achieve a circular economy and valorization within the industry. The legislative issues regarding this waste must require more advanced processing methods than what is currently in industry to successfully treat and valorize this waste. These facts lead to more research required to be completed within this field to ensure these goals are met and operations are safety continued to allow for a refined medicinal cannabis industry.
The four current legal waste disposal methods are landfilling, incineration, composting, and in-vessel digestion, as shown in Fig. 1. Landfilling is placing waste in a designated area and then closing it off; incineration is the combustion of waste for energy conversion; and composting and in-vessel digestion are aerobic and anaerobic digestion (AD) of organic waste, respectively.
Other technologies that will be examined are hydrothermal processing, pyrolysis, and plasma gasification to determine their potential to create value-added products and contribute to this industry. Technical requirements, performance, environmental impact, generation of value-added products, economic feasibility, principle fundamentals, and methods of technologies will be analyzed for each technology.
Fig. 3 shows the number of publications on cannabis and cannabis waste in recent literature. From Fig. 3a, since the 2000s, there has been constant development in research within this area. However, although the number of research articles on cannabis waste valorization and the number of different waste management systems articles are growing, this happens not nearly as fast as the cannabis industry as a whole, as shown in Fig. 3b,c. It is imperative, for the sake of sustainably processing cannabis, to prevent cannabis waste from remaining in the biosphere and water sources/streams. Cannabis waste cannot be considered sustainable until industrial methods for biorefining cannabis waste are readily available for cultivators and companies in the industry.
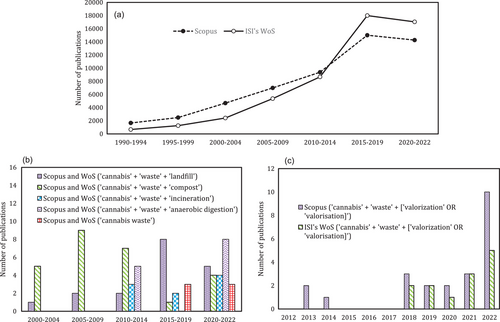
The method used for selecting literature to review was determined by using article databases and search engines using various keywords, including “cannabis,” “waste,” and “management,” with other appropriate words to discover appropriate information. The primary databases used for this study were Scopus and Web of Science.
Due to the social stigma and the controlled nature of cannabis, it has been difficult for researchers, through both execution and regulation, to study cannabis waste and the effects of cannabis waste on the environment [7]. A limitation over the years of cannabis research is the legislative challenges involved with receiving legal access to study cannabis, resulting in increases in articles written about the plant in recent years, as shown in Fig. 3.
Interest in cannabis research marginally increased in the late 2000s and has since consistently increased dramatically, as shown in Fig. 3. This can be attributed to the relaxation of legislation, a common limiting factor for research [8]. As more research is completed on cannabis, more uses can be found for the plant, allowing for more research, and so on. With research targeted at investigating the chemicals present in the cannabis plant, this will translate into a deeper understanding of the presence of molecules in waste generated and further uses this waste could be upcycled into.
As acceptance increases in the legalized medicinal cannabis markets, due to the mainstream influence and availability for research being eased, more companies and institutions will also be cultivating, manufacturing, and testing cannabis [5, 9, 10].
Legislations differ by countries and states, each having its own standards required for waste management. Canada, a country with the legalization of the plant for medical and recreational use, still has limits as to what companies can do with their cannabis waste. In terms of disposal, cannabis waste is to be destroyed or disposed of, with the option of composting being normalized in the country [6, 11]. New Zealand, a country where cannabis is legalized for medicinal use but not recreational, it is commonplace for waste to be autoclaved and then sent to a landfill. All cannabis disposal is required to be tracked and recorded within the company. Procedures for disposal are required to be expressed in “a way that renders the material unusable, unrecognisable and irretrievable” [6, 12]. In Japan, a country where it is illegal to possess cannabis for any reason, there are no regulations/requirements for cannabis disposal from a commercial standpoint [6].
In regard to investing in infrastructure to manage cannabis waste, given the uncertainty around the legalization for medicinal and recreational cannabis, it can lead to a reduction in investment into the area [13]. Companies are less likely to invest new assets into countries or states that have passed and repealed legislation, as this indicates regulatory instability [13]. With the legalization of cannabis processing on the trend of easing within certain areas of the world, these areas are likely to receive the most investment in new assets to efficiently manage this waste.
Tab. 1 highlights the most relevant research into cannabis waste management published in recent years. Most of the review articles on cannabis waste focus their attention on the removal of cannabinoids from the environment. Instead, the focus should be placed on treating cannabis waste from the source, preventing cannabinoids from ever reaching the environment. The studies of Brar, Raheja [14], Nan, Zhao [15], and Nan, Zhang [16] are examples of reviews focusing on cannabis waste and identifying this waste stream as an opportunity for valorization and creation of chemical compounds and biogas. Tab. 2 recognizes that waste management system can process which form of cannabis waste. Tab. 2 highlights important details from the most relevant literature relating to cannabis waste management and expresses any further work that is required in these articles. Tab. 3 highlights the advantages, limitations, and applicability of each technology mentioned in this study.
References | Review highlights | Areas where further work is required |
---|---|---|
Brar, Raheja [14] | Cultivation cannabis waste upgrading into useful products using numerous processing methods. Brings up disposal techniques for cultivated cannabis waste | Further analysis is required for alternative waste streams from cannabis production, such as extraction and manufacturing |
Nan, Zhao [15] and Nan, Zhang [16] | Accessing pre-treatment opportunities to improve generation of biogas from AD of Cannabis ruderalis straw and blackwater | These studies only focus on pre-treatment for anaerobic digestion and do not incorporate other methods of cannabis waste disposal |
Fontes, Maranho [17] | THC does not cause acute toxicity but produces oxidative strain and DNA damage on zebra mussels, as well as deprivation of alkaline phosphatase, intensifies transaminases and lactate dehydrogenase in carps | Research processes for wastewater treatment plants (WWTPs) to separate cannabinoids from treated water. Lacking information of processing cannabis waste at source |
How and Gamal El-Din [10] | Traces of THC have been discovered in a number of waste, surface, and drinking water sources. THC and THC-COOH pose a modest risk for dangerous consequences on the biosphere | Further research is required to remove cannabinoids from water supplies. Research should focus on treating cannabis waste generated at source |
Waste management system | Types of waste from cannabis industry | Valorization, throughput of waste |
---|---|---|
Landfilling | All waste | NA |
Incineration | All waste | Heat energy |
Composting | Biomass waste | Compost |
Anaerobic digestion | Biomass waste | Biogas for energy; digestate |
Technology | Advantages | Limitations | Applicability |
---|---|---|---|
Landfilling |
Cost-effective Simplicity |
Minimal resource recovery Limited sustainability aspects |
Cannabis biomass, growing media, growing supplies, chemical containers |
Incineration |
Reduced volume Energy generation Simplicity |
Carbon dioxide emissions Regulation |
Cannabis biomass, growing media, growing supplies, chemical containers |
Composting |
Generation of nutrient-rich compost Simplicity |
Requires large land usage Relatively expensive |
Cannabis biomass from cultivation (flowers, leaves, stalks, stems, root balls, failed plants) |
Anaerobic digestion |
Energy generation in the form of biogas Generation of nutrient-rich digestate |
Ununiform nature of waste can affect optimal operating conditions Need for trained personnel |
Cannabis biomass from cultivation (flowers, leaves, stalks, stems, root ball, failed plants) and post-extraction (waxes, fats, lipids) |
Pyrolysis | Generation of energy-dense products |
High temperatures are required Need for trained personnel |
Cannabis biomass from cultivation (flowers, leaves, stalks, stems, root balls, failed plants) |
Gasification | Generation of energy-dense products |
High temperatures are required Need for trained personnel |
Cannabis biomass from cultivation (flowers, leaves, stalks, stems, root balls, failed plants) |
Hydrothermal processing |
Generation of nutrient-rich hydrochar Generation of short-chain acids Non-toxic materials used |
Lack of fundamental understanding of technology High temperatures and pressures are required Need for trained personnel |
Cannabis biomass from cultivation (flowers, leaves, stalks, stems, root balls, failed plants) |
This study will review the waste generated from cannabis cultivation and manufacturing and will analyze the challenges, disposal methods, and potential biorefinery technologies that can influence or improve these outcomes.
2 Disposal and Valorization Technologies
2.1 Biological Processes
2.1.1 Landfilling
Landfilling, in its most simple form, is packing waste, as dense as possible, underground or in an allotted area above-ground, with the intention of biological decomposition to eventually occur and degrade the waste. Numerous considerations factor into the design of a landfill, including wind direction, the type of instruments used, procedure of filling, roadways to and within the landfill, the angle of incline of each daily cell, controlling exposure of the waste with groundwater, and the handling of equipment at the landfill location. Stormwater drainage, leachate collection, and methane collection systems are required to protect the surrounding environment of the landfill [18].
Landfilling is the most frequent form of solid waste disposal globally [19]. Worldwide, only 25 % of municipal solid waste is processed through other waste management options, such as recycling, with the rest resulting in landfill [20]. Generally, this form of waste disposal is combined with one of the other methods mentioned in this article, such as incineration, to reduce the size and weight of the waste, prolonging the landfill's lifespan [21]. Landfilling should be avoided where possible if a circular economy is to be achieved globally.
The main challenge with using landfilling as a means of disposal of cannabis waste is the legal issues that arise from the material containing cannabinoids. Because of this, cannabis waste is required to be rendered “impossible or improbable” to be consumed by persons [5] to prevent persons from ingesting and abusing cannabinoids within the waste material or propagating the material to make their own plants. To satisfy this requirement, cannabis biomass is typically combined with sawdust, sand, or another non-organic materials to create a 50/50 mix that can be disposed of through a landfill in the United States of America and Canada [22]. Creating this cannabis/non-organic mixture doubles the volume and weight of waste. If cultivators have this type of waste that is going to landfill and do not have non-organic material available on-site, further waste is required to be obtained solely to dispose of the cannabis waste. With this doubling of waste, the lifetime of landfills is reduced as further waste is required to be added just to dispose of the cannabis waste. Leachate is a biohazardous liquid produced through the passing of water through the masses throughout a landfill, dissolving and absorbing municipal waste [23]. Cannabinoids in the landfill can lead to the potential for leachate to contain these molecules. Waste piled within a landfill can produce gas, predominately methane or carbon dioxide [24]. Introducing cannabis waste into a landfill would have minimal impact on landfill gases produced in the landfill.
When other waste management methods are coupled with landfilling, the legislation challenge can be sidestepped by pre-treating the plant material, thus rendering the psychoactive substances unusable. An example is cannabis waste pre-treatment with incineration; at 232 °C, cannabinoids begin complete combustion, transforming the cannabinoids through a chemical reaction, producing non-psychoactive materials such as carbon dioxide, water, and other soot materials that can be deposited into landfill. It is important that when using landfilling as a means of disposal, there is pre-treatment, not only to reduce volume but also to recover some of the resources from the cannabis waste.
2.1.2 Compositing
Composting is the waste management process of microorganisms digesting and transforming organic material, within the presence of oxygen, into nutrient-rich compost that can be used to grow other organic-based plants. In a composting approach, cannabis biomass is mixed with other organic material, which decreases the percentage of cannabinoids in the mix, thus making this less of an issue to deal with.
Composting is the controlled act of adding soil to organic waste and leaving it for a period of time, allowing macro and microorganisms to digest the organic waste, in this instance cannabis [25-27]. The final result is a fertilizer that can be used as a source of nutrients for new plants. Waste is first decomposed by physical means, such as grinding and tearing, by macro-organisms [26]. Microorganisms are the main source for the majority of the organic breakdown that occurs through composting [25].
Disadvantages and challenges with composting include sizeable area requirements, odor pollution, greenhouse gas (carbon dioxide) release, net energy consumption, and the possibility for leachate production [28]. Depending on the area, rodents and other wildlife could become an issue when attempting to compost cannabis waste. These challenges must be considered in the implementation of composting at a cannabis cultivation site.
Due to waste cannabis being organic in nature, there is potential for that waste to be used for fertilizer production when it experiences compositing conditions [29]. Composting has reduced THC levels in cannabis waste, ranging from 0.47 % weighted to an undetectable <0.1 % amount [30]. A THC content below 0.3 % is generally considered acceptable in waste [30]. Rainbow Valley Farm, located in Sidney, Maine (US), completed tests determining how THC levels in cannabis waste changed during composting [30]. The cannabis waste was split into three differing piles, with percentages of 0.14 %, 0.19 %, and 0.47 %. After the first month of composting, all piles yielded a “not detected” limit, a reading below 0.1 % [30]. From this study, it can be concluded that THC can be degraded through composting methods under correct conditions. For example, in this study, the compost piles were stored outside, and temperatures raised up to 77 °C. Both UV light and temperature could thus have contributed to the degradation of THC.
In America, composting cannabis waste is growing in popularity compared to landfilling [31]. Transporting and logistics of transferring cannabis waste to suitable facilities for composting bring two cannabis-specific challenges: First, drivers need licenses to transport controlled substances legally, and second, there is the need to acquire alternative organic materials to mix with the cannabis for composting [31]. A number of companies have seen this as an opportunity to offer the removal of cannabis waste as a service, using the waste as feed for composting and producing fertilizer to sell.
Technical knowledge can also become a challenge for companies where the focus is on the cultivation of cannabis. Further, the act of composting has some resource requirements that might be difficult to meet, such as area, time, and access to non-cannabis organic waste. In areas where space is limited and there is no ready access to organic waste matter, these issues can hinder growers from considering composting as a feasible means of waste disposal.
2.1.3 Anaerobic Digestion (AD)
AD is the process of microorganisms breaking down organic matter in the absence of oxygen and transforming the material into biogas, mainly methane and digestate [32]. In order to produce biogas, organic matter is exposed to four different processes: hydrolysis, acidogenesis, acetogenesis, and methanogenesis in that order, which are all microbially driven [32].
Through the AD process, complex polymers, such as carbohydrates, are hydrolyzed into monomers and oligomers. The monomers and oligomers are then put through acidogenesis to create short-chain volatile organic acids. The organic acids undergo acetogenesis to create either acetate or hydrogen and carbon dioxide, which finally undergoes methanogenesis to produce the final products consisting of methane and carbon dioxide [33].
AD, similar to composting, takes advantage of microorganisms digesting and valorizing waste but in the exclusion of oxygen to create nutrient-rich digestate and biogas in the form of methane [28]. These products can be used for the fertilization of plants and energy production, respectively. AD is used to valorize a range of organic waste, including lignocellulosic biomass [34], food waste [35], animal manure [36], and sewage sludge [28, 37]. The methane produced is considered a sustainable source of energy [28, 38]. The digestate that is formed is rich in minerals and nutrients for plant flourishing and, as such, makes a competent fertilizer for other organic plant life.
Cannabis, being a biomass, organic material, allows for the opportunity of the waste to undertake AD conditions to be consumed and repurposed as biogas.
A study in Latvia researched the use of hemp (C. sativa L.) biomass as a raw material for AD. The study concluded that natural conditions in Latvia resulted in hemp that was able to successfully create biogas from AD, allowing for methane production. Greater efficiency of methane extraction was achieved through cutting the biomass into fine pieces before digestion [39].
Nan et al. analyzed the effectiveness of AD of Cannabis ruderalis straw and municipal household toilet water (blackwater) with different types of pre-treatment (ultrasonic and hydrothermal processing before digestion) [15, 16]. Both studies showed greater production of methane when AD was combined with these different pre-treatment methods.
The studies by Adamovičs, Dubrovskis [39], Nan, Zhao [15], and Nan, Zhang [16] indicate that cannabis waste can be a suitable source for methane production through AD. Other studies on using cannabis/hemp for AD include Kreuger, Sipos [40] and Matassa, Esposito [41]. The conditions for all of these studies can be found in Tab. 4. Generally, pre-treatment of cannabis can greatly improve the output of methane, and AD is a promising cannabis waste valorization process. There is a gap in these studies as soil remediation with processed digestate is a missed opportunity to add further valorization to this waste stream, and this has not been investigated within these articles.
References | Raw material input | Operating conditions | Outcome of methane generation |
---|---|---|---|
Adamovičs, Dubrovskis [39] | Hemp |
Chopped AD: 37–39 °C |
365 mL g−1 |
Nan, Zhao [15] | Cannabis ruderalis straw and blackwater |
40 kHz ultrasound pretreating at 100 W for 30 min AD at 35 °C |
399 ± 10.03 mL g−1 |
Nan, Zhang [16] | Cannabis ruderalis straw and blackwater |
Hydrothermal pretreating at 120 °C for 30 min AD at 35 °C |
351.35 mL g−1 |
Kreuger, Sipos [40] | Industrial hemp | Numerous AD pre-treatments at 40 °C | 199–256 mL g−1 |
Matassa, Esposito [41] | Hemp biomass residues |
Retting pre-treatment (soak in water), grounded, and sieved. Alkaline, acid, grinding, or untreated further AD: 36–38 °C |
Fibers: 422 ± 20 mL g−1 Stalks: 275 ± 7 mL g−1 Hurds (Unretted): 277 ± 13 mL g−1 Hurd (Retted): 280 ± 4 mL g−1 |
Asquer, Melis [42] | Cannabis sativa |
Drying at 105 °C and shredded AD at 39 °C |
53.8 ± 2.2 %wt |
Asquer, Melis [42] compared the specific gas production of anaerobically digested cannabis from an industrial plant with that of literature on other common vegetable feedstocks, finding that the specific gas production of cannabis was similar to that of other lignocellulosic crops but was inferior to highly degradable vegetable material. Analyzing Asquer, Melis [42] leads to the unlikeliness of cannabinoids being inhibitory for AD, whereas co-digestion with more degradable feedstocks would improve AD performance due to the optimized nutrient balance that can be achieved [32]. Asquer, Melis [42] does mention that they investigate specific conditions to evaluate if such conditions factor into the inhibition of AD.
AD of cannabis with other non-cannabis organic matter should be considered for future studies to improve process stability, overcome micro/macro nutrient imbalances, and improve economic viability in industrial applications.
The three studies Adamovičs, Dubrovskis [39], Nan, Zhao [15], and Nan, Zhang [16] processed their cannabis in mesophilic AD, between 25 °C and 45 °C. Of the three studies, both Nan, Zhao [15] and Nan, Zhang [16] concluded that the digestate can be used for soil amendment but did not specify any improvement from this action. Adamovičs, Dubrovskis [39] did not mention soil amendment using digestate.
Challenges that are associated with AD are low process efficiency and feedstock variability [32]. Low processing efficiency can be attributed to the four stages involved with AD. If one of these stages is delayed by any means, a ripple effect occurs, drastically affecting future stages. If an excess of long-chain fatty acids or NH3 is created, this can lead to the inhabitation of future stages. Changes in feedstock size, moisture content, cellulose, hemicellulose, and lignin content alter the ideal processing conditions for AD. The constant randomness of varying properties from biological feedstock can become a problem for processing and contribute to lowering process efficiency.
Some challenges specific to AD with cannabis waste processing can be the antimicrobial properties of cannabinoids, methanogenic toxicity that can affect AD microorganisms, and cannabis, similar to other biomass, being recalcitrant to biodegradation through the hydrolysis stage. Hemp and cannabis hold methanogenically toxic materials that can inhibit the hydrolysis stage, contributing to a lowered efficiency. Stem wood and bark extracts of hemp and cannabis are the leading inhibiting materials, with 50 % inhibitory concentration from 0.25 to 0.65 g chemical oxygen demand (COD) L−1, respectively. It should be noted that although this issue occurs, CBD does not cause methanogenic inhibition up to concentrations of 200 mg L−1, as the solubility of CBD is substandard [43]. Overcoming the hydrolysis issues of cannabis can be achieved through pre-treatment of the cannabis biomass via means of breaking down cell walls, allowing for greater lignocellulose degradability [15].
Correct monitoring of feedstock properties and AD processing parameters will reduce low processing efficiency, whereas a consistent feedstock from the same supplier could solve the feedstock variability challenges in terms of quantity and characteristics.
Dedicated trials with cannabis waste are required to determine optimal operating conditions for this waste material. Even so, changes in the feedstock's quality and physical and chemical characteristics can fluctuate processing performance [32].
Tab. 5 compares the previously mentioned biological technologies together.
Technology | Sustainability rating | Resource recovered | Challenges | Cannabis material accepted |
---|---|---|---|---|
Landfilling | Low | Energy |
Very limited resource recovery Pre-treatment required for cannabis |
Biomass, growing media, growing supplies, chemical containers |
Composting | High | Compost fertilizer | Area required for composting | Biomass from cultivation |
Anaerobic digestion | High | Biogas energy and nutrient rich digestate | Specialized knowledge required | Biomass from cultivation and post extraction |
2.2 Thermochemical Processes
2.2.1 Pyrolysis
Pyrolysis of organic material derives itself from the process of degraded waste in the absence, or limitation, of oxygen to produce solid, liquid, and gaseous products [44]. Different temperature ranges and residence times alter all three products’ characteristics and qualities. Pyrolysis acts as an endothermal reaction, consuming energy to allow the transformation of biomass material into energy-dense products [45]. As cannabis waste consists of biomass, this can allow pyrolysis to valorize the waste.
This process intends to degrade waste subjected to the non-reactive environment and convert waste into value-added products. Typically, the thermal decomposition of organic components occurs between 350 °C and 550 °C and will continue to between 700 °C and 800 °C in the absence of oxygen [46].
The prominent products produced through pyrolysis are an energy-dense synthesis gas (CO, CO2, H2, and hydrocarbons) [47], a biofuel that is commonly referred to as a bio-oil (containing water, aldehydes, acids, ketones, and alcohols), and a solid residue that is referred to as char or tar [46]. The synthesis gas that is produced can be used for the production of heat and electricity, whereas it can be processed further to produce various chemicals. Biochar is a carbon-based product converted from biomass in oxygen absent, elevated temperatures and is able to be used for soil fertilization, solid fuel, sensors, and components in batteries [48]. Biochar is typically very energy and nutrient-dense. Bio-oil can be used as a fuel or the production of other organic-based materials, such as phenols, furans, alcohols, acids, ethers, aldehydes, and ketones [47]. Wood vinegar, also known as liquid smoke, is one of the products that can be produced from fast pyrolysis [49-51], which is the aqueous phase collected when the resultant pyrolyzed product is separated from the oily fraction over a period of weeks [52]. Wood vinegar has a variety of different use cases but is mainly used for the flavoring of foods [49-51] and as herbicide/pesticides [52, 53].
Varying conditions to which the waste is subjected influence the generation of solid, liquid, or gaseous products. Maximizing liquid yield requires a low temperature, heating rate, and gaseous residence time. Maximizing gaseous yield requires a high temperature, low heating rate, and long gaseous residence time. Finally, maximizing char production requires a low temperature and a low heating rate [47].
There are three main types of pyrolysis: slow, fast, and flash. Slow pyrolysis is conducted at a lower temperature, less than 500 °C, lower heating rates, <100 °C min−1, and a longer residence time [54]. Fast pyrolysis consists of higher heating rates, 200 °C min−1, and a lower residence time, approximately 2 s [54]. Flash pyrolysis has much higher heating rates, 1000 °C min−1, and an even lower residence time, below 0.5 s [54].
Given the different conditions for pyrolysis to occur, slow pyrolysis is typically used to maximize the production of the solid yield, whereas fast pyrolysis is used to maximize the production of the liquid product yield [55].
The general changes that occur throughout pyrolysis processing start with the feedstock's temperature increasing. The initiation of the primary reaction at the elevated temperature releases volatiles that become char. A transfer of heat then forms from the hot volatiles to the yet unreacted feedstock, and as the heat from the volatiles releases, condensation occurs, starting secondary reactions that can form tar. Once the secondary reactions occur, they then become in competition with the primary reactions as they occur at the same time. Thermal decomposition, reforming, waste gas shift reactions, radical recombination, and dehydration can also occur and are dependent on the properties of the pyrolysis processing [47].
Within general biomass, hemicellulose degrades first, followed by cellulose and then lignin. A fair comparison can be made between the results of pyrolysis on wheat straw and cannabis, with only slight differences in the production of the main compounds produced [56]. The decomposition of cannabinoids occurs between the range of 200–250 °C [57], making pyrolysis a promising method within the legal requirements of waste disposal. García-Valverde, Sánchez-Carnerero Callado [58] highlight that with a gas chromatography injection, between 250 °C and 350 °C, Δ9-THC decomposes to Δ8-THC and then CBN. It is noted from this study that CBD decomposes to Δ9-THC and follows the above process. Due to the elevated temperature of pyrolysis, it can be assumed that a similar process occurs for those cannabinoids.
The first challenge associated with pyrolysis is the lack of research into the products produced during the pyrolysis process. There are many studies on the conditions for feedstock within the literature, but there is little research on the value of produced products. An example is biochar, where there is minimal research on its effectiveness as a fuel source and emissions produced through a burner [45]. Further research is required in these areas to address these issues. The industrialization of the pyrolysis process [45] and moisture content are two other challenges associated with pyrolysis as a means of waste management for cannabis. Although there are pyrolysis plants available in the industry, the uses of pyrolysis are limited to a few waste streams that are quite purpose specify [45]. To overcome this challenge, further research is required for the upscaling of pyrolysis plants within industry, particularly if this waste management system is to be used for cannabis waste. If cannabis is dried prior to pyrolysis, then the moisture content concern, similar to incineration, will be solved.
2.2.2 Gasification
Gasification is the process by which organic matter, such as cannabis biomass waste, is converted into energy-dense material under conditions of high temperature, without combustion, in a controlled environment.
Tahir, Tahir [59] conducted research into the gasification of C. sativa, utilizing the waste produced and creating bio-oil, biochar, and gas. The gas and oil are energy-dense products that contribute to electricity usage, and biochar can be utilized for fertilizer for soil remediation. The cannabis samples were ground, passed through a 500 µm sieve, mixed with nanocatalysts Co and Ni, and gasified at 300 °C. This research highlights the potential for gasification as a method for the valorization of cannabis waste.
Gasification has a few challenges to overcome before being a viable option for cannabis waste management; this includes scale-up issues and feedstock supplies for year-round use [60]. Scale-up issues revolve around the problem of decreased processing efficiency on the upscaling of the gasification process. This can be addressed by testing process optimization and carrying out simulations of the process. Feedstock supplies pose another issue, such that limited feedstock can limit the throughput of gasification and the costs of transport for feedstock. These challenges can be overcome by locating cultivating facilities near where gasification will occur, reducing transportation costs, and using mixed feedstocks, such as non-cannabis biomass waste, to continue production [60].
Plasma gasification, also known as plasma arc gasification, is an all-thermal process using plasma in an oxidant-starved environment as a means to convert organic matter into syngas that can be used for energy generation [61]. Currently, this technology is not used within the cannabis industry but has the potential to be a source of valorization of cannabis waste.
Plasma gasification is able to decrease the reaction time of converting municipal solid waste into renewable energy, predominately in the form of energy-dense biogas or syngas [62]. The plasma is able to generate additional active free radicals from molecules of the material that are inputted into the reactor. Molecules that are affected include water, nitrogen, hydrogen, carbon dioxide, and other gases. The result of the surplus of free radicals is highly reactive oxidants that promote organic material and biomass degradation in syngas [61, 63].
Biomedical waste plants use high-temperature pyrolysis and plasma gasification as a means to decompose and destroy organic and inorganic wastes via chemical and physical alterations [64, 65]. Using plasma gasification at up to 3000 K destroys all material and replaces it with simple, stable substances [64, 66, 67]. Plasma gasification has the ability to destroy drug-related material, lending to the possibility that the waste processing method could be used to render cannabinoids from cannabis waste, converting the controlled waste into useful materials.
Plasma gasification has been gaining popularity over the last decade as a means of green, carbon dioxide-neutral energy from biomass conversion technologies [68]. Plasma-assisted processing can either be allowed for pre-processing or post-processing, depending on the desired products from biomass. Plasma biomass valorization can be a promising lignocellulosic conversion process that can be used to create waste value-added products or energy [68]. As cannabis waste from cultivation largely comprises biomass, plasma-assisted processing of this cannabis waste is a promising, feasible solution.
Plasma gasification has its own set of challenges, including energy dissipation in hardware, frequent maintenance for electrode erosion, limited heat integration, and upscaling challenges that need to be considered if attempting to use this technology for the cannabis industry [68]. These issues can be resolved with further research into the area of plasma gasification, such as material compatibility for electrodes and pilot plant design, and by experimenting to improve the upscaling of such a process.
2.3 Hydrothermal Processes
Hydrothermal processing is the thermochemical process of exposing matter, commonly biomass waste, to water under high temperature (120–550 °C) and pressure conditions (20–150 bar); particularly in water's subcritical or supercritical state, altering the physical properties of reacting water [69-71]. This process allows the organic matter to be converted into either a solid (hydrochar), liquid (bio-oil and organic acids), or gas (hydrogen, methane, and carbon dioxide) [69, 70]. Due to the high energy density and nutrient concentration of these by-products, the waste biomass is able to be recycled as energy-producing products and nutrient-dense fertilizers [70]. Due to the lack of organic solvents required for processing and the use of organic waste as feedstock, hydrothermal processing acts as an environmental alternative means to create energy-dense products, as compared to fossil fuels, and to treat waste [72]. Water is non-toxic and widely available, which is an ideal characteristic for a solvent for any type of processing.
There are four main types of hydrothermal processing: thermal hydrolysis (TH), wet oxidation (WO), hydrothermal carbonization, hydrothermal liquefaction (HTL) [71], and hydrothermal gasification (HTG) [73].
Due to the organic nature of cannabis biomass, hydrothermal processing has great potential to apply cannabis waste as an organic biomass feedstock for operation.
Hydrothermal processing uses the change in water's physical and chemical properties at elevated temperatures and pressures while operating within a temperature range from which organic biomass undergoes physical degradation transformation. At these elevated temperatures and pressures, the hydrogen bonds of water become weaker, decreasing water's dielectric constant, acidity, and polarity. Because of this, water can act as a catalyst medium for reactions to occur [69]. As the dielectric constant of the water has decreased in this supercritical phase, the organic material and molecules are able to be dissolved within the water [69].
Hydrothermal processing is a biorefinery treatment method for various different types of organic material and biomass, and it is capable of effectively deconstructing and repurposing said material [74-77].
Hydrothermal technology has been present for a long period of time, with early research and uses dating back to the 1900's. Originally, during the 1900's, developments were focused on the synthesis of various minerals and crystals [78]. Due to the depletion of fossil fuel reserves, the environmental impacts of fossil fuels as a means of power generation and large amounts of organic solid waste generated globally have amplified the appeal of research into hydrothermal processing as a replacement for fossil fuel energy generation. Tab. 6 highlights the main conditions and products of different hydrothermal processing.
Hydrothermal method | Temperature range | Pressure range | Products | Atmosphere |
---|---|---|---|---|
Thermal hydrolysis (TH) | 120–200 °C | 20–150 bar | Pre-treated matter for further processing | Non-oxidative |
Hydrothermal carbonization (HTC) | 180–350 °C | 13–70 bar | Biochar | Non-oxidative |
Hydrothermal liquefaction (HTL) | 250–550 °C | 50–250 bar | Biocrude | Non-oxidative |
Hydrothermal gasification (HTG) | Above 350 °C | >220 bar | H2, CO2, and CH4 gas | Oxidative |
Wet oxidation (WO) | 150–320 °C | 20–150 bar | H2O, CO2, and short-chain acids | Oxidative |
Hydrothermal processing has promising qualities that allow the process to capitalize on the opportunity of waste cannabis valorization. First, hydrothermal processing has been proven to achieve the deconstruction of pharmaceutical drugs and waste fields [80-82], promising that cannabinoids could be destroyed using the same method of destruction, solving the legislative issue regarding the waste.
The challenges associated with hydrothermal processing are the fundamental lack of data, process design, energy intensity of processing, lack of process models, product separation, and technology commercialization [71]. Hydrothermal processing still lacks fundamental data and a limited understanding of reaction kinetics, as well as detailed fundamental studies explaining reaction pathways and reaction kinetics [71]. Due to the limited knowledge of these principles, it is difficult to create lab or pilot-scale plants to be then up-scaled, causing uncertainty in the use of such plants for industrial use, limiting the number of hydrothermal plants in literature and in industry. Coupling with the processing properties of high pressures and temperatures adds to the uncertainty of the technology in industry, creating further challenges with the implementation of the technology in industry.
The way from which hydrothermal processing is required to overcome these challenges largely lies in the requirement of further research into the technology in many areas. Whether research is completed in fundamental mechanisms, product separation, process design, or process modeling, all of this research will improve the understanding and commercialization of hydrothermal processing and allow the technology to be used for cannabis waste. Tab. 7 shows different studies of hydrothermal processing and the conditions cannabis and pharmaceuticals were subjected too.
Study | Materials | Conditions | Type | Yields/Results |
---|---|---|---|---|
Nan, Zhang [16] | Cannabis ruderalis straw and blackwater | 120–160 °C | Thermal hydrolysis | SCOD: 115 mg g−1 (+21.69 % on control) |
Jokinen, Eronen [83] | Birch and spruce bark and Futura 75 Cannabis sativa | 300 °C, 102 bar, and 114 min | Hydrothermal liquefaction | Hydrochar yield: 46 % |
Duan, Tao [84] | Hemp stalk powder | 275 °C, 30 min, and nitrogen environment | Hydrothermal liquefaction | Energy recovery: 88 % (hydrochar and bio-oil) |
Kanchanatip, Prasertsung [85] | Cannabis biomass waste | 170–230 °C, 10–27 bar, and 60 min | Hydrothermal carbonization | Energy yield: 70.41 %–82.23 % (hydrochar) |
Javid, Ang [81] | Bupivacaine, lignocaine, and pharmaceutical packaging | 200–350 °C, 30 bar, and oxygen environment | Wet oxidation |
COD reduction: Bupivacaine: 91.3 % Lignocaine: 87.8 % |
Javid, Ang [80] | Amoxicillin and Metronidazole | 200–350 °C, 30 bar, and oxygen environment | Wet oxidation |
COD reduction: Amoxicillin: 94.8 % Metronidazole: 83.9 % |
Javid, Ang [82] | Adrenaline and Progesterone | 200–350 °C, 30 bar, and oxygen environment | Wet Oxidation |
COD reduction: Adrenaline: 85.1 % Progesterone: 80.2 % |
2.3.1 Thermal Hydrolysis (TH)
TH is a non-oxidative hydrothermal process that occurs within temperatures between 120 °C and 200 °C, pressures between 20 and 150 bar, and in the presence of the inert gas nitrogen. This method of hydrothermal processing is typically used as a pre-treatment for various processing methods, such as AD, through solubilizing raw organic material [71].
TH can be used for wastewater sludge, seaweed [86], food waste, and other organic material's pre-treatment prior to use in other processes. TH enhances methane throughput and mass reduction when coupled with other waste-reducing and resource recovery methods, such as AD [87, 88]. AD contains four main stages: hydrolysis, acidogenesis, acetogenesis, and methanogenesis. Of these four stages, hydrolysis is the rate-limiting stage for lignocellulosic biomass, as complex organic molecules such as cellulose and lignin are reduced to their monomeric units, generating methane limiting particulates [86]. When TH is utilized, the hydrogen bonds of the cell walls of the organic matter are broken, which affects the cell wall decomposition [89]. This structural change improves the enzymatic hydrolysis of the matter, resulting in a larger biogas yield [86]. TH leads to the formation of volatile fatty acids, another factor that enhances biogas generation through post AD [90].
2.3.2 Hydrothermal Carbonization (HTC)
Hydrothermal carbonization (HTC) can transform biomass and organic solid waste into a value-added solid product, a porous, energy-dense, and nutrient-rich liquid. It is a non-oxidative process conducted at a temperature range of 180–350 °C and pressures between 13 and 70 bar [71].
Various plant-based materials can uptake the benefits of HTC processing. Corn cob and corn husk from maize produced coal-like fuel when subjected to HTC processing [91]. There is the potential of acetic acid being produced in the liquid on HTC processing of corn cob, which is optimal for further processing using AD [91, 92].
During HTC, oxygen and hydrogen, in the form of O/C and H/C ratios, are reduced first, destroying colloidal structures and reducing hydrophilic functional groups. The water then acts as a medium for dehydration and decarboxylation reactions to proceed. The dehydration and decarboxylation reactions yield H2O and CO2, respectively. Organic compounds then undergo condensation and polymerization to form larger molecules that then undergo further aromatization [69, 93, 94].
2.3.3 Hydrothermal Liquefaction (HTL)
Post HTC is HTL, from which the organic material decomposes and reacts even further to produce oily compounds. The HTL process involves hydrolysis of macromolecules into smaller molecules, conversion by dehydration and decarboxylation into smaller compounds, and then condensation, cyclization, and polymerization to create larger macromolecules [69].
HTL is the thermal chemical process from which selected biomass is combined with subcritical water at elevated temperatures and pressure, converting the matter into a liquid that is commonly referred to as bio-oil [70]. The conditions to achieve HTL are between temperatures of 250 °C and 550 °C at 50–250 bar [71, 95]. The process begins with the destruction of the cellulose, hemicellulose, and lignin, coupled with thermal depolymerization breaking down into smaller bio compounds [96, 97]. The conditions of HTL allow a similar process to recreate similar reactions of fossil fuels being produced deep underground in only a couple of hours [98]. The end result is an energy-dense bio-oil.
HTL processing using algae as a feedstock for production is able to produce bio-oil, with the properties of the oil-dependent on the selected pre-treatment and conditions during the hydrothermal processing stage [99].
2.3.4 Hydrothermal Gasification (HTG)
HTG is the hydrothermal process that reaches into the supercritical properties of water, conducting the processing at a temperature above 350 °C in the absence of oxidants. This thermochemical reaction creates a gas product of either H2 or CH4, depending on the reaction conditions. There are three types of HTG; aqueous phase refining, catalytic gasification in near-critical state, and supercritical water gasification [70]. Aqueous phase refining occurs at low concentrations, between 215 °C and 265 °C, with a catalyst, producing H2 and CO2. Catalytic gasification in near-critical state occurs between 250 °C and 400 °C, with a catalyst, while generating CH4 and CO2. Supercritical water gasification occurs between 600 °C and 700 °C and results in the production of H2 and CO2 without the use of a catalyst [70].
HTG allows for the processing of biomass to produce either H2 or CH4 or a mixture of both gases that can be used for energy production [100]. Biomaterials such as potato waste, sunflowers, kelp, and spent grain are all by-products used as feedstock for HTG to produce these energy-dense biogases [100]. Tab. 8 highlights the different types of HTG processes.
Type of gasification | Aqueous phase refining | Catalytic gasification in near-critical state | Supercritical water gasification |
---|---|---|---|
Temperature range | 215–265 °C | 350–400 °C | 600–700 °C |
Catalyst required | Heterogeneous catalyst (Pt, Ni, Ru, Rh, Pd, Ir) | Heterogeneous catalyst (Pt, Ni, Ru, Rh, Pd, Ir) | Does not require catalyst, but carbon can be used |
Products | H2 and CO2 | CH4 and CO2 | H2 and CO2 |
2.3.5 Wet Oxidation (WO)
Hydrothermal WO occurs under the reaction conditions of 150–320 °C and is pressurized between 20 and 150 bar with oxygen, keeping the water in a liquid state [71, 73]. Not only does WO have the benefit of reducing solid waste volume, but the process can also assist in the recovery of phosphate, reducing heavy metals in sludge, recovering value from waste, and producing organic acids as by-products from waste processing [73].
WO is an effective way to degrade non-recyclable solid waste materials. During WO, the acetic acid produced and the amount of solid reduction advance as the temperature of the reaction increases. WO at 280 °C has the ability to successfully reduce TSS concentration by more than 90 % [73].
Ahmad, Pu [101] conducted research on the effectiveness of WO as a single-step method for treating pharmaceutical wastewater. The study concluded, under optimized experimental conditions, that WO was able to remove 100 % of COD, 98 % removal of nitrate ions, 98 % removal of nitrite ions, and 68 % removal of ammonium ions.
Pharmaceutical grade drugs and medicines have displayed the ability to be interchanged using WO and instead converted into volatile fatty acids. Javid, Ang [82] conducted studies on adrenaline and progesterone where the hormones were subjected to WO for 60 min at a range of temperatures between 200 °C and 350 °C. The study concluded that both adrenaline and progesterone could be completely deconstructed, 250 °C for 5 min and 300 °C for 15 min, respectively [82].
Javid, Ang [80] used WO technology to deteriorate antibiotics amoxicillin and metronidazole into basic forms. Amoxicillin was able to achieve complete degradation at the temperature of 250 °C for the duration of 5 min. Metronidazole, on the other hand, achieved only 90 % degradation at the temperature of 350 °C for the duration of 5 min.
Javid, Ang [81] conducted research using WO processing to create ammonia from the degradation of anesthetics bupivacaine, lignocaine, and other pharmaceutical packaging. Bupivacaine had absolute degradation at the temperature of 250 °C after the duration of 10 min. Lignocaine was able to complete this degradation at only 200 °C after the duration of 30 min.
These examples show that because medical grade pharmaceutical drugs can be degraded using WO, there is the potential for THC to be destroyed using the technology in related conditions.
3 Technological and Societal Aspects
Technology readiness level (TRL) and societal readiness level (SRL) are well-established systematic reviews for developing technologies, highlighting the readiness of said technology for implementation throughout society. Originally TRL was a societal system created by NASA to track space-based technologies’ evolution. Since TRL's inception, the method has been adjusted to analyze various different technologies. The scale for TRL ranges from 1 to 9, where lab scale is shown by levels 1–3, pilot scale is shown by levels 4–6, and full scale by levels 7–9 [90, 102]. SRL has a similar structure by instead assessing the societal adaptation level for a technology. Both TRL and SRL, for technology, are required to progress at a similar rate, or else problems may arise for the adaption of technology in its selected industry.
Tab. 9 highlights the TRL and SRL for the discussed technologies in relation to organic solid waste treatment.
Treatment method | TRL | SRL |
---|---|---|
Landfilling | High | Moderate |
Composting | High | Moderate/High |
Anaerobic digestion | High | Moderate/High |
Incineration | High | Low |
Pyrolysis | Moderate/High | Low/Moderate |
Gasification | Moderate/High | Low/Moderate |
Hydrothermal processing | Low | Moderate |
4 Conclusions
As the cannabis industry grows, so do the challenges and opportunities associated with this industry. Although research on medicinal cannabis has intensified greatly over the last decade, research into cannabis waste management has not grown at the same pace. Currently, there is very little information publicly available on the management and valorization of cannabis waste, with the most common methods used for cannabis waste management being landfilling and composting. There are knowledge gaps around the possibilities for cannabis waste valorization through alternative forms of waste management.
From reviewing the different types of waste processing technologies, it is clear that each method has specific benefits, costs, and limitations that need to be considered when selecting the most efficient management method for handling cannabis biomass waste. Potential valorized products from cannabis waste are nutrient-rich fertilizer or energy-dense products, such as biochar and bio-oils, which can contribute to the mass and energy requirements for further medicinal cannabis production.
Future opportunities within this industry would include researching the technical and economic feasibility of novel methods of waste valorization, particularly plasma gasification, pyrolysis, and hydrothermal processing coupled with AD. Developing sustainability in the cannabis industry is imperative for this industry to contribute to a circular economy, and effective waste management plays a crucial role in this.
Acknowledgments
Acknowledgments for this article go to Callaghan Innovation and Green Relief NZ Ltd for the financial support and funding this study. Acknowledgments also go to Alison Robertson for her continued support and editing of this article.
Open access publishing facilitated by The University of Auckland, as part of the Wiley - The University of Auckland agreement via the Council of Australian University Librarians.
Conflicts of Interest
The authors declare no conflicts of interest.
Biographies
Kerry Jack Robertson Jack Robertson is a PhD candidate at the University of Auckland in Saied Baroutian's waste resource recovery research team. Jack's PhD is based on researching hydrothermal carbonisation and deconstruction of cannabis waste. Jack has completed a bachelors with first class honours in Chemical and Materials Engineering at the University of Auckland.
Rupinder Brar Dr Brar is a Certified Environmental Practitioner with over 12 years of experience in liquid and solid hazardous waste management. He holds a PhD in Environmental Engineering & Biotechnology from Lincoln University, New Zealand. Dr Brar has a unique blend of technical expertise coupled with hands on practical skills in the fields of hazardous waste management, contaminated site remediation, wastewater treatment and environmental management. He has several exciting research proposals to add value to cannabis waste and is currently investigating means to dispose of cannabis waste other than incineration. Rupinder as also contributed and is a director for Greenlab, working within the medicinal cannabis sector.
Parmjit Randhawa Dr Randhawa was recently a Research and Production Agronomist in a leading Australian medical cannabis company. He is a passionate researcher and has guided a talented team to be a world leader in medicinal cannabis research and cultivation. Dr Randhawa holds a PhD in Soil Science from Lincoln University, New Zealand. He has over 20 years of experience in India, Australia and New Zealand's agricultural research, food and horticultural industries. During this time, Dr Randhawa has carried out commercial research on pasture, cereals and vegetable crops under existing or altered agronomic management practices. The work also involved controlled environments to field scale research leading to the development of patented novel products. The quality of his research has been demonstrated by product commercialisation and publications in international journals.
Christine Stark Christine Stark has a background in Commercial Horticultural (Hochschule Geisenheim University, Germany) and her PhD in Soil Microbiology from Lincoln University. Christine worked as a Postdoctoral Researcher at Teagasc (Ireland) and Manchester Metropolitan University (England, UK) and investigated agricultural management and environmental change interactions. Most recently, her research on Psa in kiwifruit at Lincoln University Bio-Protection Research Centre was instrumental to the development of the commercial biological control agent Kiwivax (TM). Christine as also contributed and worked for Greenlab within the medicinal cannabis sector.
Saeid Baroutian Saeid Baroutian is a Professor of Chemical Engineering and Executive Director of the Circular Innovations (CIRCUIT) Research Centre at the University of Auckland. A sustainability advocate and cleantech entrepreneur, his work focuses on waste minimisation and advancing the circular economy. Saeid is the co-founder and Chief Scientific Officer of Nurox Hydrothermal, and co-founder and Chief Technology & Operating Officer of Gaiatech - two cleantech start-ups commercialising cutting-edge technologies for the safe and sustainable treatment of complex healthcare and hospital waste streams.
Open Research
Data Availability Statement
The data that support the findings of this study are available from the corresponding author upon reasonable request.