Aeroelastic Stability Analysis of a Laminated Composite Sandwich Panel With a Magnetorheological Fluid Core Under Yawed Supersonic Airflow
Abstract
In this study, we conducted an aeroelastic stability analysis of a laminated composite magnetorheological fluid (MRF) sandwich panel in supersonic airflow for varying yawed angles. The aeroelastic equations for a rectangular sandwich panel (MRF core layer and composite cross-ply laminate constraining and host layers) were established using a MIN3 plate element. Aerodynamic forces for different yawed angles would result in different coupled flutter boundaries of the panel. The first-order piston theory with a flow-yawed angle was employed. The flutter dynamic pressure was obtained through eigenvalue analysis. The effects of various parameters such as the magnetic field intensity, MRF core and constraining layer thicknesses, ply orientation, and yawed flow angle on the flutter dynamic pressure were studied for the simple- and fixed-support boundary conditions. Our results demonstrated that the flutter dynamic pressure of the laminated composite MRF sandwich panel (i) increased for increasing magnetic field intensity and constraining layer thickness; (ii) initially decreased and then increased with the increasing MRF core thickness; and (iii) was strongly influenced by the ply orientation and yawed flow angle.
1. Introduction
Traditional sandwich panel structures have been used for many applications in structural engineering such as airplanes, helicopter blade, space vehicles, wind turbine blade, and high-speed train. These panel structures have some limitations such as constant frequency and damping properties. Under the action of aerodynamic loads, a self-excited vibration behavior named panel flutter will occur. Panel flutter is an aeroelastic instability phenomenon caused by the coupling effect of aerodynamic, inertial, and elastic forces on the skin structure. Especially in supersonic aircraft [1], it seriously affects flight safety and, therefore, has received widespread attention from aeroelasticity experts [2]. In most previous studies, the flutter boundary and nonlinear response characteristics of the panel were mainly studied from the perspectives of structure, aerodynamics, and boundary conditions [3–6]. To improve stealth and aerodynamic performance, modern supersonic aircraft extensively use relatively large skinned panels, flattening the overall panels. Complex and harsh mechanical environments, such as high-speed airflow and aerodynamic heating, can inevitably lead to insufficient structural stiffness and strength margins and, hence, an increased risk of panel flutter. By changing the structural stiffness, damping, and mass properties, the flutter characteristics of the panel may be improved.
Piezoelectric actuators [7–9], constrained damping [10, 11], and nonlinear absorbers [12, 13] can change the structure properties or behavior to improve the flutter boundary of the panel. In recent years, among smart materials that have damping properties, materials such as electrorheological fluids (ERF) and magnetorheological fluids (MRF) [14] with controllable rheological attributes, are set as the viscoelastic cores in sandwich structures. They can modify the shear stress and viscoelastic damping of fluids through the action of electric and magnetic fields, thereby altering the structural characteristics of sandwich panels.
ERFs have been long used as core layers for vibration suppression in beam/plate structures. Yeh and Chen [15–17] established the equations of motion for an orthotropic sandwich plate with an ERF core layer and analyzed its ability for varying natural frequencies, loss factors, and static buckling loads. Mohammadi and Sedaghati [18] and Aboutablebi et al. [19] developed the nonlinear equations of motion for an ERF sandwich shell and plate structures and investigated the effects of small and large displacements, core thickness ratio, electric field intensity, and boundary conditions on their nonlinear vibration behavior. Gholamzadeh Babaki and Shakouri [20] and Shahali, Haddadpour, and Shakhesi [21] investigated the effects of functionally graded component ratios on the dynamic behavior of sandwich plates and shells with functionally graded face layers and an ERF core. Rahiminasab and Rezaeepazhand [22] examined the aeroelastic stability of ERF core sandwich plates in supersonic airflow and studied the influences of electric field intensity and the constraining and ERF layer thicknesses on the flutter dynamic pressure. They revealed the capability of the ERF core layer to shift the system flutter instability. Hasheminejad and Motaaleghi [23] investigated the aeroelastic response control of a simply supported two-dimensional sandwich panel with a tunable ERF core layer, resting on an elastic foundation and exposed to supersonic airflow.
Compared to ERF, MRF has been widely applied for its higher yield strength and invariance with temperature [24]. Sun, Zhou, and Zhang [25] studied the relationship between the magnetic field and the complex shear modulus of magnetorheological (MR) materials. They further examined the vibration characteristics of an adaptive beam for varying magnetic field intensities using a structural dynamic modeling approach. These studies illustrate the vibration control capability of MRF materials. Yeh and Shih [26] established a theoretical model of an MRF-based adaptive beam under an axial harmonic load and analyzed the influences of the magnetic field, beam length, and core thickness ratio on its loss factor, dynamic instability, buckling load, and natural frequency. Lara-Prieto et al. [27] experimentally investigated the vibration characteristics controllability of MRF-based cantilever sandwich beams. Rajamohan, Rakheja, and Sedaghati [28–30] investigated the vibration responses of a partially treated multilayer MRF beam. They revealed that the transverse displacement response and natural frequencies of the partially treated MRF beams are strongly affected by the applied magnetic field intensity, along with the fluid pocket location and length. Additionally, they (i) combined finite element analysis with optimization algorithms based on sequential quadratic programming (SQP) and a genetic algorithm (GA) to identify optimal locations for MRF treatment and achieve maximum modal damping corresponding to the first five modes of flexural vibration (individually and simultaneously) and (ii) formulated an optimal control strategy based on the linear quadratic regulator (LQR) and a full state dynamic observer to suppress the beam vibration. Li et al. [31] established the mathematical model of a sandwich plate with MRF using the finite element method and studied the natural frequencies and loss factors for varying parameters. Manoharan et al. [32] investigated the effect of a laminated composite MRF sandwich plate ply orientation on (i) the variation of natural frequencies and loss factors and (ii) the dynamic response of the sandwich plate under harmonic force excitations for varying magnetic fields. Eshaghi, Sedaghati, and Rakheja [33] numerically and experimentally investigated the vibration characteristics of a partially treated sandwich plate considering different boundary conditions and magnetic flux intensities. The GA was used to identify optimal locations for MRF treatments to maximize the variations in natural frequencies and damping ratios in response to that in the magnetic field. Aboutalebi et al. [34] performed postyield MRF characterization and studied the nonlinear vibration behavior of MRF-based sandwich plates undergoing large amplitude oscillations. Asgari et al. [35, 36] studied the aeroelastic characteristics of a sandwich beam with a partially treated MRF core in supersonic airflow and showed that the critical nondimensional aerodynamic pressure of the sandwich beam is strongly influenced by the core and constraining layer thickness, magnetic field intensity, and core configuration. Eshaghi [37] investigated the effect of plate parameters, boundary conditions, and magnetic field intensity on sandwich MR plate flutter boundaries. Houshangi et al. [38] focused on the supersonic flutter characteristics of truncated sandwich conical shells with an MRF core. They studied the effects of various parameters, such as total thickness, length, semivertex angle, magnetic field intensity, and MRF core thickness on the shell stability regions.
Although these previous works provided excellent contributions, to the best of our knowledge, no studies have been conducted on the aeroelastic characteristics of a sandwich panel with an MRF core, laminated composite host, and constraining layers in supersonic airflow with a yawed angle. Therefore, in this study, we investigated a rectangular laminated composite sandwich panel with an MRF core in supersonic airflow with a yawed angle.
The rest of the article is structured as follows: The aeroelastic equations for the MRF core are established in Section 2; program code validation is demonstrated in Section 3; analysis of the aeroelastic characteristics of the laminated composite MRF sandwich panel is illustrated in Section 4; and the conclusion is presented in Section 5.
2. MRF Core Aeroelastic Equations
A rectangular sandwich panel with an MRF core layer and composite cross-ply laminates as the host and constraining layers under a supersonic airflow is shown in Figure 1. Here, a and b are the length and width of the panel, respectively; h1, h2, and h3 are the heights of the constraining, MRF, and host layers, respectively; V∞ is the supersonic flow speed; and θ is the yawed flow angle between the airflow direction and the x-axis. Both the constraining and host layers consisted N composite layers.
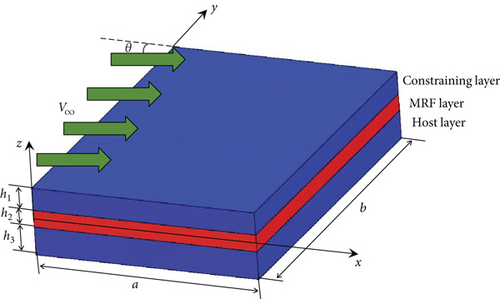
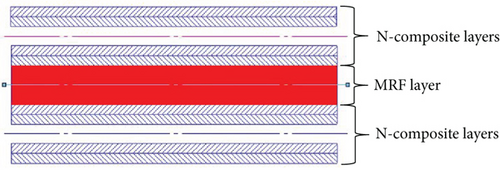
2.1. Element Model and Shape Function
[Hw], [Hwθ], [Hθx], [Hθy], [Hu], and [Hv] are the displacement interpolation functions represented by area coordinates, as shown in Appendix A.
2.2. Constitutive Equations
2.3. First-Order Piston Theory Aerodynamics With a Flow-Yawed Angle
2.4. Governing Equations
The natural frequency and flutter dynamic pressure, λcr, can be determined by the eigensystem described by Equation (28). When λ = 0, ΩI is the natural frequency of the MRF sandwich panel; Panel flutter occurs for ΩR > 0 . The D11 component varies with changes in the geometrical parameters of the composite lamina. To better represent the flutter dynamic pressure, we defined and used .
3. Methodology Verification
Since, to the best of our knowledge, no studies have been conducted on the aeroelastic stability of a composite laminated MRF sandwich panel, structure and aerodynamic load programs were validated separately. To verify the structure program, we compared the values of the first three natural frequencies of a composite laminated MRF sandwich panel at a magnetic field intensity of Ga = 400G (derived in the present analysis and those reported in [32]; Table 1). The results had good consistency, so, it verified the accuracy of the mass and stiffness matrices of the computed structure.
Present analysis (Hz) | Manoharan et al. [32] (Hz) | |||||
---|---|---|---|---|---|---|
Mode No. | ||||||
1 | 2 | 3 | 1 | 2 | 3 | |
0.5 | 127.2 | 190 | 262 | 129.2 | 191.7 | 266.3 |
1.0 | 107.4 | 160 | 222.8 | 108.1 | 160 | 222.5 |
1.5 | 97.1 | 144.7 | 200 | 97.6 | 144.2 | 198.7 |
2.0 | 90.4 | 135 | 184 | 90.6 | 134.5 | 181.1 |
2.5 | 85.5 | 128.1 | 172.8 | 85.3 | 127.5 | 170.6 |
In order to validate the aerodynamic load calculation, we performed a flutter dynamic pressure analysis of a simple-support [−40°/40°/−40°] composite panel [41]. The flutter dynamic pressure value was computed to be λcr = 382.4 (Figure 2), which was approximately the same as the previously reported value of λcr = 382[40]. Owing to the program accuracy verification, we employed it to study the flutter characteristics of the composite laminated MRF sandwich panel.
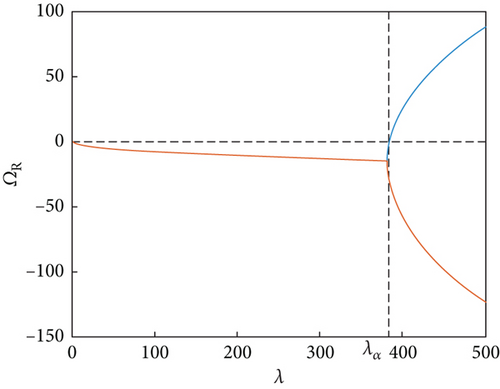
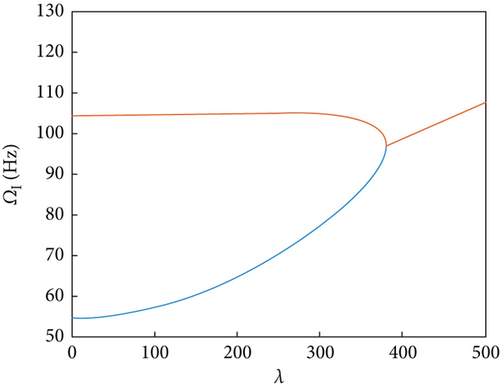
4. Results and Discussion
For the composite MRF sandwich panel, we used two types of boundary conditions, namely, four-sided fixed-support (CCCC) and four-sided simple-supported (SSSS). The properties of the constraining and host layers are mentioned as follows: E1 = 131GPa; E2 = E3 = 10.34GPa; G12 = G23 = 6.895GPa; G13 = 6.205GPa; υ12 = υ13 = 0.22; υ23 = 0.49; and ρ1 = ρ3 = 1627kgm−3. The MRF layer density was fixed at ρ2 = 3500 kgm−3. The base model parameters were fixed as follows: The length and width of the base model were a = 380 mm, and b = 350 mm, respectively; the flow-yawed angle was θ = 0°; the ply orientation of the constraining and host layers was [0°/90°/0°/MRF/0°/90°/0°]; h1/h3 = 1 and h2/h1 = 1.2.
4.1. Flutter Boundary Analysis
For a magnetic field intensity of 400 G on the MRF sandwich panel, we analyzed the variation of the real and imaginary parts of the eigenvalues with the dynamic pressure under the simple-support (Figure 3) and fixed-support (Figure 4) boundary conditions. When the real part of the first characteristic root switched from a negative to a positive value, the panel experienced unstable(flutter) dynamic pressure. When the panel experiences flutter, the first and third modal frequencies are close to each other but do not overlap due to the presence of aerodynamic and MRF damping. The panel experiences flutter due to the coupling of the first and third modes (mode-coupled flutter). Although coupled flutter also occurs for the second and fourth modes at higher dynamic pressures, the flutter boundary is only the dynamic pressure corresponding to the smallest unstable point. It was also observed that the flutter dynamic pressure at the fixed-support boundary was greater than that at the simple-support boundary.
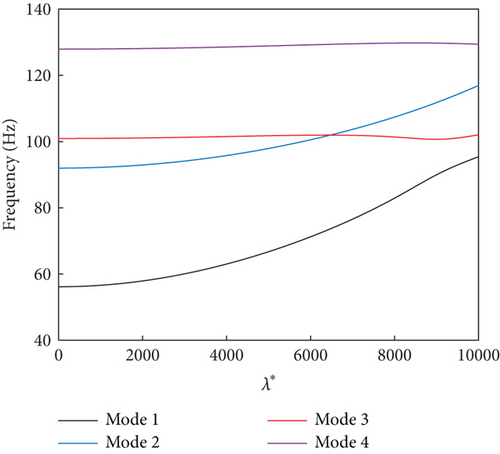
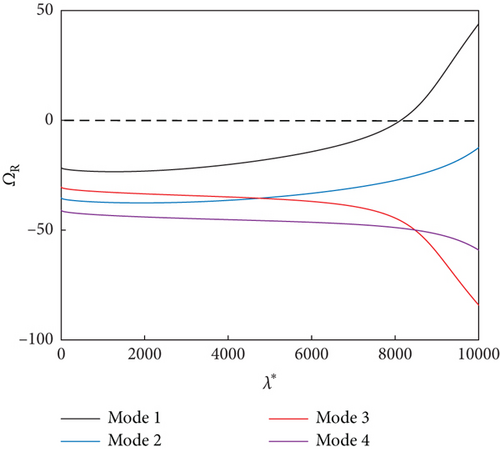

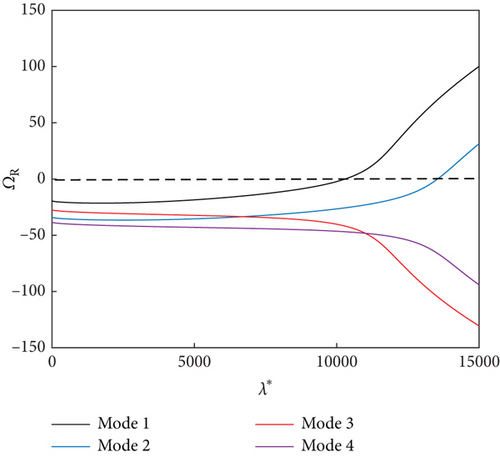
4.2. Influence of the Magnetic Field Intensity
We further analyzed the influence of the magnetic field intensity on the flutter dynamic pressure and first-order modal frequency of the MRF sandwich panels under the simple- and fixed-support boundary conditions (Figure 5). From the figure, it can be seen that as the magnetic field intensity increased, the flutter dynamic pressure of the MRF sandwich panel increased as shown in Figure 5(a). This is mainly because as the magnetic field intensity increased, the stiffness characteristics of the MRF sandwich panel increased, manifested as an increase in the first-order modal frequency as shown in Figure 5(b), thereby increasing the flutter dynamic pressure. When the magnetic field intensity was increased from 0 to 700 G, the flutter dynamic pressure increased by (i) 76.3% for the simple-support panel and (ii) 56.5% for the fixed-support panel. However, the rate of increase in flutter dynamic pressure for both cases decreased with increasing field intensity. This is mainly determined by the relationship between the MRF and the magnetic field intensity. As the magnetic field intensity increases, the shear stiffness of MRF rises rapidly at the initial stage; and the higher the magnetic field intensity is, the smaller the rate of increase of the MRF shear stiffness will become.
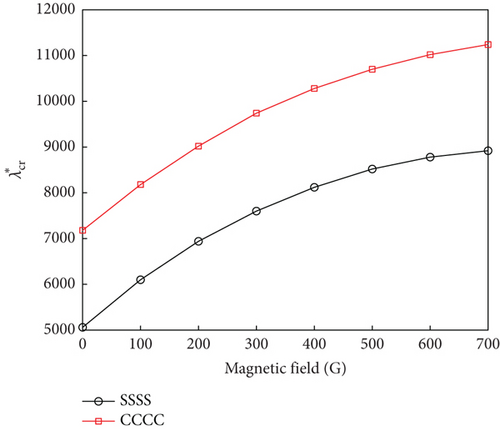
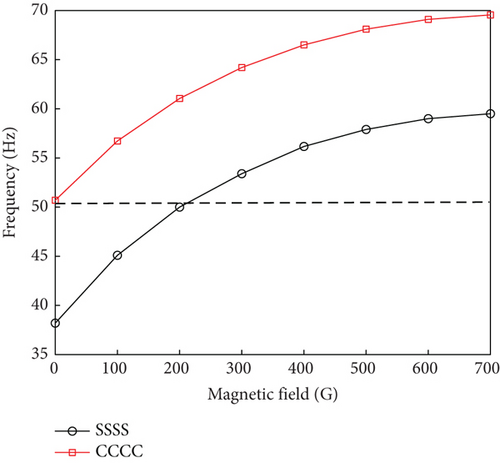
4.3. Influence of MRF Core Thickness
We further investigated the variation characteristics of flutter dynamic pressure with respect to the h2/h3 ratio for different values of h1/h3 (Figure 6). With increasing h2/h3, the flutter dynamic pressure is initially reduced followed by an increase. However, for smaller values of h1/h3, the flutter dynamic pressure decreases very slightly with the increase of h2/h3 at very small values of the ratio. Increasing the thickness of the MRF core is manifested by increasing the damping and stiffness characteristics of the panel. For smaller MRF core thicknesses, the damping characteristics (light damping) play a dominant role. According to the works by Lottati [42], for lightly damped nonconservative systems, adding small structural damping can significantly reduce the instability boundary of the system. The lower the damping, the more reduction in instability boundary. In this condition, slightly increasing the damping reduces the flutter dynamic pressure. As a result, the flutter dynamic pressure decreases with the increase of h2/h3 for small h2/h3 values. As the MRF core thickness increases, the panel stiffness increases and starts playing a more decisive role. This results in an increase in the flutter dynamic pressure with the increasing h2/h3.
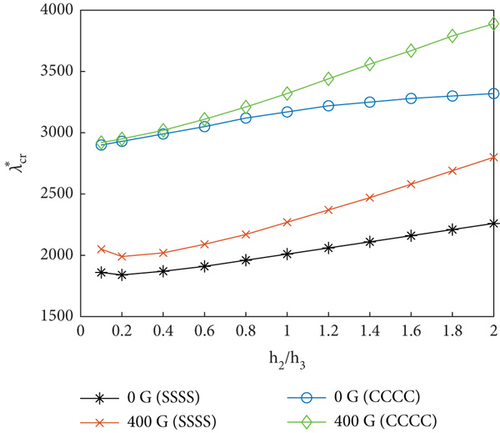
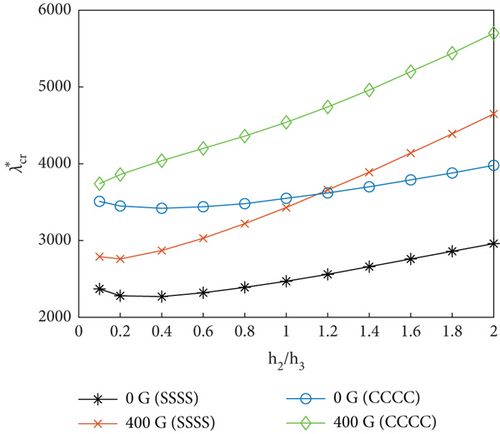
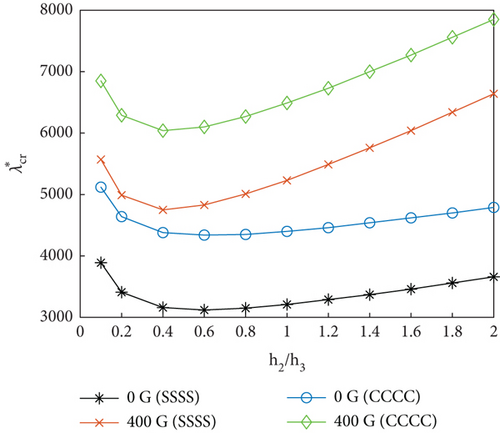
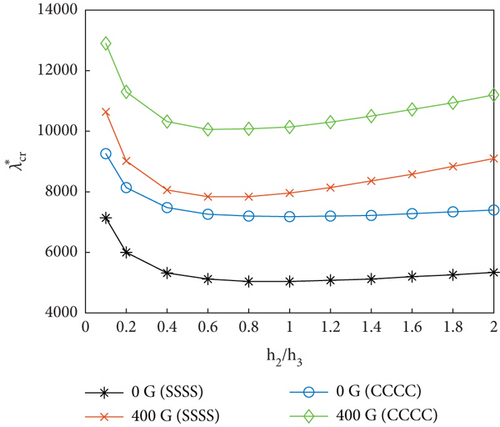
As the MRF core thickness increases, the magnetic field intensity strongly influences the panel flutter. Additionally, as the constraining layer thickness increases, the MRF sandwich panel stiffness also increases, leading to an increase in the flutter dynamic pressure (Figure 6).
4.4. Influence of Ply Orientation and Yawed Flow Angle
The influence of ply orientation and yawed flow angle on the flutter dynamic pressure of the MRF sandwich panels was studied by simulating seven different ply orientations (, , , , , and ) and five different yawed flow angles (0∘, 30∘, 45∘, 60∘, and 90∘). Figure 7 shows the variations of the flutter dynamic pressure of MRF sandwich panels with magnetic field intensity under different ply orientations and yawed flow angles for both simple- and fixed-support boundary conditions. Irrespective of the yawed flow angles, ply orientations, and boundary conditions, the flutter dynamic pressure increased with the increasing magnetic field intensity. For a fixed magnetic field intensity, the flutter dynamic pressure was affected by ply orientation (Figure 8) and the yawed flow angle (Figure 9). When the yawed flow angle is 0∘, the flutter dynamic pressure decreases with the increase of the ply orientation, the main reason is that the stiffness of the panel in the airflow direction decreases with the increase of the ply orientation. As the yawed flow angle increases, the flutter dynamic pressure of the panel first increases and then decreases with the increase of the ply orientation. When the yawed flow angle is 90∘, the flutter dynamic pressure increases with the increase of the ply orientation. Similar conclusions can be drawn regarding the influence of yawed flow angle. When the ply orientation is , the flutter dynamic pressure decreases with the increase of the yawed flow angle. As the ply orientation increases, the flutter dynamic pressure of the panel first increases and then decreases with the increase of the yawed flow angle. When the ply orientation is , the flutter dynamic pressure increases with the increase of the yawed flow angle.
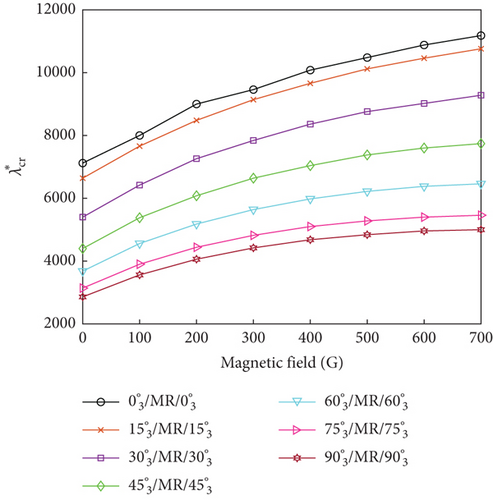
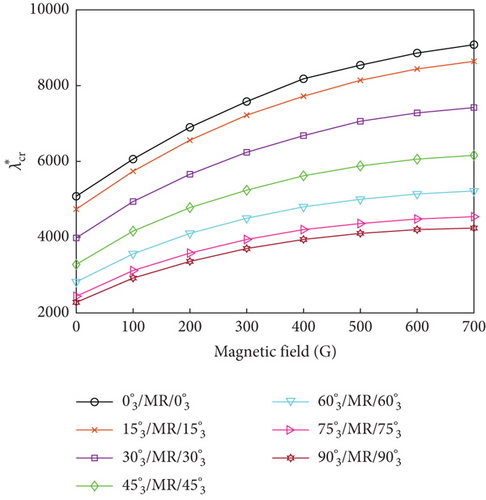
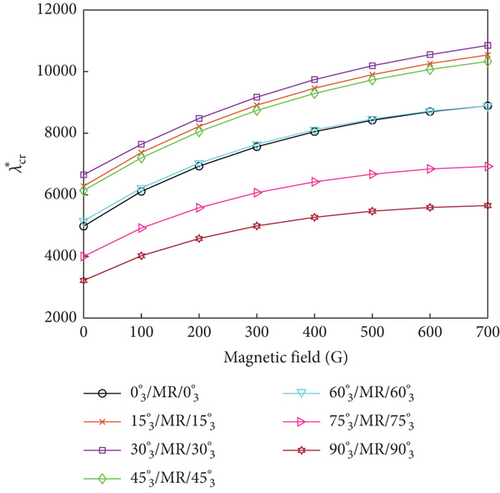
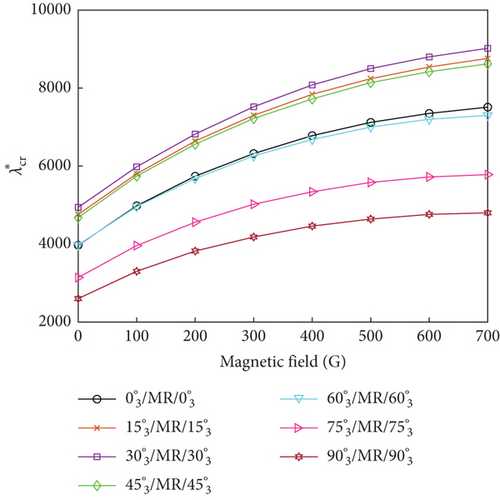
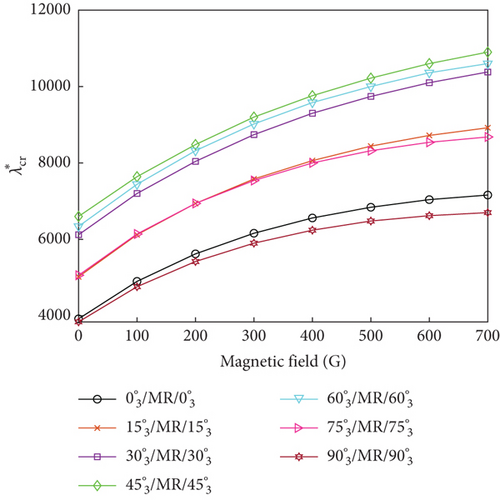
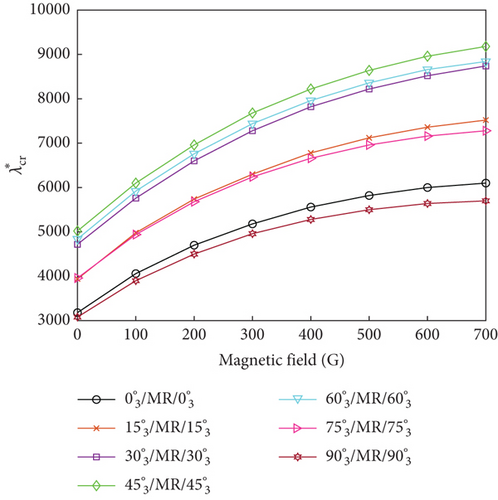
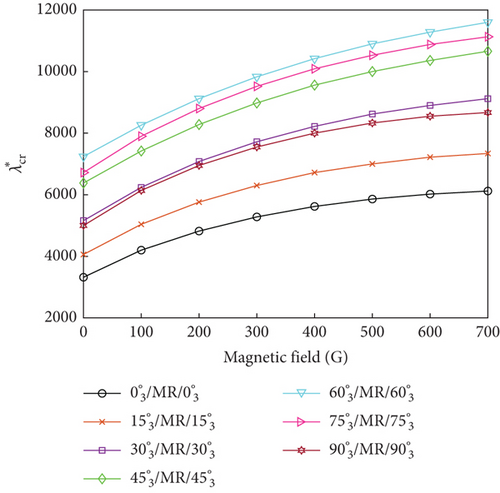
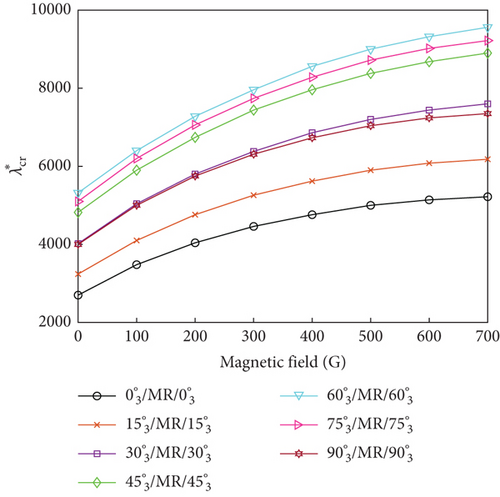
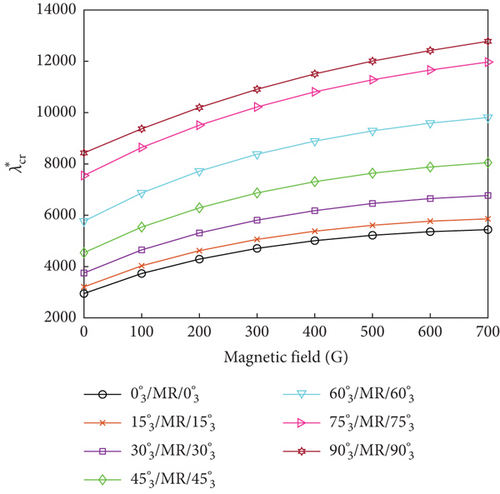

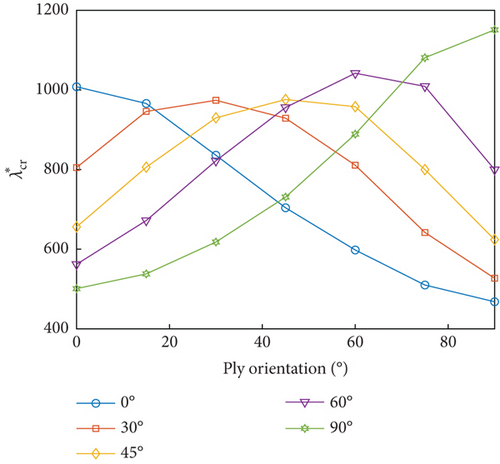
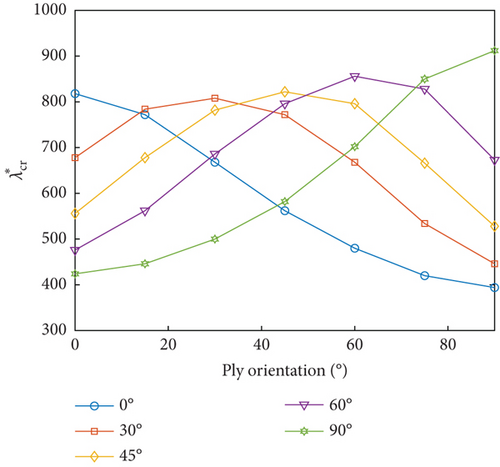
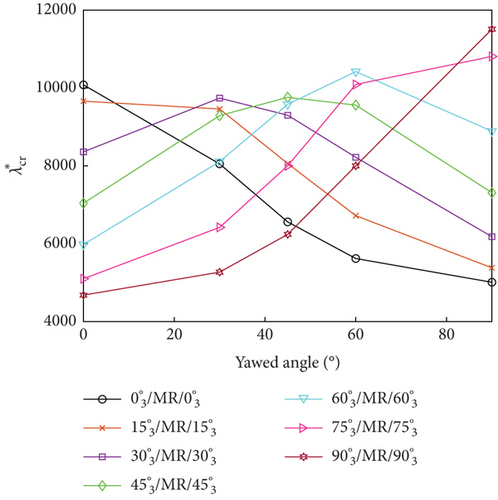
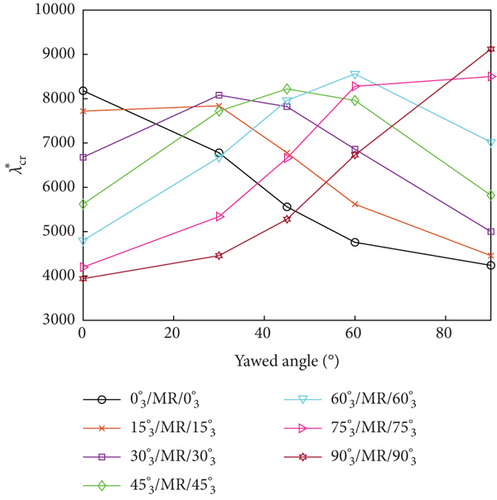
In summary, the maximum flutter dynamic pressure was obtained when the ply orientations of the constraining and host layers were aligned with the yawed flow angle, as the panel bending stiffness reached its maximum value for this condition.
5. Conclusion
- 1.
With the increasing magnetic field intensity, the flutter dynamic pressure of the MRF sandwich panel gradually increases, but its rate of increase decreases. The influence of magnetic field intensity on the dynamic pressure of the MRF sandwich panel with a simple-support boundary was higher than that with the fixed-support boundary.
- 2.
The flutter dynamic pressure initially decreases and then increases with the increasing MRF core thickness, which also enhances the influence of the magnetic field intensity on the panel flutter. Additionally, an increase in the constraining layer thickness also increases the flutter dynamic pressure.
- 3.
The peak flutter dynamic pressure is obtained when the ply orientations of the constraining and host layers are aligned with the yawed flow angle.
Conflicts of Interest
The authors declare no conflicts of interest.
Funding
This study was funded by the Natural Science Basic Research Program of Shaanxi (Program No. 2023-JC-QN-0019) and the National Natural Science Foundation of China (No. 11872050).
Acknowledgments
This study was funded by the Natural Science Basic Research Program of Shaanxi (Program No. 2023-JC-QN-0019) and the National Natural Science Foundation of China (No. 11872050).
Appendix A. [Hw], [Hwθ], [Hθx], [Hθy], [Hu], and [Hv]
The relationship between the coordinates of the three nodes can be found in [39].
Appendix B. Q11,Q12, Q21, Q22, Q44, Q55, Q66, and Tσ,Ts
β is the ply angle of the composite lamina.
Appendix C. m, ca, k0, ka, and w
Open Research
Data Availability Statement
The data used to support the findings of this study are available from the corresponding author upon request.