Sustainable Design of Structural and Functional Polymers for a Circular Economy
Graphical Abstract
Structural and functional polymers provide functions, sustainability benefits, and CO2 savings during their use phase, but present challenges at end of life. Polymer science and adjacent disciplines can enable a circular economy of polymers via biodegradation or recycling through the application of strategies for molecular and system design that leverage the latest advances in the field.
Abstract
To achieve a sustainable circular economy, polymer production must start transitioning to recycled and biobased feedstock and accomplish CO2 emission neutrality. This is not only true for structural polymers, such as in packaging or engineering applications, but also for functional polymers in liquid formulations, such as adhesives, lubricants, thickeners or dispersants. At their end of life, polymers must be either collected and recycled via a technical pathway, or be biodegradable if they are not collectable. Advances in polymer chemistry and applications, aided by computational material science, open the way to addressing these issues comprehensively by designing for recyclability and biodegradability. This Review explores how scientific progress, together with emerging regulatory frameworks, societal expectations and economic boundary conditions, paint pathways for the transformation towards a circular economy of polymers.
1 Introduction
Since the groundbreaking recognition of their nature as macromolecules,1 and their accessibility through synthetic chemical approaches, polymers have greatly expanded the spectrum of materials used by humankind. The nearly endless variety of properties that can be achieved, combined with their ready large-scale production from abundant fossil oil, made polymers a key industrial product since the 1950s, a basis of today's quality of life (Figure 1), and driver of global economic prosperity. Polymers in structural applications or “plastics” are used in the largest volumes in everyday life and combine cost-efficiency in production with ease of processing, a range of beneficial properties, and longevity. Such polymers, among their many uses, protect perishable food as packaging, safeguard health as sterile medical materials, and allow lightweight, durable technical constructs. Equally important are not as visible uses as functional polymers,2 in applications as diverse as enabling detergents, making available active ingredients in pharmaceuticals, and providing critical functions to personal care products, cosmetics and paints.3 They are also key reactive ingredients in resins or coatings and themselves give rise to new materials, composites, and adhesives.
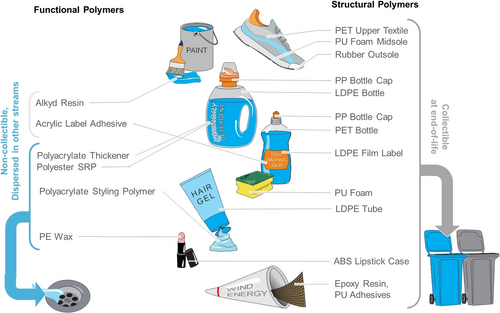
Selected examples of different types of polymers found in almost every class of products used in modern life. They fulfill structural purposes, such as in shoes, bottles or as polymer foams. Items made from structural polymers can in principle be collected at the end of their life. Functional polymers, on the other hand, are typically invisible as ingredients in products, such as cosmetics, detergents, and paints. In this case, in their application they are dispersed and therefore typically not collectable. Furthermore, in some cases such as cosmetics or detergents, they end up in wastewater. (PET: polyethyleneterephthalate, PU: polyurethane, PP: polypropylene, LDPE: low-density polyethylene, ABS: acrylnitrile butadiene-styrene copolymer, SRP: soil-release polymer, PE: polyethylene).
Structural and functional polymers are essential to establish an economy with net-zero CO2 emissions (Figure 2). They make the production of many goods possible with low energy inputs compared to alternative materials, reduce greenhouse gas (GHG) emissions as insulating materials,4 allow the construction of wind turbines for renewable energy generation, decrease energy consumption by reducing the weight of cars and trains,5 and by minimizing drag for airplanes with structured biomimetic films.6 By increasing efficiency,7 functional polymers lower energy consumption and support low-temperature cleaning.8 In addition, they extend lifetime of structures made from intrinsic CO2-intensive materials such as concrete and steel, by coatings and corrosion protection.9
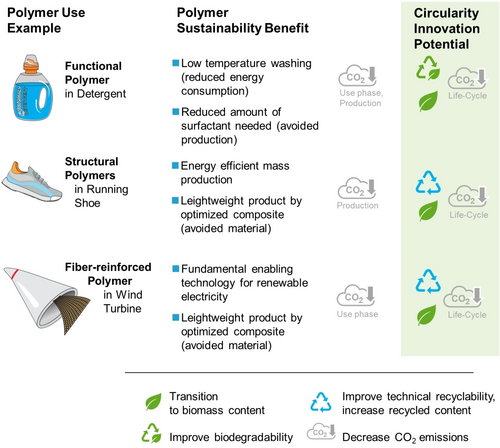
Selected examples of benefits of current structural and functional polymers in their application, together with the innovation potential for sustainability. Considering the whole life cycle, circularity and CO2 emission neutrality are the big levers to improve via polymer and product design.
From 1950 to 2015, close to 8000 Mt of structural polymers (including synthetic fibers) was made, and this amount has increased yearly at a rate of 8.4 % (CAGR).10 In comparison, around 35 Mt of functional polymers in liquid formulations was estimated to have been produced.2 As with all economic activities at scale that have considered neither external environmental and societal effects, nor limitations imposed by ecological planetary boundaries,11 this enormous success has led to significant negative impacts; the ubiquity and durability of polymers has escalated the issue of mismanaged waste polluting land and sea,12 exacerbated in global regions where the established waste collection infrastructure has not kept up with plastics usage. Together with waste proliferation, the pervasiveness of microplastics in the environment has been recognized.13 As yet another dimension, the fossil nature of >98 % of polymers produced today14 and the prevalent disposal pathway via incineration significantly contribute to CO2 emissions during the life cycle, with the contribution from the plastics value chain projected to be as high as 15 % of the global emission budget for 1.5 °C in 2050.15
A sustainable circular economy for polymeric materials reconciles these two sides. For both structural and functional polymers, chemistry as a field should aspire to:
-
support decoupling from fossil raw material inputs and help to drive CO2 emission neutrality through the introduction of recycled and biobased feedstock, and to
-
ensure that at end-of-life, polymers either are collected and economically and sustainably recycled via a technical pathway, or they should be completely biodegradable16 if they are not collectable and dispersed in the application.
2 Safe and Sustainable by Design
In addition to the traditional technical performance requirements and cost effectiveness, sustainability dimensions must already be reflected in the design of future polymers. Such forward-thinking development is increasingly anchored in ambitious sustainability transformation frameworks like the EU Green Deal and the EU Chemical Strategy for Sustainability (CSS).17 The Green Deal maps the transformation of the EU's economy for a sustainable future, aiming at zero pollution, climate neutrality, and a circular economy. Safe and sustainable-by-design (SSbD) principles are linked to this transformation and are to be applied at distinct levels: for chemicals and building blocks, for materials, for products and applications.18 In this process (Figure 3), by ambition, a safe and sustainable design emerges from an innovation process. CEFIC, the European Chemical Industry Association, has described SSbD as a “transformative power behind circular and climate neutral innovations”, and emphasizes the need for a workable framework even in initial stages of research.19
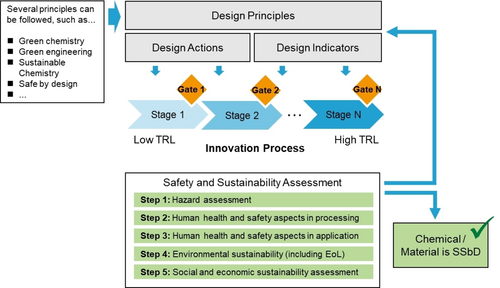
SSbD framework based on design principles that accompany an innovation process. In industry, this would typically follow different stages of development and “gate” decisions for continuation. The safety and sustainability assessment considers chemical safety, process safety, and environmental life cycle, as well as social and economic sustainability. Redrawn from Ref. 18.
The reason for using a chemical, or specifically a polymer, is due to its function and valuable properties in the application (Figure 1, Figure 2). Innovation along the chain for sustainable polymer design (Figure 4) starts (i) with a need for the specific performance in use, including cost/performance metrics and scalability, and at the same time (ii) must embrace safety, sustainability, and intrinsically a circular end-of-life (EoL). For polymer synthesis, a variety of monomers can be chosen from fossil or renewable feedstocks, including biomass and recycled feedstock or obtained from carbon capture and utilization (CCU). The choices of polymer composition and molecular structure constitute the realm of molecular design, leveraging the toolbox of polymer chemistry. With the resulting polymers, the application is enabled by system-level design to jointly fulfill the requirements of the use phase and circularity at EoL.
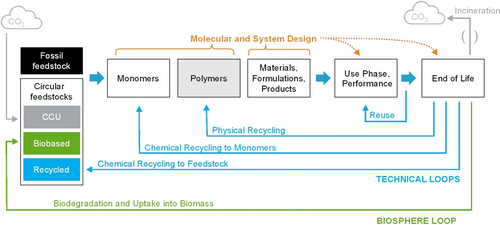
Value chain and life cycle of polymers. Design targets for performance, safety, cost efficiency, and scalability in use phase as well as for end of life (EoL) are indicated by dashed orange arrows. Circular loops can be established via the biosphere (green arrow), technical loops in reuse and recycling (light blue arrows), or in an “open loop” via carbon capture and utilization (CCU, gray arrows).
In the world of polymers, traditional chemical safety considerations rather apply to the monomers, which often are reactive and relatively small molecular species. Stable polymers have in the past generally been considered of lower concern, not being bioavailable due to their high molecular weights.20 This long-held generalization is being revisited in the evolution of regulative frameworks, like upcoming polymer REACH (Registration, Evaluation, Authorization and Restriction of Chemicals) in the EU21 or as introduced in Korea.22 To support these efforts with solid scientific data, methods and standards for the thorough characterization of polymers with their inherent polydispersity and heterogeneity are still a scientific challenge to be addressed in a joint effort by the community.23 In terms of the social dimension of sustainability, poorly managed EoL plastics, locally or exported e.g., towards the Global South, and disposal by uncontrolled burning and unsafe handling in informal settings24 highlight the detrimental impact of waste25 that needs to be mitigated.
With EoL emerging as a key lever for SSbD polymers, one fundamental circular option is a technical loop of reuse or recycling.26-29 The second is biodegradation which feeds back into biomass.30-33 An open atmospheric carbon loop via incineration and CCU can be seen as a last resort in a net-zero world.34 This will most likely be unavoidable for some legacy heavily mixed waste streams or, for example, for durable dispersed applications like protective coatings on metal structures: coatings will remain on the structures they protect and end up as a minor impurity in metal recycling at high temperatures, burning off as organic carbon. In general, however, polymer design must prioritize the smaller technical and biological loops.
Structural polymers, and in particular thermoplastics, can be collected, re-used, and recycled by a set of technologies.26 Efficient waste collection is the prerequisite to stop plastic pollution and littering.35 Separate take-back or collection schemes, and/or efficient sorting to sufficiently clean streams is needed to valorize the material in recycling.26 Inevitable aging and contamination, as well as the intrinsic challenges of intimately mixed or laminated multi-materials today still limit recycling. While the latter can be addressed by redesigning plastic-containing products on the systems level (Section 4), molecular design (Section 3) can help to open new chemical recycling routes for the polymers themselves.36 Alternatively, biodegradability is another option for structural polymers, and these options do not have to be mutually exclusive. Many biodegradable materials can in principle also fit into a technical recycling loop. A clear case for the preference of biodegradation in the case of structural polymers is when polymers are heavily contaminated with organic or natural materials during use, as happens in contact with food residues (food containers) or soil (agricultural mulch films). This use of certified compostable or soil-biodegradable polymers provides a clear sustainability benefit, closes the loop for organic waste, and diverts such streams from incineration or landfills,37 where methane emissions of organic wastes presently account for 2 % of global greenhouse gas emissions38 (exceeding global emissions of air travel39).
For functional polymers, recycling in a technical loop is not an option since these are part of liquid formulations and often dissipated during use. Water-soluble or water-dispersible polymers mostly end up in wastewater streams together with many other substances. The preferred EoL sustainability strategy for functional polymers is therefore the introduction of biodegradability through molecular design. Chemical modification of the structure of the macromolecules, which retains their performance before and during use at acceptable costs, plays a key role.32
3 Sustainable Molecular Design for Polymers
Structural and functional polymer design starts at the molecular level through the choice of polymer class, the monomers used, and considerations of the desired molecular weight, sequence, and architecture (Figure 5). For structural polymers, processing properties (in their melt stage or as reactive systems) and final bulk properties are at the focus.40 For functional polymers, the presence of functional groups, the behavior in solution (or as a liquid themselves), rheology, and interactions with other components in the system are the dominant factors.
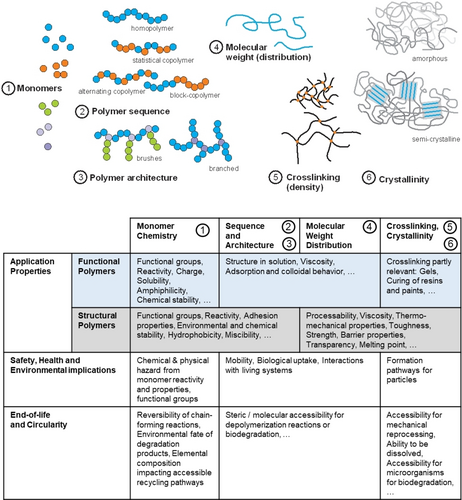
Hierarchy of molecular polymer design and exemplary resulting properties, as well as a selection of possible impacts on safety, environment, and circularity.
Durability has been a key performance criterion: Molecular structures need to withstand mechanical, hydrolytic, thermal, and oxidative stress for a structural polymer, or remain unchanged as functional polymer in dissolved state in a formulation. Uncontrolled degradation must be avoided, and is sometimes mitigated by the addition of additives, such as stabilizers or biocides. On the other hand, the introduction of cleavable bonds is a key requirement for chemical and biological recycling as well as for environmental biodegradation. For chemical recycling to monomers,36 controlled degradation is wanted at EoL (Figure 6) and conditions are set technically, which typically differ from natural environments (e.g. by elevated temperature, presence of reactants etc.). Similarly, biological recycling and environmental biodegradation leverage the metabolization of polymers by microbes with consequent complete conversion of the polymeric carbon into CO2 and biomass.31 For this to occur, polymers need to undergo either an abiotic (through e.g. moisture or UV irradiation) or, preferentially, a biotic degradation step resulting in biodegradable monomers or fragments. As a consequence, the breaking points need to be accessible for enzymes. Polyolefins, purely acrylic or most vinylic polymers containing a C−C backbone, lack these features (Figure 6) and—without molecular redesign—are excluded from the biological loop. Condensation polymers such as polyesters or polyamides, on the other hand, are based on the most common chemical linkages occurring in nature and offer potential cleavability. As we will discuss in the next section, the mere existence of bonds that are in principle cleavable is a necessary, but not sufficient condition: widely used polyesters such as PET and polyamides like PA6 and PA6.6 are durable structural polymers that do not undergo easy biodegradation.
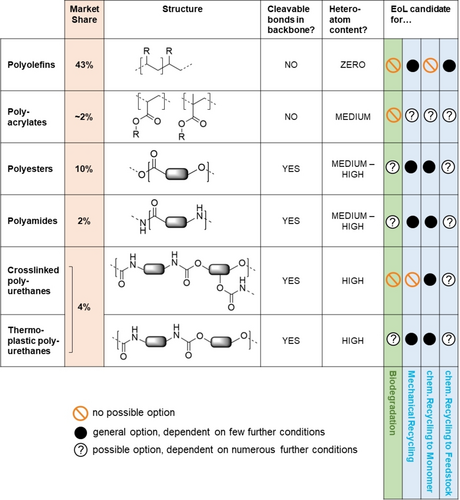
Accessible EoL options for a selection of economically relevant polymer classes. Current market shares41 are indicated; the polyolefin category includes polyethylene, polypropylene, and polystyrene. At this generic level, the final EoL path can often not yet be concluded. Complete biodegradation, for example, requires biodegradable building blocks and accessible cleavable bonds. Mechanical recycling, on the other hand, requires thermoplastic materials with sufficient stability to withstand processing. For chemical recycling to feedstock, the elemental composition of the polymers mostly describes their suitability, with a low content of heteroatoms preferred. No single recycling technology is suited for closing all loops, and complementary methods are needed.
While polyolefins constitute the major share of all polymers produced, molecular design within this class mostly has to rely on engineering of the molecular weight distributions for improved recycling (Section 3.4.1), complemented by the full spectrum of systems design options (Section 4). To elaborate the full potential of molecular design principles, giving tangible examples linked to the most important industrial applications, we will introduce in the following section a case study on polyesters and use the established framework for polyamides and polyurethanes. Based on the specific features for sustainable design, recyclability, and biodegradability, general molecular design strategies can be derived, which we will review subsequently.
3.1 Polyesters
Polyesters are well suited to highlight the connection between origin of raw materials, polymer structure, and EoL, which all have a direct impact on different sustainability dimensions of the life cycle. Structural polyesters can be divided into major categories based on the source of feedstock and their behavior in the biosphere (see Figure 7). (I) Durable and fossil polyesters: Many of the polyesters obtained on commercial production scale, such as polyethylene terephthalate (PET) and polybutylene terephthalate (PBT), belong to this category. These polymers are durable (i.e., non-biodegradable) and are derived from fossil feedstocks.42 (II) Durable and biobased polymers:43 These are chemically identical, 1 : 1 biobased replacements of the fossil counterparts, e.g., PET, PBT, polytrimethylol terephthalate (PTT), or modified variants, e.g., polyethylene furanoate (PEF), polybutylene furanoate (PBF). The major property of durability remains and is not influenced by the biobased content, since biodegradability depends on the polymer structure and not on the origin of the carbon. (III) Biodegradable and fossil polymers:30 These polymers e.g., polybutylene (adipic acid, terephthalic acid) co-polymer (PBAT), or polybutylene succinate (PBS) are biodegradable by design of their structure, and initial development in the 1990s relied on available fossil monomers.44 With increasing introduction of biobased monomers like bio-1,4-butanediol and biobased dicarboxylic acids to the market, a shift has begun to the category of (IV) biodegradable and biobased polymers.30 In addition to the biobased variants of PBAT-type polyester and PBS, polylactic acid (PLA) and polyhydroxyalkanoates (PHA) also belong to this category. These materials close the biosphere loop conceptually from biomass to biodegradation. Commercially, the use of biobased content (shift from category III to IV) depends on raw material costs and feedstock availability, which so far favor fossil origin. Change is therefore driven by sustainability commitments, consumer demand, and legislative requirements: in France, for example, 60 % biobased origin is targeted for biodegradable food and vegetable bags in 2025. Overall, the relevance of this category will increase significantly in the future. Biodegradability is the aligning property of materials for class III and IV and is determined by the material structure, abiotic factors connected to the environment (presence of water, oxygen, temperature etc.), and finally the biological factors (presence and types of microbes). Considerable progress has been made in recent years to understand this complex interaction.45-47
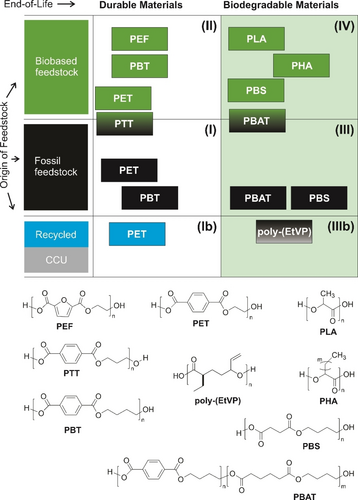
Framework for classification of structural polyesters by origin of feedstock and biodegradability at EoL.
On the raw-material side, carbon sources via the technical loop also become more important. At scale, (Ib) recycled durable polymers, mainly from mechanical recycling of PET so far (but, in future, also depolymerization26 and emerging technical enzymatic recycling48, 49) are examples with significant volumes. For recycled PET, quickly growing demand exceeds supply50 and will spur further scale-up. Future polyesters could also be based on building blocks from CO2,51 or use CO2 directly as a reactant in polyester synthesis, as exemplified recently (Scheme 1) by Rapagnani et al.52 Their product poly-(EtVP) was shown to be biodegradable in aerobic aqueous environment (OECD-301B standard) and would be a rare, and still academic, example for (IIIb) recycled biodegradable polyesters.
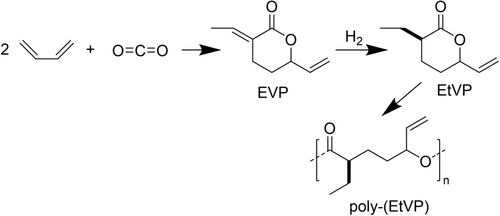
Butadiene can be reacted with CO2 to form 3-ethylidene-6-vinyltetrahydro-2H-pyran-2-one (EVP). After partial hydrogenation, 3-ethyl-6-vinyltetrahydro-2H-pyran-2-one (EtVP) can be polymerized via ROP yielding the polyester poly-(EtVP).52
In principle, all different combinations of feedstocks can and will play a future role in a circular economy that moves from incremental increases on a low percent level to system transformation and multiple cycle uses of carbon.5 Biobased carbon that enters a technical loop and is continuously recycled, for example, is a direct way of sequestering CO2 from the atmosphere for the lifetime of the polymers.
Despite the significant difference in properties of durable (categories I and II) and biodegradable polyesters (categories III and IV), polymer design, processing, and production technologies can be remarkably similar. Biodegradability is a property that results from a convolution of all factors in the polymer design hierarchy (Figure 5), from molecular structure to microstructure and crystallinity. Looking at the structural polyesters in Figure 7, there is not a single factor like the presence of a specific monomer that dictates environmental fate. In the set of examples, the presence of rigid, aromatic diacids like terephthalic acid seems to play a role—but can be mitigated as shown by PBAT.44 The durable polyester PBT was transformed into the certified compostable polyester PBAT53, 54 by “simply” introducing adipic acid as a co-monomer in the molecular structure. Additional commercially available dicarboxylic acids, such as succinic, azelaic, and sebacic acid, allow further tuning of material properties55 and show the broad potential of the toolbox of chemical design.
On the other hand, modifications favoring biodegradability also impact material properties. Introducing longer-chain flexible linear diacids increases chain mobility and accessibility for microorganisms, but also influences other properties42 e.g. mechanical strength (Young's modulus of 2–3 GPa for PBT, and 0.14 GPa for PBAT), and glass transition temperature (Tg of 55–65 °C for PBT vs. −31 °C for PBAT). The materials therefore are suitable for different applications and will require specific design at the systems level.
The transformation to biobased variants often relies on the same basis molecules (e.g., bio-1,4-butanediol) and therefore can go hand in hand for durable and biobased polyesters as well as biodegradable and biobased polyesters. This close relationship between durables (PBT) and biodegradables (PBAT) is also reflected at the level of production technology. The first generation of PBAT by BASF, for example, was produced in a slightly modified PBT plant.56 This consideration of the level of dependence between two polyesters in the categories of molecular design, properties, and production technologies resembles the application of the “phylogenetic tree” principle in biology.57 The key property of industrial compostability of different polyesters can be achieved by vastly different synthesis approaches ranging from polycondensation (PBS, PBAT) and ring-opening polymerization (PLA) to direct fermentation (PHA) (Figure 8).
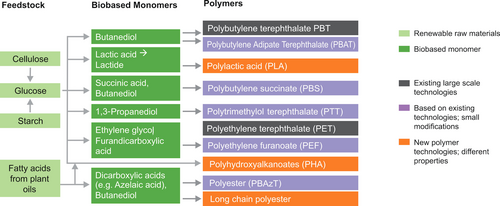
Design paths for structural polyesters, dependent on feedstock, (biobased) monomers, resulting polymers, and production technologies. In principle, a comprehensive safe and sustainable by design (SSbD) approach would require the individual comparison of all different pathways in a life cycle assessment, further multiplied by the numerous applications of the polymers in systems and products. This is not feasible, and SSbD for polymers must therefore be conducted in a modular fashion.
For functional polyesters, recycling is not an option, and the biosphere loop must be targeted instead. Esterases, such as lipases, are abundantly available in the environment and an integral part of activated sludge in wastewater treatment plants.58 Therefore, the use of functional polyesters or the introduction of ester groups in functional polymers may be an interesting strategy. For the application of “classical” polyesters as soluble polymers in aqueous environment, one challenge is their intrinsic hydrophobicity. Different building blocks and side-chain functionalities are therefore needed in this realm of application.
In one recent example, a metal-catalyzed bulk polymerization process starting from Boc-Asp-dimethylester and PEG-diol produced a functional polyester;59 removal of the Boc-protecting group then resulted in a water-soluble amine-functionalized polyester (Scheme 2). While the focus of this work was on the preparation of hydrogels for tissue engineering via subsequent cross-linking, the strategy creates options to make polyesters suitable for other applications.
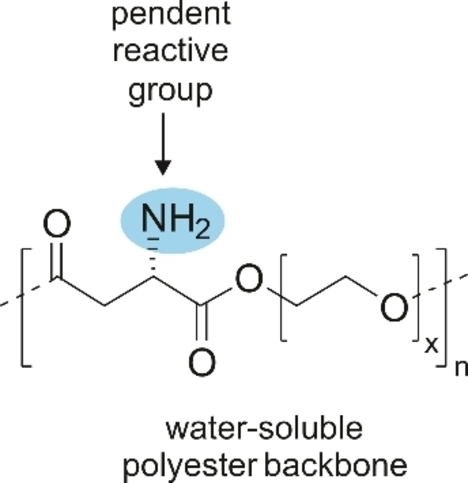
Structure of a water-soluble functionalized polyester.59
Functional polyesters are established as soil-release polymers for laundry detergent formulations.60 Copolymerization of terephthalic acid with poly(ethylene oxide) results in a water-dispersible polyester, which can be used in detergent formulations. The amphiphilic fossil polymer adheres to hydrophobic textile fibers, thereby making their surface more hydrophilic, which eases soil removal from the textiles.61 To the best of our knowledge, the biodegradation behavior of this polymer has not been disclosed in the literature. Depending on the length of the PET block,62 the polymer may have some potential to enter the biosphere loop due to the ester functionalities.
Unlike the introduction of amides, the introduction of ester groups in functional polymers has so far been limited. On the one hand, most polyesters have hydrophobic backbones and lack pendent groups that can be chemically functionalized. An example where this challenge seems to have been overcome is again in the field of soil-release polymers. Here, the use of sulfonated terephthalic acid as a comonomer, instead of unmodified terephthalic acid, resulted in an anionic water-soluble soil-release polyester.63 On the other hand, polyesters have a high susceptibility to enzymatic and non-enzymatic hydrolysis in aqueous systems, releasing low-molecular-weight compounds. While non-enzymatic (i.e. acid/base) hydrolysis could support biodegradation of the functional material after use, the polymer is not allowed to (significantly) hydrolyze before or during use. Thus, formulation concepts are required on the systems design level to ensure the necessary stability and performance.
3.2 Polyamides
Like polyesters, polyamides have a broad variety of structures, properties, and targeted applications.40 Based on the amide bond, they also represent an attractive toolbox for the development of sustainable polymers. Thanks to their high crystallinity and melting points deriving from the presence of strong hydrogen bonds, polyamides can exhibit superior stability and mechanical properties, as in the case of the most common representatives Nylon 6 (PA6) from caprolactam (as equivalent of ω-aminohexanoic acid) and Nylon 6,6 (PA6.6) from the corresponding α,ω-diamine and α,ω-diacid. These durable materials are produced at a scale of several millions of tons globally from fossil resources today (Category I in Figure 9), and are widely used as engineering plastics. Polyamides are already recycled today via the technical loop, i.e., via mechanical recycling or chemical recycling to monomers. Prerequisites for mechanical recycling are a relatively pure and uncontaminated waste stream. Often the use of additives, such as stabilizers and compatibilizers, or the addition of virgin polymer is necessary to achieve recyclability.64 This has been shown e.g. for multilayer films65 and injection molding compounds (Nypel®).66 For waste streams such as PA6-containing textiles and fishing nets, the Italian Aquafil Group has shown that hydrolytic depolymerization under acidic conditions67 is possible on an industrial scale to obtain the monomer caprolactam with virgin-like properties. No such industrial process exists for PA6.6 to date, as the addition of a small molecule (such as water) and the recovery of two monomers is more challenging than the caprolactam ring closure (see Section 3.4.2). Recycling processes for other polyamides in the technical loop are hindered by their low volumes and thus limited access to enriched waste streams of the respective polymers.
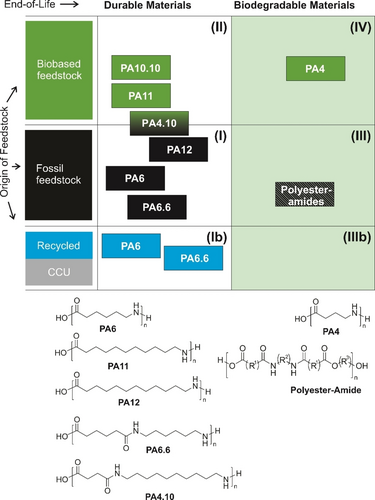
Classification of structural polyamides by origin of feedstock and biodegradability at EoL.
Biobased polyamides have recently been comprehensively reviewed by Winnacker and Rieger.68 Several commercial products with partial or fully biobased content are present on the market, for example PA4.10 introduced by DSM under the brand name EcoPaXX® from biobased C10-diacid and a fossil 1,4-butanediamine. So far, only few biogenic α,ω-diamines are available at scale.69 Earlier in 2022, Covestro announced a partnership with Genomatica to produce biobased 1,6-hexamethylenediamine in ton amounts,70 which if successfully scaled would also open a perspective for biobased PA6.6. By synthetic introduction of an amino group via halogenation, 11-aminoundecanoic acid can be obtained from biobased linoleic acid.68 The polyamide resulting from this polymerization has been introduced as Rilsan® PA11 by Arkema.
Due to their chemical similarity to proteins built from amino acids, polyamides in principle possess bonds that could undergo enzymatic cleavage leading to metabolization by microbes. However, similarly to polyesters, the choice of monomers and comonomers strongly influences their biodegradability, by directly modulating reactivity of the bonds, or by secondary effects such as imparting high crystallinity or relatively high hydrophobicity, which are key performance criteria of the established structural polyamides. Organic recycling or environmental biodegradation of polyamides71 is therefore usually not possible, despite some reports about metabolization of some polymers or oligomers by single microorganisms. The most promising material in this respect is PA4, for which partial biodegradation was reported to a certain extent in sludge, soil,72 and sea water,73 as well as its utilization by single microbes.74
Overcoming this limitation, biodegradation could be achieved by further tuning the molecular design of polyamides through the introduction of additional monomers forming polyester bonds, and hence leveraging their established biodegradability. During the 1990s this approach was followed by Bayer AG through the introduction of BAK® polyesteramides.75 The same monomers utilized for the synthesis of PA6 and PA6.6 are copolymerized with e.g. adipic acid and butanediol. The hybrid polymers were claimed to combine the mechanical properties of polyamides and biodegradability under composting conditions. The production of these materials, however, was stopped in early 2001.
What about functional polyamides? In nature, proteins, in addition to their structural functions, act as prime functional polymers. Intrinsically disordered proteins take on many functions in nature that synthetic functional polymers are capable of in their respective applications. Even highly charged polyelectrolytes are available in nature in the form of supercharged proteins and polypeptides.76 For proteins, perfect sequence control is possible in synthesis, and biotechnology might in the future allow rational production at a price conducive to non-therapeutic material applications. Synthetic homo- and copolymers of amino acids are biobased functional polyamides which have received significant attention for their use in several consumer applications, such as home and personal care.32 As one example, biodegradable poly(aspartic acid) (PASP) has been evaluated as a promising alternative to non-biodegradable acrylic acid based polymers in home care applications. Following its discovery in 1926 by Wessely and co-workers,77 polysarcosine (PSar) has regained attention recently as a potential alternative for poly(ethylene glycol) (PEG) in biomedicine.78 Both polymers are non-ionic and are characterized by their excellent water-solubility, low affinity to protein, non-immunogenicity, biocompatibility, and non-cytotoxicity. The challenge with both PEG and homo-PSar is that they are not biodegradable at higher molecular weights up to 50 kg mol−1. Although based on a naturally occurring amino acid (sarcosine), homo-PSar is reported not to be biodegradable, most likely due to the presence of the methylated amide bonds. Recently, Ling et al. described the random incorporation of alanine (Ala) into PSar via ring-opening polymerization of the respective amino acid N-carboxyanhydrides (NCAs)79 and demonstrated its degradability by porcine pancreatic elastase within 50 days under mild conditions (pH 8 at 37 °C). Both the enzymolysis rate and water solubility of the copolymer depend on the content of Ala. While this study focuses on inducing biodegradation in the human body, the concept may be extended. Besides Ala, one could think of introducing other amino acids via NCA ring-opening polymerization to tune polymer properties and biodegradability behavior for a targeted application as technical functional polymer. PSar-containing copolymers have been investigated as antifouling surfaces for medical devices, food packaging, and in industrial and marine equipment.80 To the best of our knowledge, no biodegradation studies have been published on these (co)polymers using OECD or ISO biodegradation methods, which would be necessary to assess their true potential as a circular, biodegradable functional polymer.
3.3 Polyurethanes
Polyurethanes (PU) are another general class of polymers that can serve both structural and functional applications. The urethane bond again is generally hydrolysable and potentially cleavable by enzymatic attack. A recent overview on polyurethanes from an industrial perspective has been given by Eling, Tomovic, and Schädler,81 while the use of biomass for PU has been reviewed and systematically organized by PhungHai et al.82 Owing to the modular building principle of PU from polyols and diisocyanates, the structural variety and versatility in applications is even broader than for the polymer classes discussed so far. Here, we only want to highlight some basic features that complement the earlier discussions in Sections 3.1 and 3.2, without aiming at being comprehensive.
Typical building blocks of polyurethanes today are, like for all polymers at scale, fossil based, and the resulting durable polymers are non-biodegradable. Typical PU products, like flexible or hard foams, and thermoplastic polyurethanes (TPU) are in the respective category I (Figure 10). Via the polyol component, PUs have a long history of incorporating biobased content: Multifunctional Hydroxy-decorated molecules, like sugars, are available directly as natural products. Common polyols are of the polyester-polyol type, leveraging the whole range of polyester chemistry discussed above in Section 3.1, together with the respective biobased diols and diacids. Similarly, polyether-polyols can be derived from biobased multifunctional alcohols. Using only bifunctional polyol and isocyanate, linear PUs are achieved, which as structural polymers yield thermoplastic polyurethanes (TPU) and are suitable for mechanical recycling. Using multifunctional building blocks, cross-linked systems including typical flexible and hard PU foams are created, which in the technical loop require chemical recycling approaches like glycolysis.26 Algenesis, a startup out of UC San Diego, has started commercializing algae-based polyols83 obtained by ozonolysis of unsaturated fatty acids from algae oils.84 Biodegradable PUs,85 for example, a foam system based on these algae-based polyols,86 have also been described, although biodegradation studies proving complete mineralization are still missing. Recycled polyols are available from PU chemical recycling, e.g., foam glycolysis,26 or via PET oligomers from recycling (e.g. TEROL® polyols from Huntsman87). As one of the first examples of carbon capture and utilization (CCU) in a commercial polymer, Covestro offers a CO2-based polyol (Cardyon®): CO2 is reacted with propyleneoxide to yield a polycarbonate-based polyol, which has demonstrated benefits in a life cycle analysis (LCA)88 and can be used in flexible foam applications.
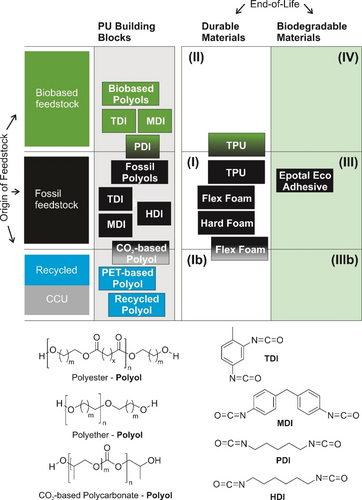
Classification of polyurethanes by origin of feedstock for the building blocks (polyols and isocyanates), as well as durable and biodegradable polymers assembled from them.
Isocyanates, on the other hand, can be derived from respective biobased diamines (see also the discussion on polyamides in Section 3.2). Commercial examples are linear pentane diisocyanates (PDI) marketed as STABiOTM PDITM by Mitsui Chemicals89 and Covestro's Desmodur N7300 PDI-trimer as a hardener for coatings,90 which is based on the phosgenation of pentane diamine derived from glucose.82 A wider variety of biobased diisocyanates has been demonstrated in a novel approach by the Burkart group, using flow-chemistry and Curtius rearrangement from renewable carboxylic acids to introduce the isocyanate functionality.91 For the two mainstay isocyanates TDI and MDI, on the other hand, variants have been introduced by Covestro92 and BASF93 based on renewable raw materials from biomass, by a mass balance attribution (see Section 5.4). In the PU building block approach, combining biobased polyols and isocyanates paves the way to introduce biobased content in the final PU polymers.94 One example is BASF's Elastollan® TPU which is available with biobased content.95
PUs, due to their enormous structural variability, are also used as functional polymers: in adhesives,96, 97 in coatings and paints,98 and in aqueous systems for hair styling.99 Similarly, PU dispersions are employed as adhesives. Epotal® Eco by BASF additionally serves as an example of a PU application offering biodegradation and is used as a laminating adhesive for multilayer packaging100 for fully compostable systems.
The multitude of different options based on PU molecular design again demonstrates the need for clear guidance on design that goes beyond chemical and polymer research. With these options, sustainable and circular design must be performed on the product level. Given the high reactivity of isocyanates, life cycle based SSbD (Figure 3) will factor in the potential hazard of these substances during production and processing, while considering the non-exposure of users to these intermediates in applications, and the benefits and safety of the final material. Additional paths towards polyurethanes are being explored that do not rely on isocyanate chemistry: Non-isocyanate PUs (NIPUs) have been reviewed.101 Chemical recycling via cleavage of ester polyols, as demonstrated by Magnin et al. using enzymes on polycaprolactone segments, would be another path towards reconstituted PUs in their subsequent life, reassembling the oligomeric products of the ester cleavage by polycondensation.102
3.4 General Molecular Design Strategies for Circularity
The distinct structural features of the polymer classes discussed above are important for the circular potential of the respective polymers. As can be seen, the versatile behavior of ester bonds is already being leveraged, e.g., for polyesteramides and in the case of polyurethane building blocks. Generalizing these features that go beyond a single polymer class, molecular design strategies (Figure 11) can be derived and have been explored to improve the circular potential of materials, in the case of structural polymers, depending on their thermoplastic or thermoset nature. These strategies include (1) reducing material complexity on the systems level by interventions on the molecular level, (2) deliberately facilitating recycling via re-monomerization (breakdown into the corresponding monomeric building blocks), (3) transitioning a thermoset into a thermoplast, while still addressing the same applications, and (4) building on existing natural biogenic polymers by modification.
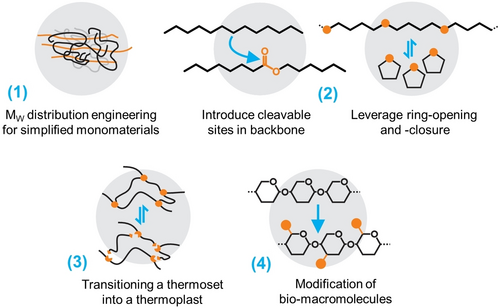
Molecular design strategies to enable polymers in a circular economy. (1) Engineered Mw-distributions allow designing out foreign reinforcement materials and facilitate recycling, while (2) the introduction of cleavable bonds opens paths for biodegradation and depolymerization—especially if leveraging ring-forming monomers. (3) Thermosets can be recycled like thermoplasts if crosslinks are switchable. (4) Modification of existing, circular biomolecules is another feasible strategy.
Strategies (2) and (3), remarkably similar to biodegradability, have in common the fact that a functional group in the polymer structure is required which is susceptible to an external stimulus (such as temperature and/or the addition of a solvent and a catalyst) and initiates the recycling process. As a last step, a chemical or physical workup process is required to isolate the monomer or polymer in such a way that it can be used again as starting material. The following section highlights some of the latest achievements and discusses challenges and opportunities of all four strategies.
3.4.1 Molecular Engineering of Molar Weight Distributions to Reduce Systems Complexity
In general, thermoplastic polyolefins are suited for mechanical recycling if they are sufficiently stabilized against oxidation and chain scission, have not suffered too much degenerative damage during their application life, and are not mixed with foreign polymeric components or contaminants.26, 29, 103 A smart molecular design approach to allow for omission of such foreign components was recently discussed by Mülhaupt et al.104 On a molecular level, multimodal molecular weight distributions of polyolefins are achieved by using novel catalyst systems during polymerization, resulting in all-polyolefin blends of ultrahigh molecular weight and highly crystalline reinforcement “domains” within a matrix of lower Mw that ensures processability. This molecular design approach has the potential to leave out fillers and reinforcement fibers on the subsequent level of polymer system design, thus improving the recyclability of these systems in the technical loop.
3.4.2 Enabling Circularity via Re-monomerization and Other Strategies for Backbone Cleavage
Polycondensation polymers such as polyesters, polyamides, and polyurethanes have an intrinsic ability to depolymerize to monomers or oligomers, as the condensation reaction is reversible and depends on a thermodynamic equilibrium. The depolymerization occursby e.g., reaction with solvent such as water, alcohols, or amines present in excess (solvolysis). The back reaction to monomers is favored at high temperatures above the ceiling temperature due to the entropy increase.36, 105 The use of catalysts106-108 and/or special solvents such as ionic liquids can increase reaction rates at lower temperatures.109, 110 While the process of re-monomerization has been extensively researched, especially for poly(ethylene terephthalate) (PET),26, 103, 106, 111, 112 purification of the obtained monomers is often a challenge and complicates the process for mixed waste streams.
For polyaddition polymers, such as the most widely used polyolefins as well as polystyrene and polyvinyl chloride (PVC), finding such a predefined pathway to monomers is more complicated, as in contrast to polycondensation polymers, C−C bond cleavage must take place. Due to their high ceiling temperature (e.g., 400 °C for ethylene105) depolymerization only starts at much higher temperatures than for the polycondensation polymers, often yielding an undefined mixture of small molecules (pyrolysis oil) or, in the case of PVC, producing hydrogen chloride instead of the monomers. Even though the ceiling temperature can be influenced for example by adding solvent,113 the re-monomerization process is often energetically very costly for pure hydrocarbon backbones. Alternative chemical strategies seek to convert such waste into other useful chemicals by C−H functionalization,114-116 but are likely limited to smaller fractions of the waste. Therefore, important research in the last years has focused on designing new polymers for which chemical recycling to defined monomers is possible. Coates and Getzler highlight in their review the possibilities of ring-opening polymerization (ROP).36 ROP allows a near-ergoneutral polymerization reaction, which means the change in Gibbs free energy is small during polymerization and can therefore easily be reversed by ring-closing depolymerization (RCD). An example for such a near-ergoneutral system is given in Figure 12A for γ-butyrolactone. ROP has mainly been proposed for heterocycles,117, 118 where the main advantage over polycondensation polymers is the absence of a small molecule that needs to be added/removed from the process and thereby complicates the reaction. Many examples for three- to eight-membered ring monomers that can be used for closed-loop recyclable polymers are given in the review by Xu and Wang.118 In addition, cyclopentenes might present a possibility for alicyclic monomers to form an all-carbon backbone.119, 120
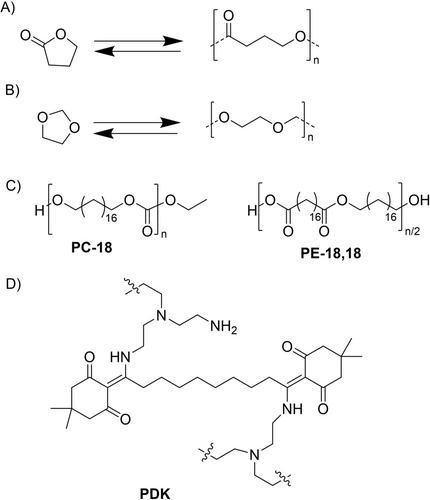
Chemical structures of selected polymers that can be easily depolymerized into their monomers: A) synthesis of poly(γ-butyrolactone), B) synthesis of poly(1,3-dioxolane), C) molecular structures of polycarbonate-18 (PC-18) and polyester-18,18 (PE-18,18), D) polydiketoenamine.
A more detailed approach on how to replace polyolefins with a polymer that can be easily re-monomerized is given by Abel et al.121 They synthesize a polyacetal with comparable properties to polyolefins (regarding tensile strength and thermal stability) which could be used for packaging products. Synthesis relies on cationic ring-opening polymerization; re-monomerization of this polymer is possible using an acid catalyst at 140–150 °C and subsequent recovery of the pure 1,3-dioxolane monomers by distillation with a high yield (Figure 12B). Moreover, they tested their approach with a mixed and contaminated waste stream obtaining a remarkably high yield of 96 % of monomers without prior separation of the mixed waste.
Häußler et al. take a different approach to replacing polyolefins by introducing defined functional breaking points into the polymer chain.122 These breaking points, which are either polyester or polycarbonate functionalities, are introduced every 18 C atoms, thereby creating molecules with properties like polyethylene (Figure 12C). Recycling back to the monomer can be done by solvolysis at 120 °C in ethanol with a KOH catalyst. They obtain the monomers in high yields and purify them by recrystallization. A similar approach is the catalyst-mediated introduction of 1 % carbon monooxide (CO) into the polyethylene chain through the formation of keto bonds that promote degradation under UV exposure but do not affect the mechanical properties of PE.123, 124
The introduction of functional groups in polyolefins while retaining their application performance might also open up a pathway towards biodegradation. In aqueous environments and towards biochemical transformations or enzymatic attack, the alkyl backbone itself is not easily accessible. Initial degradation of pristine polyethylene in the guts of wax worms, however, has been described.125 While plastic uptake by the worms seems to be confirmed, digestion126 and potential usefulness of the effect127 are still subjects of debate. Utilization of polyethylene by microbes has also been reported,128 but limited characterization of the investigated material, low biodegradation rates, and experimental conditions far from current biowaste processing technologies or environmental conditions, make these findings academically interesting, but in our view, unlikely to change the general picture. In many instances, partial biodegradation requires prior abiotic (via oxygen radicals or photochemical) backbone oxidation.128 Impurities or deliberately added oxo-degradation catalysts can support these initial steps, but this dependence on prior oxidation limits the generality and leads to the danger of only partial biodegradation and subsequent microplastics formation in the environment. Consequently, oxo-degradable plastics have been banned in the EU.129
On the other hand, chain-growth polymers with C−C - backbones, like polyacrylates in the case of many functional polymers, can be equipped with cleavable sites, e.g., ester bonds, in the backbone even via radical polymerization; radical ring-opening polymerization has been reviewed by Tardy et al. for that purpose,130 including copolymerization131 of vinylic monomers with cyclic ketene acetals (Scheme 3).130
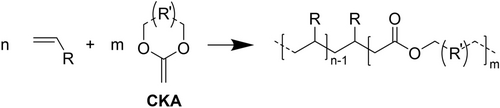
Introduction of ester bonds in the backbone of chain-growth polymers in radical polymerization by use of cyclic ketene acetals (CKA) as co-monomer.
All these publications present an impressive way of designing new polymers with a focus on both performance and recyclability or biodegradability. However, they do not consider a full life cycle analysis of the entire re-monomerization and re-polymerization process and neglect manufacturing costs, raw material costs, and the carbon footprint for the synthesis of the virgin material. These will be higher compared to the presently used polyolefins or other vinylic chain-growth polymers. However, in the case of monomer recovery, with each recycling cycle, the virgin material costs will play a diminished role. For the recycling process, costs and carbon footprint will be dominated by energy costs due to the reaction at higher temperature and the solvent recycling necessary. Additionally, a crucial factor to consider is the requirement to separately collect or identify and sort the specific polymers that were designed for the recycling process.
These considerations are also the focus of a publication by Vora et al.132 who focus on the chemistry of polydiketoenamines (PDKs, Figure 12D). Re-monomerization of the PDKs is achieved in sulfuric acid followed by ion exchange to recover the amine and by extraction to recover the triketone. The subsequent re-polymerization can be done without solvent at room temperature. Here, the production costs of the virgin material were estimated to be 30-fold higher (45 $/kg) than the recycled material, which is in the price range of commodity polymers such as HDPE (1.5 $/kg). Also, the carbon footprint for the virgin material is about 40 times higher than for the recycled material. A high collection rate and thus many recycling loops are therefore a decisive factor for such a circular solution. New business models including return of the materials and involving the whole supply chain will be necessary to implement such materials designed for circularity. The hurdles are specifically high for new polymers, starting out at low volumes, higher prices, and competition with the most abundantly produced polyolefins. Emerging markets in lower income regions globally will struggle even more to bear higher initial cost. Importantly, established bulk polymers such as PE and PP, as mentioned, will also improve along the value chain for more efficient mechanical recycling or conversion to hydrocarbon feedstock by pyrolysis. In any case, circularity will increase the value of EoL plastics, hopefully effectively reducing incentives for unsustainable waste exports and likewise encouraging quantitative collection everywhere on the globe.
3.4.3 Transitioning a Thermoset into a Thermoplast
Designing recyclability by introducing defined breaking points is not only a potential strategy for the inert backbones of polyolefins, as shown in the preceding section, but also decisive for the recyclability of cross-linked polymers (thermosets). Thermosets account for 10–15 % of total plastics production and are characterized by their high chemical, thermal, and mechanical resistance which is caused by the cross-linking between polymer chains.133, 134 Since these materials cannot be physically recycled as they are not re-processable by application of heat, design for recycling and/or processes for cleavage are necessary for achieving a circular economy. A viable strategy is to introduce dynamic or degradable cross-links that can be deconstructed by an external stimulus such as heat135 or light.136, 137 Depending on the amount and position of the labile linkages, degradation products such as monomers, oligomers, or linear (thermoplastic) polymers are achieved and can be separated from additives, fillers, and reinforcements (such as fibers in structural applications) and be re-processed.133 With respect to degradable cross-links, a common strategy is to introduce more thermally sensitive cleavable bonds such as esters138, 139 or bonds that can be easily cleaved in an acidic or basic environment such as acetals140, 141 or ketals (Figure 13A). A drawback of these degradable cross-links is that the matrix resin is often degraded into undefined fragments and the focus is usually on the recovery of structural fibers (glass or carbon), making closed-loop recycling challenging.133 In contrast, labile bonds such as dynamic covalent networks can create re-processable thermosets. An important class are the vitrimers142 which show thermoplastic behavior at higher temperatures and behave as thermosets at lower temperatures. These were pioneered by Leibler et al. by introducing ester functionalities into epoxides which allow for exchange reactions at elevated temperatures making a rearrangement of the network structure possible143 (Figure 13C). This strategy is also viable for polyurethanes where both transesterification and transamidation reactions,144 or the introduction of disulfide bonds,145 can be used to make the networks mechanically reprocessable. Another reversible exchange mechanism that can be used is the Diels–Alder reaction, the [4+2] cycloaddition of a diene and a dienophile146 (Figure 13B). The adduct is thermally unstable and makes the thermoset recyclable at higher temperatures. An additional advantage of both vitrimers and Diels–Alder systems is their intrinsic self-healing ability, thus retaining mechanical properties after material damage,147 and contributing to possibly extended lifetimes of products. A commercially available example of a recyclable thermoset is the material for a wind turbine blade generated by the cross-linking of the respective epoxy system with so-called Recyclamines® by Aditya Birla Advanced Materials. These are amine-based curing agents that enable cleavage of the thermoset at defined cross-linking points upon application of moderate heat and acid,148, 149 generating recyclable thermoplastic compounds. Using this technology, Siemens Gamesa have announced the production of the world's first recyclable wind turbine blade.150 Alternatively, Arkema designed a methyl(meth)acrylate-based system which is radically polymerized into a thermoplastic resin called Elium®. Blades manufactured with this technology can also be fully recyclable through depolymerization of the thermoplast.151-153
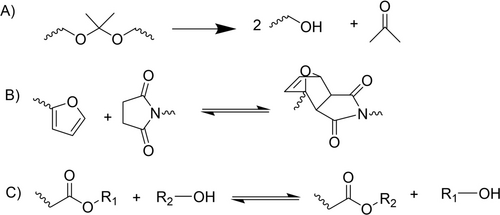
Designing recyclability for thermosets: A) by introducing acetal groups that can be cleaved by heat and acidic conditions. B) Dissociative linkage using a Diels–Alder reaction. C) Associative linkage using heat and/or catalyst for transesterification reaction. Redrawn from generic reaction schemes in Ref. 133.
3.4.4 Modification of Biological Polymers
Biological polymers provide an attractive starting point for the design of biodegradable polymers because they are generally non-toxic and metabolized in the biosphere.154 Since a native biological polymer alone typically does not display the overall desired performance in the targeted application, chemical modification is necessary. The preparation of hybrid polymers which consist of a biological and a synthetic polymer may combine the best properties of both polymer classes. Polysaccharide-based polymers, such as chitosan, cellulose, and starch, are among the most frequently used polymers for this strategy in recent literature. Examples of using chemically modified water-soluble or water-dispersible biological functional polymers in water treatment and crop protection have recently been reviewed.32
4 System Design: Increase Availability for Recycling or Enable Closing Loops in Applications
The examples above show how the capabilities of the polymer can directly impact the circularity of the system and product they are employed in. There is, however, a reverse relationship, too; the design of the system (Figure 14) must be such that it allows the polymer to shine. For many recycling technologies, heterogeneity of waste streams is a big hurdle that prohibits certain pathways or severely limits the achievable result. The circular polymer might simply get lost in a large amount of noncircular waste. Similarly, a fully biodegradable functional polymer in a liquid formulation would only provide a partial solution if the other components of that product are persistent. Polymers which are circular by design only truly contribute to a circular economy if their intrinsic benefits are not counteracted.
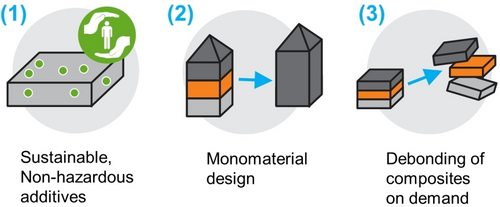
System design strategies to improve recyclability of polymers for a circular economy.
In one instance, this could be the formulation of polymers in systems together with additives. These have vital functions to stabilize the polymer, protect it from degradation, and thereby prevent small-molecule degradation products from forming, which could potentially be more hazardous than the inert polymer. The polymer damage during recycling is often accelerated by accumulated degradation damage from the use phase. A residual safe level of stabilizers at the time of recycling might be essential for circularity, and comprehensive SSbD in that sense might shift the loading levels from purely cost/performance optimization to include high-quality recyclability at EoL. Other substances, on the other hand, might be hazardous, leachable, or negatively interfere with reuse and recycling. One example for this case are legacy halogenated flame retardants, like HBCD, in polystyrene insulation panels, which had been added in the past to improve the safety profile (fire resistance) during use, but of which the hazard potential at end of life had only been recognized fully later.155 Owing to the presence of hazardous legacy additives, such materials are now excluded from many recycling options, although modern processes aim to remove the contaminant.156 SSbD, in this case on the systems level, must consider the whole perspective and prevent further such cases, while at the same time unlocking innovation for sustainable applications, e.g. in the case of additives, with non-halogenated flame retardants.157
On the one hand, advanced plastics detection and sorting techniques, e.g., by NIR sensors, hyperspectral imaging, or digital watermarking,158 can significantly improve the purity and quality of waste polymers obtained from post-consumer waste.159, 160 Mechanical or chemical recycling can subsequently be applied to the individual polymers. Products made from a single polymer in a monomaterial approach, without compromising performance,26 greatly enhance recyclability on the systems level. On the other hand, if composites are used, separation into the individual materials is often impossible. A typical example is multilayer film laminates widely used in food packaging.93 To preserve the quality of the food, the packaging needs to protect against e.g., oxygen and water vapor, provide resistance against grease, fat, and water, and must provide, in certain cases, rigid stability for handling and transportation. In many cases, these properties are not achieved economically by one single polymeric material, but by the combination of multiple different materials. Typical examples are combinations of PE with PET or PE with polyamide, laminated together with an adhesive. Additionally, labels are often glued on top of the packaging (Figure 15A). Separation after the use phase into the individual polymer materials in a waste-sorting facility is not possible here.
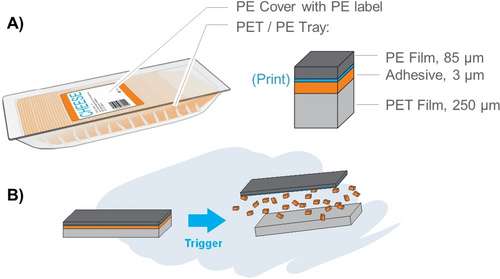
A) Typical multilayer packaging for cheese. B) Debonding of laminated plastic layers into individual materials by an external trigger.
One option to mechanically recycle such multilayer packaging is to introduce adhesives that debond by an external trigger.161 Debonding on demand (DoD) thus separates laminated layers into individual materials (Figure 15B).
Common triggers for debonding are magnetic, electrical, UV radiation, chemical, thermal and ultrasound. Adhesives themselves consist of functional polymers that can be modified to allow triggered loss of adhesiveness.162 While DoD has been studied in academia and industry for decades, commercial applications remain limited. Typical drawbacks of current DoD technologies are that they do not fit with current industrial processing conditions, whether due to the limited availability of triggers in typical waste-sorting and recycling plants, the slow debonding speed, the poorer adhesive properties when modified for DoD, or simply because of increased costs. More research is required to bring this technology to commercial success. DoD can enable the design of products for recycling, while the implementation requires players along the value chain to collaborate. To demonstrate this specifically for PET trays, a partnership was launched between the packaging converter company Evertis who produces the multilayer films, BASF as provider of a waterborne laminating adhesive which facilitates separation, the machine manufacturer Bobst enabling the coating of the adhesive, and the company Sulayr using their technology to separate the layers at EoL and reclaim them for recycling.163
This example shows how molecular and systems design for the technical circle are dependent on the infrastructure available. For improving recycling quickly and increasing plastics circularity via the technical loop, a simplification of the waste stream and standardization is highly beneficial. This creates hurdles for certain types of innovation. Completely new types of polymers not recognized by existing sorting approaches would require new infrastructure and in the worst case even negatively impact existing recycling as contaminants. There is, however, an opportunity for smart solutions that can be made to fit into existing systems, or that are delivering such clear benefits that they catalyze a corresponding upgrade of capabilities. For the biological loop, such limitations might be less pronounced: Biodegradation could be seen as a function of the biological environment alone, and any new polymer that can be proven to be fully biodegradable in it, might “fit”. This, on the other hand, requires established methods for assessment, standards, and legislative boundary conditions that define biodegradability.
5 Prerequisites and Tools for the Safe, Sustainable, and Circular Design of Polymers
5.1 Standards and Legislation for Biodegradable Polymers
As previously mentioned in Section 2, polymers have so far been exempted from parts of chemical regulation due to their stability and high molecular weight. While in some applications biodegradable polymers are seen as a solution to replace persistent materials, regulations are still struggling in creating a consistent framework for the testing of these materials. During (bio-)degradation, the polymer is cleaved into smaller fragments and ideally metabolized into biomass, CO2, and H2O. The possible formation of intermediate (bio-)degradation products needs scrutiny,164 but the development and standardization of specific testing schemes has helped address this issue.
An example shows the importance of standardized methods linked to a recognized legislative framework: in Italy the mandatory compostability for shopping and fruit and vegetable bags was introduced.165 The development of a framework to test and certify bags suitable for biowaste recollection based on EN 13432 has created the premises for legislation for the mandatory introduction of compostable bags and the ban of PE bags. These measures helped reduce the probability that non-biodegradable bags will enter the composting stream, resulting in compost with substantially reduced plastics contamination and increased biowaste collection rates. Similar legislative measures are currently being followed by other countries.
5.2 Testing Methods for Biodegradability
Reliable testing therefore is key for acceptance, as well as defining design targets for scientists. Assessing polymer biodegradability is linked to several challenges. Polymers need to undergo initial cleavage to become bioavailable for metabolization, which is often linked to longer biodegradation times. This applies to dispersed functional polymers, but it is even more challenging for structural polymers in bulk. For these, the surface-to-volume ratio will influence the kinetics of biodegradation.166 For this reason, plastic materials are typically assessed in a two-step process, including biodegradation of the matrix material on a micrometric scale, and disintegration of the final microscopic items. A second relevant aspect is linked to the chemical and structural diversity: polymer molecules can be chemically remarkably diverse and inhomogeneous in their properties, due to their polydispersity. Low-molecular-weight fractions are readily assimilated by microbes, and easily accessible partial domains of the polymer could wrongly lead to the classification of a whole material as biodegradable, if full biodegradation is not proven. Therefore, the use of biodegradation half-lives (Dt50) and the extrapolation of biodegradability from reduced testing times should be avoided.
In terms of standard methods to assess biodegradability of polymers, tests must rely on respirometric endpoints, such as tracking O2 consumption and CO2 evolution. Existing respirometric methods can be roughly divided into two classes: OECD testing guidelines, developed for the testing of small molecules, and standard methods developed for biodegradable plastics, such as ISO, CEN, and ASTM methods. Both categories have been acknowledged as suitable to assess the biodegradability of microplastic materials, and could work as well for other polymers, but validation and optimization is required. Existing methods to assess biodegradability of polymers have been recently reviewed by Albright167 and within the ECETOC working group,168 highlighting the need for systematic validation for different classes of polymers, and the lack of an overall framework to assess and regulate persistent and biodegradable polymers. Considering the urgent need for biodegradable alternatives to current existing materials, methods leading to shorter biodegradation testing times are needed. Studies investigating enzymatic cleavage of polymeric materials have been reported in the literature169, 170 and provide an excellent complement to respirometric methods. The use of enzymes allows rapid cleavage of the polymeric structure and bypasses the rate-limiting step in the biodegradation of polymers. Complete cleavage and identification of the oligomers requires thorough analysis by IR, Raman, NMR, GC-MS, LC-MS, or other methods. Challenges are the availability of a library of enzymes covering the most relevant reactions in nature, the different environmental compartments, and complex determination of the fragments formed. A universal, substrate-independent method is still missing.
For a polymer to be biodegradable, all its components, oligomers, fragments, and metabolites will have to be converted into biodegradation products. Methods to assess the biodegradability of these fragments can be based, beyond the testing of the final polymer, on a detailed analysis of the polymer building blocks and the breaking points introduced into the material. Identified oligomers could be either isolated after enzymatic or abiotic cleavage or synthesized in a targeted manner for further investigations. This approach should be favored over the use of labelling techniques on the polymers themselves, due to the high costs and the challenges in synthesizing polymers with the same properties as products on the market. Alternative, attractive methods enabling the identification of metabolites are microbial enrichments.46 Microbes from environmental samples can be repeatedly exposed to the polymeric substrate as the only carbon substrate, to enrich exclusively the microbes involved in the biodegradation process, allowing testing with increased concentrations of polymer. This method has been proven to identify the different steps in the biodegradation process and has also provided deep insights into the metabolic pathways.
5.3 Modelling the Sustainable Molecular Design of Biodegradable Polymers
As seen above, biodegradation is a function of all hierarchical levels of polymer design, while testing for biodegradation is burdensome and requires time, making iterative development loops tedious. One of the most attractive emerging tools for the optimisation of the molecular design of polymers towards biodegradability in a certain environment, is molecular modelling. If the end-of-life behaviour of a structure can be accurately predicted before or during its development, this information can be used to guide design towards a more sustainable outcome. It of course also reduces the associated materials, energy, and investment required for such a development.
QSAR (Quantitative Structure–Activity Relationships) models are predictive models which analyse correlations between the properties of a chemical structure and its biological activity.171 These models have been discussed for use by REACH as an alternative method172 of creating data where none is available. Here, QSARs are recommended for prediction of physicochemical properties and for some environmental toxicity and fate properties, such as biodegradability; they are, however, not recommended for prediction of more complex systems.
For biodegradation, several QSAR models have already been developed which can predict the biodegradation of a molecular structure in a specific environment or dataset.173, 174 A number of these are even either freely available, or available through licencing to customers;175, 176 most recent developments include OASIS Catalogic177 and EPI Suite BIOWIN (4, 5 & 6).178 Some of the more recent tools, such as EnviPath, even use modelling of known degradation pathways to map chemical breakdown pathways. Most of these tools use open-source data from three frequently cited sources, although other databases have been described in the literature.179 Since the implementation of the REACH Regulation in 2007, a large amount of biodegradation data is now available online through ECHA registration dossiers and is generally thought to be a very reliable dataset. Additionally, two databases are also freely available: the NITE database (based on MITI-I OECD 301C Tests, Chemical Inspection & Regulation Service, Japan) and BIODEG database (Syracuse Research Cooperation, USA).180 However, prediction models for larger, more complex molecules—especially polymers—are unfortunately lacking, mainly due to the absence of large datasets and the complexity of calculations required for polymer modelling.
Although fewer in number, some additional investigations have been published on modelling the more complex relationships of polymer degradation.181-184 Most recently, in 2020 Min et al. investigated the environmental degradation trends of 110 polymers to create a predictive model.185 The degradation modelled was surface erosion, and so could not be described as true biodegradation in the sense of circularity. In most cases, literature describing biodegradability prediction of large molecules does not use microbial biodegradability as its output, but structural descriptions of degradation such as weight loss,186 or “biodegradation” describing enzymatic or hydrolytic degradation in vivo.187 This still is a clear deficit, and future research should consistently measure biodegradation in terms of e.g., CO2 evolution.
With the ongoing digitalization of chemical research,188 including materials characterization and biodegradation testing, one can expect the body of useful data to drastically increase, allowing further data-driven approaches, as has been demonstrated in other fields for accelerated discovery in multiobjective target settings.189
5.4 Life Cycle Analyses and Mass Balancing
When designing sustainable polymers on a molecular or systems level, the result, i.e., how sustainable a certain design is in specific aspects, and finally all aspects of the life cycle need to be considered in a comprehensive life cycle analysis (LCA), in comparison to alternative designs. Life cycle CO2 reduction by use of biomass, for example, needs to be considered jointly with other dimensions such as land or water use within the planetary boundaries.11 Relevant examples e.g., for the introduction of biobased building blocks for polymers,190 chemical recycling to feedstock,191 and recycling approaches for mixed waste streams,192 have been published. While complete LCAs are too complex and time-consuming to perform for every design consideration in early-stage research, the level of detail and quality of assessment must increase as a technology matures in the innovation chain. Furthermore, typical LCAs still have limitations applied to circular economy cases, such as representing the non-intended end of life (littering) as a CO2 sink, which might lead to debatable conclusions. As a mitigation measure, microplastic formation as additional impact category has been suggested.193
Another practical hurdle for the introduction of circular feedstock from biomass or recycling is the need for the corresponding production assets. The production plants needed might in many instances be identical to those in the established fossil value chain. Therefore, for a circular transformation to occur, the use of assets with mixed feedstock is unavoidable. Here, industry uses an allocation principle.194 Recycled or renewable feedstock or raw material entering a chemical value chain at the beginning is allocated to downstream products, which are then marketed with a given renewable or recycled (circular) allocation, without direct physical traceability. The correct stoichiometric mass of circular feedstock at the beginning of the value chain (e.g., oil from plastics pyrolysis) must be in balance with the amount of claimed circular content in the downstream products (e.g., a polyamide grade). A prerequisite for allocation is a system boundary in which a physical connection exists between the production plants (Figure 16), enabling a physical flow that establishes a link between the feedstock and the product. For a transparent communication on mass balance, physical connectivity should be given.
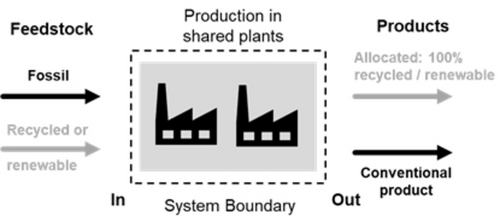
Recycled or renewable feedstock is, in addition to fossil feedstock, fed into a chemical production site. After dilution of the circular feedstock in the production site across several plants, the output will result in both conventional products and in allocated renewable or recycled products.
Audits are performed to certify that the correct mass of products with circular content is claimed. Also here, the creation of standards is vital to create acceptance and trust for customers and consumers.
5.5 Digital Representation
Creating a physical, circular material world will require not only the right polymers and processes, but also a well-established digital infrastructure to successfully close the loops. Raw materials are turned to polymers, which are processed to (semi) finished goods and eventually built into a consumer product. Transparency is required along this value chain, e.g., to track and trace the recycled or renewable content in materials and products, as well as LCA or CO2 emissions data. Digital product passports are required by the EU Green Deal, which contain sustainability-relevant data.195 Catena-X,196 for example, is a consortium led by the automotive industry to create a transparent digital value chain. At end of life, digital product passports can help to better sort and recycle certain polymers, if it is known which additives and polymers are contained in the materials. The complexity is high for a digital infrastructure for tracking sustainability data along complex value chains and more work will be required before the first commercial applications go live.
6 Summary and Outlook
The broad variety of structural and functional polymers we use in our daily life is a result of development processes over decades. Starting with the pioneering work in polymer chemistry in the last century and the following development of large-scale production and broad applications, the focus has been on cost, performance, and safety in the use phase. Today, the imperative for polymer design must be the achievement of sustainability along the whole life cycle, including end of life, as a design target, realizing a circular economy and carbon neutrality. We feel that this effort poses a similar level of opportunities for the field as the first century of polymer science, requiring a renewed spirit of pioneering step change innovation. By applying the deliberate design approaches reviewed above, polymer science can reconcile the many beneficial uses of polymers with comprehensive life-cycle sustainability and circularity (Figure 17).
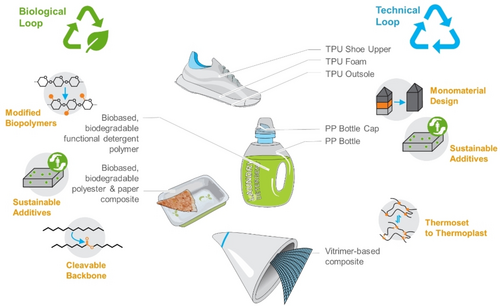
Selected examples on a product level for sustainable polymer design for a circular economy. Functional polymers that are dispersed during use, such as in laundry formulations, will be biobased and biodegradable, fulfilling a biological loop. Similarly, structural polymers that support closing the loop for organic waste in composting, consist of completely biodegradable components. The technical loop is enabled on many levels, e.g., by leveraging intrinsically recyclable thermoset polymers or monomaterial system design, be it for running shoes197 or in packaging.
In the view of the authors, the sustainable design of polymers going forward will rely on the following aspects:
-
Learning from positive case studies to improve the circular value chain: The disappointingly low recycling rate on the global level needs significant improvement. Positive examples like PET recycling in Germany42, 198 and organic waste recycling to compost in Italy199 can be a motivation to improve in other polymer material classes.
-
Leveraging interdisciplinarity: The development of a circular and carbon-neutral reality for polymers in both the technical and biological cycle requires the cooperation of different disciplines: Polymer chemistry, biology, and engineering must work closely together using the new opportunities of digital tools to speed up development times.
-
Working together in a constructive way based on scientific findings: The transformation process towards circularity and carbon neutrality requires the cooperation of all stakeholders beyond the realm of science and technology. We believe the basis for any pursued solution has to be valid scientific findings that support constructive dialogue and help to inform additional political and social dimensions. Political scientists and economists can offer advise on how to set up societal frameworks (such as Extended Producer Responsibility Systems) to finance waste collection & recycling.
-
Technological feasibility and optimism: Different polymer types are useful in different scenarios. Since polyolefins can be recycled mechanically and chemically to feedstock, their collection must be mandatory. On the other hand, e.g., polyesters offer a potential for further molecular design including the adaptation to recycling and biodegradability. Reducing the carbon footprint can be achieved by different measures, including biotechnological approaches, CO2 capturing technologies, and a certified mass balance approach. No single technical recycling technology will create a circular economy for plastics; complementary methods need to be accepted.26 The search for new and more carbon-neutral synthesis pathways and the application of a new “sustainability polymer chemistry toolbox” has only started and offers a lot of opportunities for academia and industry. It seems worthwhile to reinvigorate research on polycondensation chemistries, including enzymatic approaches for increased control.200 As a result, we need both a sense of reality for the time of implementation and the ambition to follow through. The significant level of transformation includes renewable energy supplies and will need time and commitment for realization from laboratory to large-scale industrial application.
-
A reliable and meaningful legislative framework stimulating innovation: The constructive dialogue with science should support a legislative framework that stimulates innovation of sustainable chemistry and keeps “green fake solutions” out. Ambitious fees for landfilling and incineration of solid municipal waste are needed to disincentivize such pathways. Every innovative technology has pros and cons: balancing both aspects based on scientific findings is necessary to decide how technologies should be combined in an “orchestra of solutions”, probably with some regional differences.
-
Timely action: Decisions towards legislative frameworks stimulating innovation and the build-up of infrastructure including respective investments must be taken now and within the next years. The push for the sustainable design of polymers has to be intensified in both academia and industry to achieve circularity and carbon neutrality.5
Acknowledgments
We thank Jens Hamprecht, Xenia Beyrich-Graf, Piyada Charoensirisomboon, Thomas Greindl, Dieter Boeckh, Malte Siebert, Marina Leed, Carla Seidel, and Willis Muganda for all the valuable comments and suggestions. Likewise, we acknowledge very helpful recommendations by the anonymous reviewers.
Conflict of interest
The authors work for BASF, a company that makes and sells polymers and chemicals.
Biographical Information
Bernhard von Vacano studied chemistry, and physics as an elective subject, in Tübingen (Germany), at the University of Wales in Bangor (UK), and at the Max-Planck Institute for Quantum Optics in Garching (Germany). He received his PhD in physical chemistry from Marburg University (Germany) and joined BASF in 2008 in the company′s Polymer Physics department. Since then, he has since held various positions in research & development in Germany and the USA, and is now a Senior Research Fellow, leading a program on closed loop polymer recycling.
Biographical Information
Hannah Mangold studied chemistry at Freiburg University (Germany) and completed her PhD at the Max Planck Institute for Polymer Research in Mainz on the topic of organic photovoltaics. She joined BASF Research in 2014 and has been working in diverse fields such as photophysics of luminescent materials, as well as in product development for display materials in the corresponding business unit. She is now a team leader for polymer recycling in the Process Research department, focusing on depolymerization projects and solvent-based approaches.
Biographical Information
Guido W. M. Vandermeulen studied chemistry at Leiden University (The Netherlands). He received his doctoral degree in Polymer Chemistry in 2003 at the Max Planck Institute for Polymer Research in Mainz (Germany). After a postdoctoral stay at the University of Toronto (Canada), he joined BASF in 2005. There, he has worked in research and development, product management, marketing, and project management. In 2021, he obtained his Bachelor of Science degree in Law (LL.B.) from the Fern-Universität Hagen (Germany). His current research interests focus on the development of novel biodegradable polymers.
Biographical Information
Glauco Battagliarin studied material science at the University of Milano Bicocca (Italy) and obtained his Ph.D. at the Max Planck Institute for Polymer Research in Mainz (Germany) on the topic of dyes for organic electronics. He joined BASF in 2012 as a team leader in the research department for organic electronics. In 2015 he moved to biopolymer research, where he is currently leading a team investigating and simulating the biodegradability and environmental fate of materials in different end-of-life scenarios.
Biographical Information
Maximilian Hofmann currently leads the Technology Scouting team in BASF's corporate research platform, where he is focusing on sustainability, carbon management, circular economy, and recycling. Maximilian studied chemistry at the Universities of Tübingen and Heidelberg (Germany), and was a visiting researcher at the mechanical engineering department of Stanford University (USA). He received his PhD in physical chemistry from the University of Heidelberg and joined BASF's polymer research division in 2007. He has since held positions in research to marketing and strategy, including two years at BASF's Asian headquarter in Hong Kong (China).
Biographical Information
Jessica Bean studied Chemistry at the University of Bath (UK) and completed her PhD there in Polymer Chemistry and Microbiology in 2015, including a six-month DAAD scholarship for conducting research at the University of Siegen (Germany). After a postdoctoral stay at IMTEK, University of Freiburg (Germany), developing microstructure-printed surfaces, she joined BASF in 2017. She has since worked in viral formulation development, and from 2018 has been a lab leader responsible for digitalization and automation activities within the Biopolymers research group.
Biographical Information
Andreas Künkel studied biology in Marburg (Germany) and completed his PhD at the Max Planck Institute for Terrestrial Microbiology in Marburg. He joined BASF in 1999 in the company′s biotech department. Since then, he has worked in various marketing positions for Fine Chemicals and ecoflex® & ecovio® with a focus on strategy and New Business Development. Since 2010 he has headed biodegradable and biobased polymer research. Currently, as an executive expert and Vice President, he is leading a program for biodegradable and biobased materials. Andreas lectures at the University of Marburg.