Geopolymers with High Ash Percentages: A Stability Study
Abstract
Wood ash (WA) is the fine residue left behind after wood combustion. Currently, only a fraction of wood ash undergoes recycling, with the majority being disposed of in landfills. Enhancing wood ash recycling can mitigate environmental harm, reduce transportation expenses, and minimize waste disposal. This study aims to investigate the stability of a geopolymer incorporating 30% wood ash as a filler material. The ashes, sourced from beech wood, are sieved and mixed with a metakaolin-based geopolymer matrix. The samples, cured at room temperature (25 °C) for 24 h, are evaluated through integrity tests, mass loss evaluation, FT-IR, and SEM analyses. The results of the integrity test and mass loss evaluation confirmed the stability of the geopolymers in water, with a mass loss of less than 1% after 56 days. The FT-IR peak analysis confirmed the occurrence of geo-polymerization and the incorporation of the ashes into the geopolymer paste. Finally, the SEM results showed the uniform surface of the samples and the good distribution of the ashes within the geopolymer network.
1 Introduction
Geopolymers (GPs), innovative materials in the field of construction, constitute a category of inorganic binders that differ from traditional Portland cement-based binders. Their uniqueness lies in the formation of polymeric networks through chemical reactions at low temperatures, often involving recyclable and low-carbon-emission materials.[1] This characteristic makes geopolymers an eco-friendly choice compared to conventional materials, contributing to mitigating the environmental impact associated with cement production.
Currently, to further reduce the environmental footprint of geopolymers, numerous research efforts are focusing on the possibility of incorporating industrial or agricultural waste into the production processes.[2-7] The use of waste as starting precursors or adding such materials to geopolymers not only reduces the consumption of virgin resources but also contributes to sustainable waste management. For example, fly ash, a by-product of coal combustion, is one of the most widely studied fillers.[3] Slag, a by-product of the steel industry, has also been extensively used as a precursor in alkali-activated systems.[4]
More recently, wollastonite, glass waste, and agricultural residues such as rice husk ash and sugarcane bagasse ash have also been incorporated into geopolymers as sustainable alternatives.[5, 8, 9] These materials not only provide silica content but also improve the workability and long-term performance of geopolymer concretes.
In this context, the present study focuses on analyzing the stability of a geopolymer incorporating 30% wood ash as a filler material (geopolymer with high wood ash content; GP-HWA). These ashes, sourced from beech wood, are carefully sieved (>79 µm) and blended into a metakaolin-based geopolymer matrix. The resulting compound undergoes a curing process at room temperature (25 °C), and comprehensive evaluations, including integrity tests, mass loss analyses, and FT-IR (Fourier Transform Infrared Spectroscopy) analyses are conducted at intervals of 7, 14, 28, and 56 days. Moreover, SEM (Scanning Electron Microscopy) analysis on the sample ages 56 days is conducted. These investigations provide insights into the stability of the materials and the evolution of the geo-polymerization process.
2 Results and Discussion
Once removed from the molds, the samples appeared solid, well-formed, and gray in color, demonstrating the homogeneous incorporation of the ashes within the geopolymeric matrix. The stability of the samples has been evaluated over time through integrity tests and mass loss measurements. After being immersed in water for 24 h, all samples, regardless of their aging, remained intact. No cracks or residues were visible in the water, which remained clear and clean. The pH of the water in which the samples were immersed was also measured and remained constant at a value of approximately 10.20 ± 0.05. The alkalinity of the water was expected, both due to the alkaline nature of geopolymers and the quantity of added filler, which being rich in CaO, can easily dissociate into Ca2+ and 2OH−.[7]
The results of the mass loss are shown in Figure 1. Samples aged for 7 days showed a mass loss of about 5.62%. However, over time, the mass loss reduced, reaching values below 1%. This confirms the stabilization of the samples over time.
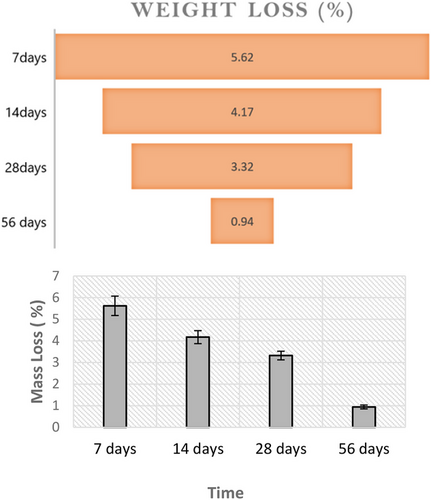
The actual geo-polymerization was assessed through FT-IR. From the results shown in Figure 2, a slight shift in the characteristic wavenumber of the asymmetric stretching of Si─O─T (T = Si or Al) between metakaolin and the samples is observed. In metakaolin, the wavenumber is recorded at 1090 cm−1, which is then shifted to 1020–1016 cm−1 in the samples. Particularly, this shift, very noticeable in samples aged for 7 days, becomes less pronounced for samples with longer aging times, indicating that over time, fewer Si─O─Si bonds are replaced by Si-O-Al bonds, confirming the completion of geo-polymerization.[10, 11]
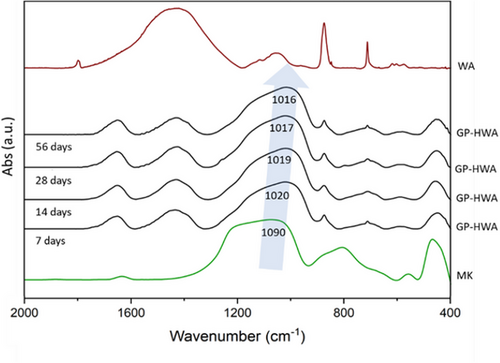
The presence of the filler within the samples is demonstrated by the peaks located at 1427, 873, and 710 cm−1, characteristic of calcium carbonate. In particular, the peak at 1427 cm−1 is attributed to C─O antisymmetric stretching vibration, the one at 873 cm−1 to CO32− out-of-plane deformation vibration, and finally, the peak at 710 cm−1 is associated with O─C─O in-plane deformation vibration.[12-14]
The SEM images of GP-HWA (Figure 33), as also demonstrated by the FT-IR, confirm the presence of the geo-polymeric network. The sample surface is uniform, with few and noticeable small fractures. The distribution of the wood ash particles within the geo-polymeric matrix is evidenced by the homogeneity of the surface, where no significant clusters or agglomerations of ash are observed. The presence of calcium carbonate, indicative of the ashes being well-incorporated into the network, is further confirmed by the distinct bright spots visible in the SEM micrograph, which reflect the scattered and uniform distribution of calcium carbonate throughout the matrix.[15]
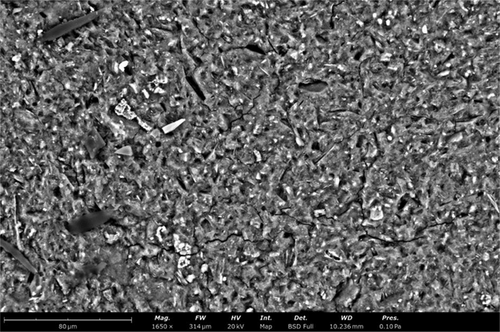
3 Conclusion
- The geopolymer samples incorporating 30% wood ash exhibit to be stable, as demonstrated by intact structures and minimal mass loss after exposure to various aging conditions.
- The consistent pH levels observed during the integrity test further support the environmentally friendly nature of these geopolymers.
- The reduction in mass loss over time signifies the gradual maturation and stabilization of the geopolymer matrix, contributing to the long-term durability of the material.
- The FT-IR analysis, revealing the characteristic shift in wavenumbers, provides valuable insights into the geo-polymerization process. The diminishing shift with increased aging times indicates a progression towards a more complete geopolymer structure.
- The SEM images visually confirm the successful integration of wood ash into the geo-polymeric network, showing a well-distributed filler and a uniform surface, thus validating the potential use of wood ash as an effective and sustainable filler material.
- These findings collectively highlight the viability of wood ash-filled geopolymers as eco-friendly alternatives in construction, demonstrating their stability, geo-polymerization completion, and structural integrity over time.
4 Experimental Section
The aluminosilicate precursor powder utilized is metakaolin (MK) sourced from IMCD Deutschland GmbH and Co. (Köln, Germany), enriched with 30 wt% of waste beech wood ash (WA) (sieved to a size smaller than 79 µm) gathered from a local restaurant in Caserta, Italy. The precursor underwent alkali activation using a blend of sodium silicate (SiO2/Na2O = 3.3, provided by Prochin S.r.l. Company, Italy) and NaOH in pellet form (Sigma Aldrich). The samples (GP-HWA) were cured at room temperature for 7, 14, 28, and 56 days.
The integrity test was conducted by immersing the samples in water for 24 h and assessing the morphology and conditions of the water in which they were immersed.
To calculate the mass loss, each sample, weighing 10 g, was immersed in C3H6O for 3 h. Subsequently, they were left at room temperature (25 °C) for an additional 3 h, and the initial mass (mi) was recorded. The samples were then immersed in water for 24 h, transferred to C3H6O for 3 h, and finally left at room temperature for another 3 h. The final mass was recorded, and the following formula was employed to calculate the mass loss: (mi – mf)/mi *100.
FT-IR analysis was conducted utilizing a Prestige21 Shimadzu instrument featuring a DTGS (Deuterated Triglycine Sulfate) KBr detector. The spectral analysis spanned from 400 to 2000 cm−1 with a resolution of 2 cm−1 (60 scans). The KBr disks employed for the analysis were prepared using 3.00 mg of sieved sample and 197 mg of KBr. Furthermore, FT-IR spectra were processed using IR-Solution and Origin 2023 software.
SEM images were obtained using the Phenoma XL G2 (Alfatest, Italy) at a magnification of 1650x and high voltage (HV) of 20 kV, utilizing a backscatter electron detector (BSD). The samples were analyzed in their native state without undergoing any surface metallization processes.
Acknowledgements
The author expresses gratitude to Prochin Italia Prodotti Chimici Industriali Srl (Italy) for generously providing the sodium silicate used in this study.
Open access publishing facilitated by Universita degli Studi della Campania Luigi Vanvitelli, as part of the Wiley - CRUI-CARE agreement.
Conflict of Interest
The authors declare no conflict of interest.
Author Contributions
All the authors contributed equally to the work.
Open Research
Data Availability Statement
The data presented in this study are available on request from the corresponding author.