Intelligent Identification and Construction System of Prefabricated Tunnel Structure Based on BIM Technology
Abstract
In order to make up for the problems of low production efficiency, high labor cost, serious environmental pollution, and low degree of informatization of traditional tunnel construction method, an intelligent identification building system of prefabricated tunnel structure is proposed. Based on BIM Technology and integrating advanced concepts and technologies in the construction industry and management field, an intelligent construction system of prefabricated tunnel structure based on BIM is proposed, the characteristics, functions, and values of each component are introduced, and the overall architecture of the system is established, which can provide technical support for the whole life cycle construction, operation, and maintenance of prefabricated railway tunnel. Only 68% of architectural designers know BIM Technology, while only 4% of designers really use or are using BIM Technology to participate in prefabricated architectural design. Through this research, the use frequency of BIM can be greatly increased and work efficiency can be improved. To meet the requirements of railway tunnel construction for intelligent construction in the new era, the new technology and new ideas also lead the further scientific and technological innovation in tunnel engineering to a certain extent, which meets the actual needs of the development of intelligent railway construction technology and has a practical significance of improving quality and efficiency.
1. Introduction
At present, great progress has been made in the tunnel construction in China, but railway tunnel construction is prioritized along with construction technology as drilling and blasting method, construction step sequence, support, safety assurance, quality control, difficulty in quality control, slow and low efficiency shortcomings, degree of mechanization, and informationization with the European and American developed countries have a certain gap. BIM Technology is based on the development of three-dimensional digital technology. It integrates the engineering data model information used in construction projects so as to completely express all the information in engineering projects. Using computer software to do the whole project into a three-dimensional model, we can more intuitively control the project construction management and project operation and design and even analyze and simulate the construction cycle to generate construction drawings and quantities calculation tables. Therefore, BIM Technology is also a process of managing, controlling, and collecting information [1]. Therefore, various types of prefabricated base structures and stability calculation methods are proposed, design parameters are calculated and construction technology is developed, a theoretical analysis system for prefabricated structures at the bottom of railway tunnels is established, and intelligent assembly machinery and equipment are developed. Prefabricated tunnel intelligent identification construction system represents a new tunnel construction mode (Figure 1), and its railway engineering practice under construction has been carried out. The characteristics of standardized, customized, and batch-fabricated structure can more effectively connect the manufacturing, construction, design, construction and operation, and maintenance units in series. Compared with the traditional tunnel construction method, it has natural advantages in informatization and mechanization. With the rapid development of the economy and the rapid improvement of the urbanization level, the construction industry plays an important role in the economy. However, as one of the pillar industries of the economy, the construction industry still has many disadvantages. The traditional extensive construction mode is faced with the problems of low production efficiency, high labor cost, serious environmental pollution, and low degree of informatization, which brings many problems to environmental protection. The development of prefabricated buildings is an effective way to promote building industrialization and building informatization [2]. Prefabricated building is a building supported by informatization and through standardized design, lean production, and site assembly. Compared with traditional buildings, it has the characteristics of design integration, coordination, dry construction and refinement in design, construction, decoration, acceptance, and management.
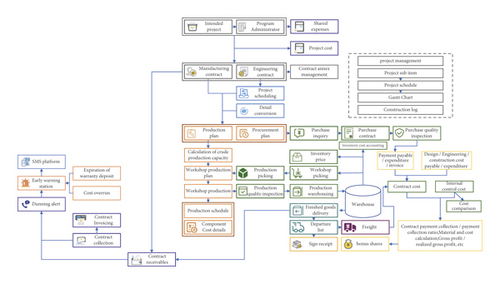
For more than the actual demand put forward based on the lightweight BIM, the RFID technology and the depth of the ERP system integration of prefabricated in the whole life cycle of tunnel structure of intelligent building system meet the railway tunnel construction in the new period to the requirement of intelligent building, new technology, new ideas, and, to a certain extent, further technological innovation, leading the tunnel engineering. In line with the actual demand for the development of intelligent railway construction technology, it has the practical significance of improving quality and efficiency.
2. Literature Review
Lin and others believed that the tunnel construction has made great progress at present, but the railway tunnel construction is mainly based on the drilling and blasting construction technology, which has the disadvantages of many construction steps, untimely support closure, difficult safety assurance, difficult quality control, slow progress, and low work efficiency, and the degree of mechanization and informatization is slightly low [3]. Zhang et al. and others said that compared with the existing technology, the prefabricated tunnel structure has the advantages of a short construction period, convenient construction, high quality, environmental protection, and easy cost control. Its characteristics of standardized design, industrialized production, prefabricated construction, intelligent management, and professional cooperation can meet the higher requirements of railway tunnel construction [4]. Sun et al. and others said that as a new tunnel structure, prefabricated prefabrication has gradually attracted the attention of the engineering community [5]. Cao et al. and others have proposed various types of prefabricated base structures through a number of scientific research, given stability calculation methods, design parameters, and construction technology, discussed the applicable conditions and stability maintenance technology of different types of prefabricated structures at the bottom of tunnel, established the theoretical analysis system of prefabricated structures at the bottom of the railway tunnel, and developed intelligent assembly machinery and equipment [6]. Liu et al. and others said that different from the tunnel excavated by shield method or TBM method, the prefabricated railway tunnel is a new structural system in which the tunnel arch wall, underrail structure, and trench cover plate are prefabricated and installed in blocks, and the key joint components are reliably connected [7]. Tong et al. and others believe that the development of new prefabricated tunnel structure is a major reform of tunnel construction mode. It is a new tunnel structure system through industrialized prefabricated components, mechanized process assembly, professional construction, and information system management technology [8]. Yuan et al. and others believe that this technology can effectively reduce process cost and improve production efficiency and construction safety [9]. According to the investigation of Zhaoping and others, at present, the prefabricated construction technology of railway tunnel has gradually carried out engineering practice, but the existing production mode of prefabricated PC components is relatively backward, and the information management level of the whole industrial chain of prefabricated construction is low [10]. Huang et al. and others said that the existing research results have not been deeply and systematically studied on the manufacturing, transportation, assembly, monitoring, and detection of prefabricated tunnel structure [11]. Fitzgerald et al. and others believed that the whole life cycle of intelligent identification and construction system architecture of prefabricated tunnel structure based on BIM Technology to realize design, construction, and assembly simulation and process progress management and visual monitoring measurement can cover the standardized prefabricated railway tunnel management, production, and design modes of management, construction, design, and construction units and practice tunnel intelligent construction to the greatest extent [12]. Kaplan et al. believed that the integrated information management platform of tunnel construction period based on lightweight BIM can access all kinds of information collected by RFID technology through system expansion, interface standardized management, and entity definition and at the same time integrate with ERP management system and display on the same platform [13].
3. Method
3.1. Intelligent Construction Architecture of Prefabricated Buildings Based on BIM
Prefabricated buildings refer to buildings assembled on-site with factory-produced prefabricated components. In terms of structural form, prefabricated concrete structures, steel structures, and wood structures can all be called prefabricated buildings, which are important for industrialized buildings. Component: the advantage of this kind of building is that the construction speed is fast, and it is less restricted by climatic conditions, which can save labor and improve the construction quality. Prefabricated building is a complex industrial product, which requires design standardization, production industrialization, construction assembly, and electromechanical decoration integration so as to drive the “five in one” building of all participants in the whole life cycle of prefabricated building with informatization. Smart construction is to realize interconnection and remote sharing of materials, equipment, personnel, and other management objects under construction with the help of the Internet of things and BIM Technology, complete the information management of the whole life cycle through information mapping, digital construction, intelligent detection, and other means, build an intelligent construction system of prefabricated buildings based on BIM, make full use of various information technologies and network technologies, and gather the information in the whole life cycle of prefabricated buildings on the same information platform. In order to facilitate the project participants to timely understand and share project-related information through the information platform during the whole life cycle of assembled buildings, so as to realize the timely flow of project information and project decision-making [14]. In order to realize the information management of design, production, and assembly of prefabricated building components, we need a unified coordination platform based on BIM to integrate project-related information and give full play to the advantages of prefabricated building industrialization. Figure 2 shows a BIM-based prefabricated building intelligent building system.
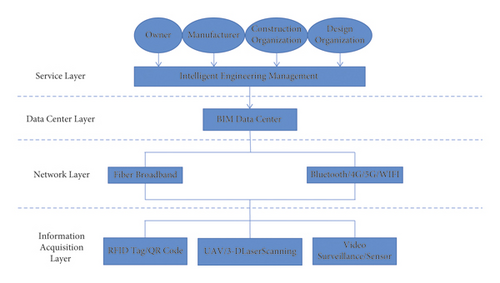
The intelligent construction system of the prefabricated building based on BIM includes an information acquisition layer, network layer, data center layer, and service layer. The information collection layer is the basis of the intelligent construction system, which mainly obtains the massive information generated in the whole life cycle of the prefabricated building and provides support for the timely collection of data through infinite RF technology, UAV, and three-dimensional laser scanning technology. This equipment can obtain timely information such as the production status, product quality, and progress of prefabricated components in time [15]. The timely acquisition of this information gives the project a more transparent perception and is the “cornerstone” to assist the intelligent construction of prefabricated buildings. The network layer is equivalent to the “nerve” of human beings. The collected information is transmitted in time through a wired network and wireless network. The purpose of existence is to interconnect people and things. The data center layer is a massive database that contains all kinds of structured and unstructured data, such as architectural geometry, nongeometric data, text document data, progress, cost, and quality. The service layer serves all participants in the whole life cycle of the building. Each participant of the project can extract the data needed by the party through the data center layer and complete the personalized and targeted work of the party through the PC or mobile terminal so as to realize the collaborative work and information transmission of all participants of the project [16]. From the design of prefabricated components to the assembly of the whole building, the prefabricated building needs to go through three stages: design, production, and assembly. Through intelligent construction technology, the information in the whole life cycle of the prefabricated building can be quickly obtained, and the participants of the project work together. The difference between prefabricated architecture and traditional architecture is reflected in each stage of architecture, and its core connotation is shown in Table 1. “Four sections and one environmental protection” is shown in Figure 3.
Content | Traditional construction method | Fabricated construction method |
---|---|---|
Design phase | Disconnection between design, production, and construction | Integrated and information-based collaborative design |
Construction stage | Wet operation and manual operation on-site | Assembly, specialization, refinement, and mechanization |
Decoration stage | Blank room and secondary decoration | The decoration is synchronized with the main structure |
Acceptance phase | Divisional and itemized sampling inspection | Whole process quality control |
Management phase | Focus on labor subcontracting of migrant workers and pursue their own interests | EPC management pursues the maximization of overall benefits in the whole process |
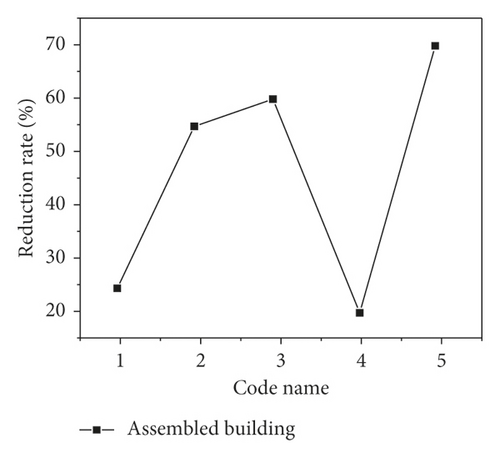
The characteristics of prefabricated buildings are as follows.
3.1.1. Green Building
Green building refers to the realization of “four sections and one environmental protection” (energy saving, land saving, water saving, material saving, and environmental protection) to the maximum extent in the whole life cycle of the building, providing people with a healthy and comfortable living environment and making good use of space to achieve harmonious coexistence with nature [17]. In the context of green environmental protection and the transformation and upgrading of the construction industry, the advantages of prefabricated buildings are reflected. Prefabricated buildings are assembled through standardized design, factory processing, transportation of prefabricated components to the construction site, and reliable connections. Compared with the traditional cast-in-place technique, the prefabricated components are prefabricated in the factory and assembled on-site. This greatly reduces the workload of concrete pouring at the construction site, reduces environmental pollution, and saves construction time. Therefore, the construction method of prefabricated buildings helps to achieve “four sections and one environmental protection” [18].
3.1.2. Change of Management Mode
The preliminary design stage of components is to estimate the shape, scale, and weight of prefabricated components on the basis of building, structural design, and electromechanical equipment, jointly with the component production enterprise, combined with the production process of prefabricated components, as well as the hoisting capacity, road transportation, and other conditions of the construction unit, and fully coordinate with the construction, structure, electrical, and other disciplines. On the basis of preliminary design, the structure discipline determines the size, quality, and other spatial geometric and physical information of prefabricated components, and the electromechanical equipment discipline determines the embedded position of pipelines. The detailed design shall be carried out before the fabrication of components, which shall meet the manufacturing capacity of the factory, the technical, and safety requirements for the overlapping of components in the construction link, determine the accurate positions of embedded parts, embedded objects, and reserved grooves, complete the checking calculation of building structure design, and finally complete the plane, elevation, reinforcement, installation, and detailed structural drawings of prefabricated components. The design drawings shall be submitted to the production unit for production. Finally, it is assembled by the construction unit [10]. At present, the traditional project management mode is used in the prefabricated building construction project. The design unit selects the appropriate structural system according to the building function needs and project environmental conditions of the construction unit, and the production unit produces according to the drawings and hands it over to the construction unit for construction. Although this project management mode is relatively mature, it still faces difficulties in coordination, long drawing modification cycle, and difficult problems for all project participants to communicate. At present, China advocates the development of prefabricated buildings in the direction of integration (architecture, structure, and electromechanical integration; design, processing, and assembly integration; technology, management, and market integration). Through the management mode of EPC (design, procurement, and construction), the whole process management is carried out by one enterprise from the design stage, production stage, and construction assembly stage of prefabricated buildings. This management mode has the advantages of promoting the effective integration of industrial chain, improving the bidding level and ensuring the construction period.
3.1.3. Reform of Architectural Form
With the development of the integration of prefabricated buildings, the production and construction links are fully considered in the design stage, and the decoration is advanced to the design stage. Due to people’s higher requirements for the living environment, there are also great changes in construction. In the design stage, the different needs of users are taken into account, such as home decoration style and parts, so as to create a good home environment. The kitchen, furniture, doors and windows, and other parts are produced in the factory quickly and with quality and quantity through the industrialized assembly line. Then the parts and components are transported to the construction site and assembled by dry connection method. Due to the integrated design of architecture, structure, electromechanical, and decoration, it is convenient to set holes and embedded parts and determine the position of parts in advance so as to avoid secondary drilling during construction, which can not only ensure the safety and stability of building structure but also reduce the generation of construction waste [19].
3.2. Application of BIM-Based Prefabricated Building Intelligent Construction in Component Production Process
The production process of prefabricated components relies on BIM Technology and Internet of things technology to dynamically track the key nodes and processes of prefabricated components and timely update the production status and expansion information of prefabricated components so as to enable the managers of prefabricated component production units to timely understand the production status of prefabricated components and better arrange the urgent work [4]. From production to assembly, prefabricated building components go through three links: production, transportation, and assembly, mainly involving the production unit, transportation unit, and construction unit. The timely update and circulation of information are very important for all participants of the project. For example, taking prefabricated concrete components as an example, the production tracking nodes can be set according to the production process of the enterprise, as shown in Figure 4.
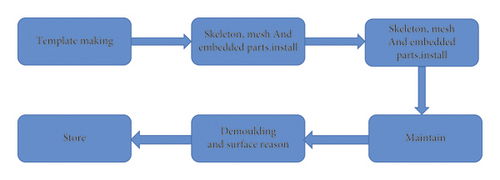
The nodes of the transportation phase are prefabricated component loading, prefabricated component ready for transportation, transportation in progress, and arrival at the destination. Based on information technology and equipment, production personnel and drivers update and upload the current status of production and transportation of prefabricated components to the information platform. Through the timely flow of information, all participants of the project can timely understand the current status of prefabricated components so that subsequent participants can timely formulate, modify, and implement plans. There are three processes for the positioning, tracking, and application of components in the production stage by BIM + Internet of things technology. The tracking management of all links is realized in the production preparation stage, prefabricated component production stage, and prefabricated component transportation stage [20]. The emergence of information technology improves the slow information flow of prefabricated buildings in all links. Through information technology, timely update the production and logistics information of prefabricated components, convert the point-to-point information communication mode into a systematic and centralized communication mode, and upgrade the paper office to a digital and electronic office mode. Through BIM Technology, Internet of Things technology, and GPS positioning system, the production, transportation, and delivery of prefabricated components can be tracked and positioned. All participants of the project can update, query, and locate the production and transportation of prefabricated components through the information communication platform. All participants of the project arrange their work with accurate and timely information, as shown in Figure 5.
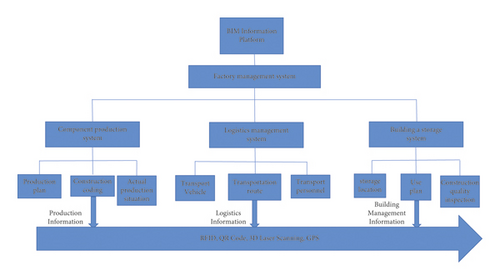
3.2.1. Preparation Stage before Component Production
Compared with other processing methods, the mold production of prefabricated components has high precision and high consistency. To a certain extent, the quality of the mold directly affects the production quality of prefabricated components. Due to the complex and diversified shapes of prefabricated components, especially the opening of grouting sleeve and exposed reinforcement, the production of mold needs to comprehensively consider factors such as cost, service times, quality, and production efficiency. The three-dimensional information model provided by BIM Technology provides the detailed information required by production components for production units and liberates designers from complex spatial imagination through the advantages of three-dimensional visualization and parameterization of BIM Technology [21]. BIM model is known as a parametric model. Therefore, while modeling, various components are given parameter information such as 3D spatial relationship, model, and material during 3D modeling. After repeated verification, verification, and modification, the established model can export the details according to the fields such as material, location, manufacturer, and material use. The material and equipment data derived from this have high reliability. The production unit quickly carries out production disclosure, material preparation, and formulation of production schedule through information model, drawings and detailed list, and bill of materials. Refine the daily output of components, production personnel arrangement, reinforcement and concrete consumption, material mobilization arrangement, and mold consumption according to the production schedule and the overall project schedule [22].
3.2.2. Production of Prefabricated Components
Before the mobilization and unloading of raw materials required for prefabricated components, the material procurement department of the production unit shall notify the quality management department of the unit to inspect the quality of new materials. The quality management department shall timely inspect relevant raw materials by batch or number, prepare quality inspection reports, and upload them to the information management platform. Unqualified products shall not be put into production to achieve prior quality control. Through the factory information management platform, the component information is converted into a format that can be recognized by machinery and equipment, and the component production information is interpreted, which enters the production link of prefabricated components [23]. Through the control program, complete the formwork production, realize the automatic cutting and bending of reinforcement, complete a series of production processes such as reinforcement binding and embedded parts installation, concrete pouring and vibration, demoulding, surface cleaning, and storage. Automatic production is convenient for lean and digital manufacturing and reduces labor cost, error rate, and accuracy. In the whole production process, there will always be real-time monitoring by the factory information automation monitoring system. In case of abnormal conditions such as production failure, it can be reflected to the factory managers in time, and the managers can quickly make corresponding measures. In the process of component production, BIM and radiofrequency technology are used to enhance the identification of components. The three-dimensional model corresponds to the component entity one by one. The production personnel of the production unit changes the production status of prefabricated components through the mobile terminal according to the production status of prefabricated components, including production tracking personnel, component production links, component types, tracking time, consumed man hours, and location of prefabricated components. The production status of prefabricated components is changed through the mobile terminal, including production tracking personnel, component production link, component type, tracking time, person-hours consumed, and the location of prefabricated components. At this time, the prefabricated component information will be updated in time in the collaboration platform, and the project participants can track the key production process links of prefabricated components through the information platform [24]. After the component is demoulded, the three-dimensional laser scanning technology is used to obtain the point cloud data, compare the point cloud data with the three-dimensional model, and determine the quality grade of the prefabricated component. Explain the quality situation through the mobile terminal; the collaborative platform gives treatment opinions on the fed-back quality information and the person in charge of the treatment. After the production management personnel take measures such as abandonment and repair through the collaborative platform, they timely feed back the status information of prefabricated components through information means and conduct quality inspection again until the quality is qualified. In this way, a closed loop of quality control of prematerial quality inspection, in-process quality inspection, and postquality inspection is formed to achieve lean production management [25].
3.2.3. Component Transportation Stage
Before the prefabricated components leave the factory, the quality management department of the production unit shall recheck the product quality of the prefabricated components to be transported according to the process and quality inspection standards. The manufacturer defines the products with qualified component quality as qualified. The supervision unit issues quality certificates for prefabricated components. Products that do not meet the quality standards can be handled according to the corresponding standards. The quality inspectors update the quality information of prefabricated components through the reader or mobile terminal, take photos, and upload them to the information collaboration platform for electronic quality certificates. To ensure the quality of prefabricated component products [11], the construction unit shall negotiate with the production unit to determine the production and transportation plan of prefabricated components according to the construction schedule. The production management personnel query locates the components to be transported through the handheld reader or mobile terminal, records the current information of the prefabricated components, such as the name of the driver transporting the components, the driver’s contact information, the license plate of the transport vehicle, the delivery time, the person in charge of the delivery of the prefabricated components, and the purpose of the components, and uploads this information to the information platform to update the status of prefabricated components and expand relevant information.
3.3. Target Tracking
At present, the motion target tracking algorithm The production staff of the production unit according to the production status of the prefabricated components. is mainly Kalman filter-based, optical flow-based, mean drift-based, and particle filter-based. Kalman filter is an optimal linear recursive filtering method based on the minimum mean-variance prediction; for a linear system, the Kalman filter is the optimal solution to the tracking problem.
In the formula, α represents the key calculation coefficient.
The formula above is used to marginalize the key images in the original image. Because the above calculation process shows high sensitivity to noise, the above operations need to be performed after the smooth processing of the original image.
4. Results and Analysis
In the process of prefabricated building construction, due to the lack of experience in prefabricated building construction, the project manager lacks control ability and cannot accurately arrange the construction schedule according to the labor volume and workload. Through the application of BIM virtual construction technology, project managers can intuitively understand the construction progress with the help of an intuitive three-dimensional visualization effect, provide effective support for the preparation of the construction schedule, and carry out virtual construction of the whole project. According to the virtual construction, the construction schedule can be inspected, such as space inspection, time inspection, labor inspection, and workload inspection, and the construction schedule can be optimized according to the inspection results. BIM Technology has a powerful integration function, but data acquisition is not the advantage of BIM Technology. Combined with the application of Internet of things technologies such as QR code and infinite RF technology, it can quickly collect the actual completion of the construction site and realize the real-time progress management of prefabricated buildings by associating with the BIM model, as shown in Figure 6.
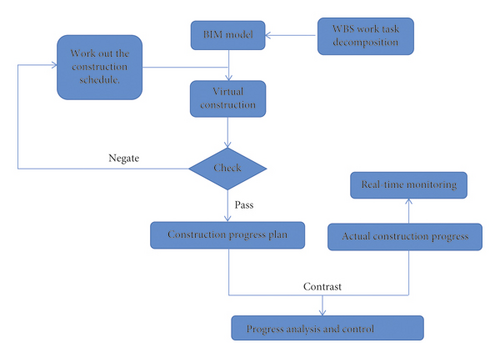
In project management, construction quality management is an important part of project management. The quality of construction directly affects the overall quality of prefabricated buildings. Before the construction of prefabricated buildings, the construction organization design and special construction scheme shall be formulated, and the corresponding construction scheme shall be formulated for the installation and construction at the nodes. The feasibility of the construction scheme shall be judged in advance through the virtual construction of collision inspection. Check the assembly difficulties and key points that may exist at present or in the next stage through three-dimensional visualization, find out the links that may affect the construction quality in the assembly process in advance, determine the key points of quality control, then supplement the construction organization design, special construction scheme, and quality control points, and select the optimal construction scheme after many construction simulations. This can ensure the feasibility and optimality of the construction scheme, facilitate the construction disclosure, and control the construction quality in advance. The quality of assembly and the progress of assembly affect each other. After the construction scheme is determined, the 3D model of prefabricated components and the time schedule can be correlated to form a 4D information model. Virtual construction is carried out through BIM Technology to dynamically display the state of components in time and space. Through collision detection, it can be found whether there will be spatial and temporal conflicts on the same working face. At the same time, view the possible quality control difficulties and key points in the construction scheme from a three-dimensional and global perspective, and output the key and difficult assembly in the form of animation, which is conducive to the construction technical disclosure. Before assembly, the placement position and control height of prefabricated components shall be determined by setting out robot or measurement and positioning. The on-site construction management personnel check the quality control difficulties and key points of prefabricated components through the mobile terminal, determine the flatness of prefabricated components by manual or three-dimensional laser scanning, and check whether there are quality problems such as missing corners of prefabricated components. If quality problems are found, take photos with the mobile terminal equipment and upload them to the background database with text records. The relevant person in charge of background management will receive the information notice and take corrective measures in time. After the hoisting is completed, the on-site management personnel modify the status information of prefabricated components through the mobile terminal equipment. At this time, the information of current prefabricated components in the background database changes from ready for hoisting to completion of hoisting, and the information will be transmitted to the relevant quality inspection personnel. The relevant responsible person will check the flatness and inclination of the prefabricated components through three-dimensional laser scanning or manual measurement to ensure the assembly quality of the prefabricated components and modify the status information of the prefabricated components through the mobile terminal or RFID reader. If there is a quality problem, the relevant responsible person shall take corrective measures in time and upload the rectification to the background database. The quality inspector shall check again to form a closed quality control loop, as shown in Figure 7.
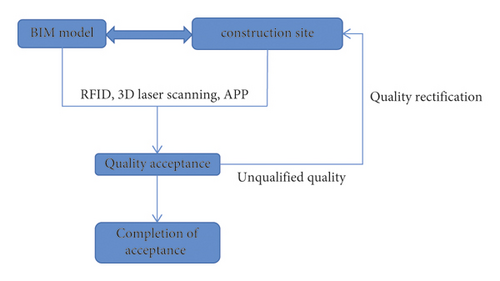
5. Conclusion
In view of the above actual needs, a full life cycle intelligent construction system of prefabricated tunnel structure based on BIM is proposed to meet the requirements of railway tunnel construction for intelligent construction in the new era. New technologies and new ideas also lead the further scientific and technological innovation of tunnel engineering to a certain extent, meet the actual needs of the development of intelligent railway construction technology, and have the practical significance of improving quality and efficiency. Comb the relevant theoretical basis of prefabricated building, BIM Technology, and intelligent construction, and introduce the emergence and development of the prefabricated building. There are problems such as safety and structural stability in the process of emergence and development of the prefabricated building. The rapid development of information technology provides a good solution for the prefabricated building to move towards intelligence. BIM Technology can eliminate 40% of budget changes, save 80% of budget preparation time, save 3% of the cost and 7% of project time, and reduce building energy consumption by 30%, which plays a very important role in green building and lean manufacturing of prefabricated buildings. Therefore, based on BIM Technology, this article innovatively researches new design methods and construction technologies of prefabricated structures so as to realize the high-efficiency construction of prefabricated structures and the full life cycle management of information.
Conflicts of Interest
The authors declare no conflicts of interest.
Acknowledgments
This work was supported by a project of Qinhuangdao Science and Technology Bureau: A study on the strategic demand and development prospect of underground space development and utilization in Qinhuangdao City (Project no. 202005A134).
Open Research
Data Availability
The data used to support the findings of this study are available from the corresponding author upon request.