Heat Treatment Effect on Some Mechanical Properties of FDM-Manufactured PCL Wood-Based Biopolymer
Abstract
The study investigates some 3D printing output parameters of a polycaprolactone (PCL) wood-based biopolymer, a category of materials obtained by embedding wood-derived components within polymeric matrices. These wood-based biopolymers have garnered significant focus in recent years due to their environmental friendliness and vast potential across many different fields. A full factorial design with three independent variables (layer height, printing speed, and heat treatment exposure time) at three levels was considered. The research explores printing speeds higher than the speed ranges typically investigated in the existing scientific literature on FDM 3D printing of wood-based polymers. Additionally, in this study, heat treatment is proposed as a post-processing operation to enhance certain crucial proprieties such as surface quality, hardness, mechanical strength, and accuracy. The findings reveal that heat treatment has a positive influence on the investigated output parameters. Notably, 3D printed samples subjected to heat treatment exhibit an average decrease of 112.1% in surface roughness for a 5-min exposure time and 121.73% for a 10-min exposure time. The surface hardness of the samples also improved after applying the heat treatment. The part hardness improved with an average of 0.65%. Furthermore, significant correlations were observed between layer height and surface quality, hardness, printing speed, and tensile strength. Notably, printing speed contributed significantly to the variation in tensile strength, accounting for 52.77% of the parameter’s variation. These insights shed light on the optimization of 3D printing processes for wood-based biopolymers, paving the way for enhanced performance and applicability across diverse fields.
1. Introduction
In the last decades, due to the advances registered in the field of 3D printing technologies and polymers and the recycling concerns, the popularity of wood–plastic composites had increased. Wood-based plastics are usually discussed as raw material for furniture and other interior structural materials, replacing the natural wood that is a limited resource that is becoming more and more expensive. Sustainability targets and increasing ecological worries have conducted to an increase for renewable and biodegradable materials demands with compatible or even superior proprieties and performances.
Wood-based polymers (WPC) are materials that incorporate in their structure wood or wood-derived components mixed into polymer matrices. Often, these materials have a reduced environmental impact; most of the wood-based polymers are decomposable, meaning they can break down naturally over time. Wood-based polymers contain wood fibres or particles that result from wood waste and by-products from other industries and, therefore, contribute to waste reduction and efficient resource utilization. The combination of wood fibres or particles with polymer matrices can enhance the mechanical properties of the resulting composite. Therefore, they may exhibit improved strength, stiffness, and toughness compared to their individual components. Wood–polymer composites are versatile and adaptable and find applications in various industry fields—construction, automotive, art, packaging, and other consumer goods.
While wood-based polymers offer many advantages, for some specific applications when choosing these materials, it is essential to overview some particular aspects like moisture absorption and decay resistance. Researchers and industries are constantly exploring and developing new formulations to optimize the performance of wood-based polymer composites.
Fused deposition modelling (FDM) is an emerging technology with many applications in field as automotive, aerospace, medical, food, and architecture. FDM is part of additive manufacturing technologies for which the three-dimensional parts are generated by layering and extruding thermoplastic materials. During the printing process, a filament made of the thermoplastic material, usually shaped as a spool of plastic wire, is directed through a heated nozzle. The nozzle moves along the generative paths, depositing the melted material layer by layer. Once the layer cools and solidifies, it bonds with the previous layers, gradually building up the part.
The FDM-printed part accuracy and mechanical properties are strongly influenced by the material proprieties and the machining process parameters. In additive manufacturing process, parameters have a stronger influence over the final part aspect, physical and mechanical proprieties compared to the traditional cutting technologies. The process parameters of the 3D printing such as the layer height, wall shell thickness, printing temperature, bed temperature, printing speed, infill structure, and infill density percentage have a strong influence on the mechanical proprieties of the printed products.
Nowadays, a special attention was directed to the research involving the developing of 3D printing techniques for wood-based biopolymers [1, 2, 3, 4, 5, 6, 7, 8, 9, 10]. Most of the paper published in this field investigate the mechanical proprieties of parts generated by additive manufacturing of commercial of self-made wood-based polymers filaments. The most popular type of wood-based polymers discussed are the ones resulted by using polylactic acid (PLA) polymer matrix mixed with different percents of by-products or waste products resulting from woodworking operations such as wood fibres, sawdust, or wood chips.
Kariz et. al [1]. studied the influence of wood content of polylactic acid wood-based polymers on the properties of 3D printed parts. They obtained six WPC filaments by varying the wood particles loading level from 0% to 50% and after testing them reported that by increasing the wood content the density of the filaments and of the 3D printed parts slightly decreased. For the 10% wood particle contents, the tensile strength of the filaments increased by approximately 22 MPa and decreased with almost 25 MPa for the filaments with 50% wood content.
Also, Martikka et al. [6] demonstrated that the mechanical properties of WPC can be adjusted by varying the amount of wood infill, although the strength of WPCs were inferior to those of pure PLA material. These findings were also supported by another studies [8, 9]. By adding fillers and lubricants, the solid content and viscosity of the wood-based polymers is diminished, and the bond strength of WPCs is enhanced [11]. Some authors attributed the inferior mechanical properties of 3D printed WCPs to the low pressure during the manufacturing process [5].
Beside the biomass infill percentage, also other process parameter exposes important influence over the mechanical proprieties of wood-based polymer 3D printed parts. It was showed by Arias-Nava et al. [7] that layer thickness, also referred as layer height, exhibit a significant influence on the mechanical proprieties. The tensile strength decreases with the increase of this process parameter. Moreover, there is a significant correlation between layer thickness and other process parameters as, for instance, the printing temperature and the influence over the mechanical properties of WPC printed parts.
Yang et al. [2] had determined the morphology and mechanical properties of WPC parts obtained with wood fibre/polylactic acid composite filaments. They used printing speeds of 30, 50, and 70 mm/s. They reported that the printing speeds have a negative influence over the density of the WPC printed parts, and lower density was obtained for the higher levels of the printing speed process parameter. Also, the printing speed exposes influence over the 3D printed part surface colour. The WPC 3D printed parts printed at lower printing speeds had a darker surface colour than the parts printed at a high printing speed. The investigated process parameter, however, did not expose a significant influence over the tensile and flexural properties of the printed WPC parts. By increasing the printing speed from 30 to 70 mm/s, the compressive strength and modulus of the WPC printed parts decreased with 34.3% and 14.6%. The authors used scanning electronic microscopy (SEM) to investigate the wood-based polymer surfaces obtained by FDM process with different printing speeds. The images obtained showed uneven surfaces with narrower width for the parts printed with higher printing speeds.
Huang et al. [4] investigate the shape of wood particles on the mechanical proprieties of wood-based polymers and concluded that the geometric features and surface asperities of the wood particles exhibit a more significant influence on the WPC printed parts than the wood particles species. Parts with higher strengths and densities were linked with WPCs obtained by addition of smooth round shape particles. It has also been observed that as the wood content is increased, the surfaces of 3D prints become rougher, revealing more voids and clusters of wood particles due to the clustering and clogging of wood particles in the printer nozzle [1].
Mai et. al [3]. investigated how the 3D printing input parameters influence the aesthetic of 3D printed parts obtained by FDM of a commercial WPC filament, type Laywoo-D3 produced by Kai Parthy–Lay Filaments (Germany). Aesthetic wood features as the grain pattern, surface texture, and colour were analysed and discussed.
He et al. [12] studied the effect of microscopic voids on the mechanical performance of continuous 3D printed CF/PA6 composites and highlighted the importance of process parameter optimization and in-process monitoring in regard to limiting void content by proving that voids have substantial negative impacts on some of the mechanical characteristics of 3D printed polymer composites (transverse tensile strength and flexural strength).
Relatively few research work that analyses the possibility and impact of heat treatment on the proprieties of wood-based polymers had been reported. Most of the paper published investigate the efficiency of applying head treatment to wood fibres before mixing with the polymeric matrices.
Aydemir et al. [13] analysed how the wood filler heat treatment influences the mechanical and viscoelastic properties of nylon 6 wood-based composites. The flexural modulus of elasticity was positively influenced by increased by the content of heat-treated pine and maple particles.
Yang et. al [14]. studied the influence of the addition of heat-treated wood particles on the mechanical characteristics and how the material deforms under constant load in time of a WPC obtained by recycled wood. The results reveal that the composites, the printed parts with heat-treated wood particles, had a lower moisture content and exposed lower water absorption, better bond strength, and thickness swelling even if the bending characteristics remain the same.
Gardner et. al [15]. had analysed the impact of thermally modified wood as filler for two different biopolymer matrices polylactic acid (PLA) and polybutylene succinate (PBS). The results obtained showed that the increase of wood content had a positive influence on the modulus of elasticity of PLA and PBS although the addition of thermally modified wood conducts to a slightly increase of the tensile strength of PBS and a decrease of the tensile strength of PLA WPCs.
Subasinghe et. al [16]. studied the microwave irradiation influence on a high-density polyethylene (HDPE) wood-based polymer. By adding microwave-treated wood particles, the mechanical and physical proprieties of the WPC were significantly improved. By increasing the microwave-treated wood particle content from 5% to 10%, the tensile strength doubled its value. Another study [17] found that the composites containing heat-treated wood exhibited higher crystallinity compared to those made with untreated wood–HDPE composites.
Biowood filaments manufactured by Rosa3D, Poland, is made of a composite wood-based biopolymer. The main components of these material are polycaprolactone (PCL), polyester, lignin, starch, natural resins, waxes and oils, natural fatty acids, cellulose, and natural fibres [18, 19]. The filament has PCL as polymeric matrix. It had been reported that natural fibres can enhance mechanical proprieties of polycaprolactone [18].
Zgodavová et al. [20] investigated the mechanical properties, geometric accuracy, and weight of the printed WPC parts and aspects as printing time, filament price, and environmental sustainability of thermoplastic materials for printing shield frames. Among the materials tested, they choose PHA Biowood Rosa3D, a prior version of the Biowood Rosa 3D. The process input parameters considered in the study were the layer height, number of perimeters, extrusion width, infill density, and printing temperature. They reported that among the investigated factors, a more significant influence on the mechanical properties of PHA Biowood 3D printed parts was exert by the infill and the interaction between the layer thickness and printing infill.
This paper analyses the influence of some FDM process input parameters—layer height, HL (inmillimetre); printing speed, s (in millimetre per second); and heat treatment, as post-process on the surface quality, hardness, accuracy, and tensile strength of commercially available Biowood, produced by Rosa 3D, Poland. The novelty of this study relays on the usage of printing speeds significantly higher than the ones recommended by the filament producer and generally reported in the research work dealing with wood-based polymers 3D printing published. This higher printing speeds can considerably improve the productivity and hence and therefore open new opportunities regarding the use of printed WPC components in new fields. Another novelty approach consists in the appliance of heat treatment as a post-processing treatment for the WPC parts and not only for the wood content, as studied till recently.
2. Materials and Methods
The study employed a 33 full factorial experimental design. The independent input variables chosen for the experimental procedure were the following: the layer height (HL) (in millimetre) and printing speed (in second) (millimetre per second), and the heat exposure time (t) (in minutes). The values of the input factor levels chosen in this study for each of the independent variable mentioned above are presented in Table 1.
Level | Input independent variables | ||
---|---|---|---|
Layer height HL (mm) | Printing speed s (mm/s) | Heat treatment time t (min) | |
1 | 0.2 | 200 | 0 |
2 | 0.3 | 250 | 5 |
3 | 0.4 | 300 | 10 |
- (1)
Shore D surface hardness
- (2)
Maximum height Sz (µm) of the top surface and lateral surface of the printed parts
- (3)
Accuracy, height dimensional errors, ΔH (mm)
- (4)
Ultimate strength, UTS (MPa)
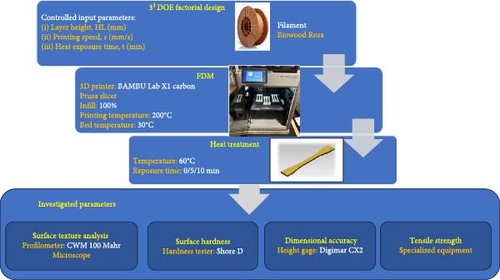
The parts used in the experiments were produced by fused deposition material 3D printing of commercially available ROSA 3D Filaments (Poland). Biowood is a biopolymer that contain natural and renewable resources. The Biowood wooden thermoplastic polymer filament has a polycaprolactone (PCL) polymer matrix and natural fibres and fillers such as starch, lignin, natural resins, waxes and oils, natural fatty acids, cellulose, and natural fibres [18]. Table 2 summarizes some of the main physical properties of the Biowood polymer, as offered by the producer. The printing recommendations suggested by the filament producer are low extrusion temperatures, between 170 and 210°C, non-heated bed or 30−50°C heated bed, and extrusion nozzle of minimum 0.5 mm [18]. By considering these recommendations, the printing temperature was set to 200°C, and the bed of the printer was heated at 30°C. The infill was set to 100%.
Property | Value |
---|---|
Softening point (°C) | 50 |
Density (kg/m3) | 1,260 |
Elastic modulus (MPa) | 3,200 |
Tensile strength (MPa) | 36 |
For the experimental tests, standardized specimens ISO 527 type 1B were used in this study for the purpose of tensile strength testing. The test sample geometry and dimensions, according to ISO 527, are presented in Figure 2.
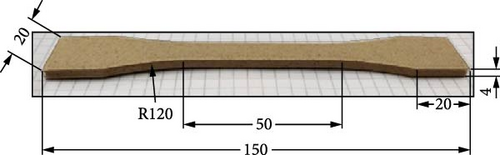
The parts were generated by 3D printing on an desktop semi-professional FDM printer type X1-Carbon Combo produced by Bambu Lab, Austin, Texas, USA (Figure 3). The main technical specification offered by the producers for the printer include resolution of 7 μm, acceleration of 20 m/s, and a maximum printing speed of 500 m/s. The 3D printing conditions were set using a Prusa-type slicer. The extruder nozzle was a 0.6 mm diameter hardened steel nozzle 50 HRC, as recommended by the Biowood filament producer. All the tested samples were generated with 100% infill. The test specimens were printed flatwise, and due to the fact that the specimens were 100% infill, the raster angle was 45° on every layer. Layer heights parameter levels were selected considering the nature of the filament. For the experiments, it was used a 0.6 mm diameter nozzle. To avoid clogging and material overflow that can influence the dimensional accuracy of the specimens, caused by the biopolymer wood fibre contain, the layer height did not exceed 75% of the nozzle diameter.
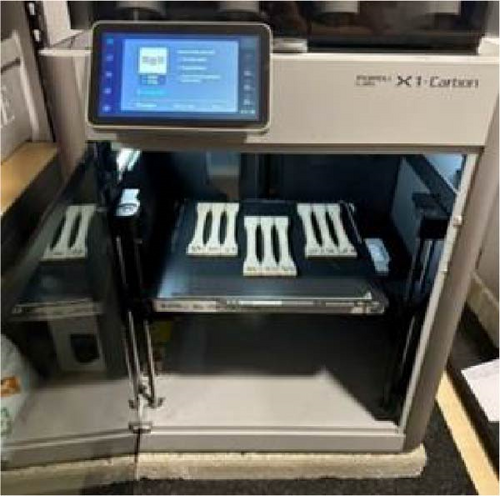
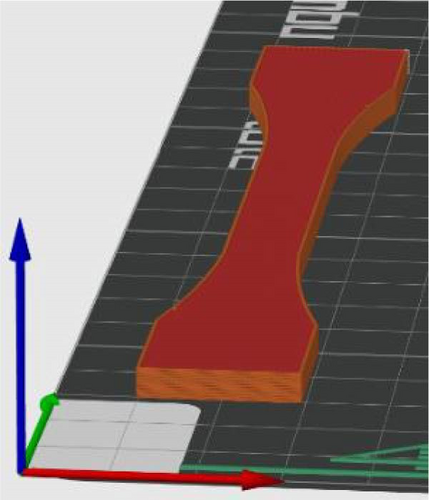
The dimensional errors of the machined parts were determined after measuring of the sample’s height with a Digimar CX2 Digital Height Gage, produced by Mahr GmbH, Gottingen, Germany. The length measuring device has a resolution of 0.001 mm and measuring error of (5 µm + L/300) [21]. To assure proper accuracy for the experimental data, we used replicates, and each sample was measured three times, and the average value was retained. The dimensional error was determined as the arithmetical difference between the determined average value and the nominal value.
The DIY equipment depicted in Figure 4 was employed to ascertain the tensile strength of the printed components. This equipment features specimen grips affixed to the cross-heads of the tensile testing device body for securing the samples. The drive system oversees the vertical motion of the moving cross-head, while sensors record both specific elongation and traction force. Subsequent to signal amplification by the amplifier, the measurement outcomes are transmitted to a computer through a data acquisition device and analysed using LabVIEW software.
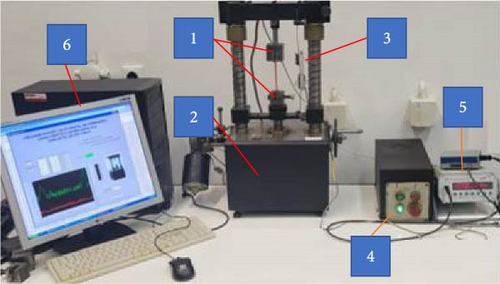
The 3D printed samples were subjected to heat treatment at a 60°C. Two different exposure times were used in the experimental runs 5 and 10 min. This low temperature was selected because of the relatively low melting point of the poly(ε-caprolactone) (PCL) polymers which served as polymer matrix for the investigated wood-based polymer. Also, the exposure time for the heat treatments was selected considering the fact that thermoplastic polymer composites require shorter heat treatment durations, and the temperature used was close to the crystallization temperature of the PLC, the polymeric matrix of the WPC tested. We also chose a short time expose to avoid the moisture of wood particles that would have softened the WPC material, affecting its mechanical properties. Short time exposures were selected to avoid the moisture of wood particles that would have softened the WPC material, affecting its mechanical properties.
The hardness of the parts was the tested according to ISO 868 : 200 with a digital Shore D hardness meter [23] (sharp cone point (SR 0.1 mm), 30° included angle, measuring range 0–100 HD, and a resolution of 0.5 HD). The measuring tests were repeated five times, and the mean value was considered.
Surface quality was studied by means of surface texture parameter Sz, also known as the maximum height. According to ISO 4,287 and ANSI/ASME B46.1, this parameter is used to quantify the vertical distance between the highest peak and the lowest valley within a specified sampling length on a surface profile. The importance of the Sz parameter lies in its ability to characterize the vertical extent of surface irregularities. In 3D printing and especially FDM processes, the resulting surface texture depends on how the melted material layers are deposited. The top surface and lateral surfaces of the parts will expose different surface textures. We included in the study the surface texture parameters for both surfaces. In order to increase the precision of the measurements, we used replicates and measured three different areas of the 3D printed part surfaces. After that, we determinate the average and used in the investigation. Sz, the maximum height of the micro-asperities surface roughness values, was determined with the Mahr CWM 100 confocal microscope and white light interferometer, produced by Mahr GmbH, Gottingen, Germany (Figure 5). The surface microscopic textures obtained were analysed with the specialized software Mahrsurf MfM software.

Table 3 presents the experimental conditions and results obtained in the study. The experimental data were statistically processed with a trial version of the DOE statistical software Minitab.
No exp. | Layer height, HL (mm) | Printing speed, s (mm/s) | Heat exposure time, t (min) | Top surface roughness, Sz (µm) | Lateral surface roughness, Szl (μm) | Shore D hardness (HD) | Dimensional error, ΔH (mm) | Ultimate strength, UTS (MPa) |
---|---|---|---|---|---|---|---|---|
1 | 0.2 | 200 | 0 | 645.45 | 574.49 | 68 | 0.08 | 64.37 |
2 | 5 | 226.37 | 525.62 | 68.4 | 0.09 | 49.84 | ||
3 | 10 | 188.63 | 510.46 | 69.3 | 0.10 | 54.37 | ||
4 | 250 | 0 | 1004.33 | 785.18 | 68.5 | 0.05 | 48.28 | |
5 | 5 | 263.14 | 459.1 | 68.6 | 0.17 | 47.34 | ||
6 | 10 | 206.87 | 462.7 | 69 | 0.11 | 38.28 | ||
7 | 300 | 0 | 766.80 | 641.21 | 69.2 | 0.10 | 15.16 | |
8 | 5 | 221.47 | 497.035 | 70.2 | 0.14 | 22.66 | ||
9 | 10 | 203.54 | 459.86 | 69.1 | 0.14 | 61.71 | ||
10 | 0.3 | 200 | 0 | 1027.40 | 535.42 | 65 | 0.23 | 51.87 |
11 | 5 | 455.74 | 523.45 | 65.3 | 0.34 | 44.06 | ||
12 | 10 | 399.82 | 477.35 | 65.5 | 0.32 | 40.62 | ||
13 | 250 | 0 | 894.96 | 653.143 | 65.5 | 0.30 | 35.78 | |
14 | 5 | 367.92 | 386.52 | 65.8 | 0.38 | 42.81 | ||
15 | 10 | 322.89 | 409.71 | 65.1 | 0.33 | 59.68 | ||
16 | 300 | 0 | 997.88 | 728.823 | 64.5 | 0.27 | 18.59 | |
17 | 5 | 321.02 | 492.38 | 64.3 | 0.51 | 41.56 | ||
18 | 10 | 304.99 | 573.99 | 64.3 | 0.36 | 34.22 | ||
19 | 0.4 | 200 | 0 | 1698.00 | 572.56 | 58.2 | 0.46 | 39.06 |
20 | 5 | 1015.78 | 519.615 | 58.3 | 0.49 | 37.34 | ||
21 | 10 | 918.86 | 456.42 | 58.4 | 0.55 | 35.31 | ||
22 | 250 | 0 | 1531.67 | 807.42 | 58 | 0.56 | 34.84 | |
23 | 5 | 937.00 | 611.14 | 59 | 0.51 | 38.59 | ||
24 | 10 | 895.14 | 507.705 | 59.25 | 0.50 | 35.62 | ||
25 | 300 | 0 | 1648.00 | 879.74 | 59.2 | 0.52 | 38.75 | |
26 | 5 | 1007.50 | 471.91 | 59.4 | 0.93 | 40.62 | ||
27 | 10 | 952.00 | 545.5 | 59.6 | 0.50 | 46.25 |
3. Results
Figure 6 presents the main effects plots and interaction plots. It can be observed that the heat treatment time exposure and the layer height are the most significant factors which influence the surface roughness parameter Rz for both surfaces investigated. The interactional plots obtained for the top surface roughness parameter investigated show that by applying heat treatment as post-process operation for the printed parts, the surface quality can be significantly improved. Also, for lower surface roughness, smaller layer heights should be selected. For the higher levels selected for the layer, height parameter over extrusion occurs causing an increase of the asperity’s height.
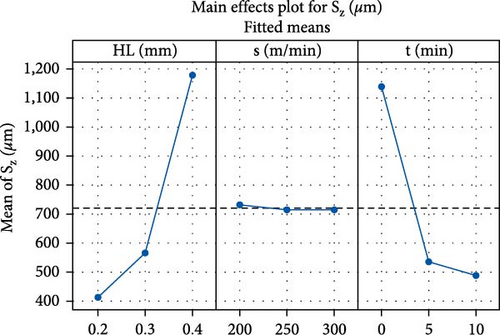
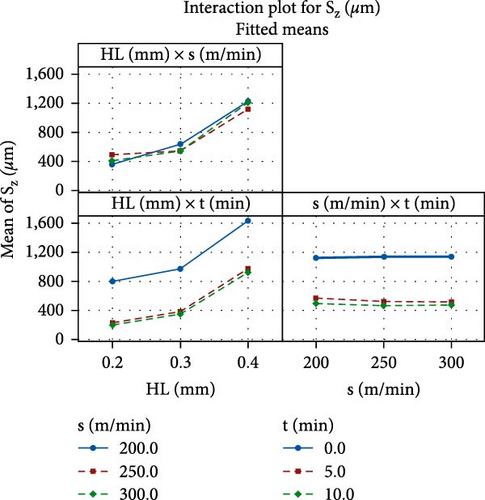
The printing speed had a more pronounced influence over the surface roughness of the lateral surfaces (Figure 7). The printing speed strongly influence the material flow rates and also the melting and layer bonding. The high Sz surface roughness parameter resulted for the 3D printing tests carried out with superior values of the printing speed which could be as result of the blobs that could be observed on these specific surfaces.
To summarize the influence exercised by each factor over the surface roughness, the investigated parameter created is shown in Table 4. The given table presents the trends (using the symbol ↑ for increase and ↓ for decrease) and the percentage with which the parameter varies from the average value with different levels of the input factors selected.
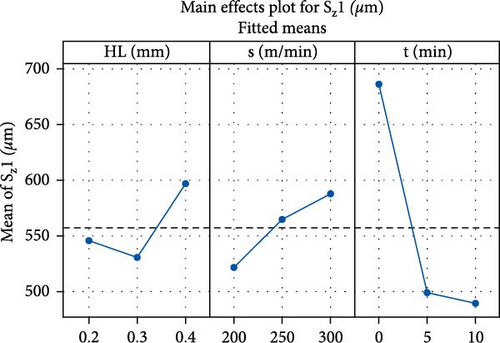
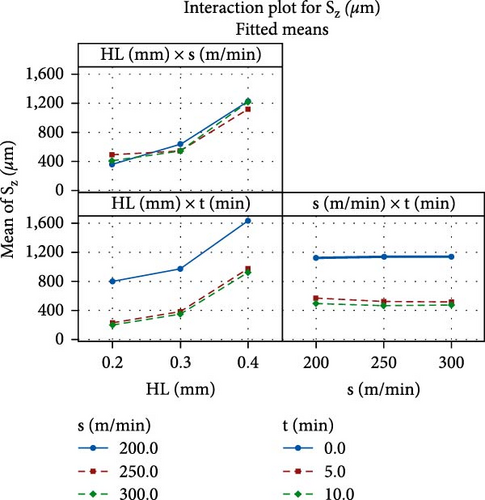
Factor | Level | ||
---|---|---|---|
Layer height, HL (mm) | Printing speed, s (mm/s) | Heat treatment time, t (min) | |
Top surface roughness | |||
1 | — | — | — |
2 | ↑26.82% | ↓2.37% | ↓112.1% |
3 | ↑51.97% | ↓0.01% | ↓9.63% |
Lateral surface roughness | |||
1 | — | — | — |
2 | ↓2.82% | ↑7.62% | ↓37.69% |
3 | ↑11.01% | ↑6.99% | ↓1.89% |
Figure 8 presents the main effects plots obtained for the Shore D hardness of the tested samples. The values obtained for the hardness fall in the range of 58–70.2 HD. As it can be seen, the printing speed and heat treatment exposure did not exert a significant influence over the printed part hardness. The layer height strongly influences the hardness of the parts and lower values of this parameter conduct to more dense structures and therefore to higher hardness. Also, because of the high asperities that resulted due to the over extrusion, the hardness measured for the parts printed with higher layer height and high speeds are significant lower.
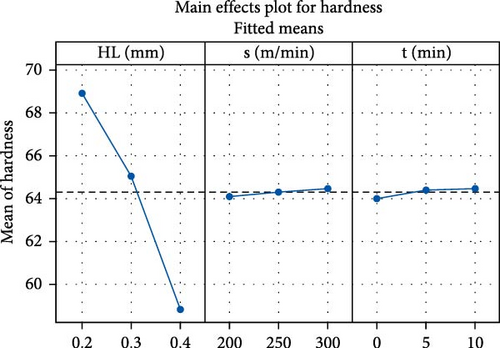
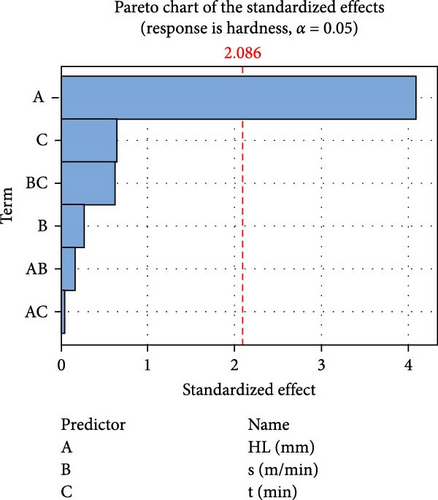
By analysing the variation graphs, a significant decrease of the surface hardness with 5.98% for the value of the layer height of 0.3 mm is observed, followed by decrease of 10.57% when the highest level of the layer height was used. As for the other two input factors considered in this investigation, the printing speed and heat treatment exposure time, they exposed almost negligible influence over the surface hardness. By increasing the printing speed and the heat exposure time the surface hardness slightly increases. The increase percentage for the printing speed parameter was of 0.34% for the medium level and of 0.69% for the highest level. As for the heat time exposure, an increase of 0.55% was obtained for the 5 min and a growth with 0.21% for the 10 min compared to the previous level.
The Pareto (Figure 8) plot shows that the cumulate influence between layer height–printing speed, printing speed–heat treatment time exposure, and layer height–heat treatment time exposure also does not expose significant influence on the investigated parameter.
Figure 9 presents the main effect plots for the dimensional error calculated for each of the 3D printed samples. The graphs show that the layer height exposes a more significant influence on the dimensional accuracy of the FDM machined parts than the other two variable factors considered. According to the main effects and interaction plots, better accuracies can be obtain if smaller layer height, lower printing speeds, and no heat treatment are considered. At higher layer heights and printing speeds, the pillowing effect was observed due to the improper thermal deformation of the filament (Figure 10).
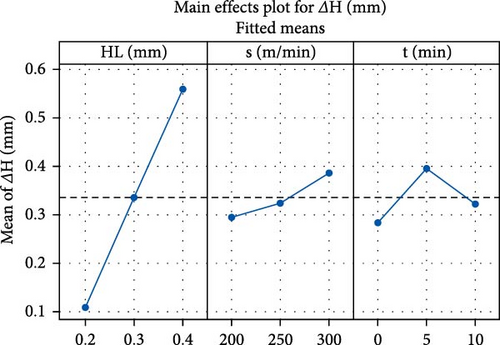
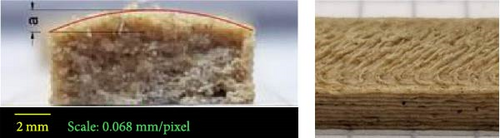
The heat treatments influence the dimensional accuracy of the WPC printed parts. It is well-known that wood tends to expand when it is exposed to high temperatures. This could explain why the height of the samples increased when subjected to the 5 min heat treatment exposure.
The dimensional error variations are similar with the ones obtained for the surface roughness parameter. It can be observed that the investigated parameter exposes a linear increasing tendency with the layer height factor variation by 67.68% for the medium level of the layer height followed by an increase of 40.19% for the layer height of 0.4 mm. These findings demonstrate the high influence exercised by the HL factor over the dimensional accuracy and the correlation between the surface roughness and dimensional accuracy.
The printing speed shows an increasing trend with a variation of 8.62% by increasing the speed from 200 to 250 mm/s, followed by an increase of 16.15% when speeds of 300 mm/s were used, compared to the previous level. For the case of thermal treatment, a total increase of 11.29% was observed.
The experimental results obtained for the ultimate strength of the FDM machined parts are similar with those presented in previous research that testes materials with semicrystalline structures similar with the PCL polymer, especially PLA. The UTS variations with the input factors have similar trends for the heat treatment influence [24, 25, 26, 27, 28, 29], as well as for the layer height [27, 30, 31, 32] and printing speed [33].
Figure 11 presents the main effect plots obtained for the ultimate tensile strength determined for the experimental samples. According to the graph’s aspect, all the three variable factors investigated expose a significant influence over the investigated parameter.
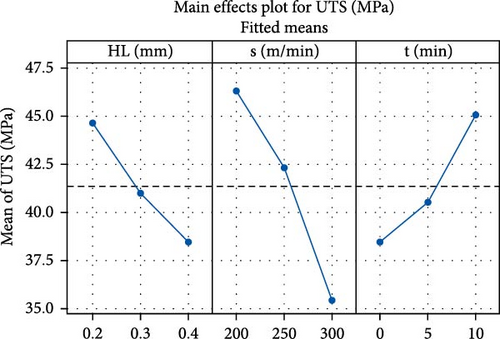
Better mechanical strength parts can be obtained by 3D printing with lower layer height and printing speed. Therefore, a linear decreasing tendency with the increase of the layer height parameter could be observed. A variation of 8.89% was registered for the 0.3 mm value of the layer height compared with the 0.2 mm level and of 6.58% for the 0.4 mm compared with the 0.3 mm level. This effect can be explained primarily by the aspects concluded by other researchers who studied the influence of HL on the mechanical properties of materials with a semicrystalline structure. Low values of UTS at higher HL may be due to the plasticization and unfavourable bonding of the layers [32], and in the case of lower values of HL, the phenomenon of reheating of the previously deposited layer occurs, an aspect that facilitates the adhesion of one of the layers [34, 35]. However, for the present case, an additional aspect can be considered for which decreasing trends are recorded through the increase of HL. As observed previously, the roughness of the surfaces increases considerably by increasing HL, an aspect that can also be observed in Figures 6 and 12.
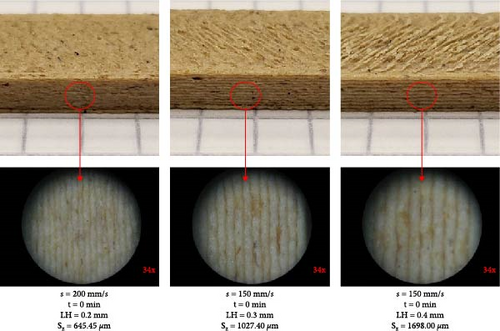
Considering that the samples were manufactured with 100% infill, it can be considered that each deposited layer exhibits the same behaviour and has the appearance of over extrusion phenomena.
These aspects are more pronounced when higher printing speeds are used. The high printing speeds affect the material flow. The filament is not properly heated, and therefore, it is not properly squished into the printed layers resulting in a pillowing effect. The asperities are formed because the nozzle drags through it pulling the material along the printing paths. The high asperities caused by the over extrusion have a strong influence on the voids between layers resulting in lower values of UTS for higher layer heights. Moreover, the same aspect influences the height dimensional error measured for the printed samples.
Printing speeds strongly influence the way in which the material is melted and deposited into the printing layers. When higher printing speeds are used the melting time of the filament, the cooling time of the deposit layer is reduced affecting the uniformity and bonding between layers. The bonding between layers seems to improve for the heat-treated parts. As a result, the heat-treated parts exposed lower value of the maximum height roughness parameter, Rz and increase tensile strength values. According to the microscopic images of the lateral surface of the 3D printed parts, the dispersion of fibres in the polymeric matrixes is more uniform for the parts printed at higher speeds (Figure 13). When lower speeds are used, because the filament spends more time in the heating chamber of the extruder, the wood fibre is released from the polymeric matrices and that is why the parts printed at lower speeds expose fibre clusters.
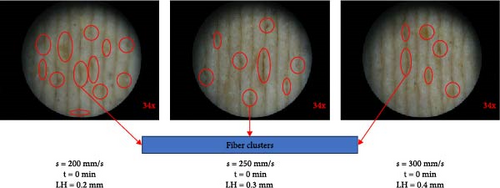
These specific aspects were also observed for the heat-treated parts. The presence of fibre clusters may be the cause of the higher tensile strength obtained for the parts printed with lower printing speeds and subjected to higher heat treatment exposure time. Furthermore, as with the layer height variation, increasing the printing speed causes a pillowing effect, resulting in air voids between layers. These aspects can also be observed even on the microscope images of the fractured surfaces of the parts printed with the higher value chosen for the layer height parameter (Figure 14).
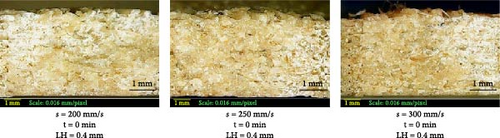
The results show a large variation of 9.34% when increasing the printing speed to 250 mm/s from 200 mm/s and 30.46% when increasing the speed to 300 mm/s from 200 mm/s.
The heat treatment exposure time has a positive influence over the strength of the 3D wood-based polymer parts. For this case, a 14.62% improvement in UTS was observed when heat-treated for 10 min compared to the results obtained for non-heat-treated specimens. This can be explained by the fact that the PCL binder of the filament has a semi-crystalline structure, and the UTS behaviour relative to heat treatment is like that of polylactic acid, variations also shown in other studies [31, 36]. For the present case, it can also be considered that by applying heat treatment, the PCL binder softens and penetrates between the biodegradable fibres, thus reducing the voids in the structure of the non-heat-treated specimens. This can also be seen in the images recorded using the MahrCWM100 confocal microscope (Figure 15). In the figure by increasing the duration of the heat treatment, the top layer surface becomes smoother, and a better roughness is obtained.
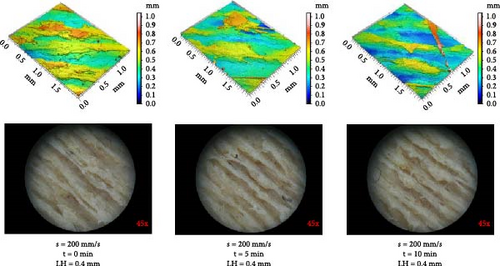
The presented aspects are also confirmed by the ANOVA analysis that was carried on. According to the Pareto graph obtained from the analysis (Figure 16), it was found that the statistically significant factors (p value < 0.05) are the printing speed with a significance of 52.76%, followed by the layer height with a significance of 25.17%, and finally, the less significant factor, the duration of heat treatment with a significance level of 22.07%.
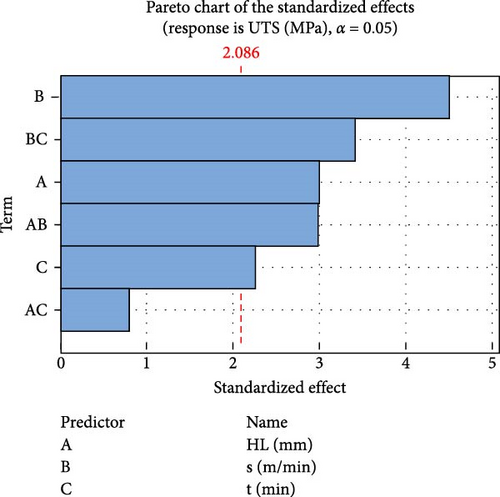
- (1)
For the top surface roughness (coefficient of determination r2 = 0.888):
(1) - (2)
For the lateral surface roughness (coefficient of determination r2 = 0.682:
(2) - (3)
For the Shore D hardness (coefficient of determination r2 = 0.943):
(3)
The coefficient of determination, commonly known as R-squared (R2), is a statistical parameter that represents the proportion of the variance in the dependent variable that is explained by the independent variables in a non-linear regression model. The R2 value ranges from 0 to 1; the 0 value indicates that the model does not explain any of the variability in the dependent variable.
By examining the mathematical empirical regression corresponding to the top surface Sz roughness parameter, it could be seen that better surface finishing for lower values of the layer height. Also, the values of Sz will slightly decrease if higher values of the printing speed and increase heat exposure time are considered. On the other hand, the empirical equation obtained for the Sz parameter measured on the lateral side of the printed part the printing speed expose a the most pronounced influence over the examined parameter compared to the rest of the input factors investigated, having the higher value of the correspondent exponent. The layer height also has a significant influence over the surface finish parameter investigated. It should be noted that by increasing the value of the printing speed, the hardness of the part will slightly increase. The hardness of the printing part will decrease for higher values of the layer height. These is because with lower values of the layer height, more cohesive and well-bonded structures are obtained in 3D printing and therefore superior hardness. Overall, the heat treatment even if it does not expose a significant impact over the investigated parameters, it shows a good influence on the surface finish and part hardness.
4. Conclusion
Limited investigations have been conducted to assess the capabilities of wood biopolymer composites, with a majority focusing solely on the mechanical properties of wood polymer composites. This current study delves into the impact of layer height, printing speed, and heat treatment time exposure on the surface quality, tensile performance, and dimensional accuracy of parts fabricated through FDM using Rosa3D Biowood filament. Rosa3D’s Biowood is a wood-based composite biopolymer formed by blending wood fibres into a PCL and polyester polymeric matrix. Additionally, fillers such as starch and lignin, along with additives like natural resins, waxes, oils, and natural fatty acids, are incorporated into the mixture.
The novelty of this study consists in exploring some of the qualitative aspects—surface roughness on upper and lateral surface, dimensional accuracy, hardness, and tensile strength of the PCL wood-based biopolymer parts generated by FDM. The study presents the possibility of applying heat treatment on WPC printed parts and analyses the impact of it on some of the part proprieties. The printing parameters varied in the experimental study were the layer height, the printing speed, and heat treatment time exposure. The printing speed levels used in the experiment test runs were significantly higher than those usually tested in previous research in this field or those recommended by the filament producer.
Among the input factors selected for this investigation, the height set for the deposit layers had the most significant influence on the investigated parameters variations. Higher values of these parameter dramatically affect the surface roughness, hardness dimensional error, and ultimate strength of WPC printed parts.
The printing speed levels used in the experiments did not have significant influence on all the investigated parameters. The surface roughness of the 3D parts printed with the highest level chosen for the printing speed factor had an increase of only 2.38% for the top surfaces and of 14.61% for the lateral surfaces. By increasing the printing speed parameter, the surface hardness registered an increase of 0.34% for the medium level and of 0.69% for the highest level. The printing speed had the highest influence over the ultimate strength parameter. The results show a large variation of 9.34% when increasing the printing speed to 250 mm/s from 200 mm/s and 30.46% and when increasing the speed to 300 mm/s from 200 mm/s.
The heat treatment applied to the wood-based biopolymer parts had a significant influence over the surface quality and dimensional accuracy. Even if the heat treatment did not have a significant influence over the surface hardness, it did, however, a considerably positive influence on the mechanical strength. For this case, a 14.62% improvement in UTS was observed when heat-treated for 10 min compared to the results obtained for non-heat-treated specimens.
- (i)
The impact of layer height, printing speed, and heat treatment time exposure on surface quality, tensile performance, and dimensional accuracy of parts fabricated through FDM using Rosa3D Biowood filament were investigated.
- (ii)
Qualitative aspects such as surface roughness, dimensional accuracy, hardness, and tensile strength of PCL wood-based biopolymer parts generated by FDM were explored, contributing to the understanding of wood biopolymer composite manufacturing and mechanical behaviour.
- (iii)
The possibility of applying heat treatment on WPC printed parts was presented and analysed its impact on surface quality and mechanical strength, providing insights into post-processing techniques for improving part properties.
- (iv)
Layer height was identified as the most influential factor on surface roughness, hardness, dimensional error, and ultimate strength of WPC printed parts, highlighting the importance of optimizing this parameter for desired part characteristics.
- (v)
Printing speeds used did not significantly influence all investigated parameters but had the highest impact on ultimate strength, with notable variations observed with increasing printing speeds.
- (vi)
The significant positive influence of heat treatment on mechanical strength, with a 14.62% improvement in ultimate tensile strength observed after heat treatment for 10 min, indicating the potential for enhancing part performance through this type of post-processing techniques.
Conflicts of Interest
The authors have no relevant financial or non-financial interests to disclose.
Authors’ Contributions
All authors contributed to the study conception and design. Material preparation, data collection, and analysis were performed by Irina Beșliu-Băncescu and Ioan Tamașag. The first draft of the manuscript was written by Irina Beșliu-Băncescu, and all authors commented on previous versions of the manuscript. All authors read and approved the final manuscript.
Open Research
Data Availability
The experimental data used to support the findings of this study are included within the article.