Study of an Amorphous Silicon Oxide Buffer Layer for p-Type Microcrystalline Silicon Oxide/n-Type Crystalline Silicon Heterojunction Solar Cells and Their Temperature Dependence
Abstract
Intrinsic hydrogenated amorphous silicon oxide (i-a-SiO:H) films were used as front and rear buffer layers in crystalline silicon heterojunction (c-Si-HJ) solar cells. The surface passivity and effective lifetime of these i-a-SiO:H films on an n-type silicon wafer were improved by increasing the CO2/SiH4 ratios in the films. Using i-a-SiO:H as the front and rear buffer layers in c-Si-HJ solar cells was investigated. The front i-a-SiO:H buffer layer thickness and the CO2/SiH4 ratio influenced the open-circuit voltage (Voc), fill factor (FF), and temperature coefficient (TC) of the c-Si-HJ solar cells. The highest total area efficiency obtained was 18.5% (Voc = 700 mV, Jsc = 33.5 mA/cm2, and FF = 0.79). The TC normalized for this c-Si-HJ solar cell efficiency was −0.301%/°C.
1. Introduction
High-efficiency solar cells with low production costs are still needed for manufacturers. Generally, operating a solar cell in a high-temperature environment degrades its conversion efficiency [1–4]. Therefore, developing solar cells for use in tropical regions is important. Crystalline silicon heterojunction (c-Si-HJ) solar cells with ultrathin intrinsic hydrogenated amorphous silicon (i-a-Si:H) passivation layers are an attractive crystalline silicon solar cell technology because they have low temperature coefficients (TCs) and high efficiencies [5–7]. However, light absorption lost to the hydrogenated amorphous silicon (a-Si:H) window layer lowers the short circuit current (Jsc) and solar cell performance. Using wide bandgap materials is a potential solution to this problem. Hydrogenated silicon oxide is a good candidate for the window layer material because hydrogenated amorphous silicon oxide (a-SiO:H) exhibited excellent passivation [8–10]. Furthermore, hydrogenated microcrystalline silicon oxide (μc-SiO:H) exhibited better electrical properties and lower optical absorption coefficients than a-Si:H [11–14]. Thus, combining a-SiO:H and μc-SiO:H for the heterojunction solar cell window layer is promising. In this paper, we investigated the effect that using intrinsic hydrogenated amorphous silicon oxide (i-a-SiO:H) films with wide optical bandgaps as the buffer layers had on p-type hydrogenated microcrystalline silicon oxide (p-μc-SiO:H)/c-Si-HJ solar cell performance at high operating temperatures.
2. Experimental Details
2.1. Deposition of i-a-SiO:H Films
The i-a-SiO:H films were prepared on soda-lime glass substrates and float-zone (FZ) silicon wafers (100) using n-type 1–5 Ωcm double side polished wafers 260–300 μm thick. Prior to the deposition, the wafers were cleaned (ethanol/acetone/ethanol: 15/15/15 min) and dipped into diluted 5% hydrofluoric acid (HF) to remove any native oxide before depositing the i-a-SiO:H films. The i-a-SiO:H films were deposited via a 60 MHz very high frequency plasma enhanced chemical vapor deposition (VHF-PECVD) in a multichamber with a parallel plate configuration. We used silane (SiH4), hydrogen (H2), and carbon dioxide (CO2) as the reactant gases. The substrate temperature, plasma power density, and deposition pressure were held at 180°C, 20 mW/cm2 and 300 mTorr, respectively. The deposition conditions are summarized in Table 1. Afterwards, the effects of the CO2/SiH4 ratio on the film properties were investigated. The i-a-SiO:H film passivation quality was characterized using the quasi-steady-state photoconductance (QSSPC) lifetime [15, 16]. The lifetime samples were deposited as i-a-SiO:H films on both sides of the n-c-Si wafer, and their passivation quality was measured in terms of the effective lifetime (τeff). The optical properties and thickness of these i-a-SiO:H films coated on soda-lime glass substrates were evaluated via spectroscopic ellipsometry (SE).
Parameters | Values |
---|---|
H2/SiH4 | 3.3 |
CO2/SiH4 | 0–0.5 |
Plasma frequency | 60 MHz |
Deposition temperature | 180°C |
Deposition pressure | 300 mTorr |
Power density | 20 mW/cm2 |
Thickness | 50 nm |
2.2. Fabrication of Heterojunction Solar Cells
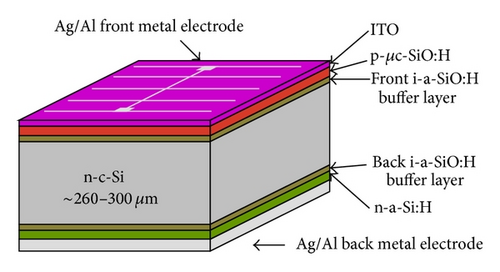
3. Results and Discussion
3.1. Properties of the i-a-SiO:H Films
The effects the CO2/SiH4 ratio had on the surface passivation quality and optical properties of the i-a-SiO:H films were investigated. CO2 was used as O source gas during the i-a-SiO:H film deposition. The samples were prepared by increasing the CO2/SiH4 ratios from 0.0 to 0.50 with a thickness of approximately 50 nm. The samples exhibited an i-a-SiO:H (CO2/SiH4: 0.0–0.50)/n-c-Si/i-a-SiO:H (CO2/SiH4: 0.17) structure. The CO2/SiH4 ratio affected the τeff of n-c-Si wafers passivated with i-a-SiO:H films as shown in Figure 2. The τeff increased with increasing CO2/SiH4 ratios. For a CO2/SiH4 ratio of 0.0, the sample showed a low τeff of 51 μs because the i-a-Si:H layer grew epitaxial silicon on the crystalline substrate. The epitaxial interface is a defect and deteriorates the passivation quality. However, the τeff increased rapidly from 232 μs to 2500 μs upon increasing the CO2/SiH4 ratio from 0.17 to 0.50. Therefore, increasing the CO2/SiH4 ratio can suppress the epitaxial silicon growth. Meanwhile, the implied Voc increased from 583 mV to 708 mV with increasing CO2/SiH4 ratio. In addition, the optical bandgap of the i-a-SiO:H films increased gradually with increasing CO2/SiH4 ratio. The optical bandgap of a conventional i-a-Si:H film with a CO2/SiH4 ratio of 0.0 was 1.72 eV. Increasing the CO2/SiH4 ratio from 0.17 to 0.50 increased the optical bandgap of the i-a-SiO:H films from 1.81 eV to 1.95 eV.

3.2. Fabrication of Heterojunction Solar Cells
The effect of the CO2/SiH4 ratio for the front i-a-SiO:H buffer layer on the c-Si-HJ solar cell performance was investigated for various CO2/SiH4 ratios. First, the front i-a-SiO:H buffer layer thickness in the c-Si-HJ solar cell was optimized. The front i-a-SiO:H buffer layer thickness was varied from 2 nm to 8 nm. Figure 3 shows the PV parameters and τeff as a function of the i-a-SiO:H layer thickness. Increasing the front i-a-SiO:H buffer layer thickness increased the Voc from 655 mV to 691 mV due to the improved surface passivation. The τeff increased from 586 μs to 1125 μs with increasing front buffer thicknesses. A high Voc of 692 mV and solar cell efficiency of 18.4% were obtained using the optimized thickness of 6 nm. A front buffer layer thickness below 6 nm decreased the Voc of the solar cell. A thicker front buffer layer improved the passivation quality but reduced the FF of the solar cell due to the increased series resistance.
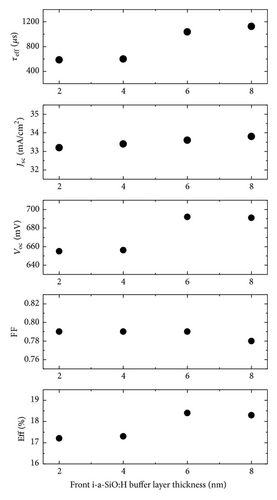
Next, the effect the CO2/SiH4 ratio of the front i-a-SiO:H buffer layer had on the solar cell performance was studied. The front i-a-SiO:H buffer layer CO2/SiH4 ratio was varied from 0.0 to 0.50 while holding the thickness at 6 nm. Figure 4 shows the PV parameters and τeff as a function of the CO2/SiH4 ratio for the front i-a-SiO:H buffer layer. The solar cells exhibited a low Voc of 626 mV at a CO2/SiH4 ratio of 0.00 due to epitaxial silicon growth [17, 18]. The Voc then increased to 699 mV at a CO2/SiH4 ratio of 0.17 and reduced to 683 mV at a CO2/SiH4 ratio of 0.50. The τeff was 1610 μs for a CO2/SiH4 ratio of 0.17 and then decreased to 357 μs for a CO2/SiH4 ratio of 0.50. However, the τeff tended to increase with increasing CO2/SiH4 ratio as shown in Figure 2. For the solar cell, increasing the CO2/SiH4 ratio in the front i-a-SiO:H buffer layer decreased the Voc and FF because of the increased series resistance. Figure 5 shows the I-V characteristics of c-Si-HJ solar cells with CO2/SiH4 ratio in front i-a-SiO:H buffer layer. Increasing the CO2/SiH4 ratio decreased the Voc and FF of I-V curves and showed S-shape influenced from the increased series resistance with the CO2/SiH4 ratio of 0.50. These results indicate controlling the CO2/SiH4 ratio can improve the surface passivation quality and solar cell performance. The spectral response of the solar cells improved with increasing CO2/SiH4 ratios as shown in Figure 6 because of the increased optical bandgap of the i-a-SiO:H layer.
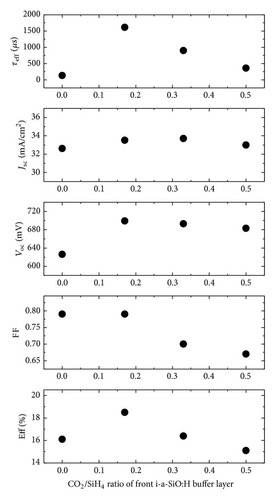
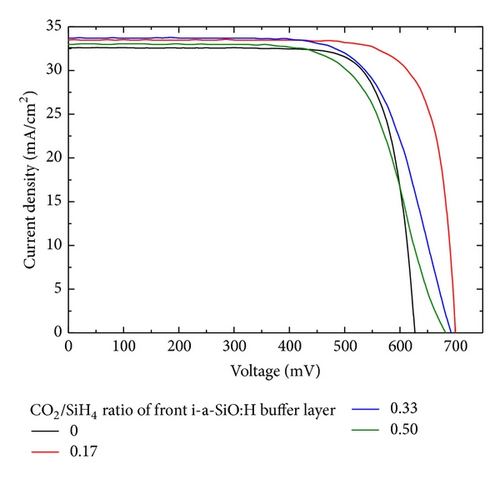
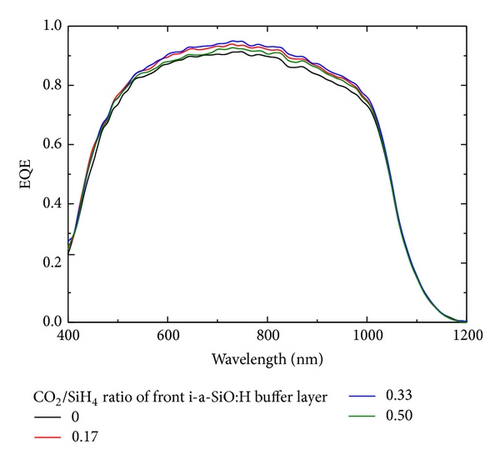
The effects the CO2/SiH4 ratio of the i-a-SiO:H front buffer layer had on the photovoltaic parameters at various operating temperatures were investigated. Figure 7 presents the normalized solar cell parameters for c-Si-HJ solar cells containing i-a-SiO:H layers with various CO2/SiH4 ratios measured in the initial state as a function of the operating temperature. The Jsc gradually increased with increasing operating temperature due to the increase in the diffusion length of the minority carriers. The FF and solar cell efficiency decreased with increasing operating temperature due to the significantly reduced Voc. The Voc decreased with increasing operating temperature because of an increase in the reverse saturation current. The normalized TC for the Voc of a solar cell with a CO2/SiH4 ratio of 0, 0.08, and 0.17 in i-a-SiO:H were −0.318%/°C, −0.314%/°C, and −0.290%/°C, respectively. Therefore, the normalized TC for η of the solar cell with CO2/SiH4 ratios of 0, 0.08, and 0.17 in i-a-SiO:H were −0.312%/°C, −0.306%/°C, and −0.301%/°C, respectively. The experimental results indicate that the i-a-SiO:H film is a promising buffer layer material for c-Si-HJ solar cells operating at high temperatures.
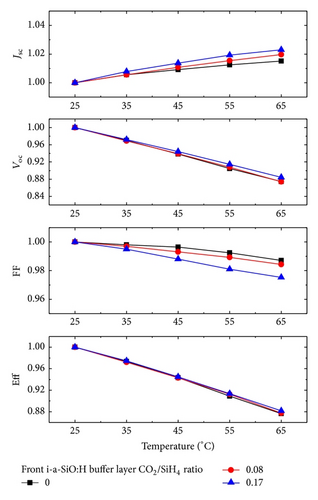
4. Conclusions
We investigated the surface passivation quality of i-a-SiO:H films for n-type silicon wafers. The τeff improved with increasing CO2/SiH4 ratio in the films. We also characterized c-Si-HJ solar cells containing front and rear i-a-SiO:H buffer layers. The thickness and CO2/SiH4 ratio for the front i-a-SiO:H buffer layer affected the Voc and FF of c-Si-HJ solar cells. Optimized solar cells exhibited better efficiencies with the i-a-SiO:H front buffer layer than with the i-a-Si:H front buffer layer. The highest total area efficiency obtained was 18.5% (Voc = 700 mV, Jsc = 33.5 mA/cm2, and FF = 0.79). The normalized TC for this c-Si-HJ solar cell efficiency was −0.301%/°C. These experimental results indicate that the i-a-SiO:H film is a promising buffer layer material for c-Si-HJ solar cells operating at high temperatures.
Conflict of Interests
The authors declare that there is no conflict of interests regarding the publication of this paper.