Feasibility study on the production of low melt flow rate recycled polypropylene from postconsumer waste
Abstract
Polypropylene (PP) recyclates face limitations in their use due to lower qualities compared with virgin PP, resulting from contaminations and the mixing of different PP grades. In particular, their high melt flow rate (MFR) hinders their suitability for applications requiring low MFR, such as pipes. This study investigates the feasibility of producing low MFR PP recyclates from packaging waste. For this purpose, recyclates were produced exclusively from manually sorted extrusion blow molding grades and compared with a recyclate derived from a conventional PP waste stream. Different washing temperatures and recyclate production processes were used to study their effects on the properties of the recyclates. The main objective was to determine the lowest achievable MFR and the rheological, mechanical, and thermal properties of the recyclates from improved sorting. The results are intended to serve as reference points for the evaluation of future automatic sorting trials. The enhanced sorting resulted in an 80% reduction in the MFR and improved ductility, thereby extending the potential applications of the recyclate. The different washing and production processes did not have a significant effect on the investigated properties, except for a slight decrease in the MFR with hot washing and the omission of the pelletizing step.
1 INTRODUCTION
In order to increase plastics recycling rates, the European Union (EU) has introduced legal measures. The EU aims to increase the recycled plastic packaging rate to 50% by 2025 and 55% by 2030.1 In addition, the European Commission launched a pledging campaign targeting the use of ten million tons recycled plastics in new products by 2025.2, 3 However, the use of recyclates is still limited by higher costs, poorer properties, and inconsistent qualities compared with virgin materials.4-6 To achieve the goals of the EU, significant efforts such as improving mechanical recycling are needed.4
Mechanical recycling of plastics usually consists of separation and sorting, shredding, additional sorting steps, washing, density separation, drying, and reprocessing.5, 7-9 In order to reach higher quantities and qualities of recyclates, proper sorting is essential.10 There are already well-established sorting systems that are able to sort different polymers using near infrared (NIR) spectroscopy.11, 12 However, there are still some limitations and challenges including the inability to sort black plastics, multi-material components, or multilayer films as well as waste masked by dirt, surface moisture or labels.7, 10, 12-15 These aforementioned problems may lead to incorrect sorting and consequently the loss of valuable secondary raw materials or high concentrations of contaminations in the recyclates. Contaminants, both nonpolymeric and polymeric, can lead to an enormous property loss.6, 7, 16, 17 In addition, material degradation during service life, end-of-life storage and reprocessing usually deteriorates the recyclates' performance.18 However, even if the mentioned negative influences are kept to a minimum, the properties of recyclates may still be insufficient for demanding applications. The reason is the mixture of different grades of the same polymer type during recycling.
Polypropylene (PP), one of the most widely used polymers, is available in many different grades.19 Since the grades differ in their molecular structure (e.g., homo and copolymers), molecular weight (MW), and molecular weight distribution (MWD), morphology and additives, they exhibit different properties and processing characteristics. During recycling, different grades are mixed, which oftentimes leads to poorer properties compared to the virgin grades.6, 20, 21 Since the largest application field of PP is packaging, which generally has a low lifetime, the main source for PP recycling is packaging waste.19 PP packages mainly comprise of grades for the following processing methods: injection molding (IM), extrusion blow molding (EBM), thermoforming (TF), and film extrusion (FE). Because of the different processing requirements, these grades differ in their viscosities. The mixture of these grades during recycling and the low viscosity of IM grades usually leads to PP recyclates with rather low viscosities.21-23
While it is state-of-the-art to decrease the viscosity by degrading the chains, for example with peroxides, it is difficult to increase the viscosity of PP recyclates to a sufficient extent. Thus, the use of recyclates is oftentimes limited to applications, where materials with low viscosities can be used. However, PP recyclates are also needed in applications where high viscosities are required. In particular, extrusion requires very high viscosities. A quickly-measured value that provides information about the viscosity of polymers is the melt flow rate (MFR)—the higher the viscosity, the lower the MFR of a polymer. Although the MFR is only a single point measurement, it is widely used in input control and quality assurance due to its simplicity.24 It is therefore almost always included in datasheets of polymers and recyclates. According to such datasheets, PP grades for extrusion applications generally have MFR values between 0.2 and 1.3 g 10 min−1.25 In addition, there are specific MFR requirements depending on the application. One application that, according to the European Commission, has good potential for the use of recyclates is pipes.3, 26 The extrusion of pipes requires very low MFR values. There are several standards that define the MFR requirements for PP pipe applications. Depending on the application, the MFR should be less than 3 or 1.5 g 10 min−1.27-30 Without changes in the mechanical recycling processes, it will not be possible to produce PP recyclates suitable for pipe extrusion from postconsumer packaging waste. Improving the sorting systems would be one way to reduce the MFR of recyclates. Among the grades that can be found in PP packaging waste, packaging grades for EBM show the lowest MFR range with 1.3–1.9 g 10 min−1.Grades for TF and FE show ranges of 1.2–4 g 10 min−1 and 0.4–13 g 10 min−1, respectively. The MFR values for IM grades range from 3.5 to 100 g 10 min−1.25 Hence, to reduce the MFR of recycled PP, the use of IM as well as FE grades should be avoided.
In addition to sorting, washing and reprocessing also affect the properties of recyclates. The aim of washing is to remove or reduce foreign materials and contaminants such as adhesives, inks, organic contaminations, and microorganisms.7, 31, 32 With the removal of low MW substances that can act as plasticizer, the washing process can help to reduce the MFR of recyclates.32 Previous studies also showed that the choice of washing temperature, time and washing agents have an influence on the recyclate quality.32-35 After washing, melt filtration during regranulation helps to remove remaining nonmelting contaminations.7 However, during reprocessing, degradation of the material is inevitable due to the high temperatures and shear rates. Degradation of PP usually results in chain scission, leading to a decrease in the MW of the chains and an increase in the MFR.16, 36
The aim of this work is to investigate the feasibility of producing PP recyclates from PP packaging waste that are suitable for applications requiring low MFR (e.g., pipe extrusion). For this purpose, a recyclate made of a conventionally sorted PP waste fraction is compared to recyclates made from only EBM PP waste samples. In order to establish the characteristics of a recyclate from optimal sorting as a reference, the EBM fraction was manually sorted from the PP waste. Different washing procedures and production processes are compared to investigate possible further reduction of the MFR. In addition to MFR measurements, rheological analyses are carried out using a plate–plate rheometer. Furthermore, differences in the composition as well as the mechanical and thermal properties of the recyclates are analyzed. The mechanical properties are investigated with tensile and Charpy impact tests. Differential scanning calorimetry (DSC) and thermogravimetric analysis (TGA) are used to determine the thermal properties such as melting temperature and degradation temperature as well as the filler content. The chemical structure is investigated with Fourier transform infrared (FTIR) spectroscopy.
2 EXPERIMENTAL
2.1 Material and sample preparation
The waste samples for the production of the recyclates were obtained from various PP waste bales kindly provided by PreZero Austria GmbH. The PP fraction from the waste bales was hand-sorted according to processing methods (IM, EBM, TF, and FE). The IM fraction consisted mainly of food containers, such as containers and lids for ice cream and spreads, and buckets. Typical EBM products were detergent, shampoo, and ketchup bottles. The TF fraction included thin-walled plant pots, yoghurt cups, and fruit and vegetable container, and the FE fraction included pasta packaging and sweets wrapping. The used mixed PP fraction consisted of 47% IM, 26% EBM, 23% TF, and 4% FE. This ratio was defined based on the results of a preliminary study, in which the proportions of the different processing method grades in PP waste bales were examined.23 In order to produce recyclates with lower MFR values, a waste fraction containing only manually sorted EBM products was used. The EBM fraction was chosen as the EBM grades are known to have the lowest MFR values in the PP packaging waste stream.25 With regard to future adaptation of sorting systems, it is assumed that the EBM fraction can be sorted out and recycled more easily than other low MFR streams, such as films, which are difficult to sort due to their thinness and possible multi-material compositions.37-39
To ensure that no other materials (e.g., caps made of PE) or processing methods (injection molded nozzles) were present in the used EBM stream, caps, spray nozzles, and sleeves were removed from the EBM products. Furthermore, all used samples from both the mixed and the EBM fraction, were cold prewashed (ca. 20°C) with a conventional washing machine of the type IWC6145 (Indesit Co., Italy). Afterwards the samples were analyzed by FTIR spectroscopy in attenuated total reflectance (ATR) mode using a SpectrumTwo spectrometer (PerkinElmer, Inc., USA) to identify the polymer type. Measurements were made in the range of 4000–650 cm−1 with a resolution of 4 cm−1. The measurements were taken from the surface of each waste sample. Films were measured on both the front and back side to check if they consist of more than one polymer type. NonPP or multi-material objects were discarded so that only PP samples were used for the production of the recyclates.
The samples were then shredded into flakes of <20 mm using a single shaft shredder of the type WS 11–15 (Wagner Maschinenbau GmbH, Austria). The flakes were then washed in a commercial washing machine of the type PW818 (Miele, Germany). The mixed fraction (MIX_CW_F) and one part of the EBM fraction (EBM_CW_F) was cold-washed (CW) at 20°C. The other part of the EBM fraction was washed with 60°C (hereafter referred to as “hot-washed” or HW) in order to compare different washing temperatures. Both programs ran for 60 min, with 15 min of cold or hot wash at 45 rpm, spin at 400 rpm, 19 min of cold rinse at 45 rpm, spin again at 400 rpm, cold rinse at 45 rpm and then spin again at 400 rpm. After washing, the flakes were dried at 50°C in a convection oven for about 15 h. After drying, all flakes were shredded to smaller flakes before further processing using a cutting mill of the type SM 300 (Retsch GmBH, Germany). With the exception of one part of the hot-washed EBM material, all of the other fractions were pelletized into granules including a melt filtration step. The recyclate from the hot-washed, pelletized, and melt-filtered stream is further referred to as EBM_HW_F, while the recyclate from the hot-washed, nonpelletized, and nonfiltered stream is labeled as EBM_HW_N. The EBM_HW_N was directly injection molded to investigate the influence of omitting the pelletizing and melt filtration step. The pelletizing of the other fractions was done using a ZSE 18 MAXX twin-screw extruder (Leistritz Extrusionstechnik GmbH, Germany) with corotating screws using a screen filter with a mesh size of 250 μm. The mass throughput ranged between 2 and 2.7 kg h−1 and the screw speed was between 150 and 200 rpm. The variations in mass throughput and screw speed were a consequence of the low bulk density of the flakes. In general, these two parameters can influence the mixing and residence time and therefore quality of recyclates leaving the extruder.40-42 However, investigating these effects was not part of this work. Multipurpose test specimens of Type 1A and bar test specimens (Type 1) were then produced from the granules or flakes using a hydraulic injection moulding machine of the type Victory 60 (ENGEL Austria GmbH, Austria) in accordance with ISO 19069-2.43-45 Because of differences in the MFR, the mixed fraction was processed with a melt temperature of 200°C and the EBM fraction with a temperature of 230°C. The further used names of the four produced recyclates and the information about their source material and processing differences are summarized in Table 1.
Recyclate name | Description |
---|---|
MIX_CW_F | Mixed fraction, cold washed, pelletized with melt filter |
EBM_CW_F | EBM fraction, cold washed, pelletized with melt filter |
EBM_HW_F | EBM fraction, hot washed, pelletized with melt filter |
EBM_HW_N | EBM fraction, hot washed, directly injection molded (not pelletized, no melt filtration) |
- Abbreviations: EBM, extrusion blow molding.
2.2 Material testing
2.2.1 Density and melt flow properties
The produced recyclates were tested and compared with different physical, mechanical, and thermal testing methods. The density and thus information about possible morphological differences or content of fillers or polymeric impurities was measured with an analytic balance of the type XS205BDU Dual Range (Mettler Toledo, USA) in accordance to ISO 1183-1.46 Four measurements per recyclate were performed on cut pieces from the multipurpose specimens. To determine the impact of the sorting on the melt flow properties, MFR values of the produced granules were measured according to ISO 1133-1 on an MF20 melt flow tester (CEAST, Italy).47 Since the EBM_HW_N recyclate was not available in form of granules, measurements were also carried out on small pieces cut from multipurpose specimens of the four recyclates. The MFR measurements were conducted at a temperature of 230°C with a mass of 2.16 kg.
As the MFR is only a single point measurement, additional rheological investigations were carried out. Rotational and oscillatory rheological characterization of the samples was performed using a Physica MCR 501 rheometer (Anton Paar, Austria). The samples were cut from the injection molded specimen. All experiments were carried out in a plate–plate configuration with a plate diameter of 25 mm and a gap between the two plates of 1 mm. The measurements were performed at 230°C in a flowing nitrogen atmosphere. In rotational mode, the shear dependent viscosity (η) of the samples was determined between the shear rates () of 0.001 and 1 s−1. In oscillatory shear experiments, the complex viscosity (η*), the storage (G′), and loss modulus (G″) were determined for circular frequencies (ω) between 0.1 and 500 rad s−1. To ensure tests in the linear viscoelastic range, strain sweeps were performed and a fixed strain of 2% was chosen for the oscillatory experiments. The crossover point was evaluated as the intersection of the G′ and G″ curves of each sample.
2.2.2 Mechanical tests
Tensile tests were performed to investigate differences in the mechanical properties of the recyclates. The tensile tests were carried out according to ISO 527-1 and ISO 527-2 using a Zwick Z005 (ZwickRoell GmbH & Co. KG, Germany) equipped with 5 kN load cell and a sensor arm extensometer.48, 49 For every recyclate five specimens were measured. At the beginning of the measurements, the test speed was 1 mm min−1 and the Young's modulus was evaluated between a strain of 0.05% and 0.25%. After Young's modulus determination, the test speed was switched to 50 mm min−1. Because of the machine limitations, the measurements were stopped after reaching a strain of 470%.
Charpy notched impact tests were carried out in order to investigate the toughness of the recyclates under impact loading. The recyclates were compared based on their notched impact toughness and thus sensitivity toward stress concentrators (i.e., defects in the material). The tests were performed on a pendulum impact tester of the type Zwick HIT25P (ZwickRoell GmbH & Co. KG, Germany) using a 2 J pendulum. The tests were conducted in accordance with ISO 179-2 on Type 1 specimens with a V-notch (according to 179–1/1eA).45, 50 For each recyclate 10 samples were measured. Both the tensile test and the impact tests were performed at room temperature.
2.2.3 Thermal properties
The thermal properties were investigated with DSC and TGA. To analyze differences in the melting and crystallization behavior, DSC measurements were performed using a DSC4000 (PerkinElmer, Inc., USA). Nitrogen was used as purge gas and the gas flow was set at 50 mL min−1. Three specimens of approximately 10 mg were measured per recyclate cut from the multipurpose specimens. The temperature program consisted of the following steps: an isothermal of 1 min at 25°C, heating from 25 to 200°C, an isothermal of 1 min at 200°C, cooling from 200 to 25°C, an isothermal of 5 min at 25°C and a second heating from 25 to 200°C. The temperature rate during the heating and cooling steps was set to 10°C min−1. The enthalpy and temperature of melting and crystallization were evaluated according to ISO 11357-3.51 The degree of crystallinity was calculated using a value for the melting enthalpy of 100% crystalline PP of 207 J g−1.52
In order to investigate differences in the decomposition temperature and filler content, TGA measurements were performed. The measurements were conducted on a thermogravimetric analyzer of the type TGA/DSC 3+ (Mettler Toledo, USA) on samples of approximately 10 mg, also cut from the multipurpose specimens. Three TGA measurements per recyclate were carried out. The temperature program included an isothermal of 1 min at 25°C and a heating ramp from 25 to 850°C with a heating rate of 10°C min−1 followed by a gas switch to oxygen and an isothermal of 10 min. The gas switch was performed to investigate possible further weight loss due to thermo-oxidation. The temperature value at 5% weight loss (T5%) compared to the value before the decomposition step was considered to be the start of decomposition.
2.2.4 Infrared spectroscopy
To determine differences in the chemical constitution of the produced recyclates, FTIR-spectroscopy in ATR-mode was performed on the multipurpose specimens using a SpectrumTwo spectrometer (PerkinElmer, Inc., USA) equipped with a Quest ATR unit (Specac Ltd., United Kingdom) with a diamond crystal. The spectra were measured in the range of 650 to 4000 cm−1, averaging four scans with a resolution of 4 cm−1 for each spectrum. For each recyclate, three spectra were recorded at the surface of the multipurpose specimens and at the cross section of the longitudinally halved specimens. The spectra were baseline corrected and then normalized with the standard normal variate method, in which each spectrum is subtracted by its mean and then divided by its standard deviation.
3 RESULTS AND DISCUSSION
3.1 Density and melt flow properties
Figure 1 compares the densities of the different recyclates. The recyclate from mixed PP products (MIX_CW_F) exhibited a density of 0.928 g cm−3, which is notable higher compared to the recyclates from EBM products, which all showed a density between 0.908 and 0.909 g cm−3. The difference may be explained by a higher amount of fillers (e.g., talc and calcium carbonate) or a higher crystallinity in the MIX_CW_F.53 This is further discussed in the results section of the thermal properties and infrared spectroscopy.
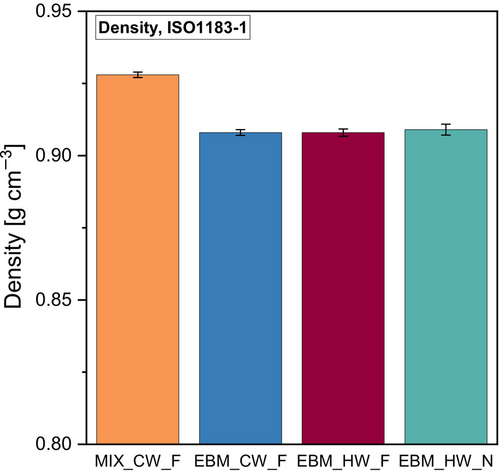
The results of the MFR measurements on the produced granules and cut pieces from the multipurpose specimen are shown in Figure 2. A significant difference was found between the EBM recyclates and the MIX_CW_F recyclate. The MIX_CW_F granules showed an MFR of 13.4 g 10 min−1, whereas the recyclates from EBM products, EBM_CW_F, and EBM_HW_F, showed MFR values of 2.8 and 2.1 g 10 min−1, respectively. The EBM recyclates would therefore be suitable for processing methods and applications requiring low MFR. With the MFR reduction, the EBM recyclates meet the requirement of MFR ≤3 g 10 min−1 set in EN 1451-1 for piping systems for soil and waste discharge.30 For applications in need of even lower MFR, such as in standards for other pipe applications, the recyclates could be blended with virgin material to achieve the target.26-29, 54 However, different applications have different additional requirements. For example, for the use in pipes, among other requirements, the long-term properties of the materials are crucial. These need to be investigated before the suitability of the recyclates or their blends with virgin materials in pipes can be confirmed.26, 55, 56 Nevertheless, with the lower MFR of the recyclates, a higher content or even the recyclate without blending can generally be used for extrusion, TF or again for EBM applications.
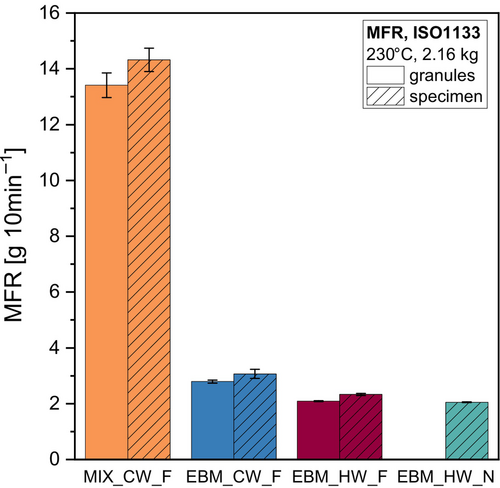
During the production of the recyclates, the material may have experienced degradation. This has been shown by several previous studies investigating the impact of reprocessing on plastics.18, 22, 57, 58 Degradation of PP leads to chain scission resulting in shorter chains and thus higher MFR values.22, 59 In this study, no stabilizers were re-added during reprocessing. Therefore, the MFR values of the recyclates could have been even lower with the addition of stabilizers.7
As previously stated, MFR measurements were also performed on multipurpose specimens to compare the hot-washed, nonfiltered recyclate (EBM_HW_N) with the other recyclates. The measurements on the cut specimens showed higher values than those on the granules, which can be attributed to degradation during the additional IM step. Compared to the other recyclates, EBM_HW_N showed the lowest MFR. This can be attributed to the lower thermo-mechanical stress due to the omission of the pelletizing step.36
Since MFR measurements provide only single-point values, rheological measurements were performed using a plate–plate rheometer to further investigate the viscosity of the recyclates. Figure 3 shows representative viscosity curves for the four recyclates. Data from both the rotational and oscillatory measurements are shown. Over the entire investigated shear rate and angular frequency range, the EBM recyclates have significantly higher viscosities than the MIX_CW_F. This is in line with the lower MFR values found for the EBM recyclates. In the lower shear rate range below 0.01 s−1 (i.e., Newtonian plateau region), the EBM recyclates from the hot-washed flakes showed higher values than the EBM_CW_F. The higher viscosity in this region (zero viscosity) implies a higher average MW of the EBM_HW recyclates compared with the EBM_CW recyclate.60-62 The differences between the zero viscosities of the EBM and MIX recyclates indicate a higher average MW of the EBM recyclates, but to compare polymers in this way, their chemical structures and MWD should be similar. The higher zero viscosity of the EBM recyclates correlates with the results of the crossover point (see Figure 4 and Table 2), as lower crossover frequencies (ωc) are attributed to a higher average MW.60 EBM_HW_F and EBM_HW_N showed lower ωc values than EBM_CW_F, indicating an even higher average MW. The crossover modulus of the recyclates showed similar values, indicating similar MWD. As mentioned above, rheological properties as discussed here, also depend on other factors, such as mixing constituents, polymer type and grade, and chemical structures. Since the investigated materials are a mixture of different PP types and grades, statements about differences in MW and MWD from the discussed data must be used with caution. Other analytical methods, such as gel permeation chromatography (GPC), can be performed to make more accurate statements about the MW and MWD of the recyclates.
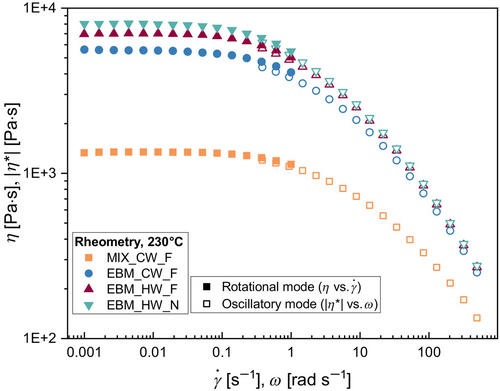
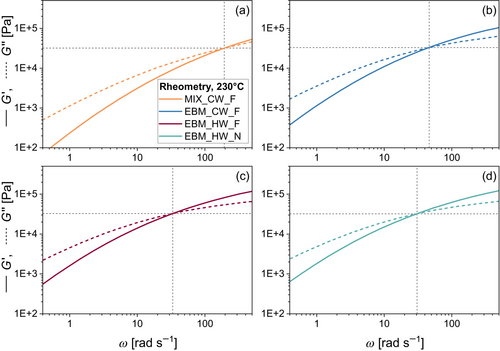
Recyclate | ωc (s−1) | Gc (kPa) |
---|---|---|
MIX_CW_F | 199 ± 4.42 | 31.1 ± 0.66 |
EBM_CW_F | 46.7 ± 0.51 | 33.5 ± 0.53 |
EBM_HW_F | 33.4 ± 0.31 | 32.6 ± 0.03 |
EBM_HW_N | 31.3 ± 1.09 | 31.9 ± 0.26 |
- Abbreviations: Gc, crossover modulus; ωc, crossover frequency.
The difference between the MFR values and the viscosity of the cold (EBM_CW_F) and hot washed (EBM_HW_F) recyclates could derive from different reasons. On the one hand, low MW contaminants, which are often found in recyclates, may have been better removed during washing with higher temperature.32, 63 However, further experimental investigations are needed to confirm this assumption. On the other hand, there may have been differences in the composition of the EBM streams used for the preparation of these two recyclates. The EBM_HW_N, where no pelletization with melt filtration was conducted, showed the lowest MFR and highest viscosity in the low shear rate range. This may be explained by less thermo-mechanical stress and therefore less degradation.36
3.2 Mechanical tests
The mechanical properties determined via tensile tests are shown in Table 3. The recyclate from the mixed fraction (MIX_CW_F) showed a higher Young's modulus than the recyclates from EBM products. Differences in the modulus can generally be attributed to various reasons. In this case, possible reasons could be differences in the molecular structure or in the amount of the different PP types (homopolymer, block or random copolymer), differences in the crystalline structure and crystallinity and different amounts of fillers.53, 64-66
Recyclate | Et (MPa) | σt (MPa) | εb (%) | acN (kJ m−2) |
---|---|---|---|---|
MIX_CW_F | 1346 ± 12 | 27.6 ± 0.2 | 38.6 ± 12 | 5.15 ± 0.67 |
EBM_CW_F | 1009 ± 12 | 26.5 ± 0.2 | >459 | 7.66 ± 0.57 |
EBM_HW_F | 1004 ± 13 | 26.6 ± 0.3 | >461 | 8.41 ± 0.50 |
EBM_HW_N | 1015 ± 14 | 26.8 ± 0.2 | 453 ± 12 | 8.92 ± 0.85 |
- Abbreviations: acN, Charpy notched impact strength; Et, Young's modulus; εb, strain at break; σt, tensile strength.
The lower Young's modulus of the EBM recyclates in the range of 1000 MPa is similar to the values found for PP random copolymers, while the value of 1350 MPa from the MIX_CW_F is more in line with the values found for PP homopolymers and block copolymers.25, 67 No differences were detected in the Young's modulus of the differently washed and processed EBM recyclates. The tensile strength (i.e., tensile stress at yield) of the EBM recyclates was only slightly lower than that of the MIX_CW_F. No significant differences were found between the three EBM recyclates. The strain at break value of the EBM recyclates was significantly higher (above 450%) than that of the mixed recyclate (39%). It can be concluded that the recyclates from the EBM fraction are more ductile than the one from the MIX_CW_F. This is consistent with the lower MFR and higher zero viscosity of the EBM recyclates. A lower MFR and higher viscosity is associated with longer chain lengths, which results in a higher degree of entanglements and a greater distance in which the chains can slide past each other under tension.24 Because of the aforementioned machine limitations, the strain at break of EBM_CW_F and EBM_HW_F can only be stated to be greater than 459% and 461%, respectively (see Table 3). Some of the samples failed before 470%, whereas others would have possibly shown higher values but had to be stopped at 470%. The potential influence of crystallinity and filler content on the tensile properties is discussed in more detail in the following sections.
The Charpy notched impact strength of the four recyclates is also given in Table 3. Under the applied conditions and test parameters, brittle fracture was observed for all specimens, indicated by complete fracture. In general, the notched impact strength is mostly influenced by PP type (i.e., homo or copolymer), MW and MWD, fillers, and crystallinity.68-70 The recyclates from the sorted EBM fraction showed higher Charpy notched impact strengths than the recyclate from the mixed fraction. This correlates with the lower MFR found for the EBM recyclates, indicating a higher average MW of the chains, which generally leads to higher impact toughness.24, 64 However, the higher filler content of the MIX_CW_F determined by TGA and FTIR (discussed in the next sections) may also have influenced the results. The three different EBM recyclates showed no significant difference in the notched impact strength as they are all within the scatter range.
The differently washed EBM recyclates did not show significant differences in their mechanical properties. There could be several reasons for this. Because of the manual sorting, the removal of sleeves and so on, and the prewashing prior to the actual washing process of the flakes, the used waste streams have generally contained fewer contaminants than real waste streams. In addition, the temperature difference between 20 and 60°C may have been too small to have a significant effect on the quality. Comparing EBM_HW_F and EBM_HW_N, melt filtration did not lead to an improvement in the mechanical performance. However, as mentioned above, the used waste streams had a higher degree of purity than the conventional waste stream used for recycling. In industrial recycling, melt filtration cannot be omitted without quality degradation.
3.3 Thermal properties
In Figure 5 the representative DSC curves of the cooling and the second heating are presented. As can be seen, the MIX_CW_F has a higher crystallization and melting temperature than the EBM recyclates. The melting temperature of MIX_CW_F is at about 166°C, which is usually observed for PP homo and block copolymers.53 In contrast, the three EBM recyclates showed melting temperatures in the range of 155°C. This is lower than the melting temperatures for homo and block copolymers, but higher than or at the upper limit of the melting temperature found for PP random copolymers.53 The difference in the melting temperatures between the EBM recyclates and the MIX_CW_F can be explained by a higher amount of random copolymers in the EBM stream compared with the mixed stream. This explanation would be consistent with the results of the tensile tests, where a lower Young's modulus typical of random copolymers was determined for the EBM recyclates. A closer look at the heating curves of the EBM recyclates showed shoulders before the main melting peak, whereas MIX_CW_F did not show such a pronounced shoulder (see blue colored area in Figure 5b). It can also be seen that both the MIX_CW_F and the EBM_CW_F showed small peaks in the area of 125°C. These small peaks may indicate small amounts of PE in these two recyclates.22, 71 However, since these peaks are very small, they may also originate from sufficiently long and thus crystallizable ethylene sequences.72 Such sequences are typically found in block copolymers.26, 72 The mean values of the melting and crystallization temperatures and enthalpies as well as the degrees of crystallinity are given in Table 4. The enthalpies and degrees of crystallinity were calculated taking into account the filler content determined via TGA (discussed below). Differences in the melting enthalpy and thus crystallinity may originate from different compositions, that is, different amounts of different PP types (homopolymer, block copolymer, and random copolymer), additives and fillers.64, 70, 73 The MIX_CW_F showed higher stiffness than the other recyclates, while the degree of crystallinity in the first heating was similar compared to EBM_HW_F and EBM_HW_N. Only the EBM_CW_F showed slightly lower values than MIX_CW_F. This indicates that not only the crystallinity but also other factors such as the crystalline structure (e.g., lamellar thickness and spherulite size) and tie molecules have an influence on the mechanical properties, which has already been discussed in the literature.65, 74
1st heating | Cooling | 2nd heating | ||||||
---|---|---|---|---|---|---|---|---|
Recyclate | TM1 (°C) | ΔHM1 (J g−1) | XC1 (%) | TC (°C) | ΔHC (J g−1) | TM2 (°C) | ΔHM2 (J g−1) | XC2 (%) |
MIX_CW_F | 164.5 ± 0.2 | 88.5 ± 4.7 | 42.8 ± 2.3 | 123.6 ± 0.2 | 95.1 ± 3.3 | 163.1 ± 0.2 | 95.0 ± 3.1 | 45.9 ± 1.5 |
EBM_CW_F | 155.9 ± 0.5 | 71.4 ± 3.2 | 34.5 ± 1.5 | 119.2 ± 0.3 | 78.4 ± 1.3 | 155.0 ± 0.3 | 77.9 ± 0.6 | 37.6 ± 0.3 |
EBM_HW_F | 155.3 ± 1.1 | 77.0 ± 4.0 | 37.2 ± 1.9 | 119.2 ± 0.1 | 82.1 ± 1.3 | 154.7 ± 0.1 | 83.5 ± 3.2 | 40.4 ± 1.6 |
EBM_HW_N | 154.8 ± 0.6 | 83.3 ± 4.8 | 40.3 ± 2.3 | 118.2 ± 0.2 | 86.8 ± 4.5 | 154.3 ± 0.2 | 88.7 ± 4.0 | 42.8 ± 1.9 |
- Abbreviations: TC, crystallization temperature; TM, melting temperature; XC, degree of crystallinity; ΔHC, crystallization enthalpy; ΔHM, melting enthalpy.
Representative TGA curves of the four recyclates are shown in Figure 6. The first decomposition step of the MIX_CW_F is located at a T5% of 410°C, while the three EBM recyclates showed a T5% of 406–407°C. These temperatures are within the typical decomposition temperature range of PP.52 However, differences were detected in the residual weight after this first decomposition step. The residual weight of the MIX_CW_F determined at 525°C was 4.0% and thus higher than for the EBM recyclates where it was about 0.7%–0.8%. In contrast to the three EBM recyclates, the MIX_CW_F sample showed a second decomposition step at a T5% of 593°C. This step is attributed to the decomposition of calcium carbonate, which decomposes into carbon dioxide and calcium oxide.52 The residual weight of the MIX_CW_F sample after the second step at 700°C was 3.0%, indicating additional nondecomposed inorganic fillers. The higher filler content in MIX_CW_F is plausible as the conventionally sorted stream contains several different products. Besides food contact containers, the mixed stream also consisted of plant pots, buckets, and so on, which may have higher filler contents. The EBM stream consisted mainly of food contact and detergent bottles, which are assumed to have lower filler contents. After changing the gas from nitrogen to oxygen at 850°C, no significant further weight loss of the samples was observed. The higher mass of residues found for MIX_CW_F correlates with the findings of the density measurements, where MIX_CW_F showed a higher density than the other recyclates. No difference in the decomposition step or the residual weights were found between the different EBM recyclates was detected, which may be due to the higher purity of the used waste streams.
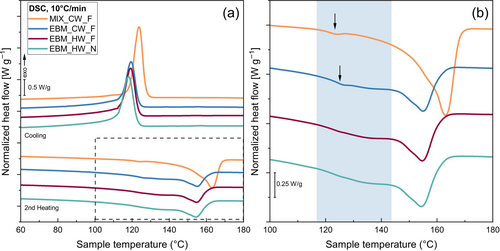
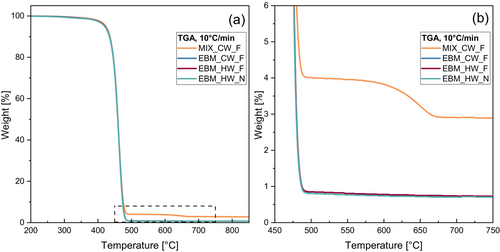
3.4 Infrared spectroscopy
The FTIR-ATR spectra of the surface and the cross section of the injection-molded specimen are shown in Figure 7. The entire FTIR spectra of the samples are depicted in Figure 7a,b, the former showing the spectra measured at the cross section and the latter the spectra measured at the surface. Figure 7c,d shows specific regions of interest of the spectra measured at the cross section. Typical PP peaks were found in the spectra of the recyclates. These include several peaks between 2950 and 2830 cm−1, two peaks between 1450 and 1370 cm−1, a peak at 1167 cm−1, two peaks between 990 and 970 cm−1, and peaks at 899, 841, and 809 cm−1.75 The spectra from the surface of the samples (Figure 7b) showed additional peaks compared to the spectra from the cross section (Figure 7a). Broad peaks were observed between 3600 and 3000 cm−1 and at around 1600 cm−1, which can be attributed to the presence of hydroxyl groups. Such hydroxyl groups may be a result of aging due to oxidation or the presence of polar contaminants and surface bound water.75, 76 Especially in the spectrum of EBM_HW_N, it is visible that besides the broad peak also small peaks are present in this wavenumber area. These peaks at 3393 and 3180 cm−1 are typical for NH2 stretching vibration and may originate from amide-containing slip agents such as erucamide.75, 77 This is consistent with the peak found at 1645 cm−1 attributed to carbonyl and NH2 groups also usually found in amide-containing slip agents.77 However, peaks in the range between 1550 and 1800 cm−1 may also derive from a series of functional groups produced during thermal degradation or oxidation. All recyclates, both on the surface and the cross section, showed peaks at 1776 and 1739 cm−1 (see Figure 7c). These peaks are often related to carbonyl groups originating from degradation products of PP, or stabilizers.75, 78, 79 All recyclates exhibit peaks at 721 and 729 cm−1 that can be ascribed to ethylene units. Such peaks are usually found in PE but are also present in spectra from PP copolymers.73, 75 However, the ratio of their intensities differs between MIX_CW_F and the other recyclates, indicating differences in the ethylene content and thus structure and amount of copolymers in the recyclates. According to Gahleitner et al. a peak at around 733 cm−1 is an indication for random copolymers, while a peak at 720 cm−1 indicates block sequences of block copolymers.73 Since the ratio between the peaks at 729 and 721 cm−1 is higher for the EBM recyclates, it can be concluded that the EBM recyclates contain a higher amount of random copolymer than the MIX_CW_F. This finding is in accordance with the results from the DSC measurements, where the EBM recyclates showed lower melting temperatures.
The peaks at 1016 and 670 cm−1 in the spectrum of MIX_CW_F (Figure 7c,d) can be attributed to talc.75 As can be seen in Figure 7d, a peak at 875 cm−1 is present in the spectrum of MIX_CW_F, indicating that this recyclate also contains calcium carbonate.75 The peaks of talc and calcium carbonate (CaCO3) correlate with the results of the TGA measurements, where the second decomposition step in the curve of the MIX_CW_F was attributed to CaCO3 and the residual weight was explained by residual filler. Fillers such as talc and CaCO3 are known to affect the properties of polymers. The particles themselves can have a direct effect on the mechanical properties or the fillers act as nucleating agents, thus influencing the crystalline structure.80-83 Such fillers generally lead to an increase in Young's modulus and a decrease in tensile strength and strain at break.82-85 However, the effect also depends on factors such as filler size, shape, and so on.86 Mineral fillers can either increase or decrease the impact toughness also depending on the aforementioned factors such as size, aspect ratio, and dispersion.85 The higher filler content in the MIX_CW_F compared with the other recyclates, as determined by TGA and FTIR, may therefore have contributed to the differences in the mechanical (e.g., higher stiffness) and thermal properties (e.g., lower crystallization temperature). However, at the rather low concentrations found in the TGA measurements, the fillers were more likely to influence nucleation, lamella thickness, and spherulite structure than the particles having a direct effect on mechanical properties.65
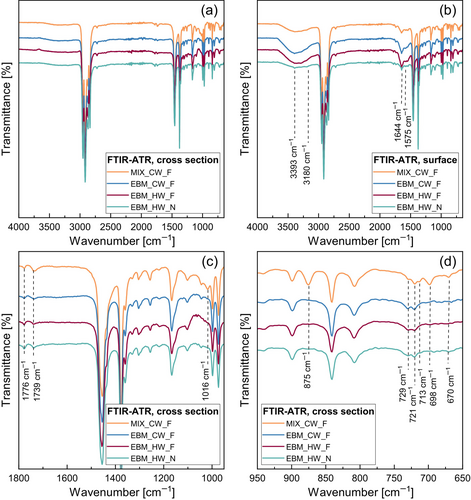
3.5 Possibilities for implementing sorting by processing grade
In order to achieve sorting by processing grade (IM, EBM, and TF) during PP recycling, current sorting systems need to be adapted. The separation of EBM products from a PP waste stream could be achieved using object recognition systems, as the EBM stream contains mainly bottles that can be recognized by their shape.87, 88 However, this will also introduce caps and other unwanted attached products into the stream. It is therefore reasonable to sort the waste in the shredded form. In this way, caps and nozzles are no longer attached to the bottles and the EBM material can be separated from other polymers or grades without contamination. Spectroscopic sorting systems are required to sort the shredded waste. Currently, these do not distinguish between different PP grades. In order to be able to sort PP waste by processing method or MFR, the NIR sorting systems currently used need to be improved.
Recent studies showed the potential for improving the mechanical sorting in plastics recycling.13, 89-91 They indicated that plastics can be better sorted by adjusting the measurement setup or improving the data analysis methods.13, 90, 91 The study by Bredács et al. showed that PE samples with different densities can be categorized into different classes using multivariate data analysis (MVDA) of NIR data from an industrial sorting line.90 The use of another spectroscopic technique even showed promising results in predicting the density and MFR of PE.90 Another study demonstrated the potential to improve the sorting of PP grades.91 MVDA of NIR spectra was used to show a possible differentiation between different PP types (homo and copolymers) and different processing grades.91 However, further work is required to confirm the results in industrial scale sorting trials.
4 CONCLUSION
This work investigates the feasibility of producing recycled PP with low MFR from packaging waste. For this purpose, a recyclate from a conventionally sorted PP waste stream was compared with recyclates from a stream consisting only of manually sorted PP EBM grades. In addition, different washing and production processes were compared to investigate the effect on the properties of the recyclates.
Recyclates from the EBM stream exhibited a significant reduction in the MFR. With the MFR values achieved, the recyclates can be used in extrusion, TF or again in blow molding applications. The values even meet the requirements for specific pipe applications. Compared to the recyclate from the conventional sorted stream, the EBM recyclates showed higher ductility and notched impact toughness but lower stiffness. This can be attributed to a higher PP-R content and the lower MFR (i.e., higher MW). The EBM recyclates showed a lower filler content compared with the recyclate from conventional sorting, which may also have influenced the differences in properties. Washing at a higher temperature showed no significant differences in the mechanical and thermal properties compared with the cold washing. However, the recyclate made from the hot-washed flakes showed a slightly lower MFR and higher viscosity. Omitting the regranulation step resulted in a further slight decrease in the MFR attributed to less material degradation.
This work highlights the potential for improving the quality of PP recyclates through enhanced sorting. It was based on manual sorting to determine the best possible results as a benchmark for future automatic sorting trials. However, the realization of automatic sorting of PP waste according to processing methods requires further development of NIR sorting systems, which will be part of future work.
AUTHOR CONTRIBUTIONS
Jutta Geier: Conceptualization (equal); formal analysis (lead); investigation (lead); methodology (lead); validation (lead); visualization (lead); writing – original draft (lead). Chiara Barretta: Investigation (supporting); validation (supporting); writing – review and editing (supporting). Jessica Hinczica: Investigation (supporting); validation (supporting); writing – review and editing (supporting). Bernd Haar: Investigation (supporting); validation (supporting). Márton Bredács: Conceptualization (equal); methodology (supporting); project administration (lead); writing – review and editing (supporting). Andreas Witschnigg: Conceptualization (equal); resources (supporting); writing – review and editing (supporting). Erwin Mayrbäurl: Conceptualization (equal); resources (supporting). Gernot Oreski: Conceptualization (supporting); funding acquisition (lead); methodology (supporting); supervision (lead); writing – review and editing (supporting).
ACKNOWLEDGMENTS
The research work was performed within the COMET-project “Improving the quality of recycled polymer waste” (FFG project-no.: 879785) at the Polymer Competence Center Leoben GmbH (PCCL, Austria) within the framework of the COMET-program of the Federal Ministry for Climate Action, Environment, Energy, Mobility, Innovation and Technology and the Federal Ministry for Labor and Economy with contributions by PreZero Polymers Austria GmbH, Poloplast GmbH & Co KG and the University of Leoben (Chair of Materials Science and Testing of Polymers). The PCCL is funded by the Austrian Government and the State Governments of Styria, Lower Austria and Upper Austria.
Open Research
DATA AVAILABILITY STATEMENT
The data that support the findings of this study are available from the corresponding author upon reasonable request.