Electron-Irradiated Montmorillonite/Polyethylene Composite Separator for High-Performance Lithium-Ion Battery
ABSTRACT
Separators play a significant role in the safety and performance of lithium-ion batteries. In this study, composite separators were fabricated using montmorillonite (MMT) as a filler in a high-density polyethylene (HDPE) matrix, followed by electron irradiation to enhance the safety and performance of separator. Electron irradiation induces chemical bonds by crosslinking between HDPE chains, also between the MMT and HDPE. MMT features a two-dimensional layered structure with a high surface area, providing abundant crosslinking sites. MMT is treated with a silane coupling agent, which induces layer exfoliation. The exfoliation increases the surface area of MMT, thereby providing more crosslinking sites. Additionally, the surface modification of MMT enhances its affinity with HDPE, leading to better dispersion of MMT within the HDPE matrix. Simultaneously, electron irradiation in an air atmosphere generates polar functional groups, improving the electrolyte affinity of the separator. Consequently, the safety of the MMT composite separator was significantly enhanced, exhibiting a high puncture strength of 0.52 N μm−1 and a thermal shrinkage rate of 21.4% at 135°C for 30 min. Li//LCO cells using the composite separator demonstrated superb cycle stability with a discharge retention of 98.7% and a coulombic efficiency of 99.6% after 200 cycles at 0.5 C, and exhibited rate capability maintaining 74.5% of the capacity at 20 C compared to 0.5 C.
1 Introduction
The demand for lithium-ion batteries is steadily increasing. Alongside the commonly seen phone batteries, the lithium-ion battery market is expanding continuously with advancements in industries such as electric vehicle batteries and energy storage systems. It is expected to grow even more in the future, as these batteries are anticipated to be used more extensively [1-3].
The separator is a fundamental component of a lithium-ion battery, along with the anode, cathode, and electrolyte, playing a significant role in safety [4-8]. Separator prevents direct contact between the anode and cathode, preventing short circuits, while maintaining a porous structure to facilitate the movement of lithium ions between the electrodes [9-11]. Additionally, it serves to shut down the battery at temperatures before thermal runaway occurs, providing protection against potential fires. Therefore, the materials used in separators must possess chemical, physical, and thermal stability, while also allowing ion passage through a microporous membrane. Meeting these criteria, polymers are currently the most widely used materials for separators, with commercially affordable polyethylene and polypropylene being the predominant choices.
Despite the use of such materials, safety issues related to battery fires have been a persistent concern for several years. Among the causes of battery fires, the separator plays a significant role, with the risk of the separator being punctured by lithium dendrites that grow from the cathode during the battery charging and discharging process [12, 13]. Additionally, there is a possibility of a sudden increase in temperature or the occurrence of defects in other parts of the battery leading to overheating. Conventional polymer separators exhibit significant shrinkage at temperatures around 130 ~ 140°C. It can result in separator damage, leading to short circuits and thermal runaway [14, 15]. Recently, with the expansion of the electric vehicle market, technologies that regulate the temperature of battery packs, such as battery thermal management systems, have been actively studied [16, 17]. However, the thermal stability of separators remains crucial in unexpected accident scenarios.
To deal with this issue, a separator technology known as coated separators is used. This involves applying a thin ceramic coating to conventional polymer separators to enhance physical and thermal properties, as well as electrolyte affinity [18-21]. However, coated separator faces challenges such as weak adhesion between the ceramic coating and the separator, which may result in the coating peeling off [22]. Additionally, the coated layer is susceptible to deformation, especially when subjected to bending [23]. Moreover, the thickness of the separator inevitably increases, negatively affecting the volumetric energy density. This becomes particularly critical in the case of lithium batteries, where numerous batteries are connected, making the thickness of each individual separator even more detrimental.
Composite separators were developed to solve the drawbacks of coated separators through the use of polymer blending, functionalization, or fillers [24-26]. Among them, polymer-nanofiller composite separators combine a polymer separator with mechanically and thermally advantageous nanofiller materials to enhance the stability and performance of the separator [27-29]. However, merely blending filler materials is not sufficient to achieve these enhanced properties. Fillers tend to agglomerate within the polymer matrix, especially when their surfaces are hydrophilic, and they do not disperse well [27]. Additionally, the adhesion between the polymer and the filler is often insufficient, leading to poor transmission of the properties of filler into the polymer matrix [30].
To address these issues, in a previous study, our research team utilized a silane-coupling agent and electron irradiation to boehmite/high-density polyethylene (HDPE) composite separator [31]. However, there are still existing drawbacks that boehmite nanoparticles have relatively small surface area at 100 m2 g−1, which cannot provide sufficient crosslinking sites.
In this study, to overcome drawbacks of using boehmite nanoparticles, montmorillonite (MMT) with a two-dimensional (2D) layered structure was used as a filler for the HDPE composite separator. Electron beam irradiation on MMT/HDPE induces crosslinking between HDPE chains as well as between MMT and HDPE, enhancing adhesion between them. 2D layered materials have a larger surface area per volume compared to 0D nanoparticles, thereby MMT provides more crosslinking sites [32]. When MMT is treated with a silane coupling agent, the silane reacts between the interlayers of MMT, causing exfoliation. This process increases surface area of MMT, providing additional crosslinking sites. Moreover, the surface modification by silane improves compatibility between MMT and HDPE, enhancing its dispersion within the HDPE matrix. A strong hydrophobic silane coupling agent, trimethoxy(octadecyl)silane (ODS), was employed for surface modification. The safety and performance of the composite separators were systematically evaluated.
2 Experimental
2.1 Materials
The HDPE powder (VH035) employed in this study was commercially manufactured by Korea Petrochemical Co. Montmorillonite k-10 (MMT) and Trimethoxy(octadecyl)silane (ODS) was purchased from Sigma-Aldrich. Paraffin oil, hexadecane, and dichloromethane were purchased from Daejung Chemical & Metals Co. Liquid electrolyte, LiPF6 in ethylene carbonate/diethyl carbonate/ethyl methyl carbonate (1:1:1 v/v) electrolyte solution with 3 wt.% fluoroethylene carbonate was supplied by Donghwa Electrolyte Co. Super-P (Imerys Co.). N-methyl-2-pyrrolidone (Jaewon Industrial Co.), lithium cobalt oxide (Cosmo AM&T Co.), carbon black (Imerys Co.) Al foil (Dongil Aluminum Co.), and Li metal (Honjo Metal Co.) were used as received.
2.2 Silane Treatment of MMT
The silane treatment initiated the hydrolysis reaction of the silane, generating hydroxyl groups. These hydroxyl groups subsequently facilitated the condensation reaction between the hydroxyl groups of each MMT and silane. To induce the hydrolysis reaction of the silane, 3 mL of ODS was mixed with 25 mL of distilled water in 250 mL of ethanol at 100°C for a few minutes. Immediately following this, to induce the coupling reaction, 10 g of MMT was added to the mixture and stirred for an additional 12 h. The mixture was then centrifuged to remove reaction by-products, leaving behind only the particles. To ensure the removal of impurities, ethanol was added to the mixture, which was subsequently centrifuged again. The resulting particles were dried at 100°C for 12 h to yield the final product in powder form.
2.3 Production of the Separator
Surface-treated MMT, HDPE powder, and paraffin oil used as a matrix were uniformly mixed at 100°C and processed using a biaxial extruder (BA-11, Bautek Co., Korea) to produce a gel film. In this process, the MMT and HDPE mixture, along with paraffin oil, were added at a weight ratio of 3:7, and the proportion of MMT in the MMT and HDPE mixture was adjusted to 1, 3, 5, and 7 wt.%. The resulting film was stretched five times in the MD direction and 5.5 times in the TD direction. The stretched film was then placed in dichloromethane for 20 min and briefly sonicated for approximately 5 s to remove the paraffin oil inside the film and create a nanoporous structure. Subsequently, the sample underwent a heat-setting process at 128°C for 1 min to enhance its thermal and physical properties before the polymer melted. Following the procedure, a separator with a thickness of 10 μm was prepared. Finally, electron irradiation with an energy of a 1 MeV beam was conducted until a dose of 100 kGy was accumulated in an air atmosphere (EB Tech Co, Korea). To maintain a constant dose, the membrane was flipped once to expose both sides to the electron beam during irradiation.
2.4 Characterization
Contact angle with electrolyte was measured by drop-shape analyzer (Phoenix-mt(m), SEO, Korea).
2.5 Electrochemical Measurements
3 Results and Discussion
3.1 Effect of Silane Treatment and Electron Irradiation on Separators
To clarify the chemical structure changes after silane treatment, FTIR absorption spectra of MMT powder were examined, as shown in Figure 1. Additionally, FTIR absorption spectra of HDPE powder are presented in Supporting Information S1: Figure S2. In pure MMT, peaks related to Si, O, and Al were observed; a peak for Si-O-Si stretching at 1035 cm⁻1, a peak for Al-O-Al stretching at 915 cm−1, and a peak for Si-O-Si bending at 529 cm⁻1 [34, 35]. After the silane treatment, ODS/MMT exhibits CH- peaks due to the spacer alkyl groups in ODS. CH2- symmetric and asymmetric stretching peaks from ODS were observed at 2847 and 2921 cm⁻1, which are also present in HDPE [36]. The alkyl groups in ODS-treated MMT (ODS/MMT) have a chemical structure similar to HDPE, resulting in higher dispersibility within the HDPE matrix compared to untreated MMT [32].
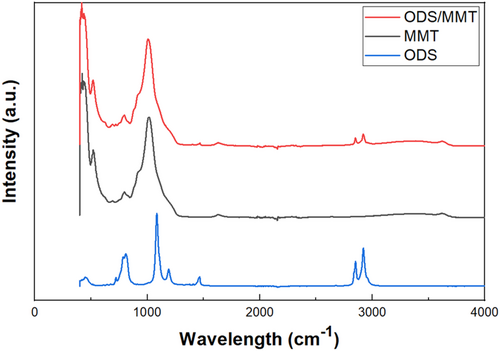
Dispersion was confirmed through SEM and EDS image analysis, as shown in Figure 2. In the case of untreated MMT/HDPE composite separators (MMT/HDPE), large particle clusters of several micrometers in size were observed scattered throughout the sample surfaces. EDS results for the Al, and Si element also indicated localized agglomerations. For the ODS-treated MMT/HDPE composite separators (ODS/MMT/HDPE), dispersion appeared to be better compared to the untreated samples. In the 3 wt.% ODS/MMT/HDPE sample, no agglomerated particles were visible on the sample surface, and EDS analysis for the Al, and Si element also indicated good dispersion. However, for the 7 wt.% ODS/MMT/HDPE sample, particle agglomeration was observed despite the silane treatment, attributed to the high filler content [30].
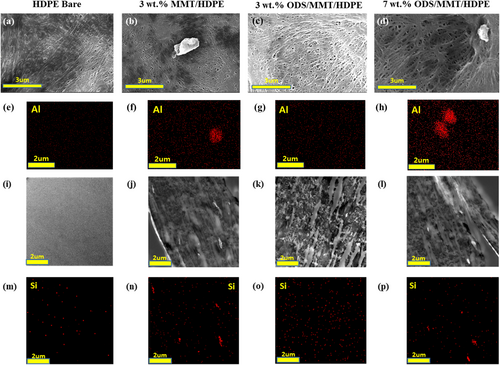
To further investigate the effects of the silane coupling agent on MMT, XRD measurements were performed on HDPE bare samples and samples containing 3, 5, and 7 wt.% MMT, as well as ODS/MMT/HDPE samples (Figure 3). The interlayer gallery of MMT was identified by the (001) peak observed between 8° and 9° in the XRD patterns. The silane treatment affected not only the surface of MMT but also the space between its layers, inducing the exfoliation of the MMT layers [37, 38]. This exfoliation enhances dispersion in nanocomposites. It was observed that the MMT-containing membranes, excluding the 3 wt.% ODS/MMT/HDPE, exhibited the (001) peak. For the 3 wt.% ODS/MMT/HDPE sample, the silane treatment caused the (001) peak to disappear, indicating exfoliation. However, in the 5 and 7 wt.% samples, the (001) peak reappeared despite surface treatment. This is attributed to increased interfacial interactions between layers at higher filler contents, which hinder exfoliation even with silane treatment [38].
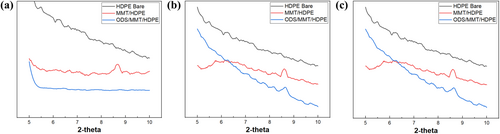
When a polymer irradiated by an electron beam, electrons collide with atoms, leading to the breaking of C–H and C–C bonds and the generation of radicals. Through this process, radicals generated combine with each other, creating new C–C bonds between different polymer chains, inducing crosslinking in the polymer structure [39]. In composites containing ODS/MMT, crosslinking also occurs between the polymer chains and the alkyl functional groups in ODS. As a result, the membrane can possess enhanced mechanical and thermal stability.
Boiling xylene tests were performed to measure the crosslinking density for HDPE bare, 3 and 7 wt.% of MMT/HDPE and ODS/MMT/HDPE samples (Figure 4). During the test, a sample enclosed in a mesh cage is subjected to boiling xylene, where the non-crosslinked portions dissolve and pass through the mesh, leaving only the crosslinked parts inside the cage. By measuring the proportion of the sample that remains in the cage, the degree of crosslinking for each sample can be quantitatively compared. The results showed that HDPE bare retained 25.3% gel, while the 3 wt.% MMT/HDPE and ODS/MMT/HDPE samples retained 27.2% and 35.4%, respectively. The 7 wt.% MMT/HDPE and ODS/MMT/HDPE samples retained each 20.7% and 24.9%. The boiling test was also conducted on 10 wt.% ODS/boehmite/HDPE, which was content-optimized to compare the crosslinking of 0D nanoparticles and MMT, yielding a result of 31.1%. The 3 wt.% ODS/MMT/HDPE samples exhibited a higher remaining gel content compared to other samples, suggesting that enhanced dispersion and layer exfoliation likely led to a higher crosslinking ratio.
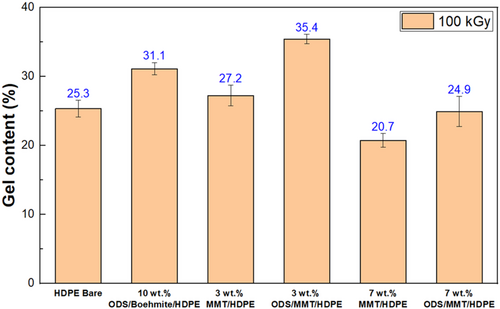
When electron irradiation was performed on the polymer in an air atmosphere, radicals reacted with oxygen, resulting in the formation of functional groups such as ester, ketone, and carboxyl on the polymer. Figure 5 shows the FTIR results of the irradiated separators, where ester, ketone, and carboxyl functional groups were observed at peaks of 1735, 1720, and 1713 cm−1, respectively [40]. These polar functional groups exhibit higher electrolyte affinity compared to the alkyl groups in HDPE, contributing to the enhanced electrochemical properties of the irradiated separators.
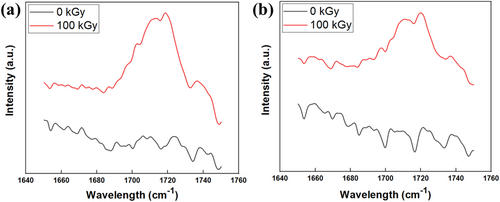
3.2 Mechanical/Thermal Stability of the Separators
To prevent accidents arising from separators, their mechanical and thermal stability is crucial. Puncture strength is particularly important among the mechanical properties of separators. During the repeated charge and discharge cycles of battery use, internal pressure can be occurred. Additionally, lithium dendrites formed during cycles can damage the separator. Puncture strength measurements were measured on HDPE bare, and samples with 1, 3, 5, and 7 wt.% MMT/HDPE and ODS/MMT/HDPE before and after electron beam irradiation (Figure 6). Before silane treatment, the puncture strength values for HDPE bare, 1, 3, 5, and 7 wt.% samples were 0.338, 0.304, 0.348, 0.315, and 0.271 N μm−1, respectively. Following electron beam irradiation, the puncture strength values for HDPE bare, 1, 3, 5, and 7 wt.% samples were measured as 0.384, 0.36, 0.411, 0.381, and 0.308 N μm−1, respectively. Only the 3 wt.% sample exhibited higher puncture strength compared to HDPE bare. For ODS/MMT/HDPE samples, the puncture strength values before electron beam irradiation were measured as 0.366, 0.449, 0.398, and 0.318 N μm−1 for 1, 3, 5, and 7 wt.% samples, respectively. After electron beam irradiation, the values were 0.426, 0.520, 0.460, and 0.358 N μm−1. The crosslinking induced by electron irradiation resulted in the formation of chemical bonds, enhancing the mechanical strength of all types of samples. Furthermore, as shown in Figures 3 and 4, ODS treatment improved layer exfoliation and dispersion of MMT, preventing filler agglomeration within the HDPE matrix. This allowed the filler to interact with the polymer over a larger surface area, thereby increasing the mechanical strength of the composite [30]. The increase in the surface area of MMT due to silane treatment further provided additional crosslinking sites during electron beam irradiation, leading to a greater improvement in mechanical strength, with the 3 wt.% sample showing the most significant enhancement. However, when the content exceeded 3 wt.%, agglomeration occurred despite the silane treatment, resulting in a decrease in mechanical strength compared to the 3 wt.% sample.
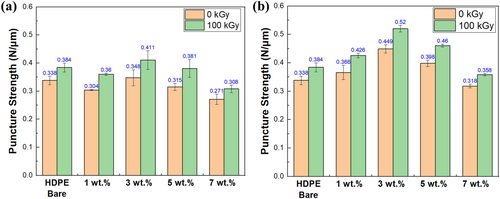
To evaluate the thermal stability, the measurement of the area thermal shrinkage was performed for HDPE bare, 1, 3, 5, and 7 wt.% MMT/HDPE and ODS/MMT/HDPE samples (Figure 7). In the case before silane treatment, the measured values for HDPE bare, 1, 3, 5, and 7 wt.% samples before electron beam irradiation were 54.5%, 51.40%, 42.4%, 53.3%, and 59.1%, respectively. After electron beam irradiation, the values were 40.2%, 43.9%, 36.7%, 39.8%, and 46.3%, respectively. Similar to puncture strength, the 3 wt.% sample exhibited the best thermal stability, and the trend was 3, 5, bare, 1, and 7 wt.% in order of better thermal stability. After silane treatment, the thermal shrinkage measurements for 1, 3, 5, and 7 wt.% samples before electron beam irradiation were 40.1%, 33.7%, 44.0%, and 50.3%, respectively. After electron beam irradiation, the values were 35.5%, 21.4%, 29.6%, and 40.6%, respectively. Similar to the trend of the puncture strength results, both silane treatment and electron beam irradiation enhanced the thermal stability, especially for the 3 wt.% ODS/MMT sample, which showed a significant decrease in thermal shrinkage by 33%, reducing from 54.4% of untreated HDPE bare sample to 21.4%. In the evaluation of thermal shrinkage, as with puncture strength, the enhancement effects of characteristics due to silane treatment and electron beam irradiation were clearly confirmed.
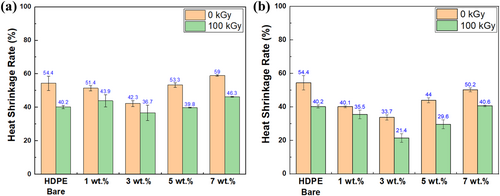
To compare MMT and nanoparticles as fillers, the optimized concentrations of 10 wt.% ODS/boehmite/HDPE and 3 wt.% ODS/MMT/HDPE were compared for puncture strength and heat shrinkage rate (Supporting Information S1: Figure S3 and S4). Puncture strength was 0.449 N μm−1 for 3 wt.% ODS/MMT/HDPE and 0.424 N μm−1 for 10 wt.% ODS/boehmite/HDPE. After 100 kGy electron beam irradiation, these values increased to 0.52 and 0.476 N μm−1, respectively, with ODS/MMT/HDPE showing better performance. Heat shrinkage rates were 33.7% and 47%, which improved to 21.4% and 36.8% post-irradiation, again favoring ODS/MMT/HDPE. Unlike boehmite, which only benefited from surface dispersion, MMT achieved better results due to silane-induced layer exfoliation, increasing surface area and crosslinking density (as seen in Figure 4). Consequently, after irradiation, the puncture strength and thermal shrinkage rate of 3 wt.% ODS/MMT/HDPE significantly outperformed those of 10 wt.% ODS/boehmite/HDPE.
3.3 Properties of the Separators
Porosity, Gurley number, and electrolyte uptake were measured for HDPE bare, 3 wt.% MMT/HDPE, and 3 wt.% ODS/MMT/HDPE, which exhibited the optimized filler content based on mechanical and thermal stability tests (Figure 8). The porosity of the membrane serves as an indirect indicator of battery performance, with higher porosity enabling better lithium-ion transport, thereby enhancing performance at the expense of reduced mechanical strength. Thus, balancing mechanical strength and increased porosity is crucial. Air permeability, measured alongside porosity, also reflects battery performance and typically increases with higher porosity. The porosity and Gurley number (air permeability) measurements indicated that the nanocomposite separator had higher porosity compared to HDPE bare. This difference is attributed to the higher density of MMT compared to HDPE when mixed at the same mass ratio during the film manufacturing process. Furthermore, porosity increased after electron irradiation, as some hydrocarbon gases escaped due to the electron beam [41].
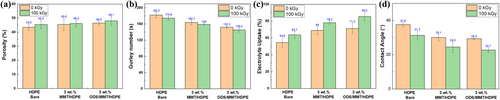
As lithium ions pass through the membrane via the electrolyte during battery operation, electrolyte affinity of the membrane is a crucial factor in determining battery performance. To evaluate the electrolyte affinity, electrolyte uptake and electrolyte contact angle were assessed. The results showed similar to porosity trends, the nanocomposite membrane outperformed HDPE bare. Even after electron beam irradiation, the values increased. In the case of composite separators, the higher electrolyte affinity of MMT compared to HDPE led to increased electrolyte uptake compared to HDPE bare. Despite the relatively lower electrolyte affinity of ODS/MMT due to the presence of surface alkyl groups, the short length of these alkyl groups, compared to HDPE chains, resulted in higher electrolyte affinity than HDPE bare. The lower values for untreated MMT/HDPE compared to ODS/MMT/HDPE are attributed to the lower overall particle dispersion, despite the better electrolyte affinity of the MMT surface [31]. Moreover, when electron irradiation was performed on the polymer in an air atmosphere, radicals reacted with oxygen, leading to the formation of functional groups such as ester, ketone, and carboxyl on the polymer as shown in Figure 5. The polar functional groups induced by irradiation exhibit better affinity with carbonate electrolytes compared to alkyl groups, resulting in increased electrolyte uptake and a significant decrease in electrolyte contact angle [42].
3.4 Electrochemical Properties of the Separators
Electrochemical property measurements were conducted by Li//LCO cells assembled with HDPE bare, 3 wt.% MMT/HDPE, 3 wt.% ODS/MMT/HDPE, and 100 kGy irradiated 3 wt.% ODS/MMT/HDPE separators. Figure 9 shows the results of the cycle stability and rate capability tests measured to evaluate battery performance. For cycle stability, discharge retention and coulombic efficiency (Figure 9a) were calculated after 200 cycles at a 0.5 C charge/discharge rate. The discharge retention for HDPE bare, 3 wt.% MMT/HDPE, 3 wt.% ODS/MMT/HDPE, and irradiated 3 wt.% ODS/MMT/HDPE samples were 86%, 94.6%, 97.2%, and 98.7%, respectively. While the bare sample showed a significant drop near 50 cycles, both the 3 wt.% ODS/MMT/HDPE samples maintained over 95% retention before and after electron beam irradiation until 200 cycles. The coulombic efficiencies were 97.7%, 98.5%, 99.1%, and 99.6% for the respective samples. Although lithium-ion batteries typically exhibit coulombic efficiencies above 95%, a slight increasing trend was observed.
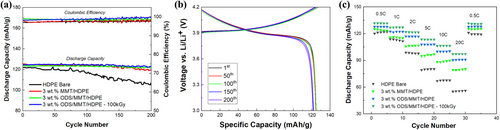
The rate capability measurement was conducted by discharging at rates of 0.5, 1, 2, 5, 10, and 20 C for five cycles each (Figure 9c). The discharge retention values for HDPE bare, 3 wt.% MMT/HDPE, 3 wt.% ODS/MMT/HDPE, and irradiated 3 wt.% ODS/MMT/HDPE samples were 45.9%, 63.9%, 69.5%, and 74.5%, respectively.
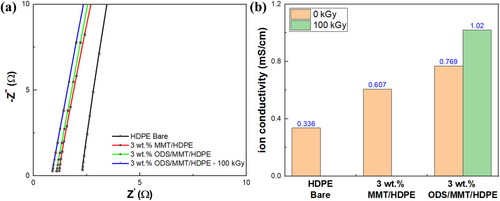
To analyze the differences in battery cycle performance based on the type of separator, ionic conductivity, lithium transference number, and AC impedance measurement were examined. The separators used were HDPE bare, 3 wt.% MMT/HDPE, 3 wt.% ODS/MMT/HDPE, and irradiated 3 wt.% ODS/MMT/HDPE, consistent with the battery cycle tests. Ionic conductivity reflects the efficiency of ion transport between electrodes, influencing battery performance and capacity retention. It was measured using the bulk resistance of a symmetric cell with stainless steel electrodes (Figure 10). The results showed ionic conductivities of 0.336, 0.607, 0.769, and 1.02 mS cm−1, respectively, indicating significantly higher values for samples with filler and electron beam treatment compared to the bare sample. This difference, as shown in Figure 8c, is due to the increased electrolyte uptake of the separator caused by the filler and electron beam irradiation. Additionally, MMT and HDPE matrix oxidized by electron beam irradiation contains highly polar atoms, such as oxygen, which enhance ion mobility by de-solvating lithium ions as they pass through the separator [42].
The lithium transference number represents the proportion of total current in the electrolyte carried by lithium ions, which is a crucial indicator of battery performance. It was calculated using the Bruce-Vincent Method with Equation (5). The chronoamperometry results are shown in Supporting Information S1: Figure S5 and summarized in Supporting Information S1: Table S1. The values of the lithium transference number were 0.317, 0.393, 0.419, and 0.480, respectively. Similar to ionic conductivity, increased due to the presence of fillers and electron beam irradiation. This is because the increase in ionic conductivity, along with the increased electrolyte uptake, contributed to the rise in the lithium transference number. Additionally, the de-solvation effect caused by polar atoms enhanced the mobility of lithium ions, further leading to an increase in the lithium transference number [43].
The AC impedance measurement was examined and is shown in Figure 11 and Table 1. Rb represents the internal bulk resistance, which denotes the resistance to ion movement within the electrolyte and the intrinsic resistance of the electrode material in the electrochemical system. This is indicated by the point where the Nyquist plot intersects the real axis (x-axis). RSEI is the resistance of the SEI (solid electrolyte interphase) layer and can be obtained from the small semicircle on the left side, that is, the high-frequency region of the Nyquist plot. Rct refers to the charge transfer resistance, which signifies the resistance to charge (ion or electron) transfer at the interface between the electrode and electrolyte, and is determined from the largest semicircle on the right side of the Nyquist plot. The value of Rb can vary depending on the ionic conductivity of the separator, thus, it decreased when MMT was well dispersed or after electron beam irradiation. Additionally, the value after 200 cycles was significantly higher than the value after the first cycle, which is attributed to the decomposition of the electrolyte or physical and chemical changes on the electrode surface as the cycling progresses. For RSEI, it was observed that the value increased as the SEI layer grew during the charge-discharge cycles. It was also observed that Rct significantly decreased due to the fillers and electron beam irradiation. This is because the ion conductivity and electrolyte affinity improved. As cycling progressed, Rct increased due to electrolyte decomposition, changes on the electrode surface, and increased ion transport pathways resulting from SEI growth [44].
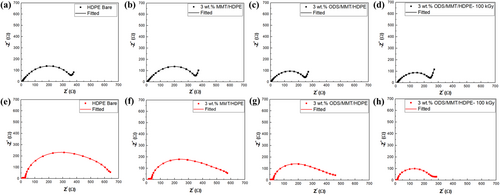
Dose (kGy) | Cycle | Rb (Ω) | RSEI (Ω) | Rct (Ω) | |
---|---|---|---|---|---|
HDPE bare | 0 | 1st | 3.9 | 9.8 | 373.2 |
200th | 6.6 | 23.7 | 632.4 | ||
3 wt.% MMT/HDPE | 0 | 1st | 3.3 | 8.8 | 336.5 |
200th | 5.5 | 20.8 | 553.2 | ||
3 wt.% ODS/MMT/HDPE | 0 | 1st | 3.1 | 8.2 | 260.1 |
200th | 4.3 | 18.7 | 438.8 | ||
100 | 1st | 2.5 | 7.5 | 211.5 | |
200th | 3.8 | 10.1 | 259.7 |
4 Conclusion
MMT/HDPE composite separators exhibiting high safety and performance of lithium-ion batteries were prepared by ODS treatment and electron irradiation. ODS treatment induces the exfoliation of MMT layers and facilitates the homogenous dispersion of MMT in HDPE. In addition, electron irradiation leads to crosslinking between the ODS-treated MMT and HDPE, as well as the HDPE chains. Layer exfoliation and high dispersibility in the HDPE resulted in an increased number of crosslinking sites for electron beam irradiation of the ODS-treated MMT. As a result, the composite separator irradiated with electron beam exhibited outstanding dimensional stability in terms of puncture strength and thermal shrinkage rate. Electron irradiation simultaneously generates oxygen-containing polar functional groups in HDPE, which improved electrolyte affinity of the separators. Li//LCO cell assembled using the composite separator demonstrated superior electrochemical performance in terms of rate capability and cycle stability. The results show that the 2D nanofiller with numerous crosslinking sites enhance the properties and performances of composite separators more effectively than when nanoparticles are used as a filler. We believe that composite separators with optimized nanofiller and surface treatment combined with electron irradiation can further improve the safety and performance of the lithium-ion batteries.
Acknowledgments
This work was supported by the National Research Foundation of Korea (NRF) grant funded by the Technology Development Program funded by the Ministry of Small and Medium Enterprises and Startups (grant number of S3207719).
Conflicts of Interest
The authors declare no conflicts of interest.
Open Research
Data Availability Statement
Data will be made available on request.