Comparative Analysis of the Effect of Needle-Based Spinneret/Collector Combinations on Morphological Properties of PVA Electrospun Mats
Abstract
Electrospinning is a promising technique for enabling the manipulation of the structural properties of nano- or microfibrous mats by altering electrospinning parameters. In this paper, it is aimed to examine the morphological variations of electrospun mats fabricated by combinations of different collector types and feeding units. In horizontal electrospinning setup, PVA polymer solutions are transformed to polymer jets by the help of needle-based feedings with single- and multinozzles. Electrospun fibers are deposited on four different collector types with identical collector-nozzle distance, feeding rate, applied voltage, and environmental conditions. It is concluded that the coarsest nanofibers are fabricated by multineedle/disc collector combination and the disc collector causes flat nanofiber handling with multineedle feeding but not with single needle feeding. On plate collector, thicker electrospun mats are obtained whichever feeding type is used. Average pore sizes on mats are found higher in multineedle feeding, especially with deposition between rods of birdcage collector. Changing the feeding type from multineedle to single needle causes to manufacture of electrospun mats with a narrower surface area and an increase is observed in packing density, basis weight and % porosity but a decrease in pore size and mat thickness with this manipulation. Nanosized but flattened electrospun fibers are handled by multineedle/disc collector and two distinct compositions are incorporated by deposition of nanofibers on birdcage collector.
1. Introduction
Electrospinning is a simple technique used for fibrous mat fabrication with a few apparatus which are a feeding unit for continuous flow of polymer solution as input material, a collector for fiber deposition as output material and a high voltage source for supplying an adequate electrostatic field [1, 2]. This technique is based on multidiscipliner studies, and fluid dynamic is the key point discipline due to the use of polymer solution. The behavior of polymer solution against disturbant forces has been examined by many researchers [3, 4]. In the electrospinning process, two different instabilities are theoretically observed and those are related with surface tension, viscosity, applied force, and conductivity. The first one is Rayleigh-Plateau instability, which turns a liquid into a series of droplets and herein the viscosity of liquid acts as a stabilizing mechanism because it only moderates the rate of disturbances such as gravity and applied voltage but does not change conditions for instability [5]. The second is well-known bending instability that refers to a spiral path in three dimensions, which is basically the resultant of electrostatic repulsion force [6]. Polymer jet becomes thinner as larger bending instability circles are observed due to thinner polymer jet diameter and an increase in centrifugal moment [7]. With the help of both continuous polymer solution feeding and then stretching of polymer solution via electrical flow, polymer jet is guided to the negatively charged collector. During this guidance, uniform electrospun nanofibers are fabricated if bending instability is bigger than Rayleigh instability or beading formation occurs if Rayleigh instability is dominant [8]. It is well known that process, solution, and environmental parameters are crucial variables during the electrospinning process [9] and even little changes in these variables, which are considered even unremarkable effects, influence the morphological characteristics of electrospun fibers significantly as proven in other studies [10, 11]. From the point of collector type, many researchers have made some attempts on electrospinning of different polymer solutions on different types of collectors with unique feeding type [12–14].
PVA is a biocompatible, odorless, water-soluble, and nontoxic polymer having excellent dyeing and oxygen barrier properties [15–17]. It is a semicrystalline polymer with many hydroxyl groups, thus PVA polymer dissolved in water shows good adhesive properties and high elongation at breaking forces. Solubility of PVA polymer depends on degree of polymerization, hydrolysis degree, solvent choice, polymer concentration, and temperature [18, 19]. In case of addition of PVA polymer solution into another polymer solution with appropriate concentration and solvent choice, PVA acts as a carrier polymer for blending natural polymers and increases the electrospinnability of biopolymer solutions in which it is incorporated [20]. Abbas et al. fabricated a three-layered mask by electrospinning of PVA polymer with chitosan, silk, and Ti2O3 on plane collector and reported that this multifunctional filtering mask acts as a barrier for personal protection. The porous structure of electrospun mats facilitated the filtration effectiveness [21]. Saar and Tuğcu Demiröz studied the manufacturing of a drug delivery system from PVA/DMF/water solution via horizontal electrospinning with a rotary collector. They fabricated electrospun mats from PVA polymers with various molecular weights by changing the electrospinning system parameters. They concluded that nanofibers electrospun from 7.5% PVA 13/140 polymer solutions were usable as a vaginal drug delivery system due to their continuous nanofiber formation, subsequent contact angle and mucoadhesive properties [22]. Renkler et al. improved a multifunctional scaffold from electrospun multicomponent PVA-based fibers via horizontal electrospinning with a plane collector. They pointed out that PVA is an easily processable polymer with different polymers in order to produce fibrous electroactive membranes. The fiber entanglement obtained by the electrospinning technique improved the cell adhesion [23]. Golchin et al. introduced an electrospun curcumin-incorporated chitosan/polyvinyl alcohol/carbopol/polycaprolactone nanofibrous composite, and they expressed that nanofibrous composite mats showed wound-repairing efficiency and could be used as potential wound dressings. Cell seeding and proliferation were developed by utilizing the high specific surface area [24].
From the literature survey, it is seen that there is a gap on which feeding type/collector combination should be used for versatile electrospinning of PVA polymer because plane collector/single needle combination has been generally used in the majority of these studies. Considering that the feeding unit is the apparatus on which a syringe with a needle is attached and Taylor–Rayleigh instability begins and also the collector is the place where electrospun fibers are deposited and bending instability is finished, the morphological variability on PVA mats should be clarified by means of feeding type/collector combination and how bending stability is finished as depositing the electrospun fibers on which geometric shape. This study is based on the construction of different setups with needle-based feedings and different collector types. It is aimed to identify which setup is the most versatile combination according to target usage area and how morphological properties of electrospun mats are affected by changing setup combination. This study will be a notable aspect for potential researchers studying on PVA-based filtration, biosensors, tissue engineering, wound dressing, and drug delivery systems.
2. Materials and Methods
2.1. Materials
PVA polymer (Mw: 61,600 gmol−1, DP: 1400, DH: 88%) was supplied from ACN Chemicals, Adana, Turkey. Distilled water was used for dissolving PVA polymer. The materials were used without further application.
2.2. Methods
A total of 3.6 g of PVA polymer was dissolved in distilled water for 3 h at a temperature of 90°C. Each resulting 12 wt% solution was cooled down to room temperature and 10 g was transferred into a 10 mL syringe. Polymer solution was conducted to electrospinning field with the help of two different spinneret types such as single needle and multineedle. Multineedle-feeding apparatus was constructed from five nozzles, which were placed 10 mm apart from each other. The 21 G needles were used in both single needle and multineedle electrospinning. Collectors were made from stainless steel with the dimensions of 80 mm in diameter for disc collector, 80 mm in diameter and 180 mm in length for drum collector, 80 mm in diameter with 8 rods (2 mm) and 180 mm in length for birdcage collector and 200 mm × 200 mm for plate collector. Process parameters were kept constant and electrospinning was performed at 15 kV applied voltage (Hena high voltage DC power supply), 0.5 mL/h feeding rate ((New Era Ne-300 syringe pump), 10 cm collector distance, and 60 min spinning duration in the horizontal axis. The rotation speed of rotary collectors was 400 rpm. Environmental temperature and relative humidity were recorded as 23°C ± 2°C and 45%, respectively. Setup combinations and electrospinning process are shown in Figures 1 and 2.
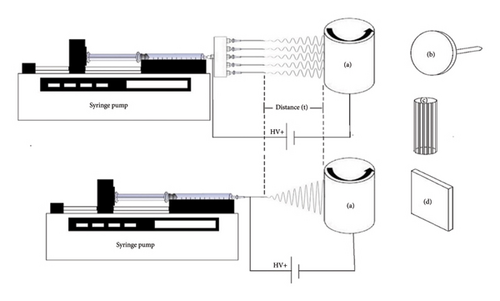
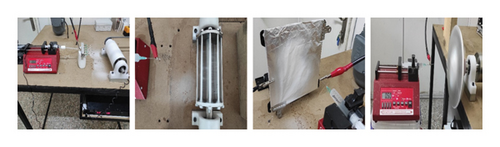
2.3. Characterization
Electrical conductivity and viscosity of polymer solution were measured at 25°C using Hanna HI 255 with HI 76310 probe and capillary viscometer, respectively. Electrospun mats were morphologically characterized by fiber morphology by field emission scanning microscopy (FESEM) (Zeiss GeminiSEM 300) analysis after samples were coated with 20/80 Au/Pd amalgam. Average fiber diameters were obtained after 50 measurements for each sample. The thickness of mats was measured using a micrometer (Digital Thickness Gauge, Mitutoyo, Japan) with a high sensitivity of 0.001 mm, and the average thickness was calculated after the measurement of five different points on each sample. Average mat weights were obtained after 5 weighting (a high precision balance with a sensitivity of 0.001 mg) and then packing density of fibrous mats were determined with the corresponding formula. For determining the pore size and estimating porosity of electrospun mats, it was utilized from ImageJ software [25] due to the good agreement of ImageJ measurements with actual experimental data [26]. The average pore size was determined after 50 measurements from FESEM images and percentage fiber and porous area of samples were compared considering setup combinations.
3. Results and Discussion
3.1. Viscosity and Electrical Conductivity of Polymer Solution
Electrical conductivity and viscosity of PVA solutions are given in Table 1. It is known that electrospinnability of a polymer solution basically depends on viscosity, electrical conductivity, and surface tension of polymer solution. In electrospinning process, polymer solutions with high or low viscosity values have some drawbacks because high viscosity limits the continuous flow of a polymer jet from needle tip to collector whereas low viscosity causes electrospraying instead of electrospinning and too many bead formation occurrence on as-electrospun fibers. By means of electrical conductivity, it is reported that electrospinnability is prohibited under the critical electrical conductivity values due to nonoccurrence of Taylor cone formation [27, 28]. Besides, the occurrence of Taylor cone formation is strictly affected from surface tension of polymer solution because electrospinnability is achievable as applied voltage overcomes the surface tension of the polymer solution. It is reported that the surface tension of PVA solution (12 wt%, DH: 88%) was in a favorable range [29]. Kinematic viscosity and electrical conductivity of the prepared PVA solutions were found to be consistent with previous studies [30–32].
Parameter | Value |
---|---|
Kinematic viscosity (mm2/sec) | 8.8452 |
Electrical conductivity (mS/cm) | 0.457 |
3.2. FESEM
Figure 3 shows the morphologies and diameter variations of PVA electrospun fibers considering the feeding type/collector combinations. FESEM images demonstrated that the electrospun fiber diameters were in the range of nanometers. The lowest and highest average fiber diameters were obtained by single needle/drum and multineedle/disc combinations, respectively. In multineedle/disc combination, standard variation in nanofiber diameter was in a wide range, and it was seen that coarse and flat-shaped fibers were fabricated. In previous studies, the formation of flat-shaped nanofibers was correlated with an increase in molecular weight of the polymer [30], solvent choice [33–35], electrospinning process parameters [33], and an increase in polymer concentration in the prepared polymer solution [30, 36]. Considering that the parameters mentioned in previous studies above are kept constant in this work, flattening of nanofibers by multineedle/disc combination is a result of the insufficient time for evaporation of solution till polymer jets try to reach the collector and the existence of many contact points while some amount of solvent evaporates on the collector [37, 38]. From these phases, it is concluded that the number of contact points on disc collector is distinctly higher than those of other collector types used in the present study. In addition, this case can be related with the blockingup of polymer jet with a vertically rotating collector like a disk collector and the interfering of bending instability of polymer jet with the help of a change in centrifugal moment. Salehuddin et al. reported that solutions from many nozzles combined together before being deposited on collector due to the attractions among polymer jets and coarser fibers were fabricated with multineedle feeding [39]. However, coarser PVA nanofibers with variable standard variations were fabricated by multineedle feeding on plate, drum, and disc collectors but not neither on rods nor between rods of birdcage collector. By the use of birdcage collector, average fiber diameters with single needle feeding was found higher than those of multineedle ones in contrast to other collector types. Comparing birdcage collector with its closest counterpart, drum collector, both mechanical and electrical forces are dominant in drum collector but in birdcage collector, electrical forces are more dominant than mechanical forces to induce and draw fiber alignment [40] because equally spaced gaps are available between rods of birdcage collectors while drum collectorsare entirely cylindrical in shape.
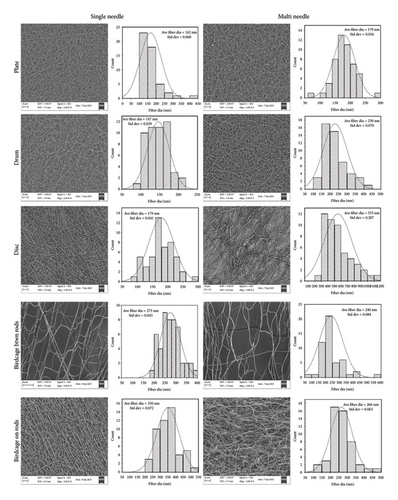
When the polymer jet reaches a birdcage collector, it is collected on rods with the triggering of mechanical and electrical forces while it is pulled from one rod to other by the interruption of electrical force. Beachley and Wen reported that an increase in gap distance in parallel electrodes leads to an increase in average fiber diameter and coarser fiber fabrication [41]. The results in this work are found to be consistent with this study. Distribution and direction of electrical force alter according to the different structure of parallel collectors [42]. With multineedle feeding on the birdcage collector, multiple polymer jets should attract from side plates on which initial points of the rods of birdcage collector are fixed, mostly drafted by electrical forces, and thereby finer fibers were electrospun with multineedle feeding/birdcage combination in contrast to single needle/other collector types. Among single-needle feedings, the finest average fiber diameter is obtained by drum collector due to continuous stretching of the polymer jet with electrical and mechanical forces as widely cited in literature. For stationary collector, plate collector, coarser PVA nanofibers are electrospun with multineedle feeding and imperfections such as beadings are observed. With respect to multineedle feeding, the PVA nanofiber continuity is found more applicable despite the high standard variation in PVA mats with single-needle feeding/plate collector combination. Figure 4 shows two distinct fields existed by deposition of nanofibers on the birdcage collector. Coarser (275 ± 0.045 nm and 350 ± 0.072 nm with single-needle feeding) and finer fibers (240 ± 0.084 nm and 266 ± 0.063 nm with multineedle feeding) are incorporated into a single mat, which will show different permeable characteristics on its own.

3.3. Mat Thickness
In previous studies, the thickness of electrospun mats has been correlated with fiber diameter and spinning duration [43, 44]. In this work, electrospinning was performed for 60 min for all different combinations. Figure 5 illustrates the comparison of mat thickness changing with respect to the average fiber diameter for the corresponding combination. Rotating collector caused an inconsistent relationship between fiber diameter and mat thickness, especially for disc collector/multineedle feeding. In multineedle feedings, disc collector gave the thinnest mat (2.60 ± 0.894 μm) despite its flat and coarse fibers (553 ± 0.207 nm). Replacing disc collector with drum collector resulted in approximately two times thicker mat fabrication (5 ± 1.581 μm) whereas finer nanofibers (230 ± 0.070 nm) with lower standard variation in fiber diameter were available than that of disc collector. This case invalidates the expressions claiming that thicker mats are fabricated by coarse nanofibers available in previous studies [43, 45, 46]. The interference to bending instability due to different feeding type/collector combination is transparently proved after mat thickness measurement. The different relations between average fiber diameter and mat thickness for each combination presented in this work show that the choice of collector geometry and feeding type has a crucial effect on the diversion of electrical forces and the dispersion of electrospun fibers on collector due to different fiber spreading routes. Results obtained by plane collector, the only stationary collector type studied in this work, support aforementioned claims because average fiber diameters and mat thickness are 162 ± 0.068 nm–12 ± 1.581 μm and 179 ± 0.036 nm–32.60 ± 7.056 μm for single and multineedle feedings, respectively. Thick mats are obtained with thinner nanofibers due to high fiber deposition on the collector. The use of a collector with larger surface area causes uninterrupted fiber deposition due to continuous electrical field with unstretching of the polymer jet on the stationary collector and thereby high standard variations are available by means of thickness. Vertically positioned plate collector acts as a blocker like disc collector despite its stationary state but multineedle feeding is responsible for high variations on mat thickness. In addition, polymer jet is focused on a larger area on disc and plate collector but on a narrow area on rotating drum and on rods of birdcage collector. The rotation speed of disc collector is responsible for the changes in mat morphology with respect to plane collector.
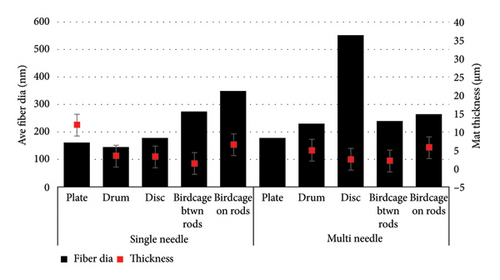
3.4. Pore Size and Porosity
The relations between average fiber diameter and average pore size are illustrated in Figure 6. The largest pores are obtained with the birdcage collector whichever feeding type is used, as also seen in FESEM images (Figure 3). The results were 7.287 ± 4.277 μm (btwn rods) and 4.454 ± 2.306 μm (on rods) for single-needle feeding and 9.312 ± 5.397 μm (btwn rods) and 6.140 ± 2.351 μm (on rods) for multineedle feeding. For disc collector, average pore size and variation (2.521 ± 1.064 μm) were found to be higher in multineedle feeding than in single-needle one. The decrease in standard variation is related to thinner nanofiber manufacturing via single-needle electrospinning and an increase in contact points due to nanofiber entanglement. Electrospinning of nanofibers on plate and drum collectors leads to making a consistent relationship between fiber diameter and pore size. The lowest pore size variation among studied combinations was obtained by plate collector/single-needle combination (1.318 ± 0.257 μm). Raksa et al. claimed that porosity, fiber diameter, and pore size of an electrospun mat could be changed by altering relative humidity [47]. In this work, all parameters including relative humidity were kept constant except collector/feeding combination. The degree of interconnection among nanofibers was manipulated by combination choice and, therefore, pore size is varied with respect to combination due to interference with fiber dispersion.
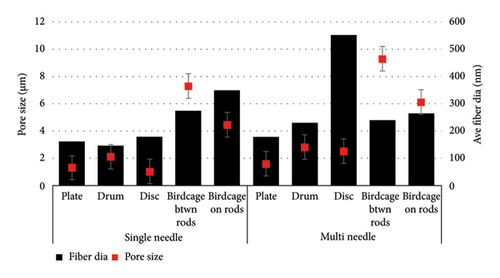
Porosity refers to the volume of voids inside a nanofibrous mat and measurements are performed with identical parameters by assuming that all pores are open in a typical nanofiber mat [48]. In this work, the porosity of electrospun mats was compared by means of % pore area. With the deposition on plate collector, the most porous fibrous mats were fabricated with different feeding types. In single-needle and multineedle feedings, the areas occupied by microsized pores were approximately 53.7% and 51.2% with average pore sizes of 1.318 ± 0.257 μm and 1.607 ± 0.259 nm, respectively. Among rotating collectors, the highest porous area was observed in the drum collector whichever feeding type was used but the number of pores were only 951 in multineedle feeding despite 1574 counts for single needle one. Considering that the average fiber diameter (230 ± 0.070 nm) and pore size (2.831 ± 0.374 μm) of mats in multineedle/drum combination (Figures 3 and 6), it is seen that changing the feeding type from multineedle to single-needle leads to the electrospinning of more porous mats consisting of smaller pores (2.116 ± 0.276 μm). It is reported that porosity is a sensitive parameter to even small changes in electrospinning parameters. Liu et al. claimed that deposited mat thickness and % porosity increased by decreasing the rotational speed of collector with single-needle feeding and the porosity of electrospun mats on the edges and at center of collector differred [49]. Considering that all parameters are kept constant and the only stationary collector in this work is the plane collector, the results are matched up with the study of Liu et al. [49], as seen in Table 2 and Figure 5. In drum collector, polymer jets fed by multineedles are guided to points on a narrower area of the collector as the collector is rotating while a polymer jet fed by single needle tries to reach same area. The oscillation of the polymer jet is not interrupted in bending instability state and thereby percentage porosity of mats with single-needle feedings is higher than that of multineedle ones.
Count | Porous area (μm2) | Fiber area (μm2) | Porous area (%) | Total area (μm2) | ||
---|---|---|---|---|---|---|
Single needle | Plate | 2334 | 313.942 | 270.722 | 53.698 | 584.664 |
Drum | 1574 | 305.549 | 278.534 | 52.320 | 584.083 | |
Disc | 2175 | 304.071 | 280.347 | 52.037 | 584.418 | |
Birdcage btwn rods | 434 | 244.348 | 340.339 | 41.798 | 584.687 | |
Birdcage on rods | 1046 | 263.498 | 321.456 | 45.053 | 584.954 | |
Multineedle | Plate | 1253 | 299.293 | 285.394 | 51.197 | 584.687 |
Drum | 951 | 296.613 | 288.354 | 50.701 | 584.967 | |
Disc | 1404 | 69.184 | 515.704 | 11.827 | 584.888 | |
Birdcage btwn rods | 453 | 112.229 | 472.763 | 19.182 | 584.992 | |
Birdcage on rods | 1316 | 259.440 | 324.978 | 44.400 | 584.418 |
However, there was no consistent relation among other rotating collectors/feeding combinations. Electrospinning of fibers on rods of birdcage collector resulted in an increase in pore count but the percentage pore area was nearly similar in different feedings. On the gap of birdcage collector (between rods of birdcage collector), % value of the porous area decreased dramatically despite a negligible increase in the number of pores by changing the feeding type from single to multineedle. This case is the result of a difference in the distribution of electrical force and the interaction of polymer jets on different parts of birdcage collector [50]. But for disc collector, the same dramatic decrease was observed with a remarkable decrease in pore count and % pore area. Centrifugal force of the vertically rotating negatively charged collector, interactions among polymer jets fed by multineedles, and restriction of bending instability are responsible for this dramatical decrease available in pore count and % porous area.
3.5. Packing Density and Mat Weight
Here, α is the packing density (unitless), m is the estimated basis weight (g m−2), t is the thickness (μm), and ρ is the density of the PVA polymer (1.25 g cm−3) [54].
A consistent relationship was established for rotating collectors and different feeding types. The tightest (2.941 and 0.96) and the heaviest (12.5 g/m2 and 6 g/m2) mats were fabricated with drum collector whatever feeding type was used. The loosest and lightest mat structure was available on the surface electrospun between rods of birdcage collector as it was expected. The gaps on the birdcage collector are lack of negative charges, thereby the polymer jet is forced to reach the nearest negatively charged field available on the birdcage collector while the collector is rotating. Due to the charge distribution difference available on different parts of the birdcage collector, the mats on gaps have the largest pore sizes, the lightest basis weights, and so the lowest packing densities as seen in Figures 6, 7, and 8 and Table 2. In contrast to the consistency seen in rotating collectors, the use of plate collector leads to inconsistency with different feedings. The heavier mats (8.75 g/m2) with medium packing density (0.583) were electrospun with single-needle feeding whereas the basis weight and packing density were 4.24 g/m2 and 0.104 with multineedle feeding. At this point, it is necessary to focus on the wideness of the electrospinnable area with this type of collector (Figure 2). On plate collector, negative charges spread over a large area, and the bending instability and elongation of polymer jet are improved with a single-needle feeding but fiber deposition is stricted to a narrower area. On the other hand, polymer jets fed continuously with multineedles interact with each other because the positive charges are carried with the jets and they push each other [55] while they are triggered to negatively charged collector and so the fibers are deposited on a larger area. This dilemma causes the fabrication of narrower mats with finer nanofibers in single-needle/plate collector combination but wider mats constructed from coarser nanofibers in multineedle/plate collector combination. When considering the pore size and porosity of mats deposited on plate collector (Figure 6 and Table 2), a decrease in packing density and basis weight is found meaningful for the plate collector.
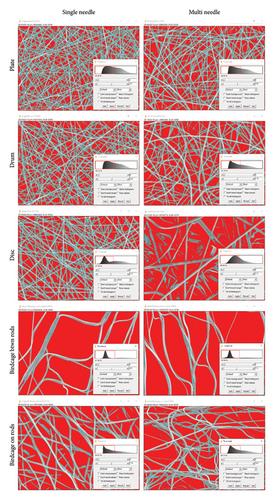

4. Conclusion
In this study, the effects of feeding type/collector combination on morphological properties of PVA electrospun mats are investigated. It is proved that electrospun mat characteristics are manipulated by different combinations of feeding types and collectors without changing any other electrospinning parameters. It is observed that the direction of spinnability and stretching degree of polymer jet are changed according to collector type because positively charged polymer jet tries to reach the place where negative charges are available on the collector. Bending stability and oscillation of the polymer jet are changed by multineedle feeding because positively charged polymer jets push each other while they are triggering the collector. Therefore, mats with larger surface areas are produced with multineedle feeding. An increase is observed in mat thickness and pore size but a decrease in % porosity, basis weight, and packing density by changing the feeding type from single needle to multineedle. Fiber fineness is varied according to combination and thicker nanofibers are manufactured on plate, drum, and disc collector but finer nanofibers are available on different parts of birdcage collector by changing the feeding type from single to multi-one. Flat-shaped and nanosized fibers are electrospun with multineedle/disc collector combination. Two distinct compositions are observed in a single matthat is electrospun on a birdcage collector. Among studied combinations, drum collector/single-needle feeding is promising for the manufacturing of thin electrospun mats with high packing density, small pore size, high porosity, finer fiber diameter, and high basis weight. This study will route the researchers studying miscellaneous fields, especially biomedical and filtration applications.
Conflicts of Interest
The author declares no conflicts of interest.
Funding
The research was supported by Scientific Research and Project Unit of KSU with grant number of 2021/3-25M.
Acknowledgments
The author would like to thank Adem Belverenli and Yunus Fedakar for their technical support.
Open Research
Data Availability Statement
Data sharing not applicable to this article as no datasets were generated or analyzed during the current study.