Waste Water Treatment after Removal of Thermic Oxides from Stainless Steel Welding Joints
Abstract
This work describes chemical methods of removal of thermic oxides from stainless steel welding joints, as well as waste water treatment. Thermal oxides were removed from the stainless steel surface using chemical and electrochemical procedures. A pickling paste that contains HNO3 and HF in different ratios was used for chemical cleansing of thermal oxides (A, B, and C). Electrochemical removal was done using an apparatus Magic Cleaner, and as electrolyte a solution H2SO4 + H3PO4 was used. Concentrations of chromium, nickel, and iron in the waste water have been determined using Method of Atomic Absorption Spectrophotometrics (AAS). Measured concentrations of Cr, Ni, and Fe are higher than allowed according to legal regulations of the Republic of Croatia. Therefore, an ionic exchange treatment of the waste water is recommended.
1. Introduction
Waste waters derived during chemical and electrochemical removal of thermic oxides of stainless steel welded joints are dangerous if they arrive into natural waterstreams. Dissolved heavy metals do not hydrolize, thus they can migrate to distances faraway from the release point, until they reach certain types of organisms in which they can accumulate (shellfish, crustacean, and fish) and thus enter human organism through food chain. Accumulation of heavy metals in liver and kidneys causes severe illnesses of chronic nature, that can often be lethal. So, for example, Cr, Ni, and Cd directly block enzymatic reactions and then the anticipated catalystic reaction does not occur.
In order to protect its water streams and groundwaters, every country uses laws and legal acts to prescribe marginal (maximal) values of hard metals concentration, allowed to dispose of into the public sewage system. In the Republic of Croatia the Regulation book on marginal values of indicators of hazardous and other materials in the waste waters [1] is in power. Prescribed values for Cr3+ + Cr6+ are 2.0 mg/L, for Cr6+ is 0.2 mg/L, for Ni2+ is 2.0 mg/L, for Fe2+ and for Fe3+ are 10.0 mg/L.
During welding of stainless steel a gas corrosion occurs on the metal surface, and metal oxides derive. When metal surface with thermic oxides is subjected to electrolyte, which happens in many cases, the change of the corrosive behaviour related to the same metal with no thermic oxides can be noticed regularly. Most common forms of corrosion in that case are pitting and crevice corrosions, which are obviously caused by influence of thermic oxides on the metal surface. Figure 1 shows oxides that derive during welding on the stainless steel surface.
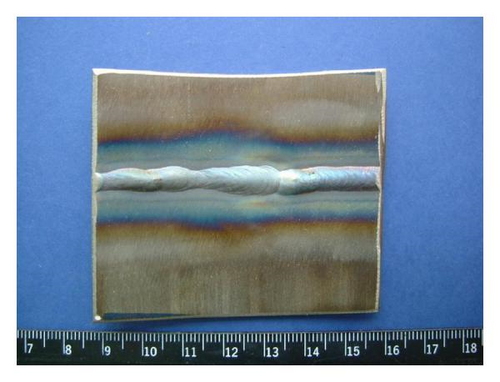
It has been proved recently that thermic oxides on stainless steel increase the possibility of the occurrence of pitting and crevice corrosions, in many solutions. Therefore, it is necessary to remove them. For their removal, we can apply the following procedures: mechanical, chemical, and electrochemical. Authors Juraga et al. [2], Esih et al. [3], Esih et al. [4], Kubo et al. [5], Kameo et al. [6] proved in their research that the removal of thermic oxides using chemical and electrochemical procedures shows more efficient results than mechanical removal, as far as the pitting corrosion is concerned.
2. Experimental Methods
Chemical method is based on controlled dissolution of nonhomogeneous coatings and on restoration of passive film. For protection, we usually use a mixture of acid 8–20 vol% of nitric acid (HNO3) and 0.5–5 vol% of hydrofluoric acid (HF).
Solutions that contain chlorides like hydroclorid acid (HCl) should be avoided in order to reduce the occurrence of pitting corrosion.
For the application of chemical corrosions the following conditions must be satisfied
- (i)
the surface must be free of organic contaminants
- (ii)
acid activity increases with the increase of temperature. The corroded surface that is being treated must be, after welding, cooled down to the temperature lower than 40°C,
- (iii)
formation of thermic oxides mostly depends on the welding process. With different welding processes, different oxide coatings can be formed, caused by uneven heat. Using the protective gas, we decrease formation of oxide coatings. The protective gas must, therefore, contain as less oxygen as possible.
For chemical removal of thermic oxides, there are also pastes and baths that can be found on the market. Pastes that are used for treatment of stainless steel weldings are made from the mixture of acids and binding agents, and baths are mixtures of acids (HNO3 + HF).
Chemical removal of welded joints was done using three different pastes:
- (1)
A ( 20% HNO3 and 4% HF),
- (2)
B (22–25% HNO3 and 5–8% HF),
- (3)
C (5% HF, < 20% HNO3).
On the surface of the welded part, using an acid resistant brush, we applied mentioned pastes. The corrosion time for all three pastes was 20 minutes. After those pastes were washed away from the welded part, using clean tap water. In derived sewage water, using Method of Atomic-Absorption Spectrophotometry (AAS), we determined concentration of Cr, Ni, and Fe.
Electrochemical method generally does not differ a lot from the chemical surface treatment technique. Applying the electrochemical treatment in similar way, only with usage of alternating current and appropriate electrolyte from the surface of the material, present damages melt. Electrochemical removal was done by means of apparatus Magic Cleaner. This electrochemical removal equipment uses invertible source of current. The current force during removal of thermic oxides was approximately 20 A, and as electrolyte, we used a solution of H2SO4 + H3PO4. Using this procedure, we completely removed oxides from the stainless steel surface.
Electropolishing treatment is also used for correcting the nonhomogenous parts of the material. The material from which thermic oxides are being removed is anode, while on the other side we have cathodes, and they are connected to the source of the DC (direct current). Thus we obtain better cleanness of the surface, and with that also a better shine, and resistance to the corrosion. This way of treatment is suitable for treatment of parts that are used in food industry, as it is easy to maintain the level of hygiene, since surface asperity is lowered down.
Stainless steel samples (AISI 316L) are cut by laser to 30 × 300 mm parts, 3 mm thick. On such samples we welded electrodes that contained Cr and Ni in the following ratios: electrode 19/9, electrode 29/9, and electrode 19/12/3.
Electrodes are rutile, and these types of electrodes, as stated, have excellent removal rate, small sprinkling, and clean weld surface. We have used chemical and electrochemical methods for removal of obtained thermic oxides A. H. Tuthill and R. E. Avery [7] and ASTM A 380-94 [8].
After chemical and electrochemical removal, we tested waste waters using Method of Atomic Absorption Spectrophotometrics (AAS), on the equipment ≪PYE UNICAM SP9 ATOMIC ABSORPTION SPECTROPHOTOMETER≫. Testing parameters on the atomic absorption spectrophotometer are presented in Table 1.
Chemical element | Wavelengt (nm) | Gas |
---|---|---|
Chromium (Cr) | 357.9 | Air/C2H2 |
Nickel (Ni) | 232.0 | Air/C2H2 |
Iron (Fe) | 248.3 | Air/C2H2 |
Testings of the susceptibility to pitting and crevice corrosions of all samples with and without thermic oxide (after removal by chemical or electrochemical) were preformed in accordance with ASTM G 48-92, using FeCl3 solution at 25°C. The samples were immersed horizontally in this solution for 72 hours, with the surface to be examined upwards. Afterwards, the samples were rinsed with water and ethanol and dried in air. On the observed surface of each sample, pits number is determined. The changes to samples with termic oxide and samples after chemical and electrochemical removal after exposure to FeCl3 solution are summarised in Table 3.
3. Results and Discussion
From results presented in Table 2 and Figure 2, we can see that concentrations of chemical elements chrome, nickel, and iron are several times higher than values legally allowed. The biggest pollution of waste waters is due to electrochemical cleaning, that gives the best results as far as demands for the weld cleanness are concerned. A satisfactory solution must be found for this problem.
Paste | Chemical element | Electrode | ||
---|---|---|---|---|
19/9 | 29/9 | 29/12/3 | ||
A | Cr, mgL−1 | 101.3 | 31.76 | 47.1 |
Ni, mgL−1 | 107.77 | 49.84 | 56.07 | |
Fe, mgL−1 | 397.2 | 206.56 | 245.17 | |
B | Cr, mgL−1 | 55.31 | 45.45 | 46.55 |
Ni, mgL−1 | 61.05 | 78.49 | 58.56 | |
Fe, mgL−1 | 299.23 | 305.02 | 279.92 | |
C | Cr, mgL−1 | 11.35 | 12.71 | 19.71 |
Ni, mgL−1 | 12.46 | 22.43 | 28.03 | |
Fe, mgL−1 | 101.83 | 166.51 | 219.59 | |
Electrochemical treatment | Cr, mgL−1 | 254.64 | 346.64 | 318.71 |
Ni, mgL−1 | 170.07 | 244.2 | 225.51 | |
Fe, mgL−1 | 482.14 | 515.93 | 506.27 |
Sample | Phenomena |
---|---|
With thermic oxide | many pits on surface |
After chemical removal thermic oxide | one pit on surface |
After electrochemical removal thermic oxide | no pits |
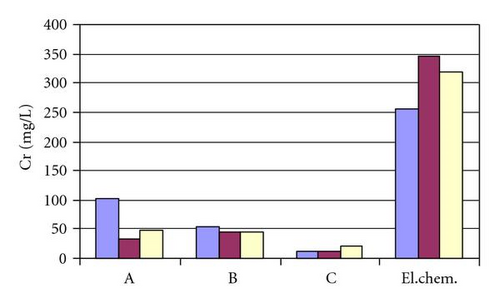
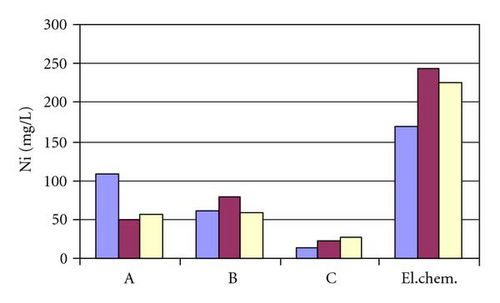
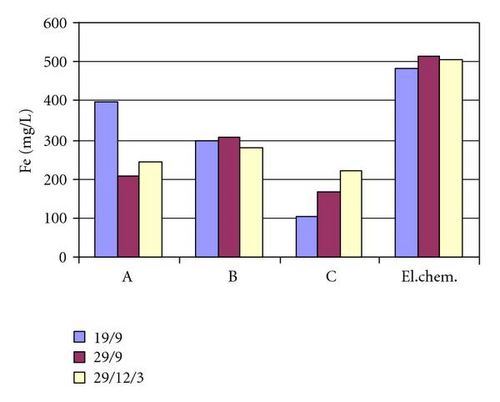
The least pollution of waste waters is obtained using a paste C on the weld, but unfortunately this result is the worst once examined visually. Using pastes A and B gives worse results regarding removal.
Concentrations of metals in waste waters were higher than legally allowed values. However, if we dilute waste water with enough fresh water (1 : 500), the concentration shall drop below the allowed values, thus such water could be disposed in the sewage.
Formally, this procedure satisfies the regulations, but we should have in mind the fact that such a concentration of metals still enters the sewage system, and those metals accumulate in living organisms, and reach, through the food chain, human body as well.
There are, in principle, two methods of metals removal from the waste water, and those are according to John et al. [9].
- (i)
irrecoverable (sedimentation with hydroxide ions (NaOH),
- (ii)
recycling (with ion exchange, reverse osmosis, etc.).
All ionic forms of metal that could be found in the waste water (Cr+3, Ni+2) can be sedimented with OH− ion in base medium accept for the Cr+6 ion, that has to be transformed to Cr+3 (reduced), using some strong reducent. Usually a solution of sodium hydrosulphite is used (NaHSO3).
Removal of metals from diluted waste water can be performed in a much simpler way, by flowing the water through ionic transformers [10, 11]. In this case diluted chromium and nickel can be recycled (i.e., used in some other processes—chroming and nickeling).
The results of the pitting and crevice susceptibility tests on samples pickled and unpickled are presented in Table 3.
4. Conclusions
In this work we have described a process of chemical removal of welded joints of Cr-Ni steel. Procedures described are those of surface preparation, before welding, welding processes, and processes of posttreatment of the weld. Chemical and electrochemical treatments of the weld have been described in detail.
In the experimental part, we described a procedure of preparation of samples for welding, chemical composition of the basic metal, electrodes and pastes for protection, that is, removal of oxide layer that has formed on the surface of the basic material during welding.
The waste water testing after completed procedure of protection was done using the Method of Atomic Absorption Spectrophotometry (AAS), on the equipment ≪PYE UNICAM SP9 ATOMIC ABSORPTION SPECTROPHOTOMETER≫ for Cr, Ni, and Fe.
Analysis results have shown that the most efficient removal of oxide layer after welding was done using the electrochemical method. Still, the concentrations of diluted metals (Cr, Ni, and Fe) were the highest with that method. The lowest results of removal were shown with the usage of paste C, where also the concentration of the diluted metals was the lowest.
If waste water is diluted enough (1 : 500), the concentration of metals in it reaches the legally prescribed levels. Such water can be disposed into the sewerage system, but there is high possibility that the metals shall accumulate in living organisms and at the end reach human body, that could cause chronic poisoning, and in extreme cases lead to death. Therefore, a treatment of waste waters is recommended.
The removal of metals from waste water can be done using method of sedimentation with hydroxides (irreversible) and by recycling (ion exchange or reversible osmosis).
Stainless steel samples with thermic oxide were tested for susceptibility to pitting and crevice corrosions by immersion in FeCl3 solution. These samples increased corrosion tendencies. Samples of stainless steel pickled chemical or electrochemical have no liability to pitting and crevice corrosions.