Improving the Physical and Chemical Specification of Diesel Fuel Using Solvent Extraction Technology
Abstract
This research provides a new structured methodology for improving diesel fuel properties through solvent extraction. Diesel fuel is analyzed using an experimental approach, including solvent selection, extraction, phase separation, and characterization. Four solvents—furfural, N-methylpyrrolidone (NMP), propylene carbonate, and acetonitrile (AN)—are tested at diesel-to-solvent ratios. Several tests are conducted. The research process involved optimizing extraction conditions and evaluating fuel quality using Fourier transform infrared (FT-IR) and gas chromatography (GC) techniques. Extraction ratio significantly improved combustion properties, reducing residual carbon, sulfur content, and viscosity. NMP is identified as the most effective solvent, with an NMP + AN mixture providing optimal performance. This research serves as a guide for systematically designing and executing research on fuel enhancement, demonstrating solvent extraction as a viable method for refining diesel fuel properties.
1 Introduction
Internal combustion engines are one of the features of our present age and evidence of its technological progress. Through them, the thermal energy of gaseous or liquid fuel can be converted into mechanical or electrical energy. Internal combustion engines with a high compression ratio are called diesel engines [1].
Diesel engines generate power by burning liquid fuel called diesel fuel, which can be obtained from atmospheric distillation units of crude oil by fractionation. The most important property of diesel fuel is the cetane number, which expresses the quality of diesel fuel in terms of combustion efficiency and the degree of popping when burning in a diesel engine [2].
Diesel fuel contains a mixture of a wide range of chemicals from different sources, and any fuel intended for continuous operation in a diesel engine, as long as it is a mixture of chemicals that can operate a compression ignition engine, is considered diesel fuel. There are types of diesel fuel; diesel fuel refined from crude oil (petroleum diesel) is the most common and is a liquid mixture of hydrocarbons (HCs) that vary greatly depending on their source and are separated from crude oil in the distillate fraction between 200 °C and 350 °C, which corresponds to molecules containing between 8 and 21 carbon atoms. Diesel molecules are heavier and less volatile than those in gasoline and therefore have a higher flash point; for this reason, diesel fuel is safer to transport and store [3, 4].
Refineries and researchers in the world are working to improve the cetane number and other properties of diesel fuel using materials that increase fuel efficiency [5]. Moreover, the application of strict regulations on diesel engine emissions is increasing all over the world and will require reducing nitrogen oxide (NOx), COx, and HC emissions [6]. Improvement in diesel fuel specifications can be achieved by reducing the aromatic content of the fuel through hydrotreating or by adding chemical cetane improvers or by solvent extraction technology [7].
The properties of diesel fuel can be improved by adding some chemical compounds. Laurinaitis and Mickevicius [8] were able to modify the combustion performance and emissions using different chemicals consisting of n-alkanes, HCs, C10–C13, and C11–C14 to diesel fuel, and the results showed that the carbon dioxide (CO2) emissions were reduced and the specific fuel consumption was the lowest when compared with pure diesel fuel.
Kim et al. [9] studied the possibility of adding ethanol to diesel fuel at blending ratios ranging from 0 %, 5 %, 3 %, and 10 %. The results showed that blending ethanol with diesel fuel increased the maximum combustion pressure by 13.5 %, NOx emissions decreased to 93.5 % of pure diesel fuel, soot opacity decreased from 5.3 % to 3 %, and the presence of HCs decreased to 50 % of diesel fuel.
Paneerselvam et al. [10] improved the properties of diesel blended with 20 % peppermint bio-oil/diesel blend by adding di-tertiary butyl/peroxide (DTBP) and diethyl ether (DEE). The results indicated significant improvement in diesel fuel specifications as NOx emissions decreased by 10.4–9.8 %, respectively. DTBP is more effective in reducing CO2, HC, and smoke emissions.
Osman et al. [11] were able to study the effect of gamma rays on the chemical and physical specifications of petroleum diesel fuel using different absorbed doses and rates. Diesel fuel was exposed to radiation for 1.3 h using different absorbed doses ranging among 3, 6, 10, and 15 kGy and dose rates ranging among 2.27, 4.5, 7.4, and 11.15 kGy h−1. The effect of gamma rays on the organic compounds of diesel fuel was studied using gas chromatography (GC)/MS technology. The results showed that the distillation values, calorific value, kinematic viscosity, density, and flash point decreased at absorbed doses 3, 6, and 15 kGy, whereas they increased at 10 kGy. The cetane number of diesel fuel increased after exposure to doses of 3, 6, and 7 kGy but decreased at 10 kGy due to the conversion of some branched cyclic and aromatic organic compounds into linear HCs, which helped increase the cetane number to 54 and improve all properties within the limits specified by ASTM.
Simesk and Uslu [12] improved the cetane number of diesel fuel by adding 2-ethylhexylnitrate (EHN) at different ratios (1 %, 2 %, and 3 %). The results showed that adding 2-EHN had a positive effect on HCs and carbon monoxide (CO) values while negatively affecting NOx (NO2) and smoke emissions. It significantly reduced HC and CO emissions. It was found that 2-EHN can be used as a diesel fuel improver.
Ebrahiem et al. [13] were able to improve the specifications of diesel fuel by adding zinc oxide nanoparticles (ZONPs) at five different concentrations and using an ultrasonicator and mechanical homogenizer to achieve good dispersion. The results showed that adding ZONP led to enhanced combustion by reducing emissions and reducing fuel consumption, although HC was eliminated by 100 % when compared to pure diesel.
Naife [14] added different nanoparticles to diesel fuel of the Dora refinery using two types of zinc oxide (ZnO) and CeO at ratios (30, 60, 90, and 120 ppm). The results showed that adding 90 ppm to the two types gave good performance efficiency and better reduction in gas emissions, where the improvement using ZnO reached 34.28 %, whereas it reached 20 % for CeO compared to pure diesel fuel. A decrease in emissions of NOx, CO, CO2, and unburned HCs was observed, and accordingly, ZnO can be considered an improved material for diesel fuel.
Vellaiyan [15] investigated the impact of a ZnO-doped carbon nanotube (CNT) nanocomposite on ammonia decomposition in aqueous ammonia (AA) emulsified diesel fuel, focusing on both performance and emission characteristics. Diesel fuel was blended with two concentrations of ammonium hydroxide (5 % and 10 %), whereas a separate blend combined 10 % AA emulsion fuel with 100 ppm of ZnO/CNTs. The findings revealed that the high decomposition energy and latent heat absorption of ammonia contributed to a longer ignition delay. Additionally, the post-combustion reactions of the emulsion fuel led to increases in brake-specific consumption (BSC), brake-specific energy (BSE), HC, CO, and smoke opacity. However, the use of ZnO/CNTs in the AA emulsion reduced emissions, with notable decreases in NOx by 4.5 %, HC by 18.8 %, CO by 11.4 %, and smoke opacity by 5 %. In a separate study, engine performance and environmental impact were investigated by adding different concentrations of water and 1-pentanol to cottonseed oil (COB)-derived biodiesel blends. Biodiesel was manufactured by transesterification of COB, followed by analysis of its elemental composition, chemical structure, and physicochemical properties. Analysis of variance (ANOVA) results indicated that COB had the greatest impact on brake-specific fuel consumption (BSFC) (93.4 %) and emissions of NOx (55.3 %), CO (78.5 %), and CO2 (97.1 %). Meanwhile, 1-pentanol significantly affected brake thermal efficiency (38.9 %) and HC emissions (70 %), highlighting the significant improvements in engine performance and emissions reduction [16].
A recent study investigated the conversion of personal protective equipment (PPE) gowns into energy via pyrolysis, resulting in the production of plastic pyrolysis fuel (PPF) suitable for use in diesel engines. The physical and chemical properties of the PPF were characterized, and fuel blends containing 10 %, 20 %, and 30 % PPF with conventional diesel were tested in a single-cylinder diesel engine, alongside pure diesel fuel (NDF) as a baseline. The findings revealed that incorporating PPF into the fuel led to reductions in in-cylinder pressure, heat release rate, and brake thermal efficiency. Specifically, the 30 % PPF blend resulted in increases in BSFC, HC, CO, and smoke emissions by 13.8 %, 23.3 %, 10.5 %, and 4.5 %, respectively, whereas NOx emissions decreased by 5.5 %. The study suggests that further optimization of combustion performance and emission control is needed to enhance the viability of PPF as an alternative fuel [17].
Using fuel additives and different solvent extraction techniques to improve physical and chemical specifications of diesel fuel is important with respect to engine performance, engine life, and environmental pollution. When searching the relevant literature, a limited number of studies are found regarding reducing the amount of carbon and increasing the cetane number and diesel factor of diesel fuel.
In this research, the extraction technique using solvents represented by furfural, N-methylpyrrolidone (NMP), propylene carbonate (PC), acetonitrile (AN), and a mixture of these solvents is used to improve chemical and physical specifications of diesel fuel obtained from the Baiji refinery. These properties are studied using characterization techniques such as Fourier transform infrared (FT-IR) spectroscopy and GC techniques, which showed the changes in the composition of the diesel fuel under study.
-
This research presents a new experimental methodology to improve diesel fuel properties using solvent extraction, providing a systematic approach that has not been widely explored in previous research.
-
The efficiency of four different solvents (furfural, NMP, PC, and AN) and their optimum extraction ratios are investigated in this research, and the most efficient combination for fuel improvement is determined.
-
FT-IR spectroscopy and GC techniques are used to comprehensively analyze the chemical changes in diesel fuel, providing clear and detailed insights into the compositional modifications.
-
By systematically comparing the effects of individual solvents and solvent mixtures, this research provides new insights into improving diesel fuel quality, reducing residual carbon, viscosity, sulfur content, and flash point, and thus improving combustion efficiency in line with global efforts to improve diesel fuel performance while reducing emissions, thus supporting environmental sustainability.
2 Methods
2.1 Materials
The solvents used in this research are furfural, NMP, and PC supplied by Shanghai Makclin, and AN supplied by Alpha Chemika, which had the specifications shown in Tabs. 1–4 [18]. Furfural has certain disadvantages, such as oxidizing quickly and having low stability. To protect it from oxidation, it must be stored under an oil layer or in a place containing an inert gas to prevent it from coming into contact with air. Furfural is toxic and requires careful handling. NMP is a strong polar solvent, a colorless or pale-yellow liquid with an acceptable odor, a highly stable and highly selective solvent for HCs, non-corrosive to processing units, and low in toxicity. The relatively low toxicity, strong polarity, low miscibility, and reasonable prices of these selected solvents compared to other industrial solvents make them a practical choice for solvent extraction in refining applications.
Seq. | Specifications | Value |
---|---|---|
1 | Density at 15 °C Kg m−3 | 1160 |
2 | Molecular weight g mol−1 | 96.03 |
3 | Viscosity at 40.0 °C (m2 s−1) | 0.907 |
4 | Solubility % furfural in water at 20 °C | 5.90 |
5 | Polarity | 3.57 |
6 | Refractive index | 1.5261 |
7 | Melting point (°C) | −38.7 |
8 | Flash point (°C) | 56 |
9 | Boiling point (°C) | 162 |
10 | Price in US $ t−1 | 2000 |
11 | Chemical composition |
![]() |
Seq. | Specifications | Value |
---|---|---|
1 | Density at 15 °C (Kg m−3) | 1028 |
2 | Molecular weight g mol−1 | 99.13 |
3 | Viscosity at 25 °C (m2 s−1) | 1.65 |
4 | Solubility % N-methylpyrrolidone in water at 20 °C | 4.8 |
5 | Polarity | 1.47 |
6 | Refractive index | 4.09 |
7 | Melting point (°C) | −24.4 |
8 | Flash point (°C) | 95 |
9 | Boiling point (°C) | 204 |
10 | Price in US $ t−1 | 2500 |
11 | Chemical composition |
![]() |
Seq. | Specifications | Value |
---|---|---|
1 | Specific gravity at 15 °C | 1.203–1.210 |
2 | Boiling point (°C) | 242 |
3 | Flash point (°C) | 132 |
4 | Viscosity at 25 °C | 2.5 |
5 | Solubility % propylene carbonate in water at 20 °C | 1.013 |
6 | Refractive index | 1.420–1.422 |
7 | Molecular weight g mol−1 | 102.09 |
8 | Melting point (°C) | −48.8 or −55 |
9 | Polarity | – |
10 | Price in US $ t−1 | 945 |
11 | Chemical composition |
![]() |
Seq. | Specifications | Value |
---|---|---|
1 | Viscosity (Cp) at 25 °C | 0.38 |
2 | Boiling point (°C) | 80–82 |
3 | Melting point (°C) | −45 |
4 | Density at 15 °C (kg L−1) | 0.781 |
5 | Refractive index | 1.344 |
6 | Molecular weight g mol−1 | 41.053 |
7 | Flash point (°C) | 2.0 |
8 | Polarity | – |
9 | Solubility %Acetonitrile in water at 20 °C | Mixes completely in water |
10 | Price in US $ t−1 | 900 |
11 | Chemical composition | H3C−C≡N |
2.2 Instrumentation
-
Injection mode: Split
-
Injection temperature: 220 °C
-
Carrier Gas: N2/Air
-
Total flow: 25 mL min−1
-
Detector temperature: 250 °C
2.3 Procedure
A sample of diesel fuel produced by the Northern Refineries Company (Baiji Refinery) is taken, and its specifications are examined according to the methods of international standard specifications, as shown in Tab. 5.
Seq. | Specifications | Value |
---|---|---|
1 | Specific gravity at 15.6/15.6 °C | 0.839 |
2 | API gravity at 15.6 Cst | 37.15 |
3 | Viscosity at Cst at 40 °C | 3.287 |
4 | Flash point | 69 |
5 | Pour point | −9 |
6 | Sulfur content | 1.324 |
7 | (C.R) Rams (10 %Res) | 0.187 |
8 | Diesel index | 60 |
9 | Cetane number | 59.1 |
10 | Calorific value kcal kg−1 | 10 921 |
11 | Color ASTM | 0.5 |
2.3.1 Specific Gravity
The diesel fuel sample is placed in a graduated glass cylinder for testing in a stable and vertical place, and then a graduated glass hydrometer with density units is placed freely, vertically, and gently inside the diesel fuel sample, and left to settle and the density reading is taken according to the method (ASTMD 1298-99).
2.3.2 Density (API Gravity)
2.3.3 Viscosity
2.3.4 Flash Point
In this test, the Cleveland open cup device (ASTMD93, IP36) is used. The test vessel is cleaned and dried, then filled to the mark with the sample and placed in the above-mentioned device. Then, the cover is placed on the vessel. The material is heated gradually, and the thermometer reading is noted for each degree Celsius. Then the torch lever is moved so that the flame descends to the location of the evaporation hole of the sample for 1 s, with the moving lever stopping during the descent of the flame. The thermometer reading is recorded when the diesel fuel sample ignites with a single flash inside the vessel, as this temperature represents the flash point of the sample.
2.3.5 Pour Point
The diesel fuel sample is placed in a glass cylindrical jar according to the ASTMD97-57 method, then a thermometer is placed inside it so that the thermometer bulb is immersed inside the sample. Then the container containing the sample is placed in the device, and the diesel fuel inside the container is observed every 3 °C, and the temperature at which the sample does not flow is recorded, which represents the sample pour point.
2.3.6 Sulfur Content
2.3.7 Carbon Residue
2.3.8 Diesel Index
2.3.9 Cetane Number
Cetane number is calculated theoretically from the distillation intersection curve at 50 °C and specific gravity Sp.Gr after converting it to API [19].
2.3.10 Calorific Value
2.3.11 Color Test
The sample is placed in a glass jar for the color test device, which consists of a light source and two glass jars, one for the sample and the other for the standard material with which the color is compared, and a graduated circular lever containing colored glass plates with a cover with a viewing hole (ASTMD1500-64).
2.4 Proposed Diesel Fuel Solvent Extraction
- Step 1: Diesel Fuel with FF
- Step 2: Diesel Fuel with NMP
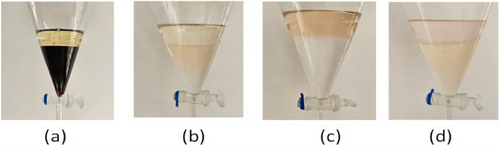
- Step 3: Diesel Fuel with PC
- Step 4: Diesel Fuel with AN
- Step 5: Diesel Fuel with a Mixture of FF + PC
- Step 6: Diesel Fuel with a Mixture of NMP + AN
- Step 7: Characterization of the Extracted Samples Using FT-IR and GC
Diesel fuel is characterized before and after solvent extraction of the extracted samples.
3 Result and Discussion
The practical results of the research show the possibility of improving the specifications of diesel fuel using the extraction technique with solvents in different proportions of FF, NMP, PC, and AN and using mixtures of solvents in different proportions as well. The diesel fuel specifications after extraction are shown in Tabs. 6–11 for comparison.
3.1 Effect of Furfural Solvent
The data in Tab. 6 indicate that the specific gravity of diesel fuel decreases from 0.8390 to 0.8101 after extraction due to the effectiveness of the FF solvent at a ratio of [1:3], which is the best ratio found, as the solvent works at this ratio to extract the aromatic and aliphatic branched materials present in diesel fuel. Therefore, diesel fuel produced after extraction became of a light type, which has a low Sp.Gr and high API, as light diesel fuel is characterized by being less resistant to flow and having a good fountain during injection into the engine.
Seq. | Specifications | Before extraction | After extraction ratio diesel fuel: FF | |||||
---|---|---|---|---|---|---|---|---|
1:1 | 1:2 | 1:3 | 1:4 | 1:5 | 1:6 | |||
1 | Specific gravity at 15.6/15.6 °C | 0.839 | 0.8205 | 0.8197 | 0.8101 | 0.8100 | 0.8100 | 0.8100 |
2 | API gravity at 15.6 Cst | 37.15 | 40.955 | 41.124 | 43.191 | 43.191 | 43.191 | 43.191 |
3 | Viscosity at Cst at 40 °C | 3.287 | 3.231 | 2.157 | 1.830 | 1.830 | 1.830 | 1.830 |
4 | Flash point | 69 | 66 | 57 | 50 | 50 | 50 | 50 |
5 | Pour point | −9 | −9 | −9 | −9 | −9 | −9 | −9 |
6 | Sulfur content | 1.324 | 1.217 | 1.061 | 0.681 | 0.680 | 0.680 | 0.680 |
7 | (C.R) Rams (10 %Res) | 0.187 | 0.173 | 0.158 | 0.140 | 0.140 | 0.140 | 0.140 |
8 | Diesel index | 60 | 63 | 66 | 68 | 68 | 68 | 68 |
9 | Cetane number | 59.1 | 60.1 | 60.4 | 62.3 | 62.2 | 62.2 | 62.2 |
10 | Calorific value kcal kg−1 | 10 921 | 10 986 | 10 989 | 11 021 | 11 022 | 11 022 | 11 022 |
11 | Color ASTM | 0.5 | 0.5 | 0.5 | 0.4 | 0.4 | 0.4 | 0.4 |
This is confirmed in Figs. 2 and 3, which represent FT-IR, as well as Figs. 4 and 5, which represent the analysis of the original diesel fuel and the addition of FF to the diesel fuel using GC, as it is noted that the concentrations of aromatic compounds decreased after extraction, and as a result the percentage of carbon remaining after extraction decreased at [1:3], and the value of the decrease is fixed even with the increase of the solvent because aromatic materials are more willing to form carbon deposits on engine parts instead of evaporating. For the same reason above, the decrease in flash point value after extraction from 69 to 50 using the ratio [1:3] can be attributed to the fact that the temperature at which diesel fuel (which contains a large amount of aromatic compounds) starts to vaporize in flammable quantity is higher because aromatic compounds have higher boiling points than aliphatic compounds.
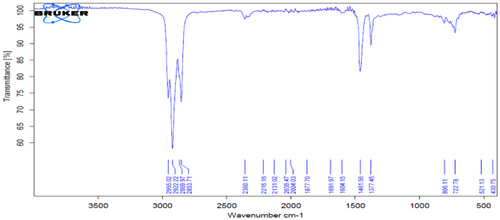
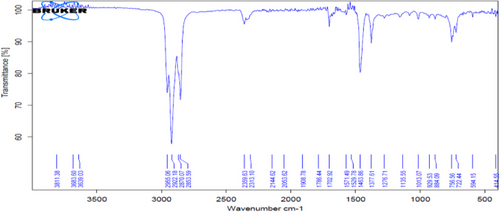
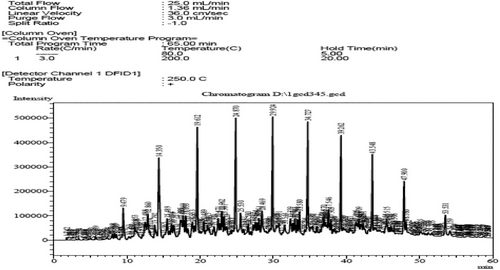
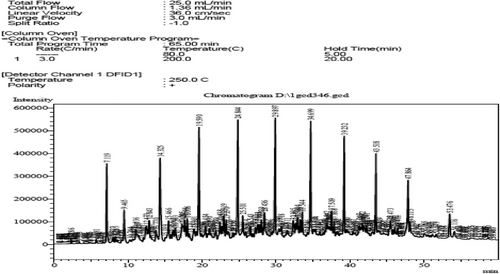
Viscosity has a very close relationship with density, as it affects the shape of the mentioned fountain during the spraying and injection of fuel when it exits the injector into the combustion chamber. Therefore, the less viscous fuel gives a relatively larger fountain and smaller and finer particles than the more viscous fuel. From observing Tab. 6, we find a clear decrease in the viscosity of diesel fuel from 3.287 Cst to 1.830 at the ratio [1:3]. This is due to the lower amount of aromatic and aliphatic branched materials (which are characterized by being compounds with high viscosity compared to the other compounds that make up diesel fuel) after the extraction process.
As for pour point, it plays a major role in the extent of diesel fuel use compared to other fuels in cold regions, where it is difficult for fuel with a high pour point to flow in the fuel channels and also creates a bad fountain when injected into the combustion chamber. When using different proportions of FF solvent, we did not find a clear and noticeable change in the pour point value, which is −9. This can be attributed to the specifications of diesel fuel produced from light crude oil compared to other types of heavy diesel fuel, such as Russian fuel, which has a flow point of −15. When extracted with furfural solvent, the flow point decreased to −12 [21].
Reducing the aromatic and aliphatic branched materials in the fuel after the extraction process led to a reduction in the percentage of sulfur in it, as the sulfur element is present in large proportions in these compounds in the form of two compounds, RSH, or the form of sulfide, R-S-R, or the form of disulfide, RSSR. This is what is observed after extraction, as the weight percentage of sulfur decreased from 1.324 to 0.681, as shown in the table above. This result is useful in extending the engine's life, as the gases resulting from sulfur compounds present in the fuel can combine with water vapor resulting from fuel combustion and lead to the formation of harmful acids that corrode engine parts.
This new method is considered economical when compared to the diesel fuel hydrogenation method used to get rid of sulfur compounds, as it requires the use of a catalyst and reactors with a specific pressure and temperature, in addition to the possibility of recovering the solvent after the extraction process and using it again.
The purpose of calculating the percentage of residual carbon is to determine the percentage of heavy materials in diesel fuel, which are more likely to form swelled compounds rather than evaporate. It is noted that the percentage of residual carbon decreased after extraction from 0.187 to 0.140. This is due to a decrease in the amount of aromatic compounds, which are characterized by their ability to form carbon deposits on engine parts, such as the combustion chamber, the upper surface of the piston, and the exhaust manifolds.
As for diesel index, it is another important property that expresses the paraffinic and aromatic content of diesel fuel and is considered one of the important properties that indicate the degree of aniline and the ignitability of diesel fuel. The lower aromatic content in fuel, a higher diesel index value, reduces the fuel's ability to generate smoke when burned. This is what is obtained as the diesel index value increased from 60 to 68.
The cetane number represents the quality of diesel fuel in terms of self-ignition and combustion efficiency, as the type of ignition is one of the most important characteristics of diesel fuel, which greatly affects the performance of a diesel engine. Cyclic compounds in general and aromatic compounds in particular are characterized by being poor quality diesel fuel, as it is observed that the value of the cetane number increased after the extraction process from 59.1 to 62.3. This is a natural result due to the low percentage of aromatic compounds in the fuel, which causes the Petra dedignition phenomenon of fuel in diesel engines, as the heating period of fuel droplets containing a large amount of aromatic materials is high, forming an explosive mixture, as HC compounds with straight, unbranched chains are considered basic and important compounds for good diesel fuel.
One of the important results reached by using FF solvent extraction at a ratio of [1:3] is the increase in the stability of diesel fuel toward oxidation resulting from the presence of oxygen in aromatic compounds, which leads to the stability of diesel fuel toward decomposition at high temperatures and thus leads to the formation of weak products in the engine.
As for the calorific value of combustion, it increased from 10 921 to 11 021 kcal kg−1. This property expresses the quality of diesel fuel, which in turn depends on the thermal stability of diesel fuel and its ability to oxidize. As for the color of diesel fuel, it is observed that it changed significantly from Grades 0.5 to 0.4, which is attributed to the removal of heavy compounds.
3.2 Effect of N-Methylpyrrolidone Solvent
This solvent is currently widely used in various countries of the world because of its high selectivity, very low toxicity, easy recovery, and no corrosion in extraction units [22, 23]. Tab. 7 shows a decrease in the specific gravity value from 0.8390 to 0.7951 after extraction. This is due to the effectiveness of the NMP solvent at a ratio of [1:3], which is the best ratio found, as the solvent at this ratio improves the quality of paraffins in diesel fuel, thus increasing the API as shown in the table above. This is observed using FT-IR technology, as in Fig. 6, and proven by GC analysis shown in Fig. 7. As a result, the percentage of residual carbon decreased after extraction at a ratio of [1:3]. For the same reason above, this led to a decrease in flash point after the extraction process, as the ratio decreased from 69 to 47.
Seq. | Specifications | Before extraction | After extraction ratio diesel fuel: NMP | |||||
---|---|---|---|---|---|---|---|---|
1:1 | 1:2 | 1:3 | 1:4 | 1:5 | 1:6 | |||
1 | Specific gravity at 15.6/15.6 °C | 0.839 | 0.8192 | 0.8073 | 0.7951 | 0.7951 | 0.7951 | 0.7951 |
2 | API gravity at 15.6 Cst | 37.15 | 41.229 | 43.775 | 46.465 | 46.465 | 46.465 | 46.465 |
3 | Viscosity at Cst at 40 °C | 3.287 | 3.104 | 2.051 | 1.753 | 1.753 | 1.753 | 1.753 |
4 | Flash point | 69 | 65 | 54 | 47 | 47 | 48 | 49 |
5 | Pour point | −9 | −9 | −9 | −9 | −9 | −9 | −9 |
6 | Sulfur content | 1.324 | 1.203 | 1.021 | 0.521 | 0.521 | 0.521 | 0.522 |
7 | (C.R) Rams (10 %Res) | 0.187 | 0.168 | 0.141 | 0.131 | 0.132 | 0.134 | 0.136 |
8 | Diesel index | 60 | 64 | 67 | 70 | 70 | 69 | 69 |
9 | Cetane number | 59.1 | 61.3 | 62.7 | 65.5 | 65.4 | 65.4 | 65.2 |
10 | Calorific value kcal kg−1 | 10 921 | 10 990 | 11 031 | 11 072 | 11 072 | 11 071 | 11 070 |
11 | Color ASTM | 0.5 | 0.5 | 0.5 | 0.3 | 0.3 | 0.3 | 0.4 |
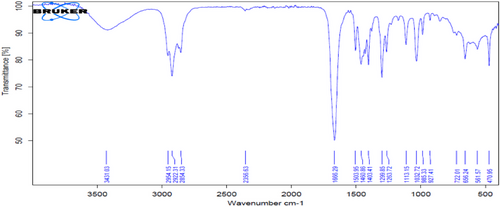
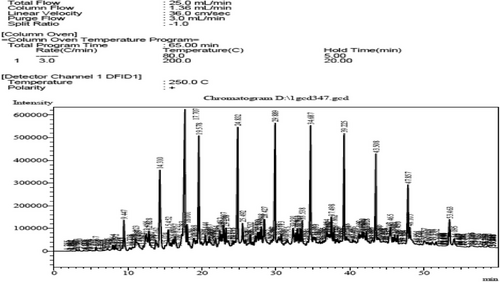
From observing the table above, it finds a clear decrease in the viscosity of diesel fuel from 3.287 Cst to 1.753, which is superior to the FF solvent when compared to it. As for the pour point, it did not find any change in the flow value, and the reason is mentioned previously. As for the weight percentage of sulfur, it decreased after the extraction process using NMP solvent from 1.324 to 0.521, which is less than the weight percentage of sulfur after extraction using FF solvent. As for the diesel factor, notice that the diesel factor increased until it reached 70, and the cetane number also increased, reaching 65.5. This is normal for removing aromatic compounds and improving the quality of paraffins. Thus, it finds that using NMP solvent for extraction is better than FF and can be used as an alternative to improve the specifications of diesel fuel produced from the northern oil refineries.
3.3 Effect of Propylene Carbonate Solvent
Polycarbonate has the advantage over other solvents of removing CO2, and PC can be used for selective treatment of H2S because it is unstable at high temperatures. Another advantage is that it does not require water washing to recover the solvent because of its low vapor pressure. Tab. 8 shows that the specific gravity value decreased from 0.8390 to 0.8033 after extraction due to the effectiveness of the solvent to the extent of the ratio of [1:3], which is the best ratio found. The decrease in specific gravity, API, and low viscosity is also evident when compared to FF and NMP solvents. This is observed using FT-IR technology, as in Fig. 8, and proven by GC analysis shown in Fig. 9. As for the carbon residues, they decreased significantly when compared to the use of NMP and FF solvents. This can be attributed to the ability of this solvent to remove CO2. We also find that the sulfur percentage decreased after extraction with this solvent. As for the flash point, the decrease is slight, and the results also showed an increase in the diesel coefficient, cetane number, and calorific value. As for the color and pour point, no change occurred.
Seq. | Specifications | Before extraction | After extraction ratio diesel fuel: PC | |||||
---|---|---|---|---|---|---|---|---|
1:1 | 1:2 | 1:3 | 1:4 | 1:5 | 1:6 | |||
1 | Specific gravity at 15.6/15.6 °C | 0.839 | 0.8312 | 0.8217 | 0.8033 | 0.8033 | 0.8033 | 0.8034 |
2 | API gravity at 15.6 Cst | 37.15 | 38.73 | 40.70 | 44.64 | 44.64 | 44.64 | 44.64 |
3 | Viscosity at Cst at 40 °C | 3.287 | 3.204 | 3.108 | 2.935 | 2.935 | 2.935 | 2.935 |
4 | Flash point | 69 | 69 | 68 | 65 | 65 | 65 | 65 |
5 | Pour point | −9 | −9 | −9 | −9 | −9 | −9 | −9 |
6 | Sulfur content | 1.324 | 1.318 | 1.300 | 1.275 | 1.275 | 1.275 | 1.275 |
7 | (C.R) Rams (10 %Res) | 0.187 | 0.163 | 0.141 | 0.122 | 0.122 | 0.122 | 0.122 |
8 | Diesel index | 60 | 65 | 66 | 68 | 68 | 68 | 68 |
9 | Cetane number | 59.1 | 60.2 | 61.7 | 63.8 | 63.8 | 63.8 | 63.8 |
10 | Calorific value kcal kg−1 | 10 921 | 10 951 | 10 982 | 11 045 | 11 045 | 11 045 | 11 045 |
11 | Color ASTM | 0.5 | 0.5 | 0.5 | 0.5 | 0.5 | 0.5 | 0.5 |
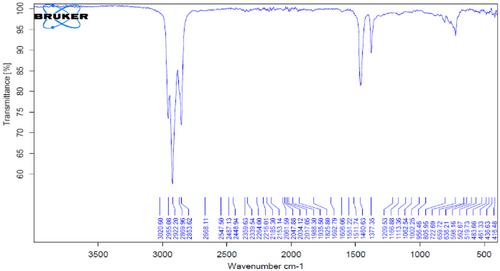
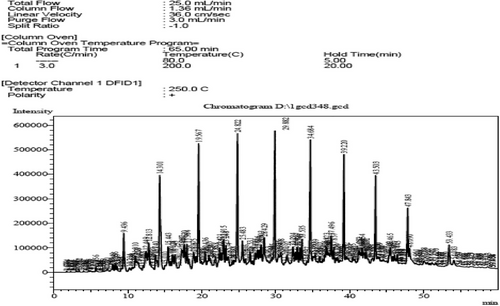
3.4 Effect of Acetonitrile Solvent
Tab. 9 data show that the drop in specific gravity from 0.839 to 0.7952, along with the increase in API gravity, is due to the effectiveness of the AN solvent at a [1:3] ratio in separating butadiene from C4 HCs and separating other HCs such as propylene, isoprene, and methyl acetylene from the HC procedure, and it is also used in special separation processes such as the extraction and separation of fatty acids from oils [24].
Seq. | Specifications | Before extraction | After extraction ratio diesel fuel: AN | |||||
---|---|---|---|---|---|---|---|---|
1:1 | 1:2 | 1:3 | 1:4 | 1:5 | 1:6 | |||
1 | Specific gravity at 15.6/15.6 °C | 0.839 | 0.8193 | 0.8125 | 0.7952 | 0.7952 | 0.7952 | 0.7952 |
2 | API gravity at 15.6 Cst | 37.15 | 41.208 | 42.653 | 46.442 | 46.442 | 46.442 | 46.442 |
3 | Viscosity at Cst at 40 °C | 3.287 | 3.118 | 2.067 | 1.918 | 1.918 | 1.918 | 1.918 |
4 | Flash point | 69 | 66 | 55 | 48 | 48 | 48 | 48 |
5 | Pour point | −9 | −9 | −9 | −9 | −9 | −9 | −9 |
6 | Sulfur content | 1.324 | 1.215 | 1.208 | 0.651 | 0.651 | 0.651 | 0.651 |
7 | (C.R) Rams (10 %Res) | 0.187 | 1.170 | 0.169 | 0.150 | 0.150 | 0.150 | 0.150 |
8 | Diesel index | 60 | 63 | 66 | 69 | 69 | 69 | 69 |
9 | Cetane number | 59.1 | 61.1 | 61.9 | 64.3 | 64.2 | 64.2 | 64.2 |
10 | Calorific value kcal kg−1 | 10 921 | 10 990 | 11 011 | 11 014 | 11 014 | 11 014 | 11 014 |
11 | Color ASTM | 0.5 | 0.5 | 0.5 | 0.4 | 0.4 | 0.4 | 0.4 |
This is observed by FT-IR technology, as in Fig. 10, and by chromatographic analysis, as shown in Fig. 11, where a decrease in the percentage of HC compounds is observed, and as a result, the percentage of carbon remaining after extraction decreased, and the value of the decrease is fixed even with an increase in the solvent, as is the case when using other solvents.
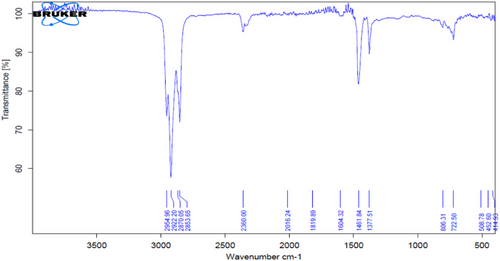
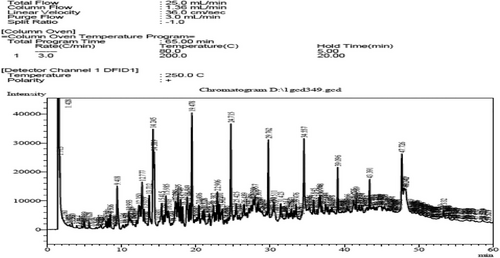
As for the flash point, pour point, diesel coefficient, and cetane number, it is noted that the changes are similar to the changes that occur in diesel fuel when using NMP solvent. Therefore, it is possible to use these two solvents instead of FF solvent to improve the specifications of diesel fuel and make it of better quality in use.
3.5 Effect of Furfural + Propylene Carbonate Mixed Solvent
Tab. 10 shows that diesel fuel specifications have been significantly improved by using a mixture of FF and PC solvents in different proportions. It is found that the best proportion for the mixture is [1:3], as the specific gravity of diesel fuel decreases after extraction, API gravity increases, and viscosity decreases significantly when compared to diesel fuel specifications before extraction, as well as when extracting diesel fuel using solvents separately. The same applies to other specifications, as the flash point value decreased, whereas the pour point did not show any significant change.
Seq. | Specifications | Before extraction | After extraction ratio diesel fuel: FF + PC | |||||
---|---|---|---|---|---|---|---|---|
1:1 | 1:2 | 1:3 | 1:4 | 1:5 | 1:6 | |||
1 | Specific gravity at 15.6/15.6 °C | 0.839 | 0.8170 | 0.8163 | 0.8091 | 0.8091 | 0.8091 | 0.8091 |
2 | API gravity at 15.6 Cst | 37.15 | 41.673 | 41.843 | 43.385 | 43.385 | 43.385 | 43.385 |
3 | Viscosity at Cst at 40 °C | 3.287 | 3.221 | 2.145 | 1.827 | 1.827 | 1.827 | 1.827 |
4 | Flash point | 69 | 67 | 50 | 49 | 49 | 49 | 49 |
5 | Pour point | −9 | −9 | −9 | −9 | −9 | −9 | −9 |
6 | Sulfur content | 1.324 | 1.324 | 1.203 | 1.053 | 0.675 | 0.675 | 0.675 |
7 | (C.R) Rams (10 %Res) | 0.187 | 0.160 | 0.140 | 0.120 | 0.120 | 0.120 | 0.120 |
8 | Diesel index | 60 | 66 | 67 | 69 | 69 | 69 | 69 |
9 | Cetane number | 59.1 | 60.4 | 62.1 | 64.5 | 64.5 | 64.5 | 64.5 |
10 | Calorific value kcal kg−1 | 10 921 | 10 999 | 11 001 | 11 026 | 11 026 | 11 026 | 11 026 |
11 | Color ASTM | 0.5 | 0.5 | 0.5 | 0.4 | 0.4 | 0.4 | 0.4 |
As for the sulfur content, it decreased significantly as a result of reducing aromatic compounds, cyclohydrocarbons, and branched compounds in the fuel due to the FF solvent and significantly reducing CO2 due to the PC solvent. As for the diesel factor, its value increased significantly from 60 to 69, which is a factor that expresses the flammability of diesel fuel, as the fuel's ability to generate smoke when burned decreased. As for the cetane number, its value increased from 59.1 to 64.5, which indicates a significant improvement in the specifications of the treated diesel fuel.
As for the calorific value, it increased from 10 921 to 11 026 kcal kg−1, which is a value that expresses the thermal stability and oxidation ability of diesel fuel. As for the color, it is noted that its value decreased from 0.5 to 0.4 due to the removal of heavy compounds. The FT-IR technique, as shown in Fig. 12, and the GC analysis used show this improvement, as shown in Fig. 13.
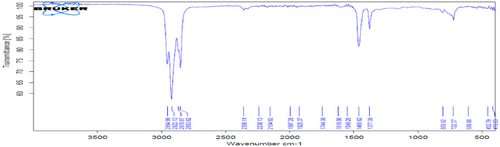
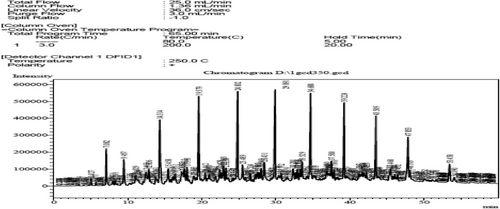
3.6 Effect of N-Methylpyrrolidone + Acetonitrile Mixed Solvent
It is clear from Tab. 11 that the diesel fuel specifications are significantly improved by using a mixture of NMP + AN solvents in different ratios, and it is found that the best ratio is [1:3], as the standard specifications of diesel fuel improve after extraction, which is the greatest improvement when compared with the specifications of diesel fuel before extraction and also when compared with the use of different solvents used in this research.
Seq. | Specifications | Before extraction | After extraction ratio diesel fuel: NMP + AN | |||||
---|---|---|---|---|---|---|---|---|
1:1 | 1:2 | 1:3 | 1:4 | 1:5 | 1:6 | |||
1 | Specific gravity at 15.6/15.6 °C | 0.839 | 0.8103 | 0.8094 | 0.7751 | 0.7751 | 0.7751 | 0.7751 |
2 | API gravity at 15.6 Cst | 37.15 | 43.126 | 43.320 | 51.080 | 51.080 | 51.080 | 51.080 |
3 | Viscosity at Cst at 40 °C | 3.287 | 3.104 | 3.005 | 2.000 | 1.841 | 1.841 | 1.841 |
4 | Flash point | 69 | 64 | 50 | 45 | 45 | 45 | 45 |
5 | Pour point | −9 | −9 | −9 | −9 | −9 | −9 | −9 |
6 | Sulfur content | 1.324 | 1.201 | 1.095 | 0.405 | 0.405 | 0.405 | 0.405 |
7 | (C.R) Rams (10 %Res) | 0.187 | 0.163 | 0.151 | 0.127 | 0.127 | 0.127 | 0.127 |
8 | Diesel index | 60 | 69 | 71 | 75 | 75 | 75 | 75 |
9 | Cetane number | 59.1 | 62.4 | 64.8 | 69.3 | 69.3 | 69.3 | 69.3 |
10 | Calorific value kcal kg−1 | 10 921 | 11 024 | 11 140 | 11 140 | 11 140 | 11 140 | 11 140 |
11 | Color ASTM | 0.5 | 0.4 | 0.3 | 0.2 | 0.2 | 0.2 | 0.2 |
Therefore, the mixture of NMP + AN solvents can be used as an excellent alternative to the solvents used in refineries to improve diesel fuel specifications, especially the cetane number. This is proven through FT-IR technology (Figs. 14 and 15) and the GC analysis of the extracted diesel fuel.
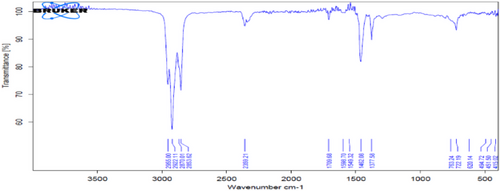
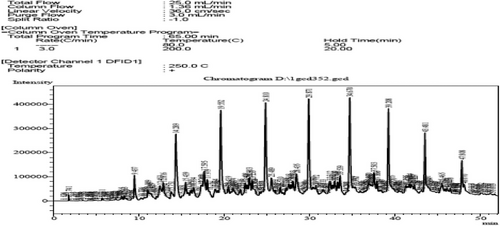
4 Conclusions
This research successfully demonstrates the effectiveness of the new solvent extraction technology in improving diesel fuel specifications and that the best ratio for using solvents is [1:3] [diesel:solvent]. It is possible to use NMP solvent to improve the specifications of diesel fuel (produced from Baiji refinery), and its advantages are that its toxicity is low and it does not cause corrosion of equipment when compared to the FF solvent widely used in refineries with its toxicity and high oxidation. An improvement in diesel fuel specifications is observed after extraction using PC solvent, which is characterized by being a non-toxic compound that causes no corrosion to metals; however, the percentage of improvement is low when compared to FF and NMP. The efficiency of AN solvent in improving diesel fuel specifications after extraction is similar to the improvement shown by using NMP. Using solvent mixtures that have proven their efficiency in improving the quality of diesel fuel, where FF + PC and NMP + AN solvents are used.
The study confirms that solvent extraction is a viable alternative to conventional desulfurization methods, offering a cost-effective and environmentally friendly approach with the advantage of solvent recovery and reuse.
Overall, NMP + AN proved to be the most efficient solvent combination for enhancing diesel fuel properties, making this method highly promising for industrial applications aimed at reducing emissions and improving fuel performance.
Acknowledgments
I extend my thanks and appreciation to the University of Mosul and the Central Laboratory of the College of Agriculture and Forestry for the facilities they provided to complete this research.
Open Research
Data Availability Statement
The data that support the findings of this study are available from the corresponding author upon reasonable request.