Digital Planning Support for Modular Logistics Plants in the Process Industry
Abstract
Modular production and logistics plants provide flexible, reconfigurable, and digital solutions to address the dynamics of specialty product markets in the process industry. They tackle high volatility and uncertainties in demand and product variety by enhancing the adaptability of planning and operations. Although most tasks and planning activities are currently time-consuming and partly carried out manually, modularization will significantly decrease the planning times for production and logistics. This contribution outlines an innovative planning process and a new planning support system for modular logistics plants that shortens the planning processes and enables short-term, virtual, and simulation-based planning activities and evaluations before implementation into the real production and logistics system.
1 Introduction
Many branches of the process industry, such as the fine chemicals and pharmaceutical industries, are facing growing uncertainty and dynamics of market developments, increasing demands for product differentiation, and shorter product life cycles [1-3]. The implementation of adaptable production concepts represents an innovation for the process industry and a radical change from previous design principles [4-6]. The modular design of these concepts allows “an improved adaptation to these dynamic boundary conditions in the dimensions of quantity output, product variety, and manufacturing location” [7]. Furthermore, these concepts enable a reduction of planning and development times [8, 9]. In order to integrate these systems into a functional operating environment and to be able to (re-)configure them quickly, they must be supplied and disposed in an adequate logistical manner and operate as cyber-physical systems according to the “Plug & Operate” principle in terms of Industry 4.0 [10-12].
In order to actually benefit from flexibility and reconfigurability by modularization, a new concept of an accelerated planning process for modular production and logistics sections is required. Therefore, this paper suggests a design of the planning process. The core of this work is the scientific investigation of the effects of modularization on production logistics in the process industry. Specifically, this work examines the effects of modularization on logistics performance according to Nyhuis and Wiendahl [13], focusing on logistics key indicators like stocks, lead times, and utilization. For this purpose, we develop a simulation-based planning support system as a tool for the implementation and simulation-based evaluation of the conceptualized accelerated planning process. The planning support system enables a case-specific (re-)configuration of production sections and areas consisting of production and logistics modules in the sense of “Plug & Operate,” allowing short-notice reactions to changing demand situations. The use of a planning support system for the modeling and evaluation of modular production and logistics as well as the associated planning process also drives the digital transformation in companies. The quantitative evaluation of a designed system serves as a powerful planning support tool, ensuring the efficiency and validation of planned plants even before their implementation. A further goal is the conceptual development of missing logistics modules.
The article follows this structure: Section 2 explains relevant basics of modular production and modular logistics as well as existing planning approaches for process industry plants. Section 3 presents the concept of an accelerated planning process. Subsequently, Section 4 deals with the planning support system, including the exemplary conceptual design of logistics modules and the creation of a module library. Section 5 presents the evaluation of the planning process with the help of the planning support system by means of a test scenario. A final conclusion summarizes the results and provides an outlook on future research questions.
2 Modular Production and Logistics in the Process Industry
Before discussing the concepts and status quo of modular production (see Section 2.1) and modular logistics (see Section 2.2), we define a “module” as a technically and organizationally separated area of a factory. Connected via well-defined interfaces, it operates as a mobile, decentralized controlled unit fulfilling a specific task and integrating material and information flows [9].
2.1 Modular Production
Conventional production systems in the process industry only meet the market complexity drivers described in Section 1 to a limited extent [10, 14]. Even though continuously operated single-product plants are very efficient, they are also largely inflexible in terms of output, product range, and relocation, whereas discontinuously operated multi-product plants offer flexibility with regard to the product range within certain operating windows but are not as efficient [10, 14]. The focus of industrial and research interests is therefore to combine the advantages of both approaches, which means modular, adaptable, and decentralized plant concepts with small to medium capacity profiles, leading to greater flexibility [5, 9].
Modularization in this context means the process of dividing a production system into modules, which provide one or more specific functions [15, 16]. The vision of the modular approach is that the individual modules can be exchanged or moved quickly and easily with existing standardized interfaces according to the “Plug & Operate” principle [9, 17]. This enables the creation of completely new production systems without the need for a new validation of the entire production process [2, 18]. Using modules enables a faster market entry time [9]. Plant capacity can be flexibly adjusted to demand by numbering modules up or down, allowing for gradual and market-oriented scaling, enabling temporal and spatial market tracking [7, 11].
In modularization, a distinction is made between physical modularization and automation modularization. Physical modularization focuses on modularizing the process engineering equipment and apparatuses into separate, encapsulated units, known as modules [9]. According to VDI2776, experts divide modular production plants into a basic structure consisting of modular plant (MP), process equipment assembly (PEA), functional equipment assembly (FEA), and components [6]. In the course of physical modularization, container solutions are being discussed in which—depending on the application—PEAs, FEAs, and components are located and together form an MP [9].
In order to automate production using modular “Plug & Operate” principles, the process chain also needs to be automated in a modularized way [3, 19]. However, conventional process control systems do not meet the requirements of modular production plants as outlined in the VDI/VDE/NAMUR 2658, a development guideline for successfully applying MPs, particularly in establishing a common interface standard [20]. A key enabler is a service-oriented architecture, where each module—also referred to as PEA—provides encapsulated process functions as services, such as starting, stopping, pausing, or holding [21, 22]. These modules are described in a functional, vendor-independent module description, the so-called module-type package (MTP), and integrated into the so-called process orchestration layer (POL), a higher level administration, coordination, and monitoring layer [3, 23]. Although the MTP thus enables the seamless integration of modules into the POL [22], the POL configures a specific MP topology in order to execute the module services provided by the PEAs in the sequence required for the production process [24, 25].
Various demonstrators and pilot projects have already proven the potential of modular production in the process industry. In research, the projects F3Factory, CoPIRIDE, and the ENPRO initiative are worth mentioning [7, 9]. Major players in the process industry, including BASF, Bayer, Evonik, Merck, Procter & Gamble, and AstraZeneca, have implemented prototypical modular production concepts [2, 3, 21].
2.2 Modular Logistics
Conventional logistics plants in the process industry offer low flexibility [26]. To meet volatile system requirements, such as variable demand quantities, product, or packaging types [5, 14], extensive technical changes are required [26]. Setup, cleaning, and maintenance measures must also be planned with sufficient lead time and lead to long downtimes [26] and underutilized capacities [27]. Because modular production can only reach its full potential if logistics plants have the same degree of modularization, research increasingly focuses on modular intralogistics solutions as they promise high transformability under volatile system requirements [26].
However, flexible, modular solutions only exist for limited areas of intralogistics systems. Researchers and developers have already conceptually created container-based logistics modules for provisioning, conveying, and storage as well as cleaning, filling, and packaging [11, 16]. As a result, Pannok et al. present a procedure for designing flexible intralogistics units for the supply and disposal of modular production systems, supporting operators in aligning their intralogistics processes with system requirements [28]. Gryczycha et al. have developed a reference process model for the modularization of production-related logistics through process standardization [29]. So far, developments focus on a flexible design of single modules [5, 11]. To ensure fast and compatible (re-)configurability in dynamic environments and to reduce planning and commissioning efforts, these systems need modular-enabled automation solutions with “Plug & Operate” capabilities [5, 11]. The following will outline the most important technical requirements of modular logistics.
The “Plug & Operate” capability of logistics modules requires compatibility through standardized automation interfaces, ensuring seamless integration on both horizontal (adjacent production and logistics modules) and vertical (control system) levels. To minimize engineering effort, integration must be simplified and automated as much as possible. The MTP concept described in Section 2.1 is also fundamentally suitable for the automation of modular production-related logistics plants [30, 31]. The logistics system adopts the basic structure of MPs by transferring so-called Logistics Equipment Assemblies, which offer their process functions as services [31]. The NAMUR recommendation NE171 outlines the automation requirements for this approach [32]. Blumenstein et al. outline the functional scope of a Logistics Orchestration Layer as a counterpart to the POL [23]. A first demonstrator has implemented this concept, focusing on rapid reconfigurability through modular automation [27]. Increasing automation flexibility enables higher mobility and flexibility by reducing assembly, dismantling, and set-up times [26]. However, mechanical and electrotechnical integration remains a challenge, and modular safety concepts must be developed to ensure machine safety.
2.3 Existing Planning Approaches in the Process Industry
Conventional planning methods rely on tailor-made process design, i.e., equipment and systems are designed for an exact operating point [9]. In contrast, MP planning adapts process parameters to standardized equipment [9], reusing cross-project planning knowledge and increasing workflow parallelization [33]. This approach enables early knowledge of available apparatuses, reducing planning time but potentially compromising process efficiency [9]. Conventional planning methods are unsuitable for shortening planning times or reducing investment costs through standardization [33]. Ultimately, it can be stated that the modular design of a plant has a significant impact on the planning process [9].
In module-based planning, the focus is on reuse of planning content and reduced times in process design resulting from the use of pre-engineered equipment [34]. The engineering of MPs consists of project-independent module-type engineering and project-dependent plant engineering [8]. Each module is designed once, including its physical design of the process step and the creation of the information technology interface to higher level systems [22]. The function of a module remains generic for various applications [22], whereas plant engineering focuses on integrating the MTP into the POL, orchestrating the services, and implementing project-specific requirements [8, 9]. This significantly reduces engineering efforts for MP construction [9, 22].
Researchers have presented various approaches to planning MPs in recent years, but almost exclusively on process engineering production. In [33], the authors present a modul-based planning approach for planning new MPs in a structured and time-efficient manner. Researchers in [34, 35] present structured approaches for the selection and configuration of PEAs for process design. The authors in [36] use a multi-criteria algorithm to select equipment modules for flexible, modular production plants with low investment costs. In [18], the authors present an approach for selecting modules from a database. The researchers in [37] consider the automated creation of an MTP skeleton from existing planning data, which they create during the engineering of a PEA.
In modular process plants, engineers reuse information and pre-engineered modules more frequently [8], accelerating engineering phases and reducing effort for final plant design [9, 18, 35]. Modularization has proven to lower planning effort, shorten time-to-market, and an increase flexibility [8]. The F3Factory project demonstrates a 25 % reduction in design effort [38], whereas another pilot application reduced engineering and commissioning efforts by more than 50 % [8, 39]. A case study indicates that a holistic rollout of modular concepts can further cut time-to-market for pharmaceutical products by an additional 50 % [40].
In the field of logistics, researchers have not identified any approaches that explicitly address the planning of modular production logistics plants in the process industry, though conventional logistics planning is time-intensive [5]. Although modularization has shown efficiency gains in production, its potential in logistics remains untapped. The need for digital planning support tools has been highlighted in the previous research [9], yet existing methods do not address the specific challenges of (re-)configuring and evaluating modular logistics plants.
3 Accelerated Planning of Modular Logistics Plants
To address this research gap, we propose an accelerated planning process tailored to modular logistics plants. Traditional planning approaches, originally developed for static systems, are not suited for the frequent reconfigurations required in modular production concepts. As highlighted in [9], there is a clear need for logistics planning assistance systems that support modular production concepts. The proposed approach enables rapid adaptation by integrating digital planning support tools that facilitate (re-)configuration and simulation-based evaluation. The digital planning support system described in Section 4 implements this acceleration of the planning process. This initially applies to both conventional and modular logistics systems equally. However, modularization itself further speeds up the planning process, as it allows the reuse of planning modules in the digital planning support system, significantly reducing planning effort and enabling a more dynamic response to changing requirements.
3.1 Requirements for an Accelerated Planning Process
The conventional planning of logistics in and around production plants in the process industry is characterized by time-consuming and partly manually performed planning efforts [5]. In addition, the supply and disposal of production plants that do not follow a modular concept are initially designed for a defined operating point and do not optimally meet current demand. This means that plants already operate in the ramp-up phase under the conditions of an operating point of maximum output, some of which is only in the distant future. Short-term adjustments to changed market conditions are difficult to implement due to lengthy and partly manually executed planning activities. Thus, each planning procedure has unique characteristics to a certain extent. Another problem is that the know-how in conventional planning processes is often personalized. In order to use the potential of modularization for production logistics plants, the procedure for planning MPs must meet various requirements.
First, researchers and developers must significantly accelerate the planning process to respond to dynamically changing situations such as frequently changing types of products, packaging units, or quantities. In order to enable structural changes such as numbering up or down or a step-by-step ramp-up, the planning of MPs must become faster. This aligns with the need to automate planning: on the one hand, because the frequency of (re-)configurations will increase and thus the absolute planning effort will rise, and on the other hand, to minimize the risk of error-prone planning. The reuse of planning content is another goal of the new planning process in order to reduce repetitive tasks. In addition, the planning process must be digitally feasible to support the planner. This means that planners can safely carry out (re-)configuration planning for MPs even with little planning experience.
For the accelerated planning of modular logistics plants, the logistics modules themselves must meet key requirements for transformability. These enablers—universality, modularity, compatibility, mobility, and scalability—are essential to ensure rapid (re-)configuration and integration within dynamic production environments [41]. Universality ensures that logistics modules can handle varying product types and packaging requirements without extensive modifications. Modularity allows for the flexible addition, removal, or exchange of functional units, supporting stepwise capacity adjustments. Compatibility enables seamless integration of modules into existing production and logistics infrastructures through standardized interfaces. Mobility simplifies the physical relocation of logistics units to align with changing operational demands, whereas scalability ensures that the system can be adapted to varying throughput requirements without major planning disruptions. Section 4.2 details how these enablers are incorporated into the conceptual design of logistics modules to ensure efficient and flexible planning.
3.2 Concept of an Accelerated Planning Process
One of the main advantages of modular production logistics is that planners can scale the system performance by numbering up or down very easily [7] and replace individual modules—for example, for maintenance and cleaning activities—very quickly. For the operator of a corresponding plant, this means that a plant does not have to be initially designed for a maximum output but can be reconfigured in case of comparatively short-term changes in the expected system output. If such a need for change arises, the operator would plan the exact production quantities required, determine requirements for reconfiguration, and then order any missing logistics modules from a manufacturer or service provider. After delivery and—compared to today—significantly accelerated implementation, the reconfiguration would be complete.
Fig. 1 visualizes the methodology of the accelerated planning process in the form of a decision tree. The planning process consists of the phases of modeling as well as simulation and evaluation, which partly run iteratively.
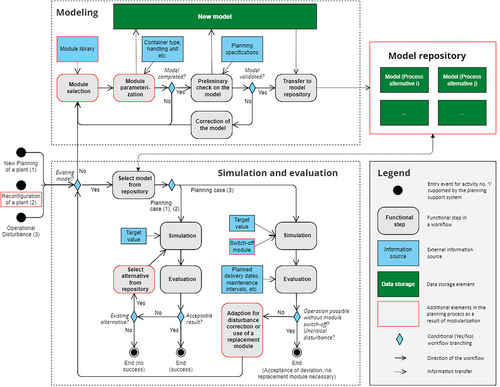
- Module data (e.g., technical specifications, capacity, compatibility with other modules);
- Production and order data (e.g., product types, demand quantities, order structure, priority rules);
- Logistics and material flow data (e.g., container types, input/output handling units, transport times, storage capacity);
- Downtime and maintenance data (e.g., module failure probabilities, repair times, maintenance schedules);
- Regulatory and economic data (e.g., approval constraints, investment costs, operating expenses).
- Technical feasibility: Sufficient capacity across all system components, compatibility, and integration of modules, complete process, and transport routes.
- Economic viability: Acceptable investment and operating costs, efficient resource utilization.
- Regulatory compliance: Fulfillment of approval procedures, safety, and environmental regulations.
Preliminary plausibility checks help to identify discrepancies such as missing transport routes, undersized storage facilities, or excessive costs. These checks are carried out iteratively each time a module is added or changed. Planning benefits from the possibility of carrying out preliminary tests quickly, as they do not require a simulation. If the model does not meet the required target values, the planner returns to an earlier phase of the modeling process to adjust module parameters, select alternative modules, or modify target values before finalizing the model and transferring it to the model repository.
The second step of the planning process includes the simulation of the modeled configuration and its evaluation and comparison with alternatives. As a result of the simulation, the planner receives information about the compliance or non-compliance with the target values on the one hand and logistical and economical key figures on the other hand to compare these with the key figures of other alternatives. The simulation generates key indicators of individual modules like capacity utilization, waiting time, idle time, downtime, and maintenance time as well as key indicators of the overall system such as throughput, stock levels, lead times, or adherence to schedules. The planner can retrieve the result reports of each simulation run for comparisons even after reconfiguration of the plant. Based on these evaluation reports, the planner decides whether a reconfiguration is necessary. For example, if orders are completed significantly after the planned completion date, the planner can reconfigure the system by changing the module parameters, malfunction data, and the order load. The planning process concludes when the system processes the order load satisfactorily.
- Capacity and efficiency: Ensure optimal utilization, avoid bottlenecks, and minimize waiting times.
- Cost and profitability: Compare investment, operational, and adaptation costs against target values.
- Performance and flexibility: Meet throughput, lead time, and production targets while ensuring adaptability to future changes.
- Stability: Assess system robustness against fluctuations and operational disruptions.
- Impact on delivery deadlines: Evaluate the effect of disturbances on planned delivery dates and production schedules.
- Maintenance intervals and downtime: Assess the impact of disturbances on planned maintenance cycles and overall plant uptime.
- Module reliability: Determine the likelihood of failure for specific modules or processes and their effect on the overall system.
- Adaptability and recovery time: Evaluate how quickly the system can adapt to disturbances, including the feasibility of temporary replacements or fixes.
- Cost of correction: Compare the cost of corrective actions, such as module replacement or downtime, against the potential impact on production or delivery.
On the basis of these decision criteria, the planner can derive further adaptations for disturbance correction. Furthermore, the planner can optimize the maintenance intervals by creating individual maintenance plans for the modules. The simulation with one or more switch-off modules and evaluation according to planned delivery dates or maintenance intervals allows the planner to decide whether a replacement module is necessary or not.
Compared to conventional logistics planning in the process industry, the workflow shown in Fig. 1 introduces significant efficiency gains through modularization, with additional steps highlighted in red. In the modeling phase, modular planning enables the direct selection and parameterization of predefined modules from a standardized module library, eliminating the need for individual design. This reduces engineering time, as planners work with pre-validated components rather than designing each unit individually. Additionally, modular planning leverages a structured model repository, allowing planners to reuse and adapt existing models instead of relying on personal expertise, which in conventional planning is often unstructured and not easily transferable. Conventional approaches also require extensive manual data management, slowing down decision-making and increasing planning effort.
The introduction of reconfiguration as a distinct planning case further accelerates the process. In modular planning, adjustments can be made by modifying existing configurations, significantly reducing planning time. In contrast, conventional planning treats reconfiguration as a full redesign, because previous planning efforts often cannot be directly reused. This results in longer lead times and higher costs for retrofitting. Additionally, modular systems standardize interfaces and compatibility, enabling “Plug & Operate” adjustments, whereas conventional systems require complex engineering to integrate new components.
Simulation and evaluation also become more efficient with modular planning. If simulation results indicate non-compliance with target criteria, alternative models can be generated quickly or retrieved from the repository without restarting the process. This enables fast iterations and optimization with minimal delay. In contrast, conventional planning often lacks integrated simulation at early stages, leading to late-stage revisions that require significant rework. In the case of operational disturbances, modular planning allows planners to quickly assess the impact of replacement modules and implement solutions with minimal downtime. Conventional planning, by contrast, lacks systematic fallback options, requiring time-consuming troubleshooting and manual adjustments, which lead to extended disruptions.
4 Digital Planning Support for Modular Logistics Plants
This section presents the developed digital planning support system. The planning support system serves as a digital tool to implement and validate the previously presented planning process. It enables the modeling and evaluation of a system, consisting of production modules and logistics modules, from a logistical and economical point of view. The use of a simulation-based, digitized solution is particularly useful here, as the planner can validate a (re-)configuration of a system digitally before implementation into the real production and logistics system.
This requires a module library that forms the basis for planning MPs and contains the necessary production and logistics modules. Currently, however, too few of the required modules are specified. Therefore, before we present the developed digital planning support system, this section first provides the conceptual specification of the modules as well as the presentation of the developed module library.
4.1 Requirements for a Planning Support System
According to the accelerated planning process and its requirements outlined in Section 3, the planning support system requires that a planner can (re-)configure an MP in an accelerated, digital, and partially automated manner with partially reusable planning content. The definition of these requirements is based on structured expert interviews with practitioners from the process industry, including plant planners and engineering professionals. Their insights reflect the specific challenges encountered in planning and adapting MPs efficiently.
- Virtual representation of modular production and logistics (as a building block library of the planning support system) for the planning of modular production and logistics sections and plants in the process industry.
- Accelerated adaptation planning (reconfiguration) and the fast rebuilding (configuration) of operational modular production and logistics sections and plants.
- Simulation-based quantitative evaluation of the modular production and logistics and a decision support for the planner based on key indicators.
These requirements ensure that the planning support system effectively addresses the challenges identified by industry professionals and aligns with the principles of modularization and digitalization in modern plant engineering.
4.2 Module Library and Conception of Logistics Modules
- Production modules: mixing, tempering, pumping, reacting.
- Logistics modules: filling, palletizing, packaging, load securing, weighing, labeling, transport.
- Supporting modules: storage, sources, sinks.
Although the module library considers the production modules as a black box in order to reduce complexity and the focus of this article, the logistics modules are dealt with in detail. However, the analysis of the state of the art reveals a lack of availability of modular, “Plug & Operate”-capable production logistics plants [9, 11]. The work of Kaczmarek et al. and Hachmann et al. supports this analysis and demonstrates the necessity of the conception of further logistics modules in modular chemical production [12, 16]. Therefore, as a further preparatory step for validating the accelerated planning process and thus the digital planning support system, we will conceptualize and specify missing logistics modules for the functions of filling, palletizing, packaging, and load securing. The reference process model presented in [28, 29] for the design of flexible intralogistics units for production supply and disposal is used as a basis for this, with which logistical tasks can be identified and corresponding module sections can be carried out.
Particular attention is paid to the transformation enablers according to Wiendahl et al. [41], which ensures that the logistics modules are designed to meet key adaptability enablers such as universality, modularity, compatibility, mobility, and scalability. These enablers are crucial for ensuring that the logistics modules can function effectively in a dynamic, modular production environment.
The logistics modules must be adaptable to various products and packaging types, enabling them to handle goods with differing physical properties or packaging requirements. This adaptability is essential for responding quickly to changing production or market demands. Furthermore, the modules should be designed as independent, interchangeable units that can be easily reconfigured or scaled to accommodate different production needs. Each module must be capable of operating autonomously while integrating seamlessly into the broader modular system. In addition to their modular design, the logistics modules must be compatible with various production systems, both existing and future. This includes ensuring standardized interfaces and communication protocols that enable smooth integration with other modules and control systems. Mobility is also a key consideration, as the modules need to be easily transportable to different production locations. Standardizing their physical size, for example, using ISO containers, allows for quick deployment in new areas, ensuring flexibility in adapting to changes in the market. Finally, scalability is an important factor, as the logistics modules must be able to expand or contract depending on fluctuations in production volume or demand. This scalability ensures optimal resource utilization and prevents inefficiencies, such as underutilized capacity or bottlenecks in the logistics process.
- Modular filling machine (vertical turbine);
- Modular inline filling machine;
- Modular bag applicator;
- Modular layer palletizer for bags;
- Modular (de-)palletizer for canisters;
- Modular robot palletizer for cartons;
- Modular packaging for small containers;
- Weighing module;
- Labeling module;
- Modular stretch hood machine.
Based on existing plants available on the market today, it will be determined at which points technologically reasonable cuts for modularization can be made, so the different plant components can be installed in suitable container formats (ISO standard container, 10-, 20-, or 40-ft). The individual containers will then be assembled to form the complete plant. At this point, reference is made to the work of Jürgensmeyer et al. They describe a transformation model for MPs and demonstrate that the path from conventional production plants to modular, smart production environments can be made step-by-step [19].
In order to prepare these modules for the use in the planning support system, they are described with regards to the transformation step by considering incoming and outgoing goods and are specified by defining simulation-relevant parameters such as the typical lead time and the throughput. In addition, the specification of the individual modules includes further parameters such as the secondary packaging materials and the space required.
To reduce complexity, we conclude the following restrictions. On the one hand, the information regarding throughput is based on existing plants available today. We can only estimate possible influences on the performance of such plants as a result of their modularization. In order to take the idea of modularization into account, we divide the individual plants into ISO containers (20-ft). The container dimensions determine the required space. Furthermore, we do not consider country-specific requirements for the individual modules.
Fig. 2a depicts an example of the conceptual design for one of these logistics modules, a modular stretch hood machine. It shows the module partition, which divides the machine into three parts. Although the first module (20-ft container) contains the foil feeding and the switch cabinet, the second module (20-ft container) contains the roller conveyors and the lower part of the foil overlayer (frame). The third module (10-ft container) on top of the first two modules contains the upper part of the foil overlayer. Fig. 2b depicts the modular stretch hood machine in container design.
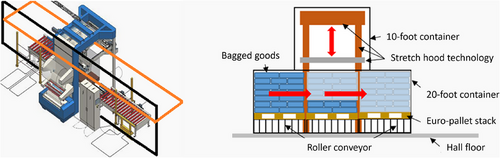
4.3 Simulation-Based Planning Support System
The planning support system contains various services for the planning and evaluation of MPs. In this way, different planning and evaluation procedures can be encapsulated as services, which can be used individually according to requirements. The planning tasks of the planning support system include, for example, resource and demand planning for forecasted or existing orders, short-term procurement and production planning, forecasting of future inventory developments as well as checking throughput, dimensioning, and performance limits. In order to fulfill these planning and evaluation tasks, the planning support system integrates with a discrete-event simulation environment, enabling the execution of simulations of the virtual production plants. The architecture of the planning support system corresponds to a client-server architecture. Therefore, the planning support system uses an “AngularJS Business-Logic” framework on the front-end side and a “Spring Boot RESTful Web-Services” framework on the back-end side. Additionally, for evaluating modularly structured plants, the planning support system interfaces with the INOSIM software suite for material flow simulation, a simulator for batch and mixed batch continuous processing systems. Via this interface, the user automatically transfers the design parameters of the considered plant to a simulation model to perform detailed quantitative analyses on the complete plant (covering both the production process itself as well as the connected modular logistics system), including, e.g., bottleneck analysis and debottlenecking, what-if-analyses, or production scheduling [42]. Section 4.4 demonstrates the functionality of simulating mixed batch production schedules and bottleneck analyses with an example.
Further services of the planning support system include the previously presented module library consisting of production and logistics modules and a graphic modeling surface for the configuration and parameterization of modular systems. Additionally, an essential feature of the planning support system includes services for persisting and loading plant models and automatically generating simulation models using the integrated discrete-event simulation engine. In order to meet the goal of a simulation-based evaluation of modular production based on key figures and decision support, the planning support system includes a service for the evaluation of simulations based on suitable key figures and their graphical representation. Furthermore, the planner can manage modules and simulation runs using different views.
4.4 Exemplary Production Scheduling and Bottleneck Analysis
The following example considers the filling of pesticides in 1-, 2-, and 5-L canisters with subsequent weighing, canister labeling, and carton packaging. Fig. 3 shows the corresponding process chain.
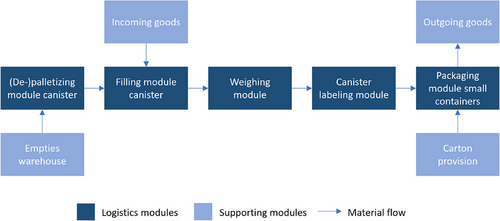
The digital planning support system provides—as a core functionality—the simulation of production schedules. Especially in the production of several product variants in one system—e.g., the filling of process-engineered products in different types of containers—product changes and the resulting different machine throughputs create a challenge to develop reliable production schedules and meet delivery dates. By simulating the production schedule, the planner can identify possible capacity bottlenecks or overcapacities, revealing the necessity of reconfiguration measures.
Therefore, Fig. 4 shows a detailed production schedule including the degree of utilization of the logistics modules for an exemplary production scenario of 1-, 2-, and 5-L canisters. The exemplary schedule illustrates that for this scenario, both the weighing and labeling modules (lines 5 and 6 in the diagram) create bottlenecks in production for this canister size mix. In contrast, the modules for depalletizing, filling, and packaging experience idle times.
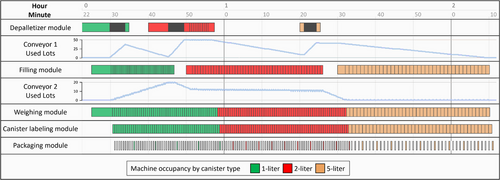
5 Evaluation
This section deals with the evaluation of the accelerated planning process for MPs by testing the developed digital planning support system on a test scenario. The core of the evaluation is the simulation-based investigation of the effects of modularization on production logistics. Therefore, we carry out the testing of the digital planning support system based on key logistics indicators such as quantity output, throughput, availability, utilization, stocks, and lead times. We use a modularized system as a basis, which we reconfigure by numbering-up certain modules. By means of simulation, we determine the effects of numbering-up on the logistics indicators mentioned above. We perform simulations for varying parameters such as order data as well as product and container types. Then we use the key indicators generated from the reconfigurations for the subsequent comparison with the key indicators of the respective original configurations to check the plausibility of the planning support system. For this purpose, we present the testing of the planning support system by a test scenario based on a common application of modular logistics derived from expert interviews and workshops. Prior to this, we formulate hypotheses on the effects of modularization on production logistics in the process industry.
5.1 Hypotheses on the Effects of Modularization on Production Logistics
-
Modularization in production logistics leads to an increase in plant utilization because capacities can be adapted to changing market conditions.
-
Modularization reduces the order backlog due to increased flexibility corridors of the overall system.
5.2 Testing the Planning Support System
The evaluation uses a test scenario that includes selected value-added sections of the process industry, for which the use of modular logistics plants is likely. For example, modular logistics plants are a promising approach for the filling of chemical products in the construction industry. In the test scenario, we consider the filling of cement into 25 kg bags with subsequent palletizing and load securing. We examine the influence of a fluctuating order volume due to a volatile market demand on the necessity of a reconfiguration of the system. Fig. 5 shows the corresponding process chain as well as the plant layout. In the initial situation, the system contains one filling module. We assume that the cement to be filled represents a resource, which is always available, so the silo (“incoming goods”) never runs empty. The aim is to estimate the critical order load of the system and to identify capacity bottlenecks. Therefore, we examine the planning objectives “order backlog” and “plant utilization” in this test scenario. The simulation in this test scenario uses data based on a detailed and real order load, which is an input variable of the planning support system. The order load extends over a period of 6 months and thus represents a sufficiently representative period of time.
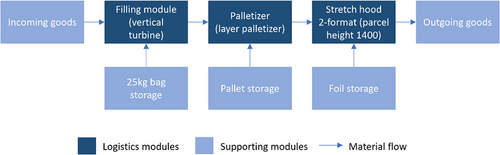
The evaluation of the simulation results generated via the integrated discrete-event simulation engine in the initial situation shows that the filling module is working at 100 % capacity, and the order backlog, shown in Fig. 7, builds up continuously and cannot be processed. Therefore, the filling module represents a capacity bottleneck in the initial situation, which necessitates the reconfiguration of the system. Following the workflow mapped in the UML diagram (see Section 3.2), the planner first analyzes the simulation results in comparison to the planned target values, such as delivery deadlines, throughput rates, production costs, and maximum allowable inventory levels. Observing that the results do not meet the planned targets, the planner identifies the filling module as a bottleneck. This leads to a return to the modeling phase, where the planner modifies the configuration by integrating a second filling module with the same capacity profile. The reconfigured model is saved as a model alternative before the planner proceeds to the simulation step again, loading the new configuration and running the simulation under the same conditions. Fig. 6 shows the process chain and the plant layout of the reconfigured system.
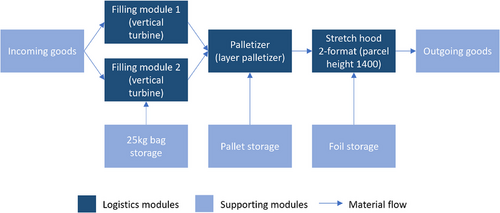
The renewed evaluation of the simulation results shows that the utilization of the downstream palletizing and stretch hood modules approximately doubles compared to the initial situation, see Fig. 8. This occurs because we supply these modules with material from two filling modules after we reconfigure the system. This aligns—according to hypothesis 1—with the expectation that numbering-up in consequence of modularization leads to an increase in capacity utilization. The capacity utilization of the two filling modules is 100 % each, i.e., the total capacity remains insufficient to complete all orders on schedule. However, the reconfiguration positively affects the order backlog, as shown in Fig. 7. The average order backlog reduces significantly, and the maximum order backlog also decreases by more than 50 % by using a second filling module. Following the iterative workflow, the planner once again compares the results to the target values and determines that the filling process remains a bottleneck. Consequently, the planner would repeat the process, adding a third filling module, re-running the simulation, and evaluating the impact until an optimal configuration is achieved.
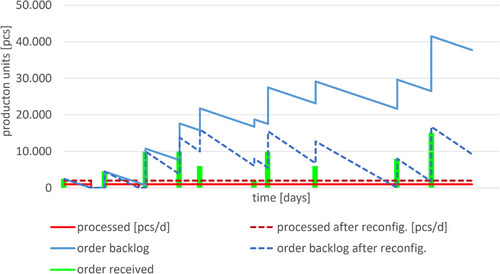

5.3 Summary of Simulation Results and Comparison to Hypotheses
The presented test scenario investigates the effects of a fluctuating order load on a modularized system. The analysis of the plant utilization shows that the filling module operates at 100 % in the initial situation and thus represents a capacity bottleneck, whereas the palletizing module and the stretch hood module are significantly less utilized. Reconfiguring the system by adding a module to the bottleneck process shows that the capacity of the bottleneck process specifically increases, and the utilization of all other modules also increases. In a non-modular setting, we would duplicate the entire system, thus unnecessarily multiplying the capacity of processes not operating at full capacity. The test scenario demonstrates that doubling the bottleneck capacity improves the utilization of other processes. Thus, the simulation results from the test scenario confirm the first hypothesis, “modularization increases plant utilization,” in the analyzed case.
In addition, the test scenario investigates the effects of numbering-up in the course of modularization on the order backlog. The simulation results show that reconfiguring the system by adding a module to the bottleneck process has a positive impact on the order backlog. The maximum order backlog decreases by more than half, and the average order backlog also decreases significantly. By making plant capacity more flexible through modularization, we can react to fluctuating market demands. As a result, the system processes the order backlog more quickly, as shown in the test scenario. Overall, this means that we confirm the second hypothesis “modularization reduces the backlog of orders” in the case of the test scenario.
In conclusion, the evaluation shows that the planning support system fully maps the required main functions described in Section 4.1. The planning support system thus offers the possibility of planning, (re-)configuration, and evaluation of modular logistics plants with high usability and graphical support. The validation of the correct functioning of the planning system and the simulation-based results show that the concept of the accelerated planning process meets the requirements for the planning procedure for MPs in the process industry.
However, as introduced in Section 4.4, the functionality for production planning and bottleneck analysis still requires further development to address fluctuating demand and sequence planning in modular process industry setups. Addressing these gaps, recent research highlights relevant approaches. The authors of [43] investigate batch production scheduling using mixed-integer linear programming, proposing a multi-step decomposition approach to enhance computational efficiency—a concept that could be extended to modular production environments. The work of [44] integrates sustainability aspects and production variability in multi-level chemical processes, offering insights into balancing economic, environmental, and operational trade-offs under uncertainty. Lastly, [45] focuses on lot-sizing challenges in the chemical industry, considering parallel processes, inventory constraints, and production flexibility, all of which are critical factors in managing fluctuating inputs. These studies provide a foundation for expanding the planning support system to incorporate demand-driven sequence planning and adaptive scheduling mechanisms.
6 Conclusion and Outlook
MPs are currently in the focus of developments in the production areas for specialty products in companies of the process industry. They respond to the current challenges of market dynamics with flexible, adaptable, and digitalized solutions.
Due to the increasingly shorter reaction and adaptation times of production and logistics systems enabled by these solutions, the necessary planning times for production and logistics also decrease. In contrast, the time-consuming and often manually executed planning poses a major challenge nowadays. Therefore, we present a newly developed accelerated planning process and a newly developed logistic planning support system. These shorten the planning processes and enable short-term virtual and simulation-based planning without direct transfer to the real system. This supports logistics planners, reduces effort, and minimizes risks.
The new planning process meets the requirements for a partially automated and digitalized procedure with reusable planning contents. This leads to a significant streamlining and acceleration of the planning process. The automation by the simulation-based evaluation as well as the digitization by the planning support system lead to advantages in the usability of the planning process. The developed planning support system has proven the feasibility and advantages of accelerated planning and evaluation of MPs. The presented test scenario demonstrates that numbering-up as a consequence of modularization has positive effects on logistical performance indicators. Thus, MP structures enable production logistics systems in the process industry to better adapt to changing market conditions and lead to an increase in plant utilization. Likewise, modularization leads to a reduction in the average as well as maximum order backlog. Modularization thus leads to an increase in the flexibility of the overall system. We tested the validity of these statements by means of simulation for a realistic test scenario.
Future research aims at the effects of modularization on the adherence to production schedules and thus the on-time delivery of production orders by flexibly adjusting capacities in the event of market fluctuations and plant malfunctions. Here, researchers must examine to what extent modular systems are able to maintain their operational capability in the event of a malfunction and at which critical order load the system can continue to operate with a reduced capability or when the provision of a replacement module is advantageous. A key focus will also be on advancing production planning methods to address fluctuating demand and optimize sequence planning in modular setups, ensuring efficient utilization of logistics modules and minimizing bottlenecks. Subject of further investigations is also the evaluation of the digital planning support system regarding software quality criteria such as robustness, reliability, and efficiency as well as usability.
Acknowledgments
This publication was made in the course of the research project “LEGOLAS—Planungsassistenzsystem für modulare Industrie 4.0 Anlagen in der Prozessindustrie” with EU funds within the framework of the funding guidelines for research, innovation, and technology of the State of North Rhine-Westphalia (FIT) under the aid number N 114/2008 as well as the European Regional Development Fund (EFRE) as part of the Objective 2 Program 2007-2013.
Open access funding enabled and organized by Projekt DEAL.