Taguchi-Based Artificial Neural Network Modeling of Friction Process on Aluminum Alloy Reinforced with SiC Nanoparticles
Abstract
Nowadays, the aluminum metal matrix composites (AMCs) play an empirical role to improve the mechanical performance by various applications. Therefore, the secondary processes need to enhance the surface morphology of intermetallic phases with the appropriate reinforcing particles. In this research, Al7075- and ceramic-based nanosilicon carbide (SiC) were utilized to compose the metal matrix composites. These composites were subjected to friction welding for intermetallic surface modification with the various forging pressure and rotating speed. Initially, the AMCs were prepared with three (8–12) kinds of SiC weight proportions by the design of Taguchi L9 orthogonal array. As per the weight proportions, nine samples were prepared and then conducted the friction welding with 10–20 MPa of forge pressure and 1,650–2,050 rpm of rotational speed of spindle. Then, the entire nine specimens were allowed to conduct the tensile and microhardness test. During the mechanical test, the overall welded zone had higher mechanical properties than the base metal. Then, the artificial neural network was utilized to predict the output responses as per the designed concept of trial and error method. The overall predicted responses are nearly closed to the experimental values.
1. Introduction
The aluminum metal matrix composites (AMCs) possess various properties that contain maximum precise potency, lesser in weight, stipulate for better performance, and constancy for maximum strength in different manufacturing utilization [1]. The importance of AMCs shows improved mechanical strength without changing the structure load. At the same time, enhanced wear rates and corrosion behavior are added advantages [2]. Therefore, the AMCs reached these properties based on the lightweight structures. From the oxide-based materials to carbides with various influencing factors of nanoceramic particles, it is predictably strengthened with ceramic particles to produce the aluminum matrix composites [3]. Even if the process characteristics are also very significant for producing the AMCs and therefore stir casting process is utilized for composing the metal matrix composites [4]. Moreover, all the nano-based ceramic particles are not easily wetted on the aluminum alloy and need some extra methods to develop the wetting process during the process [5].
During the tensile applications, the reinforced nanoceramics are not sufficiently plasticized to deform results in increasing the brittleness and reducing the toughness. In the present tendency of metal matrix composites, composing was much complicated due to the wetting condition in the surface region with presence of wrinkle when reinforced with ceramic powders [6]. The detrimental strain was created among the base matrix and nanoceramic reinforcements, which affect the thermal properties. Initially, the wetting condition of aluminum alloy is much better when mingled with nanoceramic materials; therefore, the variations of densities and thermal expansion might be changed between them. Then, the enriched intermetallic surfaces are accomplished with enhanced thermal equilibrium with liquefied aluminum [7]. The proper selection of ceramic reinforcement particles achieves better potential in the composed AMCs and made the interfacial bonding much developed. While considering the intermetallic regions, the silicon carbide (SiC) ceramic reinforcement is considered as a feasible strengthening material for aluminum metal matrix composites phases [8]. The processed AMCs with SiC reinforcements were made by various melting processing methods and its properties and characterizations were recognized with following reviews [9]. During the process, the SiC particles scattered evenly in the matrix of aluminum; meanwhile, some discarded issues like pores defect, isolation in the grain boundary region, and highly agglomerated particles were identified. The SiC enhances the ductility strength, wear rates, and hardness in the processed AMCs-Al/SiC. The scattering among the SiC and aluminum enhances the mechanical properties but the secondary methods are needed to improve the homogeneous dispersion of SiC in the aluminum; therefore, conventional method was initiated to developing that but the effective outcomes are not generated for improving the surface morphologies [10]. Hence, this research was highly focused to improve the tensile and hardness by the emerging technique; that is why, the friction welding was applied on the processed AMCs to produce the better refinement in the intermetallic surface materials. By the action of axial force from one rotatable material to the fixed material, it creates the friction and sufficient heat was attained with selected rotational speed.
Banerjee et al. [11] studied the friction welded between the 316 and A516 steel with variation of forge pressure and sustained spinning speed. The Taguchi design planned the process parameters and the entire welded specimens achieved better mechanical characteristics. The tensile and hardness properties of nugget zone were higher than the parent metal. Zhang et al. [12] composed the friction welding between the Al and steel to applications of high-level torque generated by the friction. The intermetallic layer was achieved with well-bonding structure and it led to improve the mechanical properties. Choi et al. [13] utilized the AA7050 for conducting the linear friction welding process. The welded zones of mechanical properties and micrographs achieved higher than the parent metal. The intermetallic layers were achieved at the maximum proportions of Mg and Zn phases. Lu et al. [14] investigated the mechanical properties against the friction-welded specimens of high-entropy alloys. In this research, all the welded zones were investigated properly. The tensile potency and hardness properties were improved in the nugget zone and much lesser than the base material. The micrographs revealed that the welded area exhibits the superior mechanical properties. Thakur and Patel [15] investigated the solid-state joining process on the two different polymers with varying the diameter of the specimens. The following input parameters are spinning speed, friction pressure, and butt of length, respectively. The dissimilar welded was occurred in the friction welding process and all the nugget zones were attained superior mechanical properties than the base material.
So far in the detailed literatures, most of the materials selected by the researchers are very familiar and available materials. There are various casting samples conducted to produce the AMCs with their reinforcements are titanium diboride, aluminum oxide, titanium carbide, aluminum titanium, and silicon nitride. The AMCs specimens were not yet analyzed detailed by the friction welding process. At the same time, friction welding parameters do not analyze with Taguchi-based artificial neural network (ANN) methods. The input parameters are friction pressure, various nano-SiC proportions, and rotational speed, and the output responses are tensile strength and hardness, respectively. The experimental outline is shown in Figure 1.
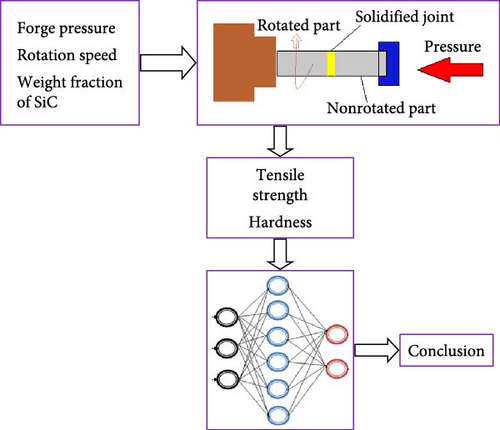
2. Materials and Methods
In this study, Al7075 as a base matrix aluminum alloy was used for stir casting process to make a metal matrix composites. The suitable ceramic nano-SiC with 10 µm was utilized by stir casting technique. The chemical properties of Al7075 percentages are 0.2 of Ti, 0.28 of Zn, 0.3 of Mn, 0.4 of Si, 0.5 of Fe, 2.0 of Cu, 2.9 of Mg, 6.1 of Zn, and balance of aluminum, respectively. The mechanical characteristics of base matrix are 140, 282, and 210 MPa of hardness, tensile strength, and yield strength, respectively [16]. Normally, the SiC possesses maximum thermal stability, greater hardness strength, and lesser density as reinforcement particles. During the stir casting process, the necessity of Al7075 was placed into the crucible furnace with graphite made by the ingot amount. The maintained temperature of stir casting process was 875°C under the furnace for preheating and meanwhile the nanoceramic particle SiC was placed into the furnace of molten matrix base material [17]. The composite slurry was maintained at 20 min for stirring speed at 400 rpm, respectively. Then, the melted composites were taken out from the casting machine and discharged into the prepared mold with preheat condition at room temperature. In this research, 25 mm diameter cylindrical mold was utilized to shape the composites.
As per the required shapes, 25 mm diameter rod with 150 mm length was approached to the friction welding. The friction welding was employed with MTI-made machine with rotary function mode [10]. Various researchers reported that the rotational speed and forge pressure extensively influence mechanical and microstructure characteristics. At the same time, strengthened particle variations on the base alloy were not findings; therefore, this investigation concentrates on one more addition to enhance the properties with the addition of nanoceramic particle (SiC) [18]. Based on the casting process, all the samples were made with SiC reinforcements with maintained parameters of stirring speed and time duration. In this research, Taguchi design utilized to arrange all input parameters like different proportions of SiC (10–14 wt%) and prepared with L9 orthogonal array [19]. At the same time, all the nine samples were achieved with increasing SiC to 2 wt%, respectively. After that, nine processed AMCs specimens were utilized to the friction welding as earlier mentioned in input parameters [20]. The input parameters of friction welding are rotational speed (1,650, 1,850, and 2,050 rpm) and the forge pressure (10–20 MPa), respectively.
The Taguchi-based L9 array with input parameter levels is shown in Table 1. The output responses like tensile and hardness were considered as an outcome for this investigation [21]. During the experimentation, tensile test was conducted with respective diameters like 6 mm of length and gauge diameter of 20 mm with sustained rate of strain is 0.003/s, respectively [22]. The hardness was employed with G5 Vickers hardness machine having the 250 gf with 14 s dwell time by the impression of diamond Vickers indenter shaped. Table 2 shows the casting and friction welding parameters with expanded level.
Input no. | Input parameters for L9 | 1 | 2 | 3 |
---|---|---|---|---|
1 | Nano-SiC | 10 | 12 | 14 |
2 | Spindle rotational speed (rpm) | 1,650 | 1,850 | 2,050 |
3 | Forge pressure (MPa) | 10 | 15 | 20 |
Sr. no. | Nano-SiC (wt%) | Spindle speed (rpm) | Forge pressure (MPa) |
---|---|---|---|
1 | 10 | 1,650 | 10 |
2 | 10 | 1,850 | 15 |
3 | 10 | 2,050 | 20 |
4 | 12 | 1,650 | 15 |
5 | 12 | 1,850 | 20 |
6 | 12 | 2,050 | 10 |
7 | 14 | 1,650 | 20 |
8 | 14 | 1,850 | 10 |
9 | 14 | 2,050 | 15 |
3. Results and Discussion
In this research, the inertia friction welding was conducted to produce all the welded samples. The friction welding is solid-state joining technique to compose the similar weld by the stir-casted Al/SiC metal matrix composites. During the process, the initial heat was generated by rubbing the action between the rounded composites rod [23]. At the same time, shear stress was initiated to make the plastic deformation process between two rods and the weld was started to make the shape as weldment. The friction welding was primarily approached to stimulate the grain refinement at the interlayer among the two similar composites rod. The joined composite specimens were achieved to develop the mechanical characteristics due to the rotational and immovable parts [24]. Because of the generation of frictional heat, it led to improve the weldment by strain rate on the composites during the friction welding which was much higher than the other traditional mechanical process. Friction welding is a prominent method to compose the greater refinement of grain structure in the nugget region [25]. As per the design of Taguchi L9 orthogonal array, all the specimens were composed by the friction welding. The outcomes of welded joints like tensile strength and hardness were listed in Taguchi table (Table 3).
Sr. no. | Nano-SiC (wt%) | Spindle speed (rpm) | Forge pressure (MPa) | Tensile strength (MPa) | Hardness |
---|---|---|---|---|---|
1 | 10 | 1,650 | 10 | 292 | 154 |
2 | 10 | 1,850 | 15 | 271 | 153 |
3 | 10 | 2,050 | 20 | 336 | 155 |
4 | 12 | 1,650 | 15 | 274 | 159 |
5 | 12 | 1,850 | 20 | 310 | 150 |
6 | 12 | 2,050 | 10 | 277 | 152 |
7 | 14 | 1,650 | 20 | 278 | 151 |
8 | 14 | 1,850 | 10 | 254 | 150 |
9 | 14 | 2,050 | 15 | 307 | 156 |
As shown in Table 3, it is clearly understood that the tensile and hardness of the welded specimens achieved better values than the base metal. Particularly, the specimen five incorporates maximum 12 wt% of SiC, 1,850 rpm of spindle speed, and 20 MPa of forge pressure composed samples procures the greater mechanical properties. It is revealed that the increase of strengthened particles from 10 to 12 is the major reason to achieve this level. Eight samples performed mechanical properties, and the optimum parameters were 14 wt% of SiC, 1,850 rpm of rotational speed, and 10 MPa of forge pressure. Increasing the SiC wt% and low forge pressure at 10 MPa generate lesser heat due to the maximum SiC on the alloy. It has reduced the friction range, and results show a decrease in tensile properties. Figure 2 shows the friction-welded composite specimens with their tensile properties, and it is revealed that the specimen four composed the better tensile strength. Figure 3 shows the welded specimen and hardness properties of the composites specimen. The microhardness values are measured from various welded zones like nugget zone, thermomechanically affected zone (TMAZ) and heat affected zone (HAZ), and base metal region. From the zones, all the nugget values achieved higher hardness than other remaining zones. The average hardness values of all the welded zone regions are shown in Table 4.
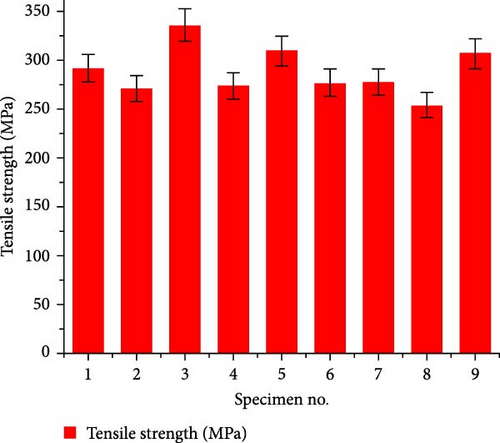
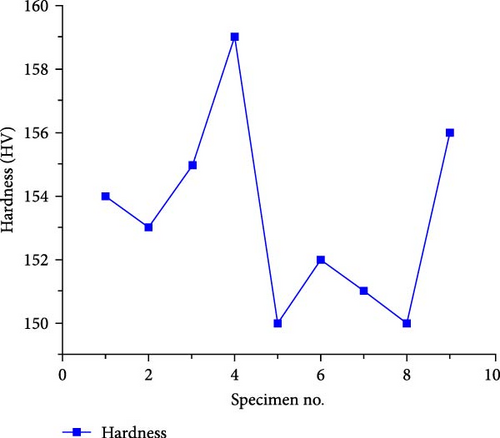
L9 | PM | HAZ | TMAZ | NZ | TMAZ | HAZ | PM |
---|---|---|---|---|---|---|---|
1 | 140.641 | 142.641 | 149.641 | 154 | 149.715 | 143.715 | 141.614 |
2 | 139.641 | 141.641 | 148.641 | 153 | 148.715 | 142.715 | 140.614 |
3 | 141.641 | 143.641 | 150.641 | 155 | 150.715 | 144.715 | 142.614 |
4 | 145.641 | 147.641 | 154.641 | 159 | 154.715 | 148.715 | 146.614 |
5 | 136.641 | 138.641 | 145.641 | 150 | 145.715 | 139.715 | 137.614 |
6 | 138.641 | 140.641 | 147.641 | 152 | 147.715 | 141.715 | 139.614 |
7 | 137.641 | 139.641 | 146.641 | 151 | 146.715 | 140.715 | 138.614 |
8 | 136.641 | 138.641 | 145.641 | 150 | 145.715 | 139.715 | 137.614 |
9 | 142.641 | 144.641 | 151.641 | 156 | 151.715 | 145.715 | 143.614 |
- HAZ, heat affected zone; TMAZ, thermomechanically affected zone.
4. Artificial Neural Network for Predicting the Tensile and Hardness
The ANN was approached to identify the complex issues in the production sectors. This technique was very helpful to achieve the predicted values of the respected outcomes very efficiently. TRAINLM mode was utilized to train the model in the first come basis methods and learning algorithm was also used to predict the output responses. The Levenberg–Marquardt method is one of the optimization in this neural network technique. This method was also similar to the human brain of their neuron systems. The trial and error method was employed to identify the responses with the help of feedforward and backpropagation algorithm. In this approach, three inputs, three hidden layers, and two outcomes were arranged for ANN predicted responses. From the Taguchi technique, the prepared output responses are tabulated with ANN with the predicted values. Table 5 exhibits the ANN predicted values of the output responses with their input parameters. The ANN model of input layers and output layers, as shown in Figures 4–6, shows the ANN predicted values of tensile and hardness properties. R-Seq value was observed as 0.96.
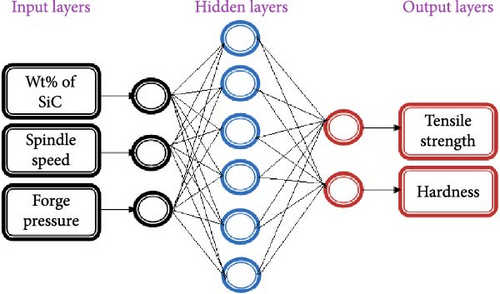
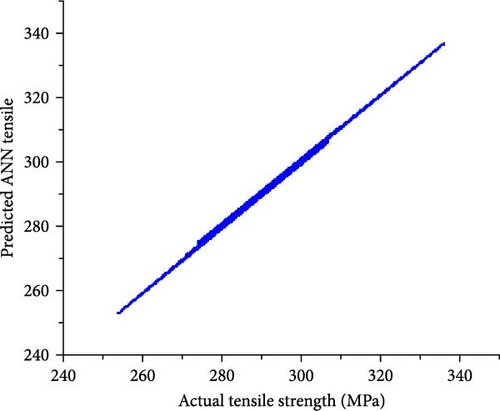
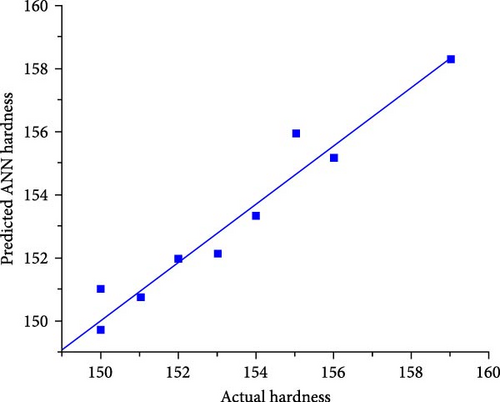
Sr. no. | Nano-SiC (wt%) | Spindle speed (rpm) | Forge pressure (MPa) | Tensile strength (MPa) | Predicted ANN tensile | Hardness | Predicted ANN hardness |
---|---|---|---|---|---|---|---|
1 | 10 | 1,650 | 10 | 292 | 292.156 | 154 | 153.369 |
2 | 10 | 1,850 | 15 | 271 | 270.986 | 153 | 152.145 |
3 | 10 | 2,050 | 20 | 336 | 336.524 | 155 | 155.962 |
4 | 12 | 1,650 | 15 | 274 | 275.010 | 159 | 158.335 |
5 | 12 | 1,850 | 20 | 310 | 310.952 | 150 | 151.018 |
6 | 12 | 2,050 | 10 | 277 | 276.548 | 152 | 151.986 |
7 | 14 | 1,650 | 20 | 278 | 277.852 | 151 | 150.743 |
8 | 14 | 1,850 | 10 | 254 | 253.215 | 150 | 149.731 |
9 | 14 | 2,050 | 15 | 307 | 306.169 | 156 | 155.193 |
5. Conclusion
- (1)
In this research, Al7075 with nanoparticles of SiC was successfully produced by the stir casting process.
- (2)
The processed AMCs samples were subjected by the friction stir welding with respective forge pressure and spindle speed.
- (3)
The input parameters like various weight proportions of nano-SiC, forge pressure, and spindle rotation speed were successfully designed with Taguchi L9 orthogonal array.
- (4)
The overall nine friction-welded specimens achieved better tensile and hardness than the base metal. Especially, the hardness on the welded zones like TMAZ, HAZ, and parent metal gets less hardness than the nugget region.
- (5)
The 12 wt% of SiC, 1,850 rpm of spindle speed, and 20 MPa of forge pressure composed samples that procure the greater mechanical properties.
- (6)
The least mechanical properties were achieved by the sample eight, and the parameters are 14 wt% of SiC, 1,850 rpm of rotational speed, and 10 MPa of forge pressure.
Conflicts of Interest
The authors declare that they have no conflicts of interest.
Open Research
Data Availability
The data used to support the findings of this study are included within the article. Should further data or information be required, these are available from the corresponding author upon request.