Robust Design Optimization of a 4-UPS-S Parallel Manipulator for Orientation-Regulating Control System of Solar Gather Panels
Abstract
This paper proposes a redundantly actuated parallel manipulator 4-UPS-S that is applicable for orientation adjustment in the gathering process of solar power. A thorough analysis involving the kinematic issues is performed. Inverse kinematic problems are solved in the close-loop. The Jacobian matrix and some performance indexes are analytically derived. The multiobjective optimization model is established, and the determinacy optimization is completed on the basis of previous research works. Six-Sigma robust analysis is performed on the basis of the determinacy optimal solution. Results show that 4-UPS-S does not satisfy the quality requirement. Therefore, it is necessary to implement Six-Sigma robust optimization, and select optimial solution of robustness to complete the nondeterminacy optimization. The research results show that the proposed methodology has a simple operation and high optimization efficiency. The methodology commodiously obtains robustness parallel manipulator that satisfies the quality requirement.
1. Introduction
Determinacy analysis and design is a traditional optimization design of system inputs, mechanical structures, material properties, manufacturing, and installation with no error or with a constant error value. Most of the above parameters in practical engineering application problems are uncertain problems with some existing errors [1–3]. In accordance with certain distributions, the actual values fluctuate up and down beside the theoretical values and are not artificially controlled. The robust analysis and design are the process of studying parameter errors as random variables. Research on the robust design optimization of the parallel manipulators is uncommon [4, 5]. Gao [6] used the robustness optimization design of the 3-RPS parallel manipulator by adopting the Box-Behken experimental design and the ANSYS Workbench that generated the initial sample points. He further used the Kriging interpolation and neural network methods to regenerate new sample points. Yu [7] analyzed and solved the parallel robot manipulator deviation used in the sheet metal assembly. He further derived a new robustness design index on the basis of the sheet metal assembly deviation model. Meng et al. [8] treated the design variables as random variables and built the robustness optimization design mathematical model with a four-bar manipulator. Kato and Muramatsu [9] proposed a method that is the Monte Carlo simulation and particle swarm optimization method to evaluate robustness of adjustable mechanisms. Abdellatif et al. [10] presented a self-contained approach for the robust dynamics identification of parallel manipulators in terms of uncertain parameters and illustrated the control accuracy by numerous experimental investigations. Rahman et al. [11] presented the robust design of suspension arm using stochastic design improvement technique based on Monte Carlo simulation. Many scholars employed different methods for robustness design optimization (e.g., blind number theory [12] and Monte Carlo simulation method [13, 14]).
The paper is organized as follows. In Section 2, the structure of the 4-UPS-S parallel manipulator that can be applied in the solar gather panel orientation control system is described and the reference systems of the parallel manipulator are established. In Section 3, the inverse kinematics of the parallel legs and forward kinematics of serial passive legs of the manipulator are studied. Section 4 explains the performance indexes including the maximum payload capacity, maximum and minimum stiffness, and kinematic dexterity to evaluate mechanical performances. In Section 5 a determinacy optimization design is performed based on software Isight. In Section 6, Six-Sigma optimization technique for robust design optimization is analyzed. In Section 7, Six Sigma robust optimization is conducted with consideration uncertain parameters and achieves reliability and quality level. Section 8 analyzes and explains the results of the robust design optimization. Finally, Section 9 summarizes and arranges contents of this study. The robustness analysis optimization flow diagram is described in Figure 1.
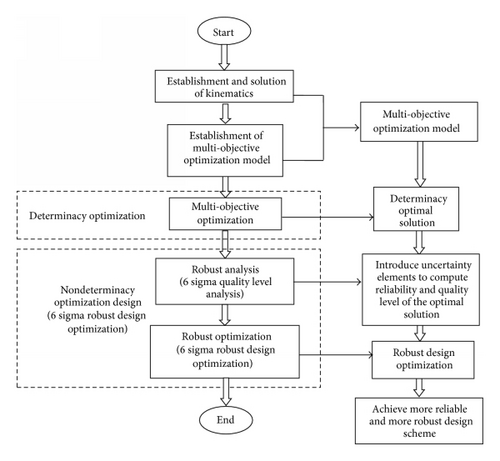
2. Parallel Manipulator Description
The traditional orientation-regulating control manipulators of solar gather panels generally have two degrees of freedom. These degrees of freedom regulate the azimuth and manipulator elevation to track the trajectory of the sun. However, solar equipment cannot achieve the requirement of maintaining the azimuth level with changes in the tracking process (e.g., solar water heaters). This paper adds a degree of freedom on the basis of the original two degrees of freedom. The additional degree of freedom rotates on its own to regulate the equipment level. This study further proposes a three-rotation redundant parallel manipulator (i.e., 4-UPS-S) for the orientation control system of solar gather panels. The redundant active chain of the 4-UPS-S eliminates the various singular configurations of the 3-UPS-S parallel manipulator [15].
The structural schematic of the 4-UPS-S parallel manipulator and its application as an adjusting manipulator in the solar gather panel are shown in Figure 2. The four active UPS chains contain the hinged points Ai of the bases A and Bi moving platform B (i = 1,2, 3,4). The distance between the base and moving platform is constant and equal to 500 mm. The moving platform is directly connected to the fixed base by a passive spherical joint O. Each chain consists of universal, prismatic, and spherical joints. We assign a fixed Cartesian coordinate system O-XAYAZA and the moving Cartesian system O-XBYBZB at the centered point O for analysis (Figure 2(a)). The XA axis of the fixed coordinate system is parallel to the OAA1. The ZA axis is perpendicular to the base and top. The YA axis is based on the right-hand rule. The XB axis of the moving coordinate is parallel to OBB1. ZB is perpendicular to the moving platform. The YB axis is based on the right-hand rule. The distance between the coordinate origin and moving platform is h. The circumcircle radii of points A1, A2, and A3 are rA. Point A4 is located in the plane perpendicular to the base and parallel to OAA3. Point A4 in the region to the base is calculated as hA = 250 mm. The projection distance between points A1 and A4 is s. The circumcircle radii of points B1, B2, and B3 are rB. Point B4 is located in the XBOZB plane. The distance from the point to the ZB axis line is (t · rB). The distance to the moving platform is hB.
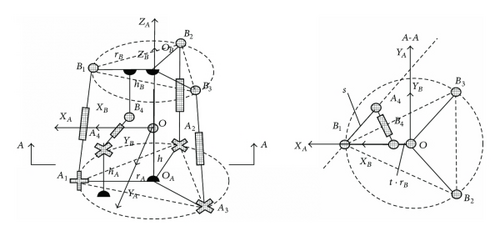
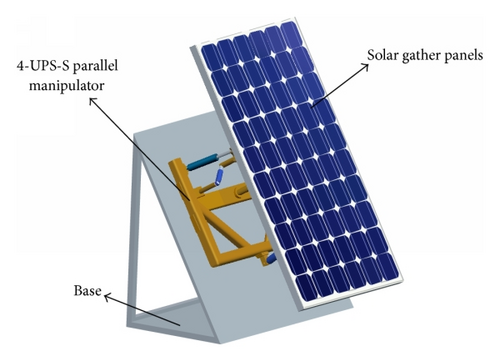
3. Kinematics Model Solution of the Parallel Manipulator
3.1. Inverse Kinematic Solution
3.2. Passive Constraint Chain Forward Model
The passive constraint chain of the 4-UPS-S parallel manipulator is an open-kinematics chain with three-rotation degrees of freedom. For analysis, we separate the spherical joint into three revolute joints by adopting the Denavit-Hartenberg (D-H) method. We use three rotation angles (i.e., φ1, φ2, and φ3) to describe its orientation. The coordinate system of the adjacent links is settled by using the D-H method. The overlap coordinate system origin is separated for convenience of illustration (Figure 3).
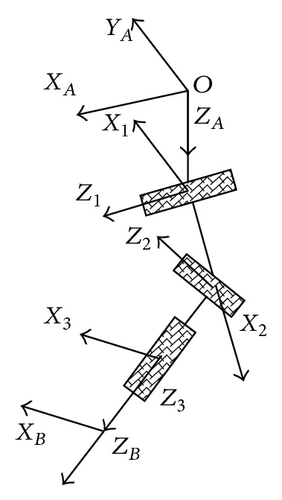
θi | di | ai | αi | |
---|---|---|---|---|
0 | 0 | 0 | 0 | 0 |
1 | 90° + ϕ1 | 0 | 0 | 90° |
2 | 90° + ϕ2 | 0 | 0 | 90° |
3 | ϕ3 | 0 | 0 | 0 |
4. Establishment of the Parallel Manipulator Performance Indexes
4.1. Global Kinematic Dexterity
The global dexterity index is in the range 0 ≤ kj ≤ 1. A global dexterity index closer to one corresponds to better dexterity and control precision. We generally calculate the condition number κJ of the Jacobian matrix in different workspace positions and orientations to increase indicator operability. The mean of the reciprocal of the Jacobian matrix is calculated as a global kinematic dexterity index kj.
4.2. Global Stiffness Performance Index
Larger global stiffness evaluation indexes kmax and kmin correspond to better parallel manipulator stiffness.
4.3. Global Maximum Payload Capability
A greater global maximum payload capability-evaluation index gmax corresponds to better parallel manipulator payload capability.
5. Deterministic Optimization Design Model of the Parallel Adjusting Manipulator
This study maximizes the global payload capacity and global maximum stiffness to improve the parallel adjusting manipulator of the loading ability that bears the solar equipment weight. The global kinematic dexterity and minimum stiffness are the constraint conditions. The design variables are h, s, and t (Figure 2(a)).
We employed the Simcode components to integrate MATLAB and calculate the parallel manipulator evaluation indexes. The NSGA-II optimization algorithm is adopted for the present study. The population size is 16, rate of crossover is set to 0.9, rate of mutation is set to 0.1, rate of migration is set to 0.1, and the generation number is 15. The design variables, constraint conditions, and optimization objectives are selected on the basis of the application requirement [2, 19]. We run the software platform once the parameter setting is completed.
The deterministic optimization design is a multiobjective optimization design problem. The history points of the two objective functions in the solving process are plotted in Figure 4. The two objectives increase or decrease at the same time. The Pareto optimal solution is a convenient solution for this multiobjective optimization design problem when the global stiffness and global payload capacity obtain the maximum values at the same time.
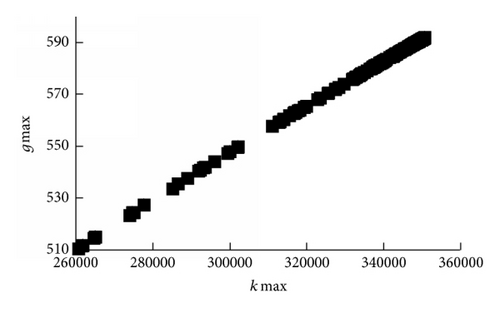
The deterministic optimization design result and initial scheme comparison is presented in Table 3. The deterministic optimization design analysis solution results show that the optimization objectives (i.e., global maximum stiffness and global payload capacity) have a considerable improvement. However, the parameters (i.e., h, s, t, and kj) are all close to the constraint boundary at the same time. If the uncertainty factor influences are considered, the deterministic optimization scheme violates the constraint conditions. Therefore, performing a robust analysis that evaluates the quality and reliability level of the deterministic optimization design scheme is necessary [20, 21].
6. Six-Sigma Robust Analysis
In this study, some uncertainty factors include the design variables h, s, and t. The radii rA and rB of the base and moving platform follow the same normal distribution. The optimal design point value of the deterministic optimization design is considered the mean of the random design variables. The standard deviation is presented in Table 2. σ = 1% × μ represents the 1% coefficient of variation (i.e., σ/μ = 0.01). The robust analysis of the 4-UPS-S parallel manipulator is implemented by adopting the Six-Sigma component based on Isight software.
Random design variables | h: μ = 200.005, σ = 1% × μ |
---|---|
s: μ = 129.096, σ = 1% × μ | |
t: μ = 0.799, σ = 1% × μ | |
Random noises | The radius rA of the base: μ = 500 mm, σ = 1% × μ |
The radius rB of the moving platform: μ = 400 mm, σ = 1% × μ | |
Quality constraints | The global kinematic dexterity: kj ≥ 0.3 |
The global minimum stiffness: kmin≥3 × 104 |
Variables | Initial scheme | Determinacy optimization scheme | Robust optimization scheme | |||
---|---|---|---|---|---|---|
Determinacy optimal solutions | Six-Sigma analysis | Robust optimization analysis | Quality level | |||
Input variables | ||||||
h | 300 | μ | 200.005 |
|
213.330 | 6.356 |
σ | 2.00005 | 2.13330 | ||||
s | 200 | μ | 129.096 |
|
218.936 | 8.0 |
σ | 1.29096 | 2.18936 | ||||
t | 0.6 | μ | 0.799 |
|
0.683 | 8.0 |
σ | 0.00799 | 0.00683 | ||||
Output variables (performance indexes) | ||||||
Global kinematic dexterity kj | 0.310 | μ | 0.305 |
|
0.305 | 7.809 |
σ | 0.007 | 0.007 | ||||
Global minimum stiffness kmin | 30045 | μ | 36880 |
|
42991.7 | 7.563 |
σ | 1721 | 1739 | ||||
Global maximum payload capability gmax | 538.736 | μ | 591.702 | 574.223 | ||
σ | 4.276 | 4.014 | ||||
Global maximum stiffness kmax | 290141 | μ | 350500 | 329940 | ||
σ | 5084 | 4624 |
The Six-Sigma robust analysis results are concretely summarized in Table 3. The input variables h and t do not reach the One Sigma level. The reliability is approximately 50%, which is considered low. The global kinematic dexterity and the global minimum stiffness have a relatively high reliability. The minimum stiffness attains a reliability of 99.99% but cannot reach the Six-Sigma level. The global minimum stiffness Sigma level is 4.161. In the long term, when the 1.5σ quality shift occurs in the system, the defective products per million with a Sigma level of four will sharply increase from the short term 63 × 10−6 to 6200 × 10−6. The quality levels of h and t are low and do not achieve the One Sigma level. Therefore, performing a robust optimization for this problem is necessary in the long term.
7. Six-Sigma Robust Optimization (Uncertainty Optimization)
The essence of the Six-Sigma robust optimization is to add the mean, the variance of the response in optimization objectives, and the upper quality level limit of the random variables in the constraint conditions to satisfy the quality level, minimize the mean of the optimal objectives, and increase the robustness and reliability of the mean [22].
When setting the optimization objectives, the scale factor of the standard deviation should be set to 0.01 to ensure that the standard deviation and mean have the same order of magnitude.
The Six-Sigma robust design optimization flow diagram is shown in Figure 5. During the procedure, the Six-Sigma component robust analysis is used to analyze the single design point robustness. The optimization design component robust optimization is employed to perform the optimization design on the basis of robustness analysis. If the quality of the single design point cannot satisfy the quality level requirements, Isight will continue to improve the optimization variables for the quality analysis of the next group; otherwise, the results will be exported, and the robust optimization is completed. The present study selects the nondominated sorting evolution strategy, namely, NSGA-II, as the optimization algorithm.
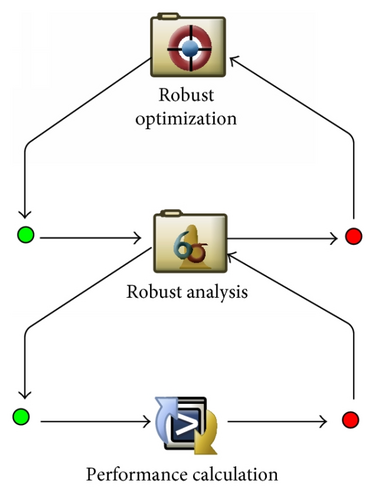
-
The population size: 4.
-
The generation number: 10.
-
Crossover probability: 0.9.
-
Crossover distribution index: 10.
-
Mutation distribution index: 20.
-
Max failed runs: 5.
-
Failed run penalty value: 1.0E30.
-
Failed run objective value: 1.0E30.
We obtain the Pareto solutions and frontier after the Six-Sigma robust optimization design. The Pareto frontier of the mean, as well as the variance of the maximum payload capacity and maximum stiffness, is illustrated in Figure 6. The relationship among the optimization objectives from the Pareto solutions is observed. According to this relationship and the practical application requirements, we select the optimal solution for the multiobjective design problems and choose the point of optimal solution (Figure 6). In view of reliability and quality level theory, we can obtain the quality level, mean, and variance of each response after the robust optimization through the post-processing functions of Isight software. And the results are listed in Table 3.
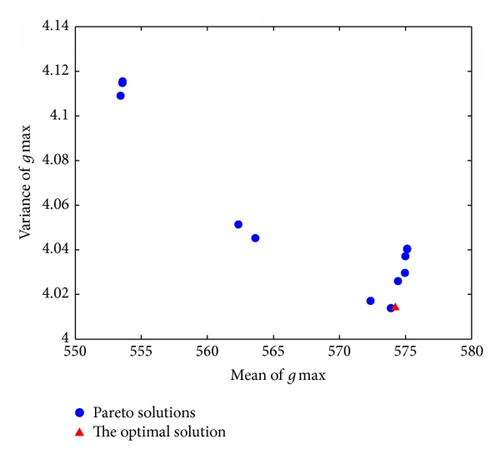
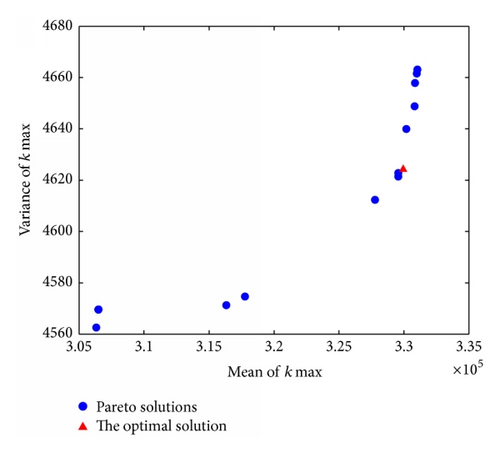
Comparing the quality level with robust optimization, that is, variable quality level of h, s, t is 0.676, 7.142, 0.755, respectively. Performance indexes quality level of kj, kmin is 1.187, 4.161, respectively. After robust optimization, the quality level of each response is greater than six.
8. Result Analysis of the Six-Sigma Robust of the Parallel Adjusting Manipulator
By taking the global kinematic dexterity index as an example, the probability distribution and Six-Sigma level were compared before and after optimization (Figure 7). We intuitively obtained the probability distribution, mean, standard deviation, and Six-Sigma level of each response (Figure 7).
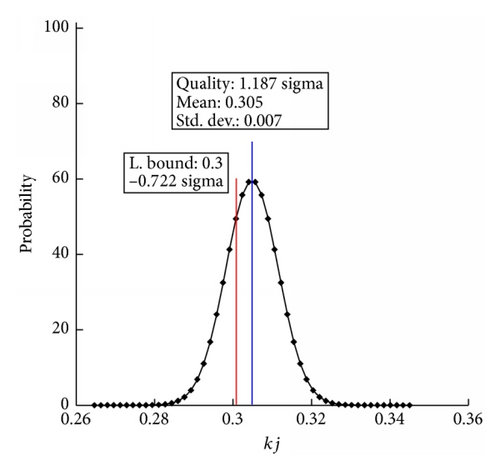
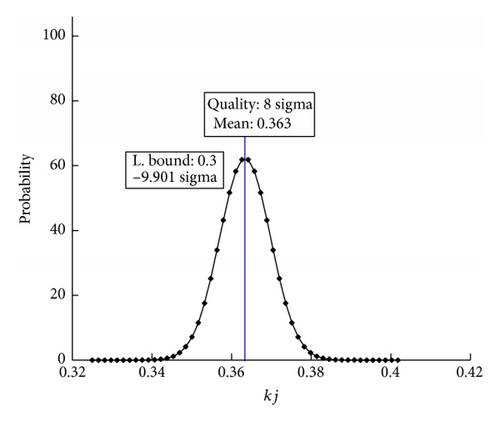
We rearranged and listed the reliability of each variable before and after optimization (Table 4) to concretely illustrate the difference between the reliability and defective quality per million before and after the robust analysis. The defective products per million are shown in Table 5.
Before robust optimization | After robust optimization | |
---|---|---|
h | 50.099% | 99.999% |
s | 100% | 100% |
t | 54.980% | 100% |
kj | 76.472% | 100% |
kmin | 99.997% | 100% |
Before robust optimization | After robust optimization | |
---|---|---|
h | 499002.670 | 2.069e − 4 |
s | 9.213e − 7 | 0 |
t | 450199.849 | 0 |
kj | 235279.150 | 5.773e − 9 |
kmin | 31.653 | 3.930e − 8 |
The parameter variables (i.e., h and t) and quality constraints (i.e., global kinematic dexterity kj) (Tables 4 and 5) greatly improves after optimization. However, the reliability of the other parameter variables only improved slightly. By contrast, the defective quality per million improved considerably (Table 5). In the long term, the adjusting manipulator designed and manufactured with optimal design variables has fewer defective products per million than before optimization. This result is based on the assumption that the design variables, manufacturing, and installation error of the base and moving platform can be effectively controlled, thus greatly improving the resistance ability of the uncertainty factor disturbance in the whole manufacturing process. Data in Tables 4 and 5 show that the Six-Sigma robust optimization design based on Isight is effective and feasible.
9. Conclusions
- (1)
The parallel adjusting manipulator was designed by using multiobjective optimization design on the basis of the inverse kinematic solution. The performance indexes are established, the optimal solution is obtained, and the determinacy optimization is completed.
- (2)
Robustness analysis is performed on the basis of determinacy optimization design. Some parameter variables and performance indexes are close to the constraint boundary. The Sigma level is low, and the defective quality per million is high. The implementation of the Six-Sigma robust optimization is necessary to complete the nondeterminacy optimization design.
- (3)
The comparison of the manipulator before and after the robust design optimization shows that the new one has a higher Sigma level. Furthermore, the comparison shows a lower defective quality per million than before optimization. The optimization objectives are optimal. The mean and standard deviation are in their minimum. This result indicates that in the long term, the manipulator after optimization is more suitable for batch production applications than the manipulator before optimization. The robust optimization based on Isight is efficient and convenient for operation with accurate results. These results are applicable to the robust design optimization of large-scale and complex manipulators.
Conflict of Interests
The authors declare that there is no conflict of interests regarding the publication of this paper.
Acknowledgments
This research is supported by the National Natural Science Foundation of China (Grant no. 51175143).