Assessment of Homogeneous and Heterogeneous Catalysts in Transesterification Reaction: A Mini Review
Abstract
The utilization and production of biodiesel have seen a significant increase in recent years due to its numerous advantages over other biofuel products. Biodiesel can be produced through various methods, including transesterification, direct mixing, microemulsion, and pyrolysis. Among these, transesterification is the most commonly employed method and utilizes three types of catalysts: enzymatic, homogeneous, and heterogeneous. While enzymatic and homogeneous catalysts are effective, they also present drawbacks, such as costly purification steps and high water and oil consumption. Heterogeneous catalysts, on the other hand, are more favorable as they mitigate these negative aspects. Some challenges still exist with heterogeneous catalysts, but they can be overcome by manipulating their structure. The use of heterogeneous catalysts not only reduces the overall cost of the reaction but also renders the process more environmentally friendly. The present study provides a comprehensive overview of biodiesel, including its characteristics, production methods, and specifically, the use of heterogeneous catalysts and their supports in biodiesel production. In addition, it examines the impact of these catalysts on the production process and the parameters that affect the yield.
1 General View on Biodiesel
Biodiesel is an essential component of sustainable development efforts aimed at creating a cleaner future. It is a mono alkyl ester (fatty acid methyl or ethyl esters (FAMEs) of long-chain fatty acids found in vegetable oils and animal fats. These resources had processed as triacyl-glycerides (TAGs), also known as triglycerides. Biodiesel can be used and distributed in existing infrastructure and blends of traditional fuels. In contrast, other alternative fuels such as Liquefied Petroleum Gas (LPG), require new distribution systems to be placed. The ecological benefits of biodiesel are also significant. It was primarily used for its ability to reduce pollutants emissions. Currently, the main focus of biodiesel production is its low greenhouse gas emissions and its positive impact on the environment. Furthermore, biodiesel usage with blends of vegetable oil reduces CO2 emissions, making it a cost-effective and efficient alternative to traditional fuels in the long term. Biodiesel feedstocks are primarily composed of straight vegetable oils (SVO), which include both edible and non-edible recycled waste oils, by-products of edible oils, and animal fats 1, 2.
Due to feedstocks diversity, biodiesel classifies into three generations: 1st generation had produced from edible SVOs. 2nd generation had developed from non-edible oils. 3rd generation had gotten from recycled fuels or waste oils and animal fats. Most of the biodiesel used today is from the 1st generation. The criteria that researchers consider while selecting the feedstock are the availability of the product, oil quality (configuration), cost, and the output's self-life. Researchers 3 detected greater than 350 oil-bearing plants that would be utilized to develop a new biofuel harvest every year. The categorization of the feedstocks is given in Tab. 1.
Biodiesel resources |
||||||
---|---|---|---|---|---|---|
Edible Oils |
Non-edible oils |
|||||
Palm oil |
Crops oil |
Animal fat |
|
|
|
|
Rapeseed oil |
Jatropha curcas oil |
Mutton tallow from rendered sheep |
Insect oil |
Sewage sludge |
Waste cooking oil |
Microalgae oil |
Corn oil |
Calophyllum inophyllum |
Pork lard obtained from pork rendering |
||||
Sunflower oil |
Mahua indica |
Chicken fat |
||||
Soybean oil |
Croton megalocarpus |
|
To define biodiesel, some properties have to be known. Because it has a significant effect on the dimensioning of biofuels and the technological particularities of the supply organs, density is considered one of the main characteristics of biofuels. Moreover, on an installed system, the usage of biofuels in different densities would lead to some variations in the combustion properties with a knock-on maximum power, efficiency, and pollutant. Viscosity is another essential characteristic of biodiesel because it impacts the function of the injection system. Comparing biodiesel with conventional fossil fuels detected that biodiesel has an elevated molecular mass and chemical configuration. Acid number (AN) is the amount of free fatty acids placed in the fuel sample and AN unit is inclined by mg KOH/g-oil. An excess acid number creates corrosion in the engine's distribution channels and this high AN is caused by high free fatty acid content. AN had been utilized as the indicator of the quantity of lubrication degree as well 5. Flashpoint (FP) is the lowest temperature at which the application of a test flame ignites a portion of vapor under specified test conditions. In general, biodiesel FP's is higher than 150 °C and for diesel is between 55–65 °C. Higher FP ensures safer storage and transportation of the fuel. Cloud point (CP) is the minimum accomplishable temperature presented for fuel when it firstly begins to crystallize and make a cloudy outlook. CP is useful for controlling the fuel at low temperatures. Pour point (PP) performs the lowest temperature which biodiesel begins to proceed when it is cooled, without stirring under standard conditions. Both PP and CP of diesel fuel are often lower than those of biodiesel fuels. Cetane number (CN) is used to determine the capacity of diesel to self-ignite on a scale of 0 to 100. It measures the ability of the oil to ignite under pressure. This index characterizes the time between injection and combustion. The higher value indicates that the fuel is easily flammable.
The specifications for the biodiesel are outlined by ASTM D 6751 (in the U.S.), EN 14214 (in the European Union), IS (in India), etc. All biodiesel fuels should satisfy these specifications. These standards fix guidelines for testing biodiesel fuels and describe applicable values for various chemical and physical characteristics of oil consecutively to use within the engine. Several of the main chemical and physical characteristics of fuel are kinematic viscosity (mm2s−1), oxidation stability, glycerol content (% m m−1), CN, sulfur amount, PP, acid number (mg KOH g−1oil), boiling purpose (°C), cloud point (°C), flash point (°C), density (kg m−3), calorific value (kJ kg−1), etc. are lined in these specifications 6. In Tab. 2, the standard values for biodiesel and petrodiesel are given.
|
Biodiesel standards |
Petrodiesel standards |
||
---|---|---|---|---|
Properties |
EN 14214 |
ASTMD-6751 |
EN 590 |
ASTM |
Method – value |
||||
Viscosity @ 40 °C [mm2s−1] |
3.5–5.0 |
1.9–6.0 |
2.0–4.5 |
ASTM D445 – 2.0–4.5 |
Flash point [°C] |
> 120 |
> 130 |
> 55 |
ASTM D957 – 60–80 |
Density @ 15 °C [kg m−3] |
860–900 |
880 |
820–845 |
ASTM D1298 – 820–860 |
Sulfur content [mg kg−1] |
10 |
50 |
10 |
– |
Acid value |
< 0.50 mg KOH/g |
< 0.50 mg KOH/g |
7 % (v/v) |
– |
Water content |
< 500 mg kg−1 |
< 0.5 v/v, % |
< 200 mg kg−1 |
ASTM D2709 – max. 0.05 % mass |
Cetane number |
> 51 |
> 47 |
> 51 |
ASTM D4737 – 46 |
Oxidation stability |
Min 6 h |
Min 3 h |
< 25g m−3 |
ASTM D2274 – max. 25 mg L−1 |
Iodine value |
< 120 g/100g |
– |
– |
– |
Free glycerin [% (m/m)] |
< 0.02 % |
< 0.02 |
– |
– |
Total glycerin [m/m%] |
< 0.25 |
< 0.24 |
– |
– |
Emissions from biodiesel are low compared to petrodiesel. For instance, biodiesel has a 50 % low ozone depletion potential due to its hydrocarbon emissions. Additionally, sulfur emissions and sulfur oxides, which are major contributors to acid rain, are significantly reduced when using biodiesel compared to traditional diesel fuel. The produced carbon monoxide from biodiesel is 48 % less than the one from diesel.
Biodiesel production is increasing worldwide. According to Fig. 1, the United States of America (USA) remarked the highest rate of biodiesel production globally. It reached 6.9 billion L of biodiesel in 2018. Brazil comes in second place reaching 5.4 billion liters while Indonesia's production rate was 4.0 billion L.
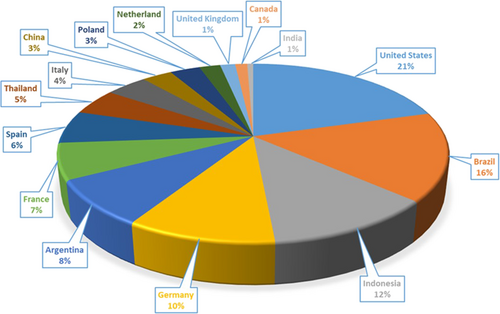
It is emphasized in the literature that biodiesel production, especially due to environmental sensitivity, is very important. Although the industrial use of kinetically fast-homogeneous catalysts is common, it creates a bottleneck when the separation of the catalyst from the product is considered for the transesterification reaction and this phenomena creates a conflict between production demands and environmental issues. Therefore, this study is prepared to highlight the advantages of the catalytic transesterification method for biodiesel production. Considering the reaction rate and production capacity, the scope of this study is limited to the comparison of homogeneous and heterogeneous catalysts in the transesterification reaction.
2 Biodiesel Production
The growth in energy and environmental challenges caused by the reliance on fossil fuels is parallel to the increase in population. However, it provides an opportunity for researchers to investigate new alternative energy sources 8. Alternative energy resources refer to any energy source that can be used as an alternative to fossil fuels. Biodiesel is one the alternatives which is a mono alkyl ester of long-chain fatty acids produced by the interaction of vegetable oils or animal fats with short-chain alcohols. Biodiesel is considered a crucial renewable and sustainable energy resource. For efficient usage of vegetable and animal oils as feedstocks for biodiesel production, it is necessary to decrease the high viscosity and to improve volatility. There are four methods 9 for biodiesel production, including direct mixing, pyrolysis, microemulsion and transesterification, which is the most commonly used method. In direct mixing, a mix of oils (vegetable or waste frying oils) with diesel fuel is used in specific proportions, and the viscosity is decreased to the desired value. B20 fuel – produced by mixing 20 % vegetable oil with diesel fuel – is determined costly, and its performance is similar to diesel fuel. Vegetable oils such as safflower, soy, peanut, and rapeseed oil are preferred in the industry 10. The pyrolysis process corresponds cracking the bonds of high carbon hydrocarbons to obtain smaller molecules to decrease the viscosity. Although the viscosity is reduced successfully, the fuel is compatible with diesel fuel features. High energy consumption and its unprofitable price make this process unfavorable in industrial practices 11. Emulsification is converting one or more organic liquid microstructures (sizes between 1–150 nm) with balanced distribution. Decreased viscosity and improved spraying properties can be obtained. However, this process has negative effects on the produced fuels. A decrease in the thermal value negatively affects engine efficiency due to the type of alcohol they contain 12. Pyrolysis and emulsification have several unacceptable effects on the quality of the product. They can cause carbon deposits and increase of viscosity. They bring out partial combustion and undesired byproducts, these byproducts are alkanes, alkenes, alkadienes, aromatic compounds, and carboxylic acids 13. A transformation process in which the glycerol-based vegetable and animal oils constitute the triglycerides, and the alkyl radical in the alcohol used got replaced by the glycerol is named as transesterification. In other words, it is the esterification of fatty acids with alcohol in the presence of a catalyst. In Fig. 2, a schematic diagram of the transesterification process is given.
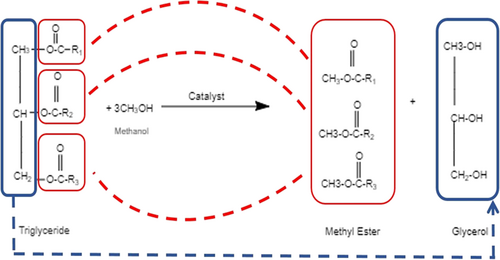
Stoichiometrically, while one mole of oil is used, three moles of alcohol are needed. The product is 3 mol of fatty acid alkyl monoester (biodiesel) and the byproduct is one mol of glycerol. Fig. 3 shows the mass balance of a stoichiometric transesterification reaction. General conditions for transesterification reactions are 60–70 °C, atmospheric pressure, and 90 min.
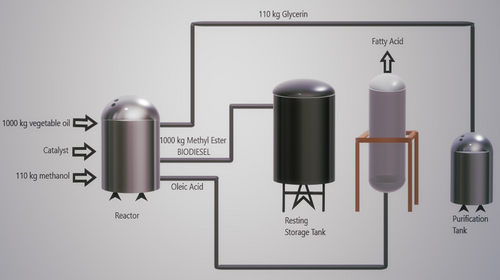
In accordance with the International American Society of Testing and Materials (ASTM) standards 9, 14, the amount of glycerol contained in biodiesel should not exceed 0.24 % of the product; that is, the value of purity of biodiesel is the most essential aspect in the process. The variety of alcohol, oil to alcohol ratio, quantity of free fatty acids, reaction conditions and the type of catalyst in the reaction, play a determinative role in obtaining the necessary purity and yield from biodiesel fuel.
The most used alcohol (during transesterification) are methanol, ethanol, propanol, and butanol. Researchers studied the variations among them, and different values had obtained in terms of kinetics and product diversity. Canakçı et. al. 15 studied acidic catalytic reactions to investigate the effect of alcohols. At room temperature, a solution of methanol, 2-propanol, 1-butanol, and ethanol with sulfuric acid (3 %) had been prepared. The solution was added to soybean oil at 60 °C, 45 °C, and 25 °C at atmospheric pressure. After reaction for 48–96 h, they concluded that branched structure alcohol, butanol, exhibited the lowest conversion.
The total of free fatty acids and the influence of water are two of the most essential parameters that inhibit transesterification. The amount of water affects more negatively than the existing free fatty acid. The conversion yield decreases as the acidity of the oil increases. During esterification, the presence of water in the oil causes soap production and rendering the catalyst useless. The formation of soap causes difficulties such as increasing the viscosity, formation of gel. One other problem is purifying process that separating the soap from reaction medium and connected to separation step, washing process causes an increase in production costs.
In a stoichiometric transesterification reaction, as mentioned before, one mol of glycerol is converted into three moles of fatty acid when one mol of triglyceride combines with three moles of alcohol. Therefore, another critical consideration is the alcohol-to-oil ratio. Tomasevic et. al. 16 studied the effect of molar ratio on ester conversion by conducting a study on biodiesel production using frying oil. 1.5 % and 1 % as a catalyst, NaOH and KOH, respectively, at 0.5 % mass ratios, they examined ester conversion at 25 °C and 30 min at 4.5: 1, 6: 1, and 9: 1 molar ratios. As a result of the study, the impact of the molar ratio was more than the impact of the catalyst. The molar ratio of methanol to vegetable oil is one of the most fundamental variables that affect ester formation because the yield and the viscosity of produced ester depend on it. According to their study, maximum conversion to the ester could be achieved by a molar ratio of 6:1.
Çanakçı et. al. 17 investigated the factors that affect the esterification of oils with a high range of free fatty acids. They prepared a solution of methanol and potassium hydroxide (1 %) at room temperature and performed an 8-h reaction using a 6:1 molar ratio. The temperature of transesterification reaction was controlled according to the types of alcohol and oil presented. Encinar et. al. 15 carried out the reaction without changing the reaction time for the temperatures 25, 40, 55, and 60 °C, and the ester yield varied by 86, 90, 93, and 94 % respectively. Although the temperatures were limited by boiling point of alcohol, they observed an increase in the yield by increasing temperature.
3 Catalysts in Biodiesel Production
A catalyst is a substance used in chemical reactions to accelerate and direct the process. Biodiesel manufacturing had been developed and improved by researchers 18 utilizing three types of catalysts: enzymatic, homogenous, and heterogeneous. In Fig. 4, both negative and positive properties of the catalysts in transesterification are given.
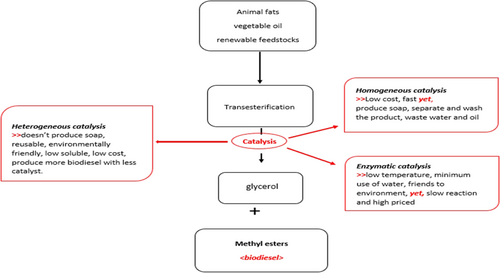
3.1 Enzymatic Catalysts
Utilizing enzymes as a catalyst in the production process of biodiesel has some pros compared with other catalysts in different chemical processes. Producing the glycerol with the minimum amount of water, applying the procedure at low temperature with high yield and using the enzymes as a catalyst is eco-friendly 19. The enzymatic catalyst used in biodiesel production is lipase. It can catalyze both transesterification and esterification in one stage 20. Although the enzyme catalysts exhibit high yields, they have a high cost 21, 22 and they are sensitive to high temperatures where the reaction rate is low. These disadvantages make the enzymatic transesterification reaction unattractive due to the feasibility of the process.
3.2 Homogenous Catalysts
The biodiesel production reaction by homogeneous catalysts can be managed in a short period. Studies 23-26 indicate that under moderate conditions it can be produced in 60 min in average. The catalyst type (acidic or alkaline) can vary according to the free fatty acid content of the oil. If the oil has high free fatty acid with excess water content, acid catalysts (phosphoric acid, sulfuric acid, hydrochloric acid, or organic sulfonic) are preferred. Fatty acids perform saponification reaction faster than the transesterification reaction when alkaline catalysts are used. After the reaction, the neutralized product is esterified by using an alkali catalyst. Moreover, KOH, NaOH, CH3KO, and CH3ONa are samples of alkaline homogeneous catalysts and they are favorable in industrial practices because of their economic costs 27. However, utilizing homogeneous catalysts create a waste of oil because they get merged in the product during the process. The separation 28, 29 of homogeneous catalysts from the product is problematic. The separation and purification processes like washing and distillation 30-32 cause a rise in the expense of the operation. Additionally, according to the high acidic environment, the materials used in the process should resist corrosion. Additionally, using them in biodiesel production leads to undesired soap production 33.
Bilgin and co-workers 34 studied the variations of KOH and NaOH as catalysts in biodiesel production to compare the viscosity and efficiency. As shown in Tab. 3, they found that various parameters in the production process affect the physical and chemical properties of biodiesel.
Parameter |
Variation of efficiency |
Variation of viscosity |
Change of viscosity when the amount of the parameter is excessive |
Change of efficiency when the amount of the parameter is excessive |
Reference |
---|---|---|---|---|---|
Catalyst amount |
Increasing |
Decreasing |
Increasing |
Decreasing |
34 |
Reaction temperature |
|||||
Alcohol/oil molar ratio |
|||||
Reaction duration |
It is clear that there are optimum values for the parameters investigated, such as increasing the catalyst amount, the viscosity starts decreasing till it reaches its lowest value then starts to increase gradually. Raising the temperature also increases the efficiency according to the molecules' motion but high reaction temperatures negatively affect the yield related to the alcohol's boiling point. Generally, the optimum alcohol to oil ratio is given as 9:1.
3.3 Heterogenous Catalysts
In the previous discussions, the barriers for operating the process of producing biodiesel, in terms of cost, catalyst efficiency, catalyst usage, etc. were mentioned. In order to develop the process by considering all the aforementioned problems, researchers have been studying the heterogeneous catalysts as an alternative to the previous catalysts and some of the results are given in Tab. 4.
Unlike homogeneous catalysts, heterogeneous catalysts can be reusable until deactivation and presence of heterogeneous catalysts prevents soap production 42. Furthermore, more biodiesel can be produced with low amounts of catalysts, the comparison is given in Tab. 5.
Catalysts' name |
Homogeneous catalyst |
Heterogeneous catalyst |
---|---|---|
NaOH |
MgO |
|
Used amount [t] |
88 |
5.6 |
Produced biodiesel total [t] |
8000 |
100 000 |
Heterogeneous catalysts are classified into subgroups according to their proton strength such as alkaline earth oxides, alkaline oxides, non-metal oxides, metal phosphates and acids, metal oxides, and cation-exchange resins (Fig. 5).

The performance of heterogeneous catalysts in biodiesel production is affected by various parameters, including the type of oil used, the temperature, the catalyst type, the amount of catalyst used, and the molar ratio of alcohol to oil. Mass transfer constraints and low active sites can decrease the efficiency of the catalysts in certain conditions. To address these limitations and enhance the efficiency of the catalysts, researchers 43 have employed various types of catalyst support materials, such as alumina, silica, titania, zirconium oxide and activated carbon. Catalyst supports play a crucial role in the reactions by increased total surface area, stabilizing the chemicals, and maintaining the ability to distribute the active sites such as metals or metal oxides over the surface. Among these, alumina is the most commonly used catalyst support due to its numerous advantages such as improved heat and mechanical stability, high surface area and wide pore diameter, all the properties which can be achieved at a low cost. However, it should be noted that active alumina can soften or become malleable under acidic conditions. Nevertheless, utilizing it as a support material for heterogeneous catalysts in biodiesel production can help to overcome the previously mentioned drawbacks. Silica is prepared with a mixture of acid and a solution of water glass. Silica keeps its form stable under acidic conditions. Usually, silica can be in the form of quartz in nature, and it has several species incorporating intertwined quartz, smoldered silica, silica gel and aerogels. Researchers investigated the usage of heterogeneous catalysts in biodiesel production and have employed a range of low-cost biodiesel feedstocks. The results are shown in Tab. 6.
Feedstocks |
Catalyst |
Preparation method |
Temperature [°C] |
Alcohol:oil ratio |
Catalyst content [wt %] |
Duration |
Biodiesel yield [%] |
Ref. |
---|---|---|---|---|---|---|---|---|
Soybean oil |
SrO |
Thermal (Calcination) |
65 |
12:1 |
3 |
30 min |
95 |
44 |
CaO |
Commerial |
65 |
12:1 |
8 |
3 h |
95 |
45 | |
KI/mesoporous silica |
Incipient wetness |
70 |
16:1 |
5 |
8 h |
90 |
46 | |
Tetramethyl-guanidine, bonded onto silica gel surface |
Precipitation |
80 |
– |
0.05 |
3 h |
86 |
47 | |
Sr(NO3)2/ZnO |
Impregnation |
65 |
12:1 |
5 |
5 h |
94.7 |
48 | |
Soybean frying oil |
Mg-Al hydrotalcite |
Impregnation |
60 |
– |
0.1 |
25 h |
97 |
49 |
Refined soybean oil |
Na2MoO4 |
Precipitation |
65 |
54:1 |
5 |
3 h |
95.6 |
50 |
Sunflower oil |
NaOH/γ-Al2O3 |
Incipient wetness |
50 |
12:1 |
0.4 |
24 h |
86 |
51 |
Incipient wetness (non-calcined support) |
50 |
12:1 |
0.4 |
24 h |
99 |
|||
Sunflower oil |
Fe-Zn double-metal cyanide complexes |
Precipitation |
170 |
15:1 |
3 |
8 h |
98.3 |
52 |
WCO |
Chicken bones |
Thermal (calcination) |
65 |
15:1 |
5 |
4 h |
89.3 |
37 |
It is pointed out that the interaction between the support and active metal/metal-oxide alters the production yield. Therefore, preparation method of the catalyst and also the selection of the support have to be compatible with the feedstock. The solubility of the catalyst has to be prevented and adsorption capacity for alcohol which is rate-determining step has to be improved.
Titania is found in nature in three phases, anatase, rutile, and brookite and they can be used for different purposes. For the past few years, titania has had numerous industrial practices. These practices are up-and-coming since the range of options for managing the catalyst's activity 53 and selectivity is expanding. Some of the titania-based catalysts in biodiesel production are sulfated titanium dioxide (,
,
,
,
,TiO2 supported ZnO4, TiO2–MgO, CaTiO3) catalysts. The majority of the results that researchers obtained from studying the titanium dioxide as a heterogeneous catalyst in biodiesel production are given in Tab. 7.
Feedstock |
TiO2 based Catalyst |
Preparation method |
Temperature [°C] |
Methanol: oil ratio |
Catalysts content [wt %] |
Duration |
Yield [%] |
Ref. |
---|---|---|---|---|---|---|---|---|
Waste oil |
Ti(SO4)O |
Sol-Gel |
75 |
9:1 |
1.5 |
3 h |
97.1 |
23 |
SO42/TiO2/La3+ |
Sol-Gel |
110 |
10:1 |
5 |
1 h |
96.16 |
54 | |
Cottonseed oil |
TiO2-SO42- |
Precipitation |
230 |
12:1 |
2 |
8 h |
90 |
55 |
Soybean oil |
Nano-MgO TiO2 |
Precipitation |
225 |
18:1 |
5 |
1 h |
84 |
56 |
Rapeseed oil |
CaTiO3 |
Solid state |
60 |
6:1 |
– |
10 h |
90 |
57 |
Canola oil |
K/TiNT |
Wet impregnation |
70 |
36:1 |
20 |
5 h |
100 |
58 |
K/TiO2 |
The high activity and versatility of titania in a wide range of reduction and oxidation processes at low temperatures and pressures have generated significant interest in its use as a catalyst in various reactions. Titanium dioxide is an effective metal oxide catalyst due to its robust support for metal strength, chemical stability, and acid-base properties.
4 Comparison and Impact of the Catalysts' Types on the Biodiesel Overall Cost
The usage of a catalyst can significantly reduce the cost of biodiesel production by saving the time and by reducing the energy input that required. Throughout the paper, diverse types of catalysts are demonstrated. The main comparison and competitivity in biodiesel plants got implemented between the homogeneous and the heterogeneous catalysts. After all the pros and cons mentioned previously, the cost of the product is an essential scale in the process. The cost of biodiesel production can vary depending on many factors, including the types of feedstocks, catalyst, operating conditions, materials (alcohol, oils, etc.), and consumed energy. Some studies 59 on the economic impact of the catalysts exhibit variations in the acquiring prices as 0.08–0.22 $ kg−1. The reusability, durability, and availability of a catalyst can affect the product overall in a big-scale production. Elgharbawy et al. 60 studied heterogeneous natural mineral rocks in biodiesel production with the ultrasonic method. The same heterogeneous catalyst was used with seven runs without losing its efficiency. This study indicated that the usage of heterogeneous catalysts with an optimal operating condition brings the biodiesel cost below the selling price. The less amounts of heterogeneous catalyst would produce more biodiesel than homogeneous ones. For instance, a comparative study 61 examined two different catalysts, MgO and NaOH. The results showed that 5.6 tons of MgO could produce 12.5 times more biodiesel than the process where 88 t of NaOH had been used. In general, heterogeneous catalysts have cost-effective sources, e.g., eggshells, seashells and many others can reduce the cost and also the energy input for the transesterification reaction.
5 Future Perspectives of Homogeneous and Heterogeneous Catalysts for Transesterification Reactions
The right decision to minimize the destructive effects of emissions to the environment is to replace fossil fuels with renewable fuels. The ideal replacement for fossil fuels is biofuels when the production yields are considered, they are also renewable, biodegradable, non-toxic and beneficial for the environment. Transesterification is defined as the conversion of triglycerides from a variety of feedstock into fatty acid methyl esters (biodiesel) in the presence of alcohol. Triglycerides are transesterified in a batch or continuous mode of operation at atmospheric pressure and at boiling point temperatures of the alcohol in the presence of a catalyst. At this point, selection or designing a catalyst plays a vital role. It is well known that a purification step is necessary for catalytic transesterification processes even if the catalyst is homogeneous or heterogeneous. In this step, the processes with homogeneous catalysts require more energy and purifying agent which are not satisfy the principles of green chemistry. Transesterification with heterogenous catalysts meets many of these requirements in the point of view of atom economy, waste reduction and safety. Heterogenous catalysts have advantage of easy separation and reusability. As a result, the processes with heterogeneous catalysts appear to be a promising technology for biodiesel synthesis in the future. Therefore, the designing of the catalysts has to be considered as an art. It is well known that the efficiency of a heterogeneous catalyst depends on several factors. The surface properties such as acidity, pore size of the support and distribution of active sites affect the efficiency of the catalyst. These properties can be arranged by many modifications such as using different preparation techniques, altering the calcination temperature and use of alternative shapes of supports such as nanowires or nanotubes. Differentiating the morphology of the catalyst will overcome the mass transfer limitations and enhance the adsorption capacity.
Titania is the commonly most used semi-conductor photocatalyst. The morphology of titania can be modified, and it can be transformed to different nano shapes easily. The energy requirement of photocatalytic transesterification reaction can be supplied from Sun. In this point of view photocatalytic transesterification reaction could be the best process of biodiesel production which also can fulfill the green chemistry principles such as less hazardous chemical synthesis, design for energy efficiency and designing safer chemicals.
6 Conclusions
Biodiesel is an emerging fuel due to its renewability and environmentally friendly production processes. It can be produced from a variety of edible, inedible, waste oils, and animal fats. Millions of liters are produced annually around the world. The transesterification process is the most suitable method for producing biodiesel. In the transesterification reaction, for every one mole of oil, three moles of alcohol react, resulting in the production of three moles of fatty acid alkyl monoester (biodiesel) and one mole of glycerol. The highest yield of biodiesel production had achieved using methanol. While transesterification is the preferred reaction compared to others, the type of catalyst used in the reaction can have positive or negative impacts. The main aim of producing biodiesel using heterogeneous catalysts is to lower the cost since 70 % to 95 % of biodiesel cost depends on the feedstock cost. Enzymatic catalysts are not practical due to their high cost and while homogeneous catalysts have low costs, the purification, washing, and product cleaning stages increase the cost of the process. Heterogeneous catalysts can use inexpensive feedstocks and are easy to handle as there are fewer purification and washing stages. However, while heterogeneous catalysts overcome many of the obstacles associated with homogeneous catalysts, they have some disadvantages. Catalyst supports such as alumina, silica and titania had used during the reaction to address these issues. Finally, the actual results of the biodiesel produced using heterogeneous catalysts with different feedstocks and types of catalysts used were presented. The importance of the interaction between a catalyst and a support for heterogeneous catalyst was also discussed. It can be concluded that producing biodiesel sustainably and economically is a very desirable goal that will benefit humankind's need for energy in the future and heterogeneous catalysts will be the most attractive part of the whole process.
Conflicts of Interest
The authors declare no conflict of interest.
Acknowledgements
The authors sincerely extend their thanks to all the researchers whose work has been cited in this mini review paper.
Abbreviations
-
- AN
-
Acid number
-
- ASTM
-
American Society of Testing and Materials
-
- CFPP
-
Cold filter plugging point
-
- CN
-
Cetane number
-
- CP
-
Cloud point
-
- CV
-
Calorific value
-
- EN
-
European normalization
-
- FAME
-
Fatty acid methyl ester
-
- FP
-
Flash point
-
- IN
-
Iodine number
-
- IS
-
Indian standards
-
- LPG
-
Liquefied petroleum gas
-
- PP
-
Pour point
-
- SO
-
Safflower oil
-
- SVO
-
Straight vegetable oils
-
- TAG
-
Triacyl-glycerides
-
- WCO
-
Waste cooking oils
Biographies
Murat Efgan Kibar is currently working as associate professor at the Department of Chemical Engineering, Kocaeli University. He got his doctoral degree in 2016 at Kocaeli University. In 2022 he became a deputy director of the Alternative Fuels Research and Development Center at Kocaeli University. His main research areas are catalysis and reaction engineering. He is currently working on the photocatalytic hydrogen, methanol and dimethyl carbonate production and designing photothermal reactors.
Lina Hilal is a senior chemical engineer in Türkiye, she has been working in the renewable energy industry since her freshmen year. She worked on multiple researches in varied types of fields, to approach her genuine interest, including biodiesel production, catalytic reactions, hydrogen energy storage systems, hydrogen production, biomass to power concept. Recently she had worked at the University of Sharjah as a research assistant and now she is working on two national funded projects in her college, Kocaeli University.
Begüm Tuna Çapa is an undergraduate student. She completed her graduation work on rubber technology at Kocaeli University. Currently she is working in the field of process engineering; she conducts her studies on oil refineries.
Buse Bahçivanlar is currently an undergraduate student at the Department of Chemical Engineering, Kocaeli University. She works on process safety in an engineering company. She also works on a national funded project about production of borophene titanium dioxide composite and photocatalytic effect of the composite under the supervision of Assoc. Prof. Kibar. Her research interests include renewable energy, hydrogen production, catalysts and borophene.
Brahim Ben Abdeljelil is a fourth-year chemical engineering student at Kocaeli University in Türkiye. He is actively involved in the research group of Assoc. Prof. Kibar. His research interests encompass hydrogen production, photo-catalytic reactions, renewable energy and biodiesel production. Through his collaboration with Assoc. Prof. Kibar, he contributes to the exploration of innovative approaches in these areas.