An Efficient PINN–Based Calibration Method for Mesoscale Peridynamic Concrete Models
Abstract
Mesoscale models are crucial for the refined analysis of material damage behaviors. However, it remains a challenging task to calibrate a mesoscale model so as to accurately simulate the mechanical behaviors (MBs) of macroscale structural components. The models may be nonlinear, involve numerous material parameters (MPs), and be large-scale. In addition, solutions to inverse problems may lack accuracy or be nonunique. A recent emerging method, physics-informed neural network (PINN), combines deep learning with physical laws to solve complex problems and significantly reduce computational costs. This paper presents an effective PINN approach for mesoscale model calibration. The approach establishes a relationship between the MPs of a mesoscale model and the MBs of structural components using PINN, with constraints based on known physical relationships. Both forward PINN (MPs as inputs and MBs as outputs) and reverse PINN (swapping inputs and outputs) models are used. Calibration is achieved efficiently by combining the forward PINN model with an optimization algorithm or directly using the reverse PINN model. Validation is performed using a mesoscale concrete model in peridynamics (PDs). The relationship between the elastic modulus of bonds in PD and MBs of components is constrained by physical laws. The datasets are generated through OpenSees analysis. The PINN method demonstrates its effectiveness, particularly with the reverse model, which is both efficient and accurate.
1. Introduction
Mesoscale models are designed to accurately capture the microscopic damage mechanisms within materials. However, when employing mesoscale models to simulate structural components, calibration of the material parameters (MPs) is required. This process is often elaborate and time-consuming, primarily due to the typically extensive computational scale, encompassing nonlinearities and numerous parameters for adjustment. In recent years, the rapid advancement of computer technology has propelled the progress of machine learning (ML). In this evolving technological landscape, ML has emerged as a powerful tool for modeling and solving complex engineering problems [1]. MLs have demonstrated remarkable success in fitting structural responses with high precision and efficiency [2–5]. By leveraging well-constructed neural network models, the process of fitting structural responses becomes not only rapid but also remarkably accurate, leading to a substantial reduction in the computational time traditionally required for such tasks. Many scholars have applied ML to capture the complex nonlinear plastic behavior of materials or structures. For example, Siow et al. employed ML to extract the main structural damage-sensitive feature while maintaining dynamic characteristics [6]. Fu and Wei proposed a two-stage ML–based method to model the elastic modulus of concrete [7]. Teng et al. employed a convolutional neural network (CNN) to extract damage features of the bridge population [8]. Although ML has made significant advancements, the calibration process for mesoscale model parameters is notably complex. Traditional ML methods may struggle to meet some physical requirements. Recently, a kind of ML method called physics-informed neural network (PINN) has been proposed, which integrates physical laws into the architecture of neural networks, offering a unique blend of traditional numeric simulation and ML [9]. This integration enables PINN not only to learn from data but also to respect the governing physical principles, ensuring more reliable predictions. Currently, numerous scholars have also employed PINN to study the nonlinear behavior in civil structures. Jeong et al. proposed a PINN–based topology optimization, which opened up a new avenue for structural design [10]. Pu et al. proposed a PINN model to enhance the fitting of nonlinear data with prior knowledge, providing greater stability and accuracy than traditional DNNs, especially in noisy conditions and with inadequate samples [11]. Yamaguchi and Mizutani proposed a PINN–based damage identification algorithm to assess earthquake-induced damages in reinforced concrete bridge piers, achieving precise parameter estimations [12].
The advent of PINN represents a significant advancement in the ability to integrate data-driven insights with physical laws. This integration can be crucial in the field of fracture and damage simulation. Within this domain, various models have been developed, including the discrete cohesive crack model, phase field model, nonlocal damage model, and peridynamics (PDs). The discrete cohesive crack model offers precise control over crack initiation and propagation but requires preinserted cohesive elements and crack-tracking strategies, limiting its wider applicability [13]. The phase field model effectively handles complex crack patterns with simple implementation but incurs high computational costs due to its implicit numerical methods [14]. The nonlocal damage model provides mesh-independent solutions, yet it may suffer from spurious damage growth across overly extensive areas due to constant interaction domains [15]. In contrast, PD is a nonlocal continuum theory developed by Silling and Lehoucq [16, 17]. Due to the absence of spatial derivatives in its governing equations, PD excels in addressing discontinuous field problems, such as cracking and fracture [18–22]. PD theory can be categorized into bond-based PD (BPD) and state-based PD (SPD). In BPD, it is assumed that points within the horizon are interconnected by fictitious bonds. The force exerted by each bond is assumed to be along with the bond itself, and the magnitude can be determined based on the bond’s elongation and a suitable uniaxial material’s constitutive model. Due to its simplicity and practicality, BPD has been extensively applied to the refined simulation of various damage and fracture problems. For example, Huang, Zhang, and Qiao proposed a refined BPD to simulate damage and progressive failure of concrete materials and structures under various loading [23]. Li and Guo proposed a mesoscopic BPD model for mesofracture simulation of the cracking process in concrete, i.e., truss elements with appropriate stiffness properties are used to represent the PD bonds [24]. Zhang et al. proposed a novel coupled axial–shear interaction bond-slip BPD model to simulate the relative slip and interface damages between the concrete and steel [25]. Despite the widespread application of BPD to numerous engineering problems, the practical implementation often requires elaborate calibration, particularly for nonlinear materials. In addition, the MPs will vary with changes in the PD model’s grid spacing dx. This inefficiency in calibration complicates the use of PD and restricts its practical application in engineering to some extent.
This paper utilizes PD as a case study to demonstrate how the PINN model can delineate the relationship between MPs and mechanical behaviors (MBs). In this context, “mesoscale” specifically refers to a refined PD model designed to target damage processes at the millimeter scale or smaller. This definition contrasts with the conventional interpretation of mesoscale, which typically pertains to phases such as aggregates and mortar [15]. Specifically, the paper develops the PINN by incorporating the mesoscale elastic modulus formula from PD theory into the loss function of a CNN model. Initially, a forward PINN model is developed where MPs serve as inputs (“causes”) and MBs as outputs (“effects”). Then, an optimization process is used to align the predicted MBs with the targeted values by iteratively adjusting the MPs. Lastly, a “reverse” PINN model is designed, where MBs are the inputs and MPs are the outputs, effectively flipping the relationship from outcomes back to causes. This approach streamlines the calibration process, eliminating the need for mathematically solving the inverse problem and demonstrating the capability to rapidly and accurately complete the calibration of parameters. The approach proposed in this paper offers the following advantages: (1) An efficient PINN model is developed to calibrate mesoscale models using ML with integrated physical constraints. (2) Both forward and reverse PINN models are comparatively explored for calibrations, with forward models combined with optimization techniques. (3) Relationships are established between the MBs of macroscale concrete structural components and the MPs of mesoscale PD bond models. (4) The training datasets are analyzed using the nonlinear finite element software, OpenSees, which utilizes its comprehensive material libraries, nonlinear algorithms, and parallel computing capabilities.
2. The PINN Model
The proposed PINN model is constructed by the input layer, convolution layer, fully connected (FC) layer, and output layer. Taking the forward PINN model as an example, Figure 1 illustrates the workflow of the entire PINN, detailing the process when the inputs are MPs with dx and the outputs are MBs. Further details about MPs and MBs will be introduced in the next section. In Figure 1, pi denotes the output size of the ith layer, θ represents the model parameters, kn represents the kernel size of the convolution layer, and MSE represents the mean square error function.

2.1. Convolution Layer, Pooling Layer, and FC Layer
In the CNN model, pooling layers are typically employed to reduce the spatial size of feature maps while dealing with large input data. Generally, pooling methods include max pooling and average pooling, which extract the maximum or average values from the pooling window, respectively. However, pooling layers compress feature maps, which can lead to loss of critical information, reduced precision in tasks needing high accuracy, and obscured fine details [27]. In the proposed PINN model, the use of pooling layers would result in shorter output lengths, which is undesirable for the regression problems between MBs and MPs. Therefore, the application of pooling layers is restricted in the proposed PINN architecture.
FC layers are typically employed in the latter stages of CNNs to facilitate the transition from feature extraction to output generation. Each neuron in a FC layer is interconnected with all activations from the previous layer, effectively integrating learned features by computing a weighted sum over them, followed by adding a bias term (as shown in Figure 2).

2.2. Loss Function and Solution
3. Mesoscale Simulation of Concrete Using a Fine BPD Model
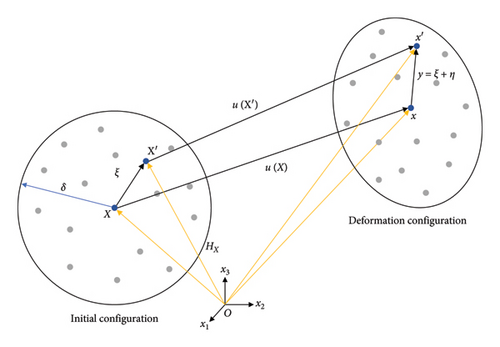
Therefore, in the elastic state, the microelastic modulus in BPD can be determined through analytical derivation. However, when the material exhibits nonlinear behavior, which is particularly evident in simulations of reinforced concrete components characterized by strong nonlinearity, the microelastic modulus may no longer fully comply with equation (15), and other nonlinear MPs become difficult to estimate. These parameters can only be inferred through postcalculation analysis, leading to a significant expenditure of time in the iterative calibration of these parameters when simulating reinforced concrete components with BPD. This scenario highlights the intricacies involved in modeling such materials and the challenges associated with accurately predicting the response. The following will introduce the parameters that need to be calibrated when simulating concrete materials using the fine BPD model.
3.1. The MPs of the BPD Concrete Model
In simulations utilizing BPD, the linear tension softening model in OpenSees (i.e., Concrete02 Material [29]) is chosen for the concrete bond model. As shown in Figure 4, this model can adeptly simulate the complex strong nonlinear behavior of concrete under compression or tension with a limited set of parameters, where epsc and fpc represent the yield compressive stain and stress of concrete, respectively. epsu and fpcu denote the ultimate compressive strain and stress. λ is the ratio between the unloading slope (at ultimate strain) and the initial slope. ft is the yield tensile stress, Ets is tension softening stiffness, and E0 is initial stiffness which can be calculated as E0 = 2fpc/epsc.
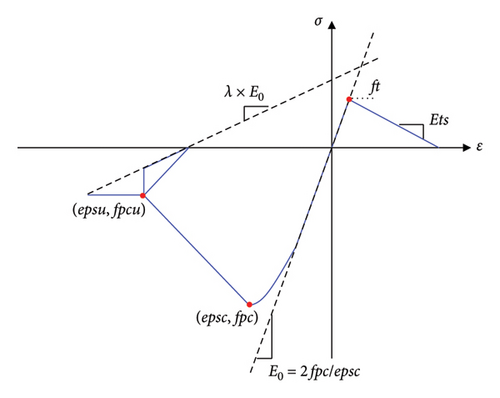
Therefore, in the practical application of this material model for simulating concrete, a total of seven parameters require calibration. This paper primarily focuses on the stress–strain curve of concrete specimens under compression or tension. Considering that parameter λ mentioned previously manifests during the unloading phase, it does not need to be calibrated in this context. Consequently, within the scope of this study, there are six parameters that require calibration in the employed linear tension softening model (refer to Table 1).
Parameter | Symbol |
---|---|
Yield compressive strain | epsc |
Yield compressive stress | fpc |
Ultimate compressive strain | epsu |
Ultimate compressive stress | fpcu |
Yield tensile stress | ft |
Tension softening stiffness | Ets |
To obtain appropriate BPD model parameters, calibration is typically based on the mechanical properties of standard specimens, with the most commonly used being the tensile and compressive stress–strain curves. This will be detailed in Section 3.2.
3.2. MB of the Concrete Specimen
Figure 5 displays the stress–strain curve obtained from the uniaxial tension and compression numerical simulation of standard concrete specimens using the Concrete02 Material in BPD. Through the comprehensive analysis and synthesis of a vast amount of data, this paper identifies eight key data points within the curve to depict the stress–strain behavior of the components as accurately as possible. These key data points include peak points, significant turning points, and the slopes of the descending segments of the curve, which are crucial for defining the mechanical response accurately. It is also noteworthy that the yellow points D and E shown in the Figure 5 are not directly extracted from the curve but are interpolated auxiliary inflection points derived from point B. The specific method used is xD = (1/2)xB, yD = (3/4)yB, xE = (1/2)xB + (1/2)xD, and yE = (3/4)yB + (1/4)yD. After determining these key points, they are connected with multisegment lines to fit the entire stress–strain curve, as illustrated in Figure 5, where the solid black line represents the stress–strain curve obtained from numerical simulation, and the red dotted line is the fitted curve based on key points. The authors, after validating across all datasets, have found that the selection of these key points can adequately simulate the complete uniaxial tension-compression curve. In the practical application of BPD simulation for concrete, it is common to compare this curve to further simulate the overall hysteretic behavior. Among these eight key points, three are related to tensile behavior: the yield tensile strain εty, yield tensile stress σty, and the slope of the tensile softening segment kt. The remaining five are related to compressive behavior, including yield compressive strain εcy, yield compressive stress σcy, strain εc0, and stress σc0 at the inflection point of the softening segment, and the slope of the compressive softening segment kc. With these eight data points (see Table 2), it is possible to accurately reconstruct the overall curve.
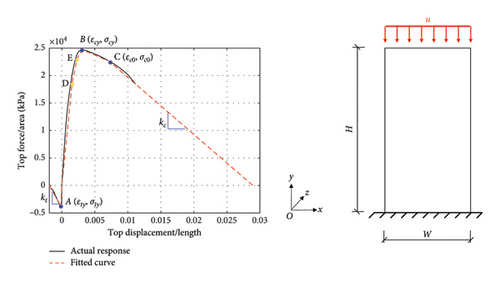
Parameter | Symbol |
---|---|
Yield tensile strain | εty |
Yield tensile stress | σty |
The slope of the tensile softening segment | kt |
Yield compressive strain | εcy |
Yield compressive stress | σcy |
Strain at the inflection point | εc0 |
Stress at the inflection point | σc0 |
The slope of the compressive softening segment | kc |
4. Calibration Based on Forward and Reverse PINN Models
This paper utilizes forward and reverse PINN models to predict the relationship between MPs of BPD and MBs of components. For both the two PINN models, a total of 1044 simulation cases were conducted, with 730 cases (70%) used to train the neural network model, 157 cases (15%) used to validate, and the remaining 157 cases (15%) employed to test the accuracy and reliability of the trained model. It is noteworthy that the grid spacing dx needs to be set within BPD simulations. Due to the boundary effects inherent in BPD, if dx is too large, it leads to a reduced number of PD points, thereby accentuating noticeable boundary effects and causing inaccuracies in the simulation. Conversely, if dx is too small, it results in an excessive number of PD points, which does not significantly enhance computational precision but drastically increases computation time. For standard specimens (150mm × 150mm × 300mm), this paper sets dx within the range of 8–20 mm and includes it as one of the input variables for training. Figure 6 illustrates the dimensions and boundary conditions of the PD model of the component, where the model’s width and height are 150 mm and 300 mm, respectively, with a thickness of 150 mm. The PD points at the base of the model are fixed in all three directions, while a uniform displacement is applied to the top in the y-direction to simulate both tensile and compressive conditions.
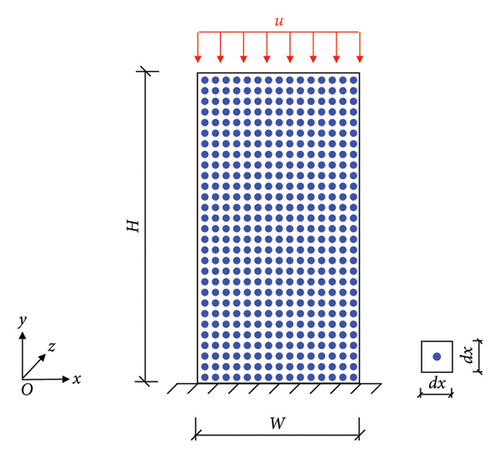
Hence, the forward PINN model predicts MBs based on MPs, and there are seven input variables (six MPs and dx), resulting in eight output variables (eight key data points). Conversely, the reverse PINN model predicts the required MPs based on MBs, and nine input variables are needed (eight key data points and dx), which lead to the output of six MPs.
4.1. Forward PINN Model
Figure 7 compared the convergence histories of CNN and FC network (FCNN). It is important to note that these two models used in our comparisons are designed with a comparable number of trainable parameters, ensuring a fair comparison in terms of model capacity. Based on this, it can be observed that CNN demonstrates superior efficiency and effectiveness. The CNN model not only converges faster but also achieves lower loss and L2 norm error across epochs. By the 50th epoch, the loss stabilized at 0.035 and the L2 norm error at 0.073 in the CNN model.

The sample correlation coefficient R is often used to measure the degree of linear correlation between two sets of data. The range of R is from 0 to 1, and a value of 1 shows that the predictions are correct. As depicted in Figure 8, the R values for the training, validation, and test sets were 0.95966, 0.95410, and 0.94954, respectively, all of which are close to 1. This indicates the high accuracy of the trained PINN.
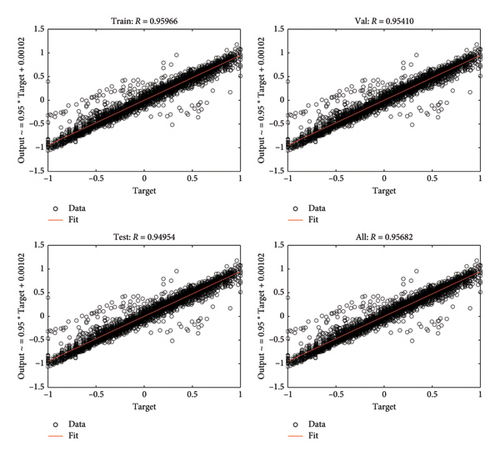
A set of 157 test cases was employed to conduct a more detailed examination of the discrepancies between the predicted values and actual values for each MB. As depicted in Figures 9 and 10, the predicted values of 8 MBs agree well with the expected values. The mean relative error (MRE) calculates the average of absolute errors as a percentage of the real values and is defined as , where and are the real and predicted values, respectively. From the detailed analysis presented in Table 3, it is evident that the proposed forward PINN model can precisely predict three key points of stress and strain in the MBs based on the MPs, with the maximum MRE reaching only 1.70%. While the relative errors for the slopes in the tensile and compressive segments (kc and kt) are slightly higher, they remain within acceptable limits at 6.79% and 4.79%, respectively. Notably, the maximum REs across all data points hover around 10%, and the minimum REs are exceptionally low, typically less than 0.01%. These findings robustly confirm the reliability and effectiveness of the trained forward PINN model in capturing the complex dynamics of the simulated materials and behaviors.

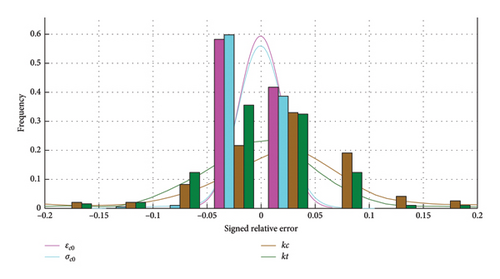
Parameter | MRE (%) | Maximum RE (%) | Minimum RE (%) |
---|---|---|---|
εty | 1.70 | 10.84 | 0.01 |
σty | 0.87 | 10.73 | 0.005 |
εcy | 0.93 | 2.86 | 0.004 |
σcy | 0.95 | 10.09 | 0.006 |
εc0 | 0.20 | 1.09 | 0.002 |
σc0 | 0.60 | 10.13 | 0.001 |
kc | 6.79 | 13.39 | 0.005 |
kt | 4.79 | 13.77 | 0.007 |
The accuracy of the optimization algorithm is corroborated by the previous 157 sets of cases. Figures 11 and 12 illustrate that, given specific MBs, the fully trained model successfully determines an appropriate set of MPs through the optimization process. Although a small number of datasets have a maximum RE of about 20%, for the majority of datasets, the error can be controlled within 10%. The outputs generated from these optimization-derived MPs align closely with the initially provided MBs, showing a good level of agreement. The REs for eight parameters are detailed in Table 4. Furthermore, the inputs predicted by the optimization algorithm are compared with the actual MPs, yielding a MRE of 7.47% across six MPs. This indicates the effectiveness of the proposed method in substituting the conventional calibration process, facilitating the swift and precise identification of optimal BPD MPs from essential points on the stress–strain curve.
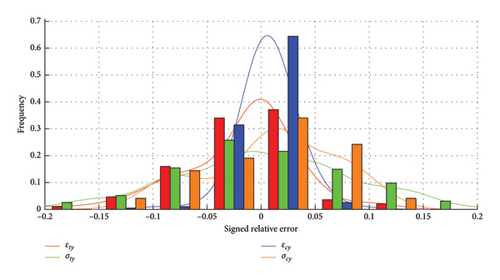
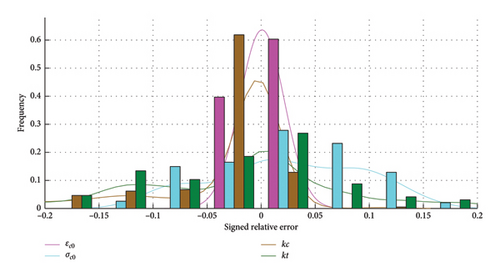
Parameter | MRE (%) | Maximum RE (%) | Minimum RE (%) |
---|---|---|---|
εty | 3.95 | 24.39 | 0.001 |
σty | 6.62 | 26.07 | 0.060 |
εcy | 1.57 | 10.05 | 0.001 |
σcy | 4.94 | 13.03 | 0.006 |
εc0 | 0.39 | 3.06 | 0.003 |
σc0 | 6.05 | 16.29 | 0.012 |
kc | 4.42 | 24.94 | 0.001 |
kt | 8.69 | 25.54 | 0.001 |
4.2. Reverse PINN Model
In the reverse PINN model, the layers of the network, division of the datasets, and control parameters remain identical to those of the forward PINN model, with the exception that the input layer size has been adjusted to 8. The distinction lies in the input and output variables: for the reverse PINN model, the input variables are the key data points from the macroscopic stress–strain curve of components (MBs) and the grid spacing dx, while the output variables are the MPs required for use in BPD.
In the reverse PINN model, the R values for the training, validation, and test sets were 0.92606, 0.92792, and 0.92117, respectively (shown in Figure 13). It can be observed that all R values are close to 1, proving the accuracy of the model.
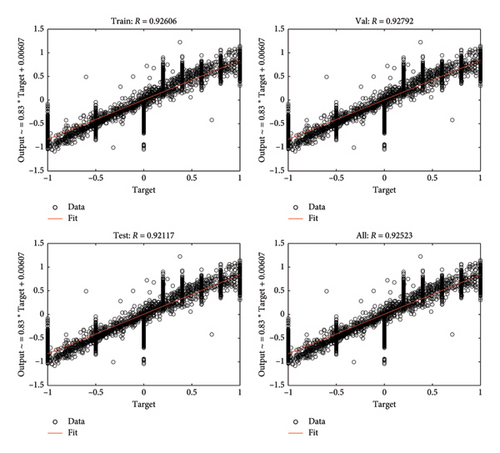
Similar to the forward PINN model, 157 additional test cases are employed to validate the accuracy of the predicted values. Figures 14 and 15 clearly show a good agreement among the six output values. The MRE for the six data points has been listed in Table 5, with the highest relative error being only 3.02%. These results indicate that this methodological approach enables the inverse prediction of essential MPs, facilitating the calibration of fine BPD models for accurate simulation of MBs. This reverse-engineering capability significantly enhances the practical utility of BPD in complex material modeling and structural analysis, demonstrating the versatility and efficacy of integrating ML techniques with traditional computational mechanics methodologies. Table 6 shows that, the forward PINN model combined with an optimization function, required 47.46 s to predict 157 sets of appropriate inputs. In contrast, using the reverse PINN model to predict inputs for the same number of datasets took only 0.68 s. The training times of the forward and reverse models are 43.30 s and 75.10 s, respectively. In contrast, simulating the tension and compression process of the component in OpenSees takes about 2 h. It is obvious that the two proposed PINN models significantly enhance calibration efficiency.
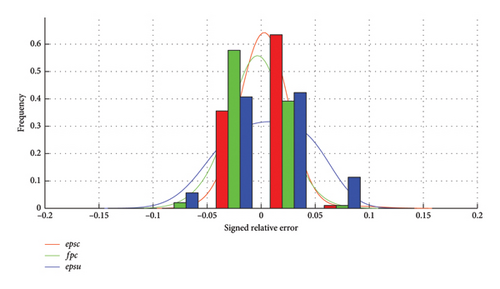
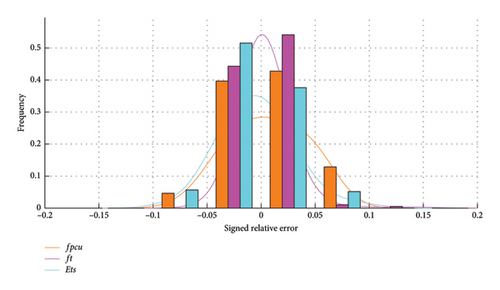
Parameter | MRE (%) | Maximum RE (%) | Minimum RE (%) |
---|---|---|---|
epsc | 0.98 | 9.81 | 0.02 |
fpc | 1.44 | 6.32 | 0.01 |
epsu | 3.02 | 8.49 | 0.07 |
fpcu | 2.92 | 7.55 | 0.01 |
ft | 1.01 | 14.0 | 0.0001 |
Ets | 2.51 | 9.80 | 0.01 |
Training | Prediction (157 sets) | OpenSees (1 set) (h) | |||
---|---|---|---|---|---|
Forward (s) | Reverse (s) | Forward (s) | Reverse (s) | ||
Time | 43.30 | 75.10 | 47.46 | 0.68 | 2 |
It is also worth noting that while the method is efficient and accurate, it has limitations. Specifically, the calibration results are model-dependent, i.e., they may vary and cannot be directly applied across different concrete bond models, which complicates their use in direct engineering applications. Future efforts will focus on expanding mesoscale models, incorporating additional physical constraints and examining complex components such as reinforced concrete to develop practical tools for engineering analyses.
5. Conclusions
This paper presents a PINN approach for effectively calibrating mesoscale models, integrating known physical relationships between MPs and MBs. We established both a forward PINN model, where MPs serve as inputs and MBs as outputs using an optimization algorithm for calibration, and a reverse PINN model, which switches the input and output roles and eliminates the need for optimization. The methods are validated through a mesoscale concrete model using PD, trained and tested on 1044 sets of cases from OpenSees, which offers a well-established framework for structural analysis. The forward PINN model demonstrated high accuracy with a maximum MRE of 6.79% in MBs, while the reverse model further improved efficiency with a maximum relative error of 3.02% in predicting MPs. This study underscores the potential of PINN to streamline and enhance the calibration of mesoscale models, combining accuracy and efficiency, especially notable in the reverse PINN approach. The limit of the method is that calibration results may vary when using different concrete bond models, which can complicate direct engineering applications. Future work will expand on mesoscale models, incorporate more physical constraints, and explore complex components such as reinforced concrete to provide practical tools for engineering analyses.
Conflicts of Interest
The authors declare no conflicts of interest.
Funding
The authors acknowledge the financial support received from the National Natural Science Foundation of China (Grant nos. 52378539 and 51978591).
Acknowledgments
The authors acknowledge the financial support received from the National Natural Science Foundation of China (Grant nos. 52378539 and 51978591).
Open Research
Data Availability Statement
The data that support the findings of this study are available from the corresponding author upon reasonable request.