A Numerical Simulation Study of Focused Hydraulic Blasting in Coal Seams of Open-Pit Mines
Abstract
In the process of open-pit coal mining, traditional blasting methods often lead to issues such as uneven fragmentation, difficult vibration control, and significant dust pollution. Addressing how to improve blasting techniques to better align with the production characteristics of open-pit mining has been a focal point for both enterprises and scholars. This study combines focused energy blasting with hydraulic blasting through theoretical analysis and numerical simulation to address these challenges. The study theoretically explains the mechanisms by which stress waves and explosion-generated gases fracture coal seams during blasting. It also investigates the role of focused hydraulic blasting in enhancing the effectiveness of coal seam blasting, demonstrating that this method can improve the effectiveness of blast-induced stress, increase explosive utilization, and promote better crack development. Numerical simulations using ANSYS/LS-DYNA were conducted to study the focused energy structure. The results indicate that four-way focused blasting saves the most explosives and reduces the peak compressive stress by a small margin but significantly increases subsequent compressive stress, with a strain range that better meets the needs of open-pit mine blasting. The four-way focused blasting method was thus determined to improve coal seam blasting outcomes. Further simulations to optimize the focused groove structure revealed that a groove shape with a 60° focusing angle and a focusing depth of 4R/5 produces the best blasting results. Both theoretical and simulation results confirm that focused hydraulic blasting can effectively reduce mining costs, control blasting vibrations, and reduce dust emissions, contributing positively to the development of environmentally friendly mines.
1. Introduction
In open-pit mining, the overlying rock strata and surface soil above the coal seam must first be stripped away before coal extraction can proceed [1]. Typically, the surface soil can be easily removed using excavation equipment. However, the underlying rock layers are much stronger, making direct excavation difficult and likely to cause damage to the machinery. Therefore, blasting is commonly used to break up the rock into smaller fragments, making it easier for shovels and other equipment to transport the material out of the mining site [2]. Due to considerations of operational efficiency and cost, open-pit coal mining generally favors simple blasting methods, but this often results in poor energy utilization, uneven fragmentation, and suboptimal blast quality.
Focused hydraulic blasting is an advancement of smooth blasting technology [3, 4]. Compared to traditional smooth blasting, focused hydraulic blasting produces better surfaces and reduces over excavation [5–7]. This method mainly employs focused energy blasting, where a specially shaped focusing tube is placed around the explosive charge to direct the blast energy towards both ends of the borehole. This promotes crack development along the sides of the borehole, achieving a smooth blasting effect. Hydraulic blasting complements this process by using water bags in the borehole to transmit blast energy. Water, as a medium, releases energy more effectively than air [8]. The water wedge effect helps to enhance crack development along the sides of the borehole and extends the duration of the blast’s effectiveness by utilizing the water’s energy storage capacity [9]. Additionally, the water mist generated by the explosion can suppress dust inside the borehole, contributing to the construction of environmentally friendly mines [10, 11].
Extensive research on this method has been conducted both domestically and internationally, yielding promising results. Zhu et al. [12–14] and Tang et al. [15] used LS-DYNA to study the damage and fracture characteristics of coal and rock masses during shape blasting and analyzed the mechanism of crack directional propagation during the blasting process. Studies have shown that focused blasting relies on two primary mechanisms to propagate cracks: the sharp shockwave produced by focused blasting impacts the borehole walls, causing cracks [9], and high-pressure explosion gases further expand these initial cracks. Some studies have also explored using metallic focusing caps to create a metal jet during the blast to open up fractures [16]. Scholars have analyzed the crack evolution in single, double, and multiple borehole-focused blasting, concluding that focused blasting significantly affects stress distribution and crack formation, with the maximum stress on the borehole wall in the focused direction being 2.3 times higher than in the nonfocused direction [17, 18]. The most significant advantage of focused blasting is its ability to achieve directional crack formation in coal seams.
Deyong et al. used numerical simulations to demonstrate that when adjacent boreholes are blasted simultaneously, stress wave superposition creates a pressure equilibrium zone, leading to a fracture-free zone between the boreholes [19]. They proved that focused blasting can expand cracks directionally, bridging the gap between boreholes and promoting crack development for better fracturing. While two-way focused blasting is effective at forming fractures, it has a suppressive effect on stress in the nonfocused direction, making it more suitable for smooth blasting in tunnels and permeability enhancement in coal seams. However, open-pit mining requires multidirectional crack propagation to break and cut through rock masses. In response, Yangbo et al. proposed a multidirectional focused explosive charge based on the two-way focused charge. They found that multidirectional focused blasting created a fracture network with the main fractures aligned in the focusing direction and numerous auxiliary fractures [20]. This method significantly improved fragmentation compared to conventional blasting. Dunwen et al. further increased the number of focusing directions, comparing five-way focused blasting with conventional blasting in slightly weathered granite [21]. Their study analyzed crack distribution, residual borehole characteristics, and specific charge consumption, concluding that the new multidirectional focused explosive column could generate directional cracks, enlarge the fracturing range, and increase the proportion of explosive energy used in rock breakage.
The fundamental principle of focused blasting is to guide the propagation of blast shockwaves using specially shaped focusing structures. Different focusing structures result in different focusing effects. Changing the focusing structure directly affects the quality of the focusing effect. Wu et al. studied the thickness of the focusing shell in elliptical bipolar linear focused explosive charges and found that an excessively thick shell causes excessive reflection, leading to the formation of a large square groove in the focusing direction, which is detrimental to subsequent rock fracturing [22]. The selection of structural parameters for the focused charge is critical to the performance of the focused jet. Studies on elliptical bipolar linear focused charges have shown that the focusing angle significantly affects jet head velocity. You Yuanyuan et al. conducted mathematical calculations, numerical simulations, and field tests to determine the optimal focusing angle and concluded that a focusing angle of 75° yields the highest focusing efficiency [23].
As research on focusing continues to evolve, a variety of focusing structures have emerged, each capable of achieving different focusing effects [24]. The application scenarios for focused blasting continue to expand. Huai et al. used a C-shaped focusing tube for focused hydraulic blasting in tunnel construction, successfully controlling over excavation and significantly reducing blasting vibrations [25]. Jingguo et al. further improved the C-shaped focusing tube by sealing the focusing grooves, achieving excellent blasting results [26]. Yongxing et al. proposed an innovative spiral focusing structure, which is more effective at leveling the blast base and has been successfully applied in deep-hole blasting in a reclamation area in Zhoushan [27, 28].
In addition to selecting the focusing direction and structure, the uncoupling coefficient also significantly affects the focusing effect. When the uncoupling coefficient is too small, the focusing jet does not have enough time to cut through the rock. Conversely, when the uncoupling coefficient is too large, the focusing jet loses too much energy. Moreover, if the charge amount is too large, the blast shockwave becomes too intense, and the focusing jet does not have enough time to cut through the rock [29]. Wang et al. discussed the uncoupling coefficient for focused blasting, suggesting that the optimal range is between 1.67 and 2 [30]. In engineering practice and theoretical research, uncoupled water medium blasting has been shown to achieve better results compared to coupled charges and air medium blasting [31]. Jiu et al. compared the fragmentation distribution of concrete after blasting with air and water media under an uncoupling coefficient of 1.67 and found that the fragmentation sizes K50 and K80 for water medium blasting were 65% and 66% of those for air medium blasting, respectively, proving that water medium blasting can significantly reduce the fragmentation size [32].
Binwei et al. conducted comparative experiments and found that the peak stress exerted outward by hydraulic blasting is very close to that of coupled blasting and is 1.5 times that of air medium blasting [33]. This proves that the blast shockwave attenuates much less in water than in air. Wangyang combined focused blasting with hydraulic blasting, comparing the crack propagation in four explosive structures: conventional charges, focused charges, focused air coupling, and focused water coupling [34]. They found that focused water coupling produced the best blasting effect, with longer cracks in the focusing direction and a larger fracture zone in the nonfocusing direction.
Unlike previous studies, this paper is the first to combine focused blasting with hydraulic blasting in the context of open-pit mining. Theoretical research was conducted to investigate the roles of focused blasting and water medium blasting in coal seam blasting, and improvements to the application of focused hydraulic blasting in open-pit coal seam loosening blasts were analyzed. Numerical simulations were used to study different focusing structures, leading to the identification of a focusing structure suitable for open-pit bench blasting. This research has practical significance for reducing mining costs in open-pit operations. Additionally, hydraulic blasting helps control blasting vibrations and reduce dust, contributing to the construction of environmentally friendly mines.
2. Research Methods
This study focuses on the loosening blasting of coal seams at the Shengli no. 1 open-pit coal mine and investigates two key aspects: the rock-breaking mechanism of focused blasting and improvements to its structure. Through theoretical research and numerical simulations, the rock-breaking effects of focused hydraulic blasting are analyzed. Based on the coal seam blasting theory, as well as the principles of focused and hydraulic blasting, the mechanism of focused hydraulic blasting is explored. Building on two-way focused blasting, the study further investigates the mechanism of multidirectional focused blasting, using numerical simulations to statistically analyze crack formation patterns and determine the optimal number of focusing directions. Lastly, to meet the needs of large-diameter blasting in open-pit mining, the study investigates a large-diameter focused blasting structure suitable for such operations.
2.1. Mechanism of Focused Hydraulic Blasting
Blasting is the most effective method for large-scale loosening and fragmentation of coal seams and is widely used in mining. Its process is characterized by the release of immense energy that is difficult to precisely control. Focused blasting is an attempt at precision blasting in open-pit mines, playing a significant role in the advancement of mining technology. To understand the mechanism of focused blasting in breaking coal seams, it is first necessary to understand the basic mechanism of coal seam fragmentation by blasting. This requires integrating knowledge of both blasting mechanics and statics to clarify how blast energy acts on the coal seam. From this foundation, the mechanism of focused energy effects can be identified and further investigated.
2.1.1. Mechanism of Coal Seam Fragmentation by Blasting
Due to the instantaneous, complex, and uncertain nature of explosives, three main theories currently explain coal seam fragmentation by blasting. These include the blast stress wave theory, the explosion gas theory, and a combined theory that considers both stress waves and explosion gases acting together.
2.1.2. Mechanism of Focused Blasting
During blasting, the explosion products diffuse outward along the normal direction of the explosive charge’s surface. When the explosive is constrained into a sharp-angle shape, as shown in Figure 1, the explosion shockwave converges along the axis of the angle, forming a focused energy jet. The outward force in this direction is greater than in other directions. This phenomenon of explosive energy concentrating along the axis of the sharp angle and exerting greater outward force is known as the focusing effect of the blast. This focusing effect can be utilized to achieve directional crack propagation.
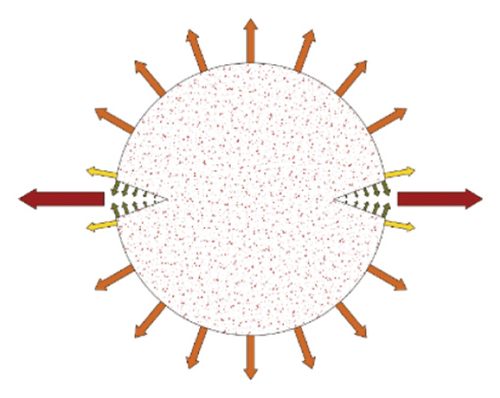
2.1.3. Study on the Mechanism of Hydraulic Blasting
Hydraulic blasting is a method that uses the pressure and energy generated by high-pressure water flow to break and fracture rock or coal seams. Its mechanism involves the transmission and diffusion of pressure formed by high-pressure water flow, leading to localized stress concentration and crack propagation. Simultaneously, the impact and shearing forces of the water flow accelerate the destruction process of the rock or coal seam, releasing kinetic energy and achieving energy conversion.
2.2. Study on the Efficiency-Enhancing Structure of Focused Blasting
Focused blasting can improve the distribution of blasting energy within the coal seam, promote crack development, and reduce the rate of fine coal generation. This study employs the ANSYS software to perform numerical simulations of coal seam blasting, analyzing the differences in stress variation and crack development under different focused explosive charge structures.
2.2.1. Model Parameter Design
2.2.1.1. Geometric Model Parameters
Referring to the selection of borehole diameters and arrangement of borehole grids in related open-pit coal mine blasting, a circular model with a diameter of 6 m is established to simulate the coal seam, with a 150-mm borehole in the center, as shown in Figure 2. The yellow part represents the coal seam model, the central circular blank is the borehole, and the red part is the filled explosive. To conserve computational resources, only the cross-section of the coal seam along the vertical direction of the borehole is simulated, observing the lateral blast results. The thickness of the coal seam and borehole models is set to 50 mm.
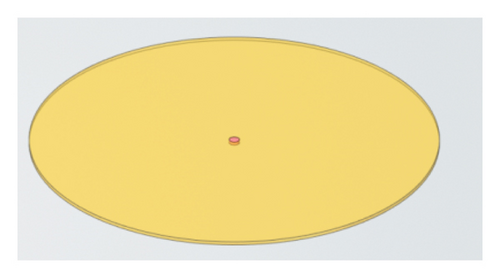
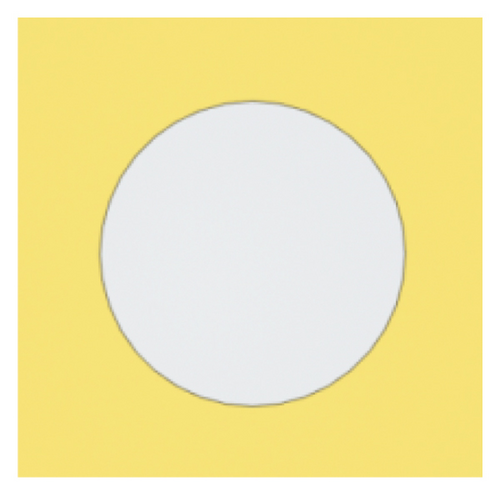
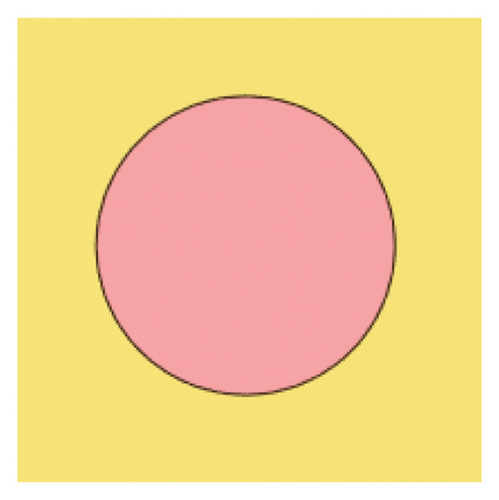
2.2.1.2. Material Simulation Parameters
The coal seam model uses the ∗MAT_PLASTIC_KINEMATIC model, which is suitable for isotropic and kinematic hardening plasticity models. It offers high computational efficiency and is widely applied in numerical simulations under large strain conditions, such as blasting. Additionally, tensile strain parameters of the coal seam are incorporated into the equation of state. Some parameters of the coal seam are listed in Table 1.
Young’s modulus (MPa) | 1.06e4 |
Bulk modulus (GPa) | 10.4 |
Hardening parameters | 1 |
Poisson’s ratio | 0.33 |
Shear modulus (GPa) | 4 |
Effective plastic strain in erosion units (m/m) | 0.05 |
The pressure transmission during the explosion of the explosive is simulated using a fluid-solid coupling method. The material model for air is selected as ∗MAT_NULL, with the equation of state being ∗EOS_LINEAR_POLYNOMIAL. The explosive used is ammonium nitrate fuel oil (ANFO), which is commonly used in coal seam blasting. Its material model is ∗MAT_HIGH_EXPLOSIVE_BURN, and the equation of state is ∗EOS_JWL. Relevant parameters are listed in Tables 2 and 3.
Pressure truncation (Pa) | −10 |
Coefficients of the equation of state, c4 | 0.4 |
Initial internal energy, E0 (Pa) | 2.5e5 |
Dynamic viscosity (Pa·s) | 0.0008684 |
Coefficients of the equation of state, c5 | 0.4 |
Coefficients of the equation of state A (GPa) | 371.2 |
Coefficients of the equation of state B (GPa) | 3.231 |
Coefficients of the equation of state R1 (Pa) | 4.15 |
Coefficients of the equation of state R2 (Pa) | 0.95 |
C-J pressure (GPa) | 2100 |
Coefficients of the equation of state | 0.3 |
Burst energy per unit volume (GPa) | 7 |
Initial relative volume | 1 |
Blast velocity (m/s) | 6930 |
BETA combustion symbol | Burns and explodes |
2.2.2. Study on the Optimal Focusing Direction of the Focused Groove
To investigate the effect of different numbers of focusing directions on the blasting stress, two different focused models were established and compared with conventional circular explosive charge blasting, as shown in Figure 3.
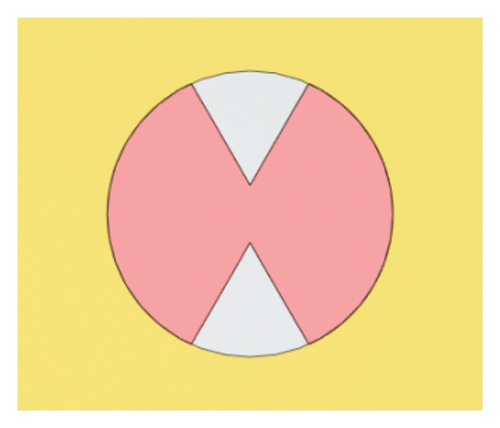
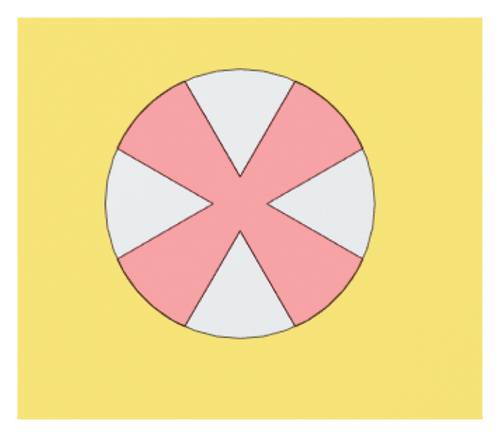
2.2.3. Study on the Optimal Focusing Structure of the Focused Groove
Building upon the study of focusing directions, two new schemes were proposed, resulting in a total of three different focused groove structures with varying angles and depths. These designs were used to explore the effect of the groove shape on focusing efficiency and the overall blasting performance in coal seams, as shown in Figure 4.
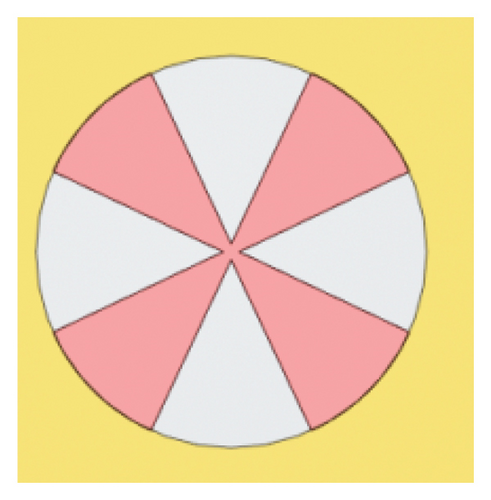
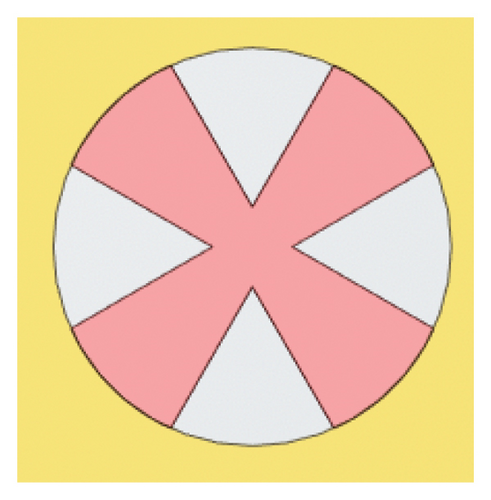

3. Results and Discussion
3.1. Study on the Mechanism of Focused Hydraulic Blasting
3.1.1. Study on the Mechanism of Coal Seam Fragmentation by Blasting
3.1.1.1. Blasting Stress Wave Destruction Theory
The explosion of explosives is an instantaneous, single-impact process. When the explosive detonates, it releases a large amount of heat, along with a substantial amount of gas. These high-temperature, high-pressure gases generate intense shock waves that impact the coal seam borehole walls and then continue to propagate through the coal seam as a medium.
During this propagation, the coal seam first undergoes compression from the shock waves. The closer the coal seam is to the borehole, the stronger the shock waves it experiences. Due to the coal seam’s dynamic compressive strength being much lower than the pressure of the stress waves, the coal around the charge will be excessively fractured. Figure 5 illustrates the process of the stress waves generated by the explosion propagating through the coal seam and then rebounding.
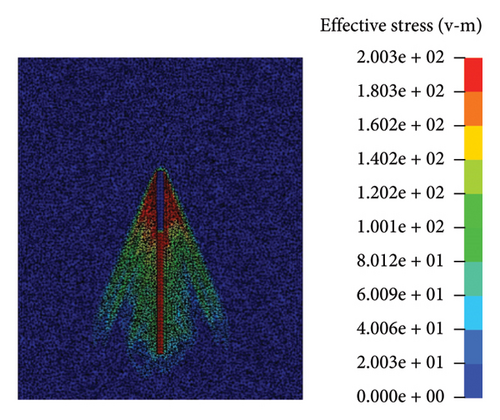
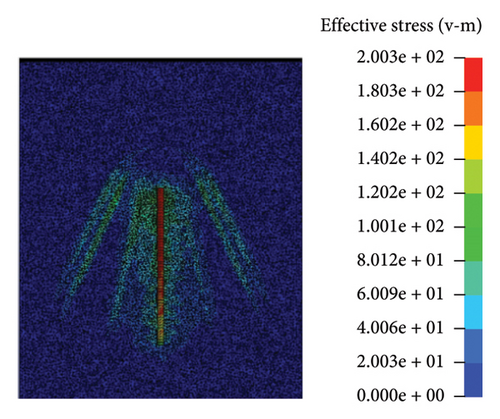
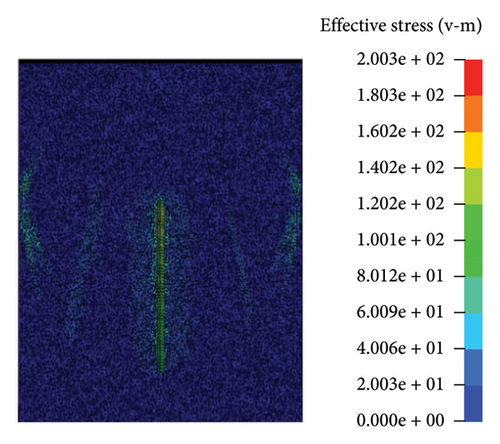
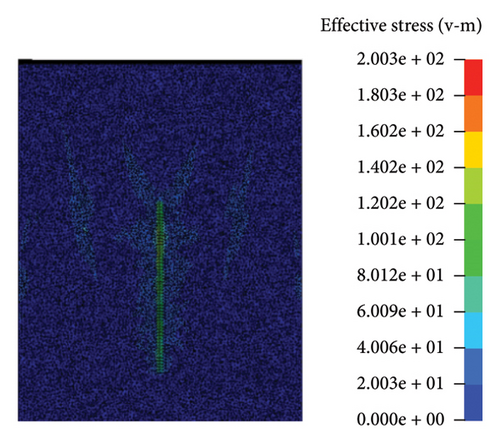
It can be observed that after the explosive in the borehole is detonated, multiple stress waves are generated in succession within the coal seam. These stress waves first compress the coal seam and then continue to diffuse outward. When the stress waves reach the free surface, they rebound. The rebounding stress waves overlap with the subsequent waves that are still diffusing, causing the coal seam to experience complex and intense stress impacts. These stress waves continue to propagate within the coal seam, rebounding repeatedly due to the generation of more free surfaces, creating increasingly complex stress patterns. This process leads to further fragmentation of the coal seam until the energy is exhausted.
3.1.1.2. Explosive Gas Destruction Theory
The theory of explosive gas destruction is based on rock statics and focuses on the large amount of gas produced by the explosion. These gases are generated instantly and are confined within the narrow space of the borehole, resulting in extremely high pressure. Once the initial blast shockwave has fractured the rock within a small range around the borehole, creating a crushed zone with many fissures, the high-pressure gas quickly fills these cracks. The gas then forces its way along the fissures, causing them to expand further into the coal seam. Since the gas becomes tightly wedged into the coal seam cracks, this effect is referred to as the “gas wedge” effect, as shown in Figure 6.
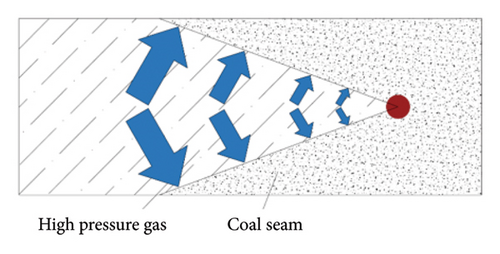
It is evident that significant stress concentrations can easily form at the tips of cracks. When the stress exceeds the coal seam’s static tensile strength, the coal seam is pulled apart, forming larger and more numerous fissures. The explosive gases then enter these new cracks, causing them to expand further. This process continues, progressively fracturing the coal seam until the pressure of the explosive gases decreases to a level insufficient to continue crack propagation.
As shown in Figure 7, the block represents the coal seam, and the black lines outline the expansion of the explosive gases. It can be seen that the explosive gases fill nearly all of the cracks created by the blast, continually promoting the development of the fissures initiated during the early stages of the explosion, thereby forming a larger fractured zone.
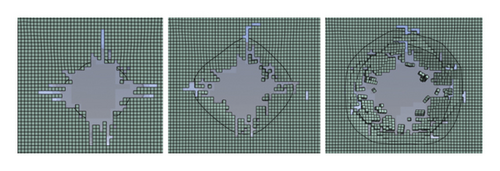
3.1.1.3. Combined Theory of Blasting Stress Waves and Explosive Gases
Both blasting stress waves and explosive gases can fracture coal seams, and the combined theory of their interaction provides a more comprehensive explanation of the coal seam fragmentation mechanism. This theory is widely accepted and can also be harmoniously integrated with the “three zones” theory of coal seam blasting fragmentation, which divides the blast-affected area into distinct regions. Figure 8 shows a schematic diagram of the three zones in coal seam blasting.
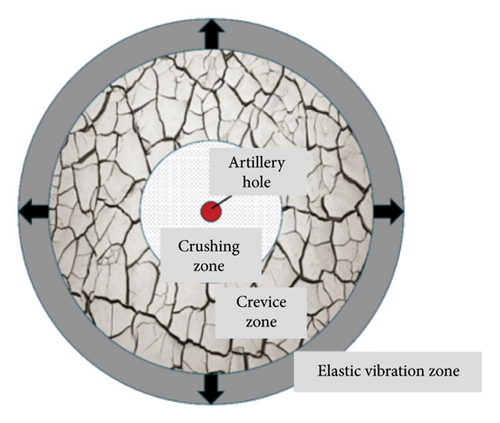
Assuming that the coal seam surrounding the circular borehole is completely homogeneous with no natural fractures and the explosive charge within the borehole is also evenly distributed, three concentric zones with distinct damage characteristics will form around the borehole when the explosive detonates. These zones, from innermost to outermost, are defined as the crushed zone, the fractured zone, and the elastic vibration zone.
3.1.1.3.1. Crushed Zone
The crushed zone is the area closest to the explosive borehole, located in the innermost part of the three coal seam damage zones. In this area, the coal seam is shattered into scattered fragments under the influence of the explosion. The radius of the crushed zone is generally considered to be 1.65 to 3.05 times the diameter of the borehole. During the initial stage of the explosion, the shock wave generated by the explosive impacts the borehole walls, which is the phase with the highest pressure. The surrounding coal seam is directly crushed into powder or small fragments, and this zone is the primary area where fine coal is generated.
3.1.1.3.2. Fractured Zone
The fractured zone is located in the middle of the “three zones” and is characterized by the development of numerous cracks, though the coal seam is not completely disintegrated. The radius of the fractured zone is generally considered to be 8 to 10 times the diameter of the borehole. In this zone, the intensity of the blast stress wave rapidly decays, and while it is no longer strong enough to fully crush the coal seam, it still induces tangential strain that exceeds the coal’s tensile strength, resulting in the formation of cracks. The high-pressure explosive gases primarily act in this stage, further promoting the development of cracks initiated by the stress wave, forming the fractured zone. Research suggests that in weaker coal and rock layers, explosive gases have a more significant effect on the generation of cracks.
3.1.1.3.3. Elastic Vibration Zone
Beyond the fractured zone is the elastic vibration zone, where the coal seam experiences minimal damage. The radius of the elastic vibration zone is generally believed to be no more than 20 times the diameter of the borehole. By the time the stress wave reaches this area, its intensity has drastically diminished, causing only elastic vibrations in the coal seam. Explosive gases do not reach this zone, and the coal seam only experiences micro-cracks and slight damage due to the elastic vibrations.
3.1.2. Study on the Mechanism of Focused Blasting
In an ideal air domain, when a long and uniformly charged circular explosive column detonates, the resulting shockwave propagates radially outward from the explosive column. When the shockwaves generated by two separate explosive columns meet, they merge and amplify, forming a stronger shockwave. Figure 9 illustrates the changes in the shockwave isosurface over time when two explosive columns detonate in the air.
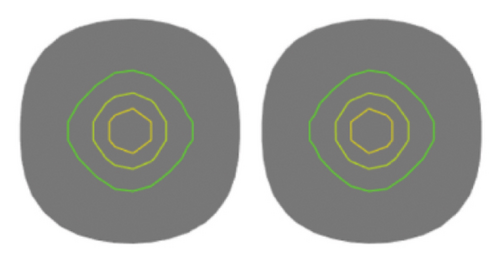
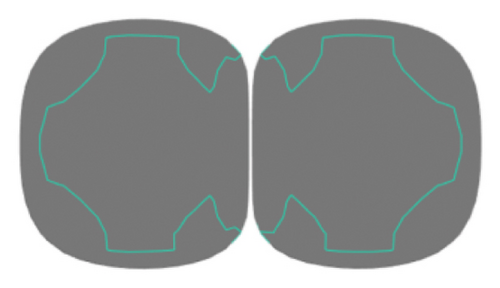
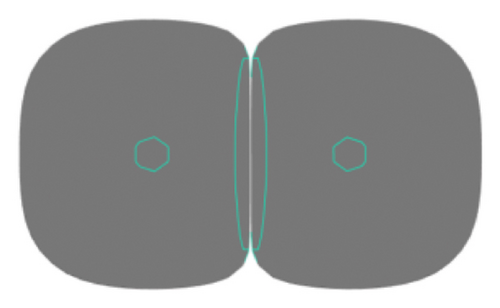

When there is only one explosive column, cutting a groove symmetrically along its diameter will cause the blast shockwave to propagate approximately perpendicular to the groove plane. Two shockwaves will meet and merge along the diameter line, redirecting and forming a stronger shockwave that propagates radially outward from the explosive column. This groove is called the focusing groove, and the axial direction of its angle is referred to as the focusing direction. The shockwave in the focusing direction is stronger compared to circular blasting, while the shockwave in the nonfocusing direction is weaker. Additionally, the density and pressure of the explosive gases are higher in the focusing direction and lower in the nonfocusing direction. The combined effect of the changes in stress waves and gas pressure results in the formation of more and deeper cracks in the focusing direction and fewer and shallower cracks in the nonfocusing direction. This is the basic principle by which focused blasting promotes crack development. Figure 10 below shows the morphology of the explosive gas for a circular blast and a polygonal blast with grooves cut at both ends, and the black part of the figure shows the explosive gas.
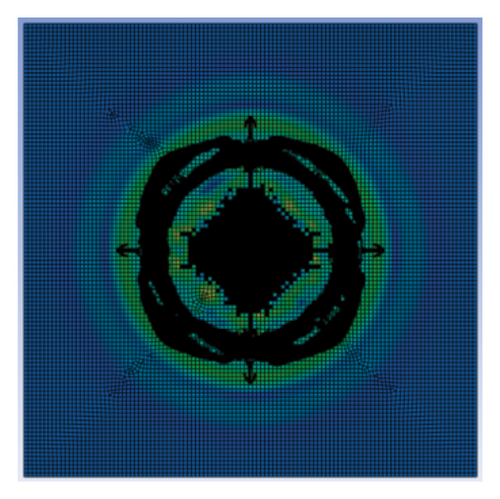
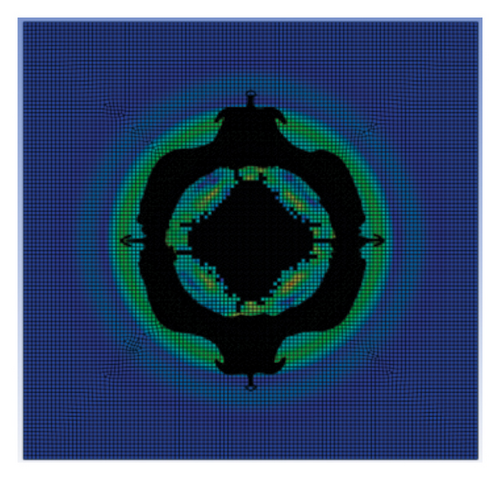
3.1.3. Study on the Mechanism of Hydraulic Blasting
In extensive studies by scholars, water as a blasting medium has demonstrated superior properties compared to air in coal and rock blasting. It is generally believed that water medium blasting experiences less energy loss during shockwave transmission compared to air medium blasting. This is partly because water is less compressible than air, so the energy loss from water compression under shockwave impact is smaller. Additionally, the difference in wave impedance at the interface between water and coal/rock significantly affects the transmission of stress waves. The differing speeds of sound and wave impedance between water and air result in different reflection characteristics when the shockwave enters the medium. The shockwave reflection is smaller when it passes from water to rock, allowing more energy to be transmitted.
Moreover, the high temperature and pressure caused by the explosion decompose water into hydrogen and oxygen, absorbing a large amount of heat. The decomposition products participate in the blasting reaction, extending the detonation time, smoothing energy release, reducing vibration, and slowing stress attenuation, which provides an energy storage and shock absorption effect. Additionally, the instant high temperatures from the explosion vaporize part of the water medium into bubbles, and when these bubbles collapse, water flows back, creating bubble pulsations. These pulsations transmit oscillations to the coal and rock layers, enhancing their destruction.
Beyond pulsation, the water medium in the borehole also produces a water wedge effect on the cracks. When the blasting stress wave initiates cracks in the borehole wall, water moves to the crack tips. The surface tension of the crack draws water droplets into the crack, where the water acts like a wedge, enlarging the crack and concentrating stress at the crack tip, further promoting crack development.
3.2. Study on Focused Blasting Structures
3.2.1. Study on the Optimal Focusing Direction
3.2.1.1. Simulation of Conventional Circular Charge Blasting
The model for conventional circular charge blasting is established as shown in Figure 2, with a circular charge area of 17,671.46 mm2. A numerical simulation was conducted for 1200 μs on the circular charge blasting model. The postblast coal damage pattern and the shape of the explosive gases are shown in Figures 11 and 12.
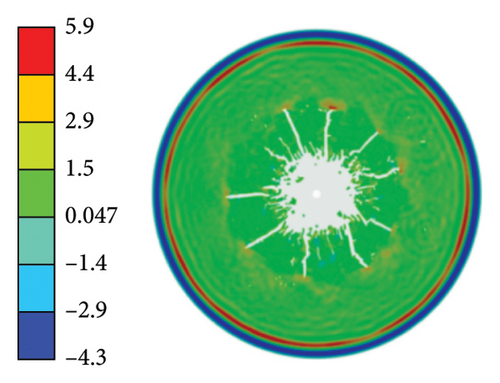
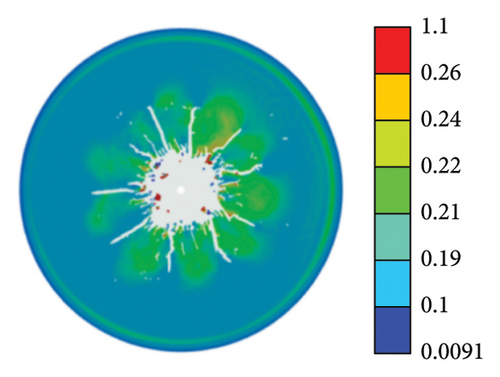
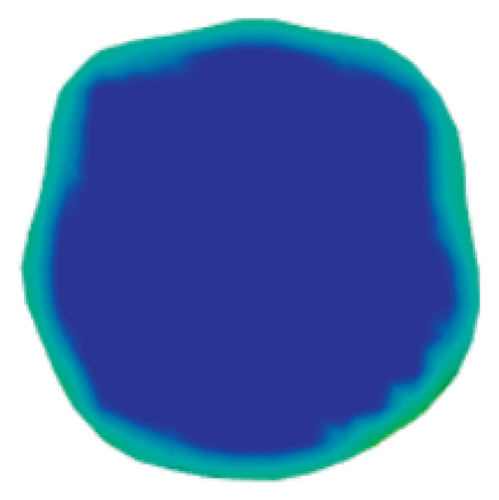
The circular charge blasting produced cracks that expanded uniformly outward, with the coal seam strain also displaying a circular distribution. Although the coal seam model lacks perfect homogeneity due to the tetrahedral-dominated meshing method, which causes slight directional tendencies in the cracks and strain, the circular distribution pattern around the borehole is still apparent.
The maximum principal stress within 1200 μs after the blast was recorded at 10 μs intervals, and the detailed maximum principal stress values were obtained. The trend of stress variation is shown in Figure 13.
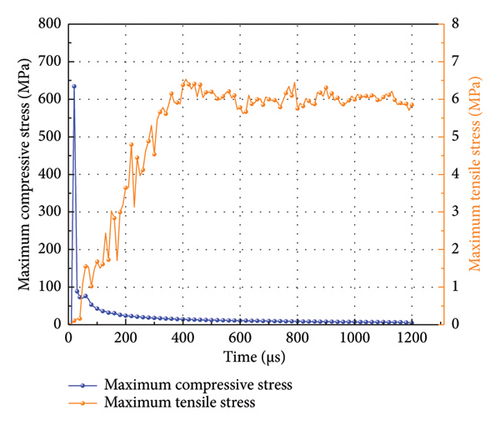
After the explosion, the maximum compressive stress experienced by the coal seam immediately surged, reaching its peak of 634.310 MPa at 20 μs. The maximum compressive stress then rapidly decreased to below 100 MPa within 10 μs, after which the rate of decay slowed down. The maximum tensile stress, starting at 0 MPa, rose gradually and stabilized at around 6 MPa. Before 1170 μs, the maximum compressive stress remained higher than the maximum tensile stress, but the gap between them gradually narrowed. At 1170 μs, the blast stress wave reached the coal seam boundary and began to decay rapidly due to the presence of the free surface. The average compressive stress, calculated from time points after 100 μs, was 12.850 MPa.
3.2.1.2. Simulation of Two-Way Focused Blasting
The two-way focused blasting model is established as shown in Figure 14. The yellow represents the 6-m-diameter coal seam model, with a 150-mm-diameter borehole in the center. The red represents the two-way focused explosive model, with an explosive area of 13,832.36 mm2, a 22% reduction in explosive charge compared to the circular charge model.
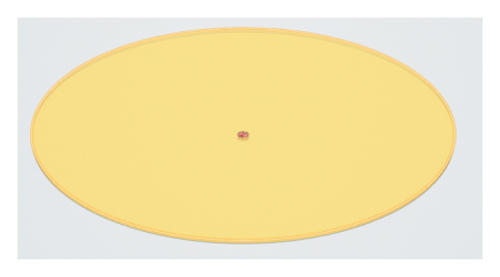
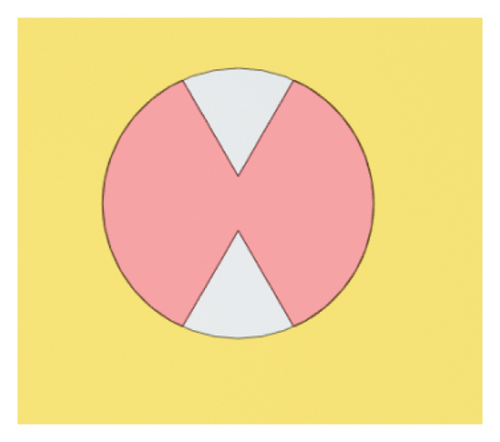
A numerical simulation was conducted for 1200 μs on the abovementioned blasting model, and the postblast coal damage pattern and the shape of the explosive gases are shown in Figures 15 and 16.
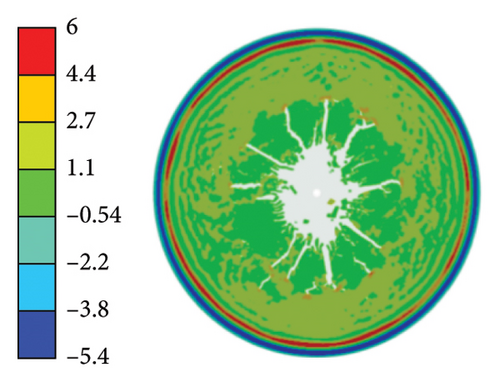

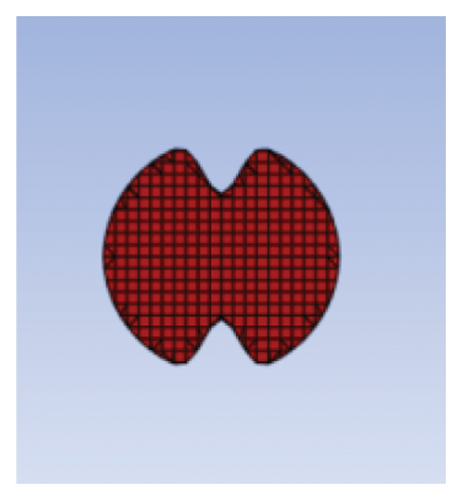
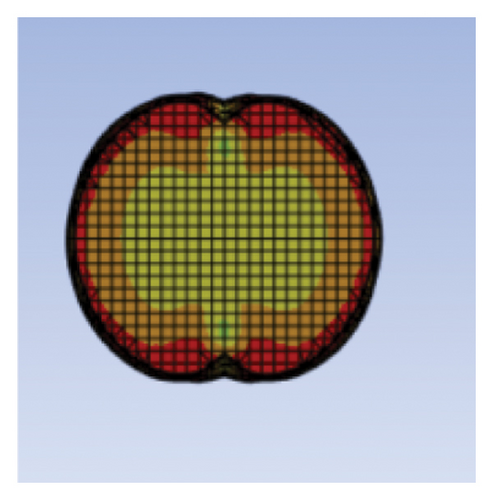
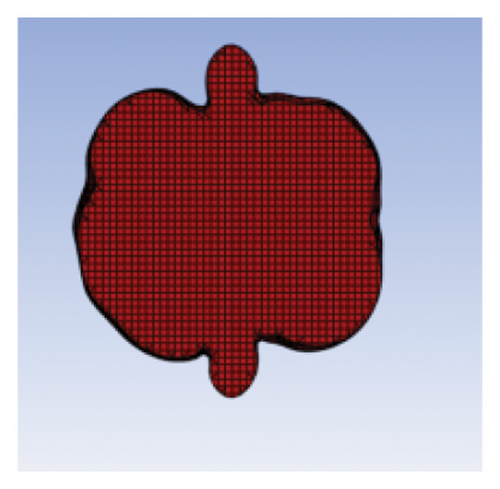

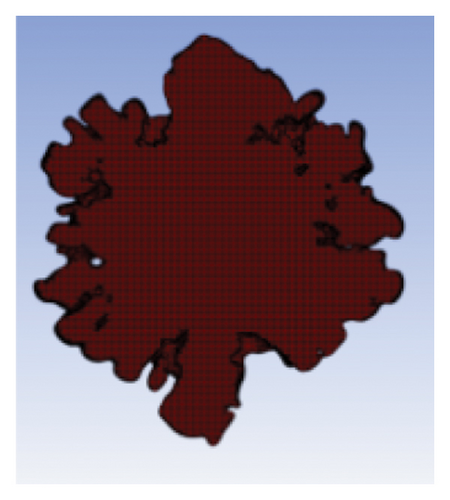
It is evident that the cracks from the two-way focused blasting tend to develop in the two focusing directions, with more pronounced strain observed in these areas, indicating that the focusing structure has indeed altered the distribution of the blast stress waves. The number, length, and depth of cracks produced by the two-way focused blasting are not smaller than those from conventional circular blasting, and the strain has not significantly decreased, meaning that the loosening effect of the blast has not been reduced.
The maximum principal stress within 1200 μs after the two-way focused blast was recorded at 10 μs intervals, and the detailed maximum principal stress values were obtained. The trend of stress variation is shown in Figure 17.
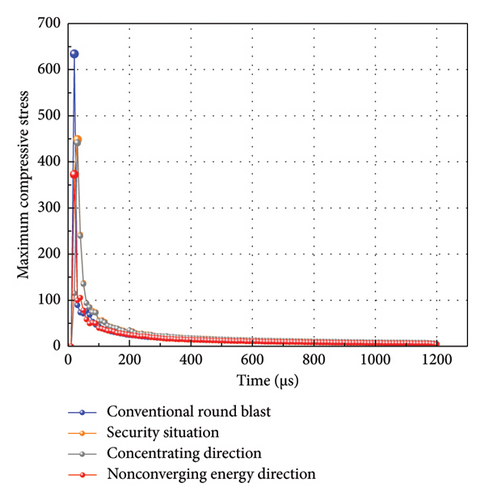

The trend of maximum compressive stress over time in two-way focused blasting is essentially the same as in the control blasting, and the maximum tensile stress is almost identical. The peak maximum compressive stress in the focusing direction occurs at 30 μs, with a peak stress of 411.270 MPa, while in the nonfocusing direction, the peak stress occurs at 20 μs, with a peak stress of 372.670 MPa. The average compressive stress after 100 μs was calculated for the overall maximum compressive stress, the focusing direction, and the nonfocusing direction, with average values of 15.778 MPa, 15.697 MPa, and 12.657 MPa, respectively.
3.2.1.3. Simulation of Four-Way Focused Blasting
The four-way focused blasting model is established as shown in Figure 18. The yellow represents the 6-m-diameter coal seam model, with a 150-mm-diameter borehole in the center. The red represents the four-way focused explosive model, with an explosive area of 9993.26 mm2, a 43% reduction in explosive charge compared to the circular charge model.
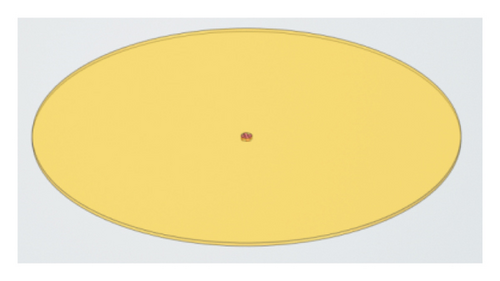
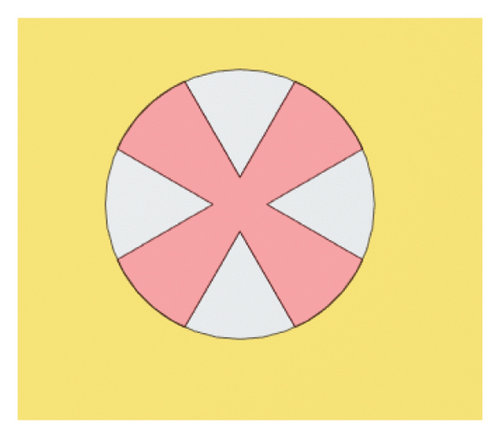
A numerical simulation was conducted for 1200 μs on the abovementioned blasting model, and the postblast coal damage pattern and the shape of the explosive gases are shown in Figures 19 and 20.
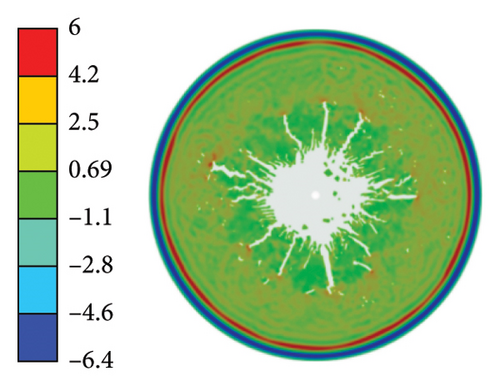
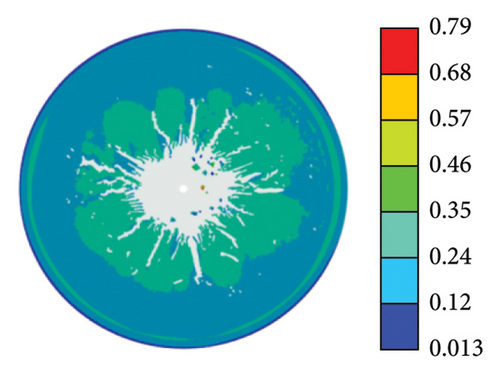
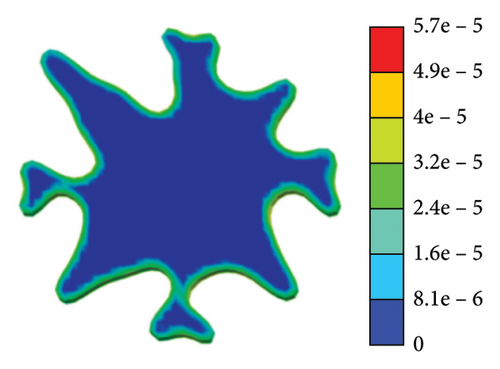
It is clearly visible that the cracks in the four-way focused blasting tend to develop in the four focusing directions, with strain distribution in the coal seam appearing more uniform. This indicates that the focused structure has indeed altered the distribution of the blast stress waves. The number, length, depth, and complexity of the cracks generated by the four-way focused blasting are significantly greater than those produced by conventional circular blasting, with a slight increase in the strain, thus clearly enhancing the loosening effect of the blast.
The maximum principal stress within 1200 μs after both blasts was recorded at 10 μs intervals, and the detailed maximum principal stress values were obtained. The trend of stress variation is shown in Figure 21.
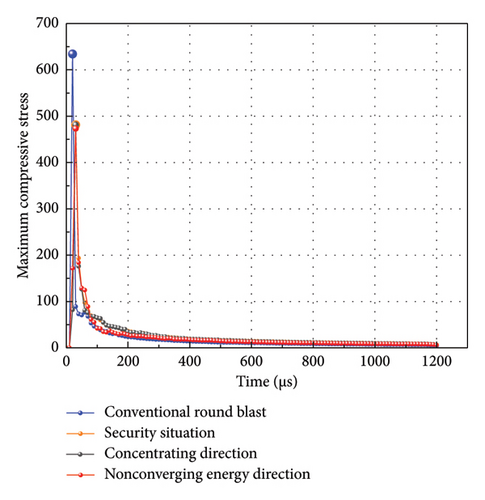
The trend of maximum compressive stress over time in four-way focused blasting is essentially the same as in the control blasting. The peak compressive stress in the focusing direction occurs at 30 μs, with a peak stress of 481.460 MPa, while the peak compressive stress in the nonfocusing direction also occurs at 30 μs, with a peak stress of 473.360 MPa. The average compressive stress after 100 μs was calculated for the overall maximum compressive stress, the focusing direction, and the nonfocusing direction, with values of 17.691, 17.629, and 14.974 MPa, respectively.
A comparison of the blasting stresses for the three focused structures and the conventional circular charge blasting shows the corresponding improvements or reductions. Detailed values are provided in Table 4.
Index | Two-way (%) | Four-way (%) |
---|---|---|
Explosive quantity | −22 | −43 |
Peak compressive stress | −35 | −24 |
Peak compressive stress in the nonconvergent direction | −41 | −25 |
Average maximum compressive stress | 23 | 38 |
Average maximum compressive stress in the direction of energy concentration | 22 | 37 |
Average maximum compressive stress in the nonpolygon direction | −2 | 17 |
Among the two focused explosive structures examined in terms of explosive charge and stress variations, the four-way focused blasting structure saved the most explosive material and experienced a smaller reduction in peak compressive stress but had a greater increase in subsequent compressive stress. The strain range also better meets the needs of open-pit mining blasting. Therefore, the four-way focused blasting structure is considered to provide the best blasting performance.
3.2.2. Optimal Focusing Structure for the Focused Groove
Using the same parameter settings as in the previous section, a numerical simulation of blasting was conducted for the abovementioned four focused groove structures and the circular charge structure with the same borehole diameter. The stress variation over time for each structure was obtained. The parameters for each structure are listed in Table 5, and the groove shapes are as shown in Figure 4 from Section 2.2.3.
Structural parameters | Structure 1 | Structure 2 | Structure 3 |
---|---|---|---|
Angle of convergence | 50° | 60° | 75° |
Concentrating depth | R | 4/5R | 3/5R |
Charge area | 8514.06 mm2 | 9993.26 mm2 | 11,842.27 mm2 |
3.2.2.1. Structure 1
A numerical simulation was conducted for 1200 μs on Structure One, and the postblast coal damage pattern and the shape of the explosive gases are shown in Figures 22 and 23.
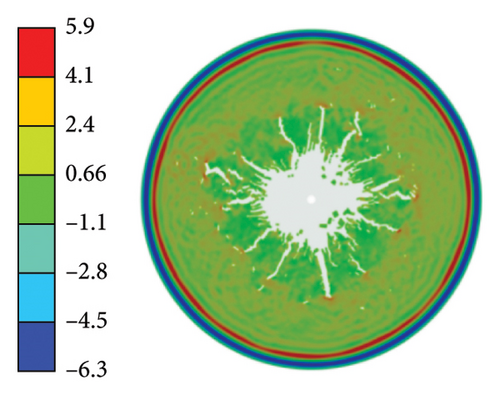
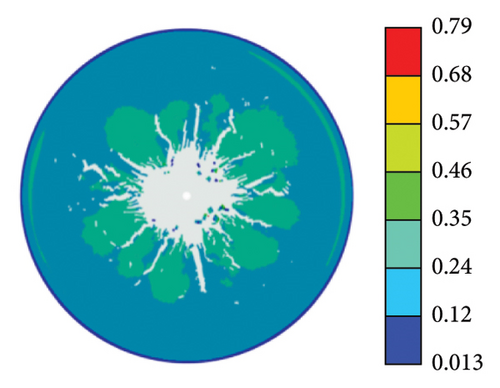

The maximum principal stress within 1200 μs after the blast for Structure One was recorded at 10 μs intervals, and the detailed maximum principal stress values were obtained. The trend of stress variation is shown in Figure 24.
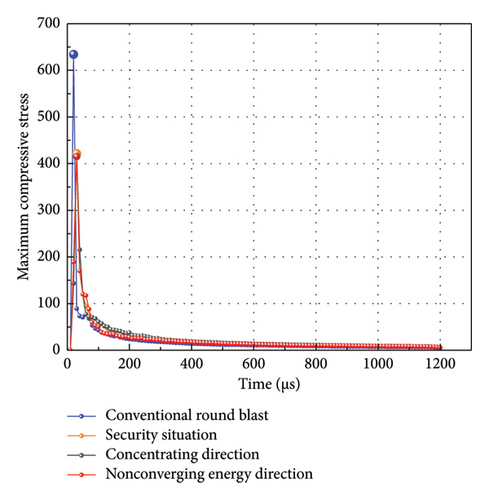
The peak compressive stress in the focusing direction for Structure One occurred at 30 μs, with a peak stress of 421.380 MPa, while the peak compressive stress in the nonfocusing direction also occurred at 30 μs, with a peak stress of 378.440 MPa. The average compressive stress after 100 μs was calculated for the overall maximum compressive stress, the focusing direction, and the nonfocusing direction, with values of 16.892, 16.807, and 13.641 MPa, respectively.
3.2.2.2. Structure 2
The four-way focused blasting structure from Section 3.2.1 is used as Structure Two. The blasting results for Structure Two are based on the simulation results of the four-way focused blasting in Section 3.2.1.
3.2.2.3. Structure 3
A numerical simulation was conducted for 1200 μs on Structure Three, and the postblast coal damage pattern and the shape of the explosive gases are shown in Figures 25 and 26.
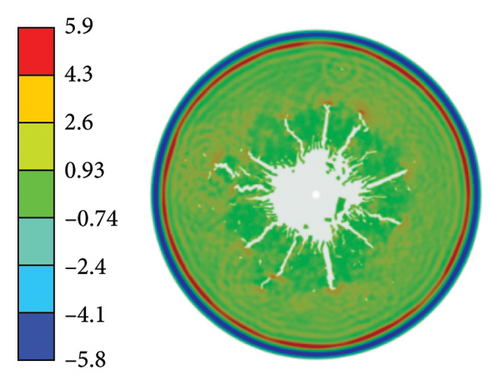
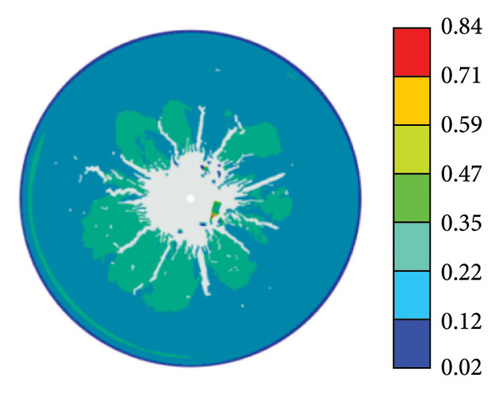
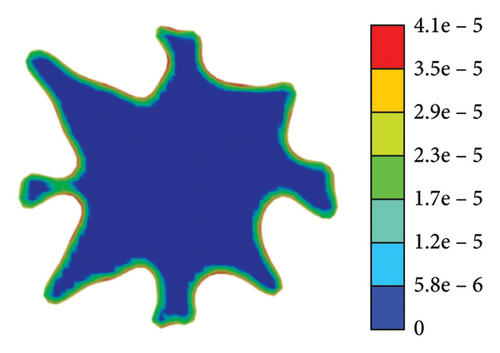
The maximum principal stress within 1200 μs after the blast for Structure Three was recorded at 10 μs intervals, and the detailed maximum principal stress values were obtained. The trend of stress variation is shown in Figure 27.
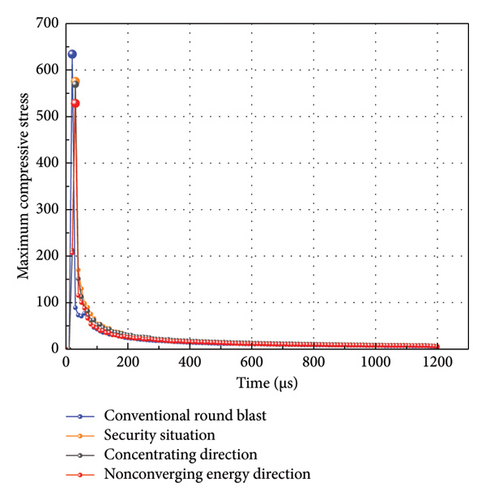
The peak compressive stress in the focusing direction for Structure Three occurred at 30 μs, with a peak stress of 569.430 MPa, while the peak compressive stress in the nonfocusing direction also occurred at 30 μs, with a peak stress of 441.980 MPa. The average compressive stress after 100 μs was calculated for the overall maximum compressive stress, the focusing direction, and the nonfocusing direction, with values of 15.381, 14.944, and 12.961 MPa, respectively.
The blasting stress of the three types of focused energy structures is compared with the blasting stress of conventional circular charge. The parameters compared include explosive quantity (EQ), peak compressive stress (PCS), PCS in the nonfocused direction (PCS-NFD), average maximum compressive stress (AMCS), AMCS in the focused direction (AMCS-FD), and AMCS in the nonfocused direction (AMCS-NFD). The corresponding increase or decrease in these parameters is detailed in Tables 6 and 7, Figure 28.
Index | Control subjects | Structure 1 | Structure 2 | Structure 3 |
---|---|---|---|---|
Charge cross-sectional area (mm2) | 17,671.46 | 8514.06 | 9993.26 | 11842.27 |
Peak compressive stress (MPa) | 634.31 | 421.38 | 481.46 | 569.43 |
Peak compressive stress in the nonconvergent direction (MPa) | 634.31 | 378.44 | 473.36 | 441.98 |
Average maximum compressive stress (MPa) | 12.85 | 16.892 | 17.691 | 15.381 |
Average maximum compressive stress in the direction of energy concentration (MPa) | 12.85 | 16.807 | 17.629 | 14.944 |
Average maximum compressive stress in the nonpolygon direction (MPa) | 12.85 | 13.641 | 14.974 | 12.961 |
Index | Structure 1 (%) | Structure 2 (%) | Structure 3 (%) |
---|---|---|---|
Explosive quantity | −52 | −43 | −33 |
Peak compressive stress | −34 | −24 | −10 |
Peak compressive stress in the nonconvergent direction | −40 | −25 | −30 |
Average maximum compressive stress | 31 | 38 | 20 |
Average maximum compressive stress in the direction of energy concentration | 31 | 37 | 16 |
Average maximum compressive stress in the nonpolygon direction | 6 | 17 | 1 |
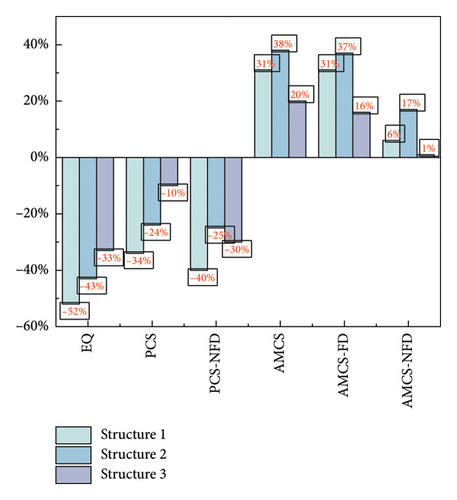
The amount of explosive used in focused groove Structures One through Three increases sequentially, and the peak stress also rises accordingly. However, the peak stress in the nonfocusing directions for all structures is lower than that of the circular control group. During the decay phase after the stress wave peak, the residual stress does not correlate linearly with the amount of explosive consumed. Instead, it first increases and then decreases as the explosive charge increases. Structure Two has the highest average maximum compressive stress after 100 μs among the three focused groove structures. This is because residual stress is influenced by two factors: the amount of explosive and the effectiveness of the focused groove structure. From Structure One to Structure Three, the increasing explosive charge raises the stress, while the widening focus groove angle reduces the focusing effect, causing stress to decrease. Due to the interplay of these factors, residual stress reaches its maximum in Structure Two. Taking into account both the reduction in peak stress and the increase in average stress and their influence on fine coal generation and overall coal seam loosening, focused Structure Two is deemed to produce relatively better blasting results.
4. Conclusion
- 1.
Based on the theory of coal seam blasting, focusing blasting, and hydraulic blasting, the role of focused hydraulic blasting in coal seam bench blasting was analyzed. Through numerical simulation, compared to conventional circular blasting, focused blasting shows significant differences in stress waves between the focusing and nonfocusing directions, with the maximum stress value typically occurring in the focusing direction of the coal seam. The peak compressive stress generated by focused blasting is much lower than that of conventional blasting, and the peak compressive stress in the nonfocusing direction is significantly smaller than that in the focusing direction. After the peak, the residual stress in focused blasting is higher than that in circular blasting. Therefore, it can be concluded that focused blasting reduces the compressive stress within the coal seam at the initial blast stage, and as the stress wave moves outward, its attenuation is slower, slightly increasing the pressure on the outer coal seam. The crack development pattern and stress changes in four-way focused blasting are most suitable for open-pit coal seam blasting. When paired with triangular borehole patterns, it can achieve maximum coal seam loosening.
- 2.
As the depth of the focusing groove decreases and the angle expands, the explosive consumption increases sequentially, and the peak stress also increases accordingly. However, in the decay phase after the peak stress wave, the residual stress does not correlate linearly with explosive consumption but instead follows a trend of first increasing and then decreasing with the increase in explosive charge. A focusing groove with a 60° focusing angle and a focusing depth of 4/5 of the borehole radius produces the best blasting effect. It reduces the peak compressive stress around the borehole by more than 20% and increases the average residual stress in the farther regions by approximately 20%, resulting in a smoother postblast stress curve and a more uniform coal particle size.
Conflicts of Interest
The authors declare no conflicts of interest.
Author Contributions
Conceptualization, Wang Guilin and Cai Qingxiang; methodology, Ding Xiaohua; validation, Liu Xiu; formal analysis, Liao Zhouquan; investigation, Liao Zhouquan; resources, Liu Xi; data curation, Liu Xi; writing – original draft preparation, Ding Xiaohua and Liao Zhouquan; writing – review and editing, Wang Guilin and Cai Qingxiang; and visualization, Liao Zhouquan. All authors have read and agreed to the published version of the manuscript.
Funding
This paper was supported by the National Natural Science Foundation of China (grant no. 52174131; 52374145; 52474153), the Nation Key R&D Program of China (2023YFC2907305; 2023YFF1306001), and the Fundamental Research Funds for the Central Universities (2021ZDPY0227).
Open Research
Data Availability Statement
The data presented in this study are available on request from the corresponding author due to the confidentiality of production data related to the test site, the Haerwusu open-pit coal mine.